November 28, 2017
One Step Ahead of Wear and Tear
Predictive maintenance saves a significant amount of time and costs compared to conventional maintenance procedures that are still widely used today. It also enhances process efficiency and reduces the risk of injury and damage to equipment and the environment. Benedikt Rauscher (Head of Global IoT/I4.0 Projects) and Andreas Grimsehl (Product Marketing Manager for Interface Technology) share their views on this topic.
Andreas GrimsehlIn order to implement a predictive approach to maintenance or predictive analytics, high-performance hardware and software systems are required that can interpret and establish relationships between process and status data in real time. Only a few years ago, such data volumes would have been considered unusable from a commercial perspective, since analyzing this data would have simply taken too long. Today, we have the necessary computing power to handle these data volumes, making 'big data' aggregated from machines more and more attractive—both for manufacturers that want to make specific projections about production processes and for machine builders who know that offering a high level of machine and plant availability is a lucrative business model.
Benedikt RauscherCondition monitoring—where the individual components within a machine are monitored—is required to enable comprehensive predictive maintenance to be implemented at a higher IT level. For this form of monitoring to be effective, individual components need to be present on the machine that are able to record their own status, or dedicated components need to be installed to monitor the condition of other components in the machine. Building 'see-through' machines that provide maximum transparency over their own status gives customers a real competitive advantage.
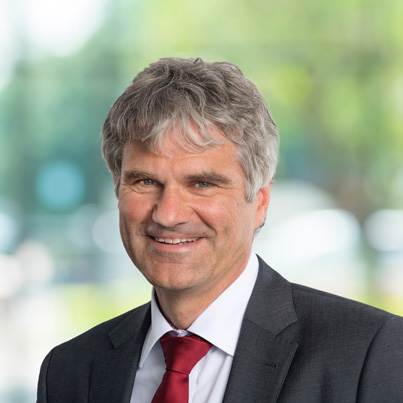
Andreas GrimsehlA good example is a ball bearing in production machinery. The bearing balls are subjected to constant wear. In the worst-case scenario, if they wear completely, an entire process could come to a standstill. This would be a classic example of 'small cause, large effect.' However, even these kinds of failures can be avoided: A sensor can be installed in conjunction with a special voltage repeater module to monitor the wear of the balls. Using characteristic patterns within the mechanical vibrations of the balls as a basis, a higher-level software system can then draw conclusions about the status of the bearing.
Benedikt RauscherIf you view this scenario in the context of processes being networked as much as possible, the IT system could then trigger a fully digitized order for a new ball bearing. The maintenance technician would then be automatically notified via push notifications of the problem and the date on which the spare part is being delivered. This is of course an application in which the sensor supports condition monitoring in a very specific way. However, sensors are used in all aspects of industrial automation to fulfill conventional switching functions in a discrete production process, so they are not there solely to monitor other components.
Benedikt RauscherNo, that is not necessarily the case. The photoelectric distance sensors in the R100 series from Pepperl+Fuchs show how this setup can be intelligently implemented without the need for additional equipment. In addition to the actual process data, these state-of-the-art devices also deliver a value that provides information about the signal quality—the 'functional reserve.' This information provides a good indication of how much of the light emitted is actually being received. Dirt and contamination are the most common reasons that this level drops. Dirt can then be removed before the sensor function is impaired in any way, and the sensor monitors this status independently. Thanks to IO-Link, a field-level communication standard that is becoming increasingly relevant, users are now benefitting from more and more of these diagnostic functions. Another example of intelligent products that are developed with predictive maintenance in mind are modern fieldbus modules. These modules offer a counter function for monitoring wear directly in the module. When the limit value is reached, a maintenance message is sent to the controller. This provides the information needed for predictive maintenance and requires even less programming in the complex PLC software—an added advantage!
Andreas GrimsehlProcess plants with explosion-hazardous areas are rather slow when it comes to updating and implementing major technology changes. For this reason, the focus is often on optimizing existing systems while posing as little risk as possible to operational reliability. It is precisely here where there is potential to develop truly exciting products and applications. We just developed a modular surge protection system, for example, that transmits status information to the control room directly via the Power Rail. This saves a lot of trips to the switch cabinet. Fieldbus solutions such as FieldConnex® from Pepperl+Fuchs have long been demonstrating the potential of full digital connectivity of field devices. In these architectures, in addition to status information, the field devices also independently transmit diagnostic information and alarm messages. Any adjustments can then be made to the instrumentation directly from the control room. Amid increasing digitization, the HART protocol has also become more appealing to plant operators. Many field devices are able to 'speak' HART but have not been used for this purpose to date.
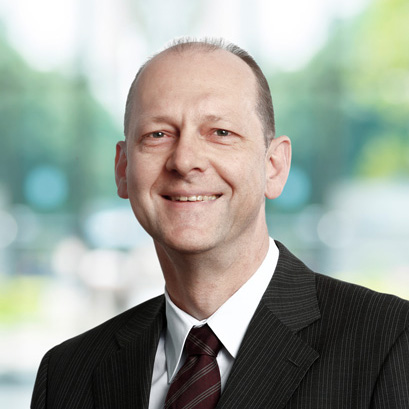
Benedikt RauscherPlant operators are beginning to see the potential and benefits that come with increased data. Particularly in outdoor areas that are difficult to reach with conventional wiring, WirelessHART is a real option for achieving greater levels of plant transparency without the need for major modifications. Working with our partners at Endress+Hauser, Samson, and SAP, we implemented an application in the chemical industry in which valves and flow meters are equipped with the BULLET WirelessHART adapter. This adapter enables the components to channel not only the actual process data into the SAP cloud, but also additional diagnostic information, without the need for extensive cabling. With this setup, extensive analysis can be conducted and data can be interpreted with ease, fully in keeping with the principle of predictive maintenance. And all this without having to intervene in the control system or shut down the plant!
Andreas GrimsehlAlongside this, under the working title 'Ethernet for Process Automation,' a consortium of automation companies is already working on the next steps: making Ethernet available at the field level, even in explosion-hazardous areas. To carry out this work, the consortium is resolving many challenges that are typical in the field of process automation: long cable runs of up to 1000 meters and an extremely harsh environment with exacting requirements in terms of EMC and explosion protection. Using Ethernet in its conventional form, overcoming these challenges would only be possible at a great cost, if at all. Ethernet for process automation will overcome these limitations and make it possible to significantly speed up communication. This is truly revolutionary for process instrumentation. If a cloud solution can receive comprehensive process and status data from the field in real time, this will give real momentum to the topic of predictive maintenance within the process automation industry.
Benedikt RauscherYour impression is correct. We're of course seeing that at Pepperl+Fuchs too and are actively participating in shaping this development. You can see that from our newest startup, Neoception GmbH, which will be focusing precisely on this topic: How can I create added value for customers from big data? Our colleagues at Neoception have the necessary expertise from the field of software development to tackle this topic.
Andreas GrimsehlAt Pepperl+Fuchs, a new version of our remote I/O gateways is in the making. This device is used to establish a connection between I/O modules and IP-based bus communication. It is built to be modular, allowing a software agent developed by Neoception to be implemented. The agent takes on the role of an intelligent converter and data collector. It queries information from all kinds of devices/sources, including the HART protocol. It then converts this information and makes it available at defined endpoints. In addition to process variables, information such as asset and status data is also included. Thanks to this potential second communication path, it could be possible to use the gathered information to see how the parameters of individual field devices develop over time.
Benedikt RauscherHere you can see how hardware and software development can work side by side to benefit the customer in the age of the IIoT. This collaboration will become even closer in the future, that much is clear. It will also become increasingly important to advise customers when introducing solutions for condition monitoring and predictive maintenance. I'll allow myself to make that prediction now, without a stochastic analysis tool at my disposal!