Aug 15, 2018
From Herbal Medicine to HMI
Join us on a journey through the different stages of a pharmaceutical manufacturing process and learn about the benefits Pepperl+Fuchs HMI systems offer for each process stage.
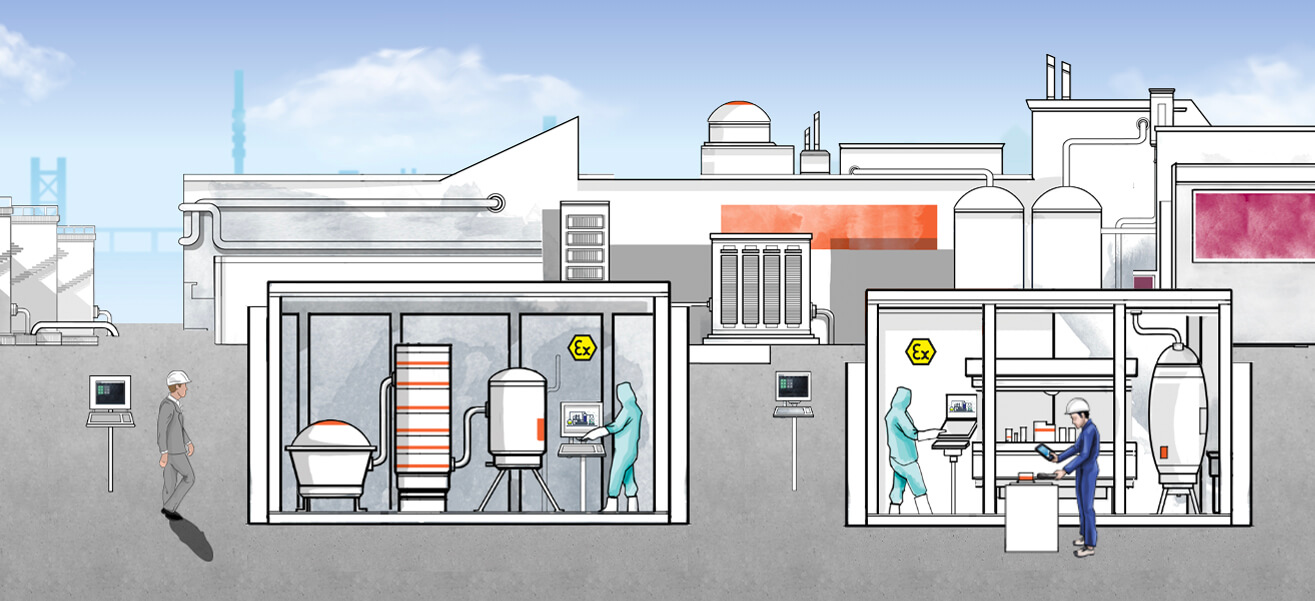
Press "Play" and scroll down to join Site Manager Paul on a tour through his plant.
Play!The history of medicine is as old as humanity itself. A discipline that largely consisted of monastic herbal lore in Europe from the Middle Ages onwards has in the 21st century become a high-tech process that, due to its complexity, involves an abundance of related data—and this data volume is continuing to grow: “As a result of Industrie 4.0, it is also becoming increasingly important to allow decentralized access to information and control functions. And pharmaceutical production is no exception. Increasingly, companies are relying on multi-purpose plants that are designed for the most efficient possible production of various medicinal products,” explains Business Development Manager Stefan Sittel. His colleague, Dr. Marc Seißler, Product Portfolio Manager, adds: “Networked HMI systems are essential for achieving sustainable, efficient manufacturing in the pharmaceutical industry. However, they must also comply with regulatory requirements for pharmaceutical production, the GMP (good manufacturing practices) directives, and, in some cases, explosion protection directives."
Fine Chemistry for a Powerful Effect
If you were to accompany medications on a typical journey through their manufacturing process, you would encounter various Pepperl+Fuchs operating and monitoring systems along the way that solve this problem. The spectrum of operating locations begins with the upstream suppliers from fine chemistry, who provide the basic materials to the pharmaceutical manufacturers in what is known as the “upstream phase” of pharmaceutical production. To obtain these substances, every detail—such as the purity of the various components, the storage temperature, and the pH value—must be correct. Only in this way can it be ensured that they will achieve the desired effect during the subsequent synthesis of the active ingredients. The latest development from Pepperl+Fuchs in this field can be seen in the form of VisuNet GXP—a thin-client-based remote monitor that can be used to display process information and control functions and is fully aligned with the needs of fine chemistry. It is built to be resistant to liquids, dirt, bacteria, and aggressive cleaning processes, while its extremely lightweight and modular design allows for high flexibility in the field.
In addition, the VisuNet GXP is suitable for the potentially explosive atmospheres that occur in these process stages due to dust or detergents and solvents containing alcohol. During batch or dosage control, it reliably displays information transmitted via Ethernet from the control system or MES—directly in ATEX Zones 1 and 21 or Zones 2 and 22. “Whether it is connected with conventional PC workstations and servers via the network infrastructure or used on future-oriented, virtualized PCs and servers plays no role in the integration into the automation architecture. Our new firmware VisuNet RM Shell 5 is based on Windows 10 IoT Enterprise and supports the latest remote services such as Microsoft® RDP 8.1 or Emerson’s DRDC and therefore both approaches,” Sittel explains.
Under Open Skies
Pepperl+Fuchs has also equipped its other highly specialized, Ethernet capable operating and monitoring systems with the RM Shell 5. This includes the VisuNet IND product family, which is used in tank farms for pharmaceutical substances. In these potentially explosive atmospheres—corresponding to Zone 2 and Class I, Div. 2 respectively— where basic chemicals from fine chemistry are temporarily stored, the filling and emptying of the tanks must be monitored and controlled. Wind and weather also take their toll on the equipment used. “The VisuNet IND shows process-critical information about fill levels and temperatures on the display in a clear format. It therefore helps the tank farm personnel make decisions and provides a real gain with regard to process safety and availability. When used in conjunction with integrated identification systems from our portfolio, it can also provide reliable identification of truck drivers making deliveries and of loading orders,” Sittel explains.
“As outdoor solutions, remote monitors from the VisuNet IND family have displays that are visible in daylight and are designed to be rainproof. The temperature range in which they can be operated extends from a wintry –20°C to +50°C in the summer sun,” says Seißler, describing the design features. As for the software level, he says, “The Ethernet connection of HMIs is particularly advantageous in outdoor areas. Thanks to digital communication between the remote monitor and host system, consistently high image quality can be maintained without the comprehensive configuration required for the formerly prevalent analog KVM systems. Additionally, the possible transmission range via the network infrastructure is not limited as with a KVM system.” Mobile devices from ecom are a useful recent addition to the Pepperl+Fuchs product portfolio for recording raw material deliveries in these outdoor areas quickly and efficiently. "PDAs such as the i.roc Ci70 -Ex and the Ident-Ex handheld scanner from ecom combine Auto ID in ATEX Zone 1 with mobility. A modular head system allows devices to detect RFID tags across a wide range of frequencies, plus 1-D and 2-D barcodes. This means they can be used for almost any identification task required during pharmaceutical production," adds Sittel.
Hand in Hand
During the subsequent batch-oriented production of “intermediates”—that is, the interim products needed for the actual medicine—numerous manual inputs are required at the plant; as a result, operating and monitoring systems are everywhere. VisuNet GXP also offers a suitable solution for these scenarios: in addition to an antibacterial membrane keyboard with a capacitive touch pad or optical trackball, it is equipped with a large Full HD multitouch panel, which allows personnel to operate it without any problems even when wearing gloves. According to Seißler, this illustrates how the interaction between human and machine can look in Industrie 4.0 environments: “With the GXP, the qualified personnel are given an operator workstation that is completely tailored to the numerous manual interventions required in the life science sector. Since the RM Shell 5, which is a supplement to this, and the additional management tool VisuNet Control Center greatly streamline the commissioning, administration, and support of these operator workstations, there is a double gain in efficiency.”
In fact, thanks to Control Center, production technicians can connect with any VisuNet Remote Monitor from a distance, which allows them to support plant operators without having to enter the sensitive production areas at all. As a result, the monitors can be set up faster and more efficiently than ever before. “The commissioning engineer connects to a remote monitor in the clean room via ‘session shadowing,’ creates a new profile on it, and transfers this profile to any number of additional monitors via the Ethernet network,” Seißler says by way of example. He continues: “Further, thanks to the VisuNet Control Center, possible faults or interference in the connection between remote monitors and their host computer can be detected immediately. A process engineer then supports the employee on-site from a distance or, if necessary, takes over control via password-protected access. In addition to remote monitoring, telephone-based communication may also be useful here. The Smart-Ex® 02 from ecom has been developed specifically for such applications. The fact that it is a fully operational Android-based smartphone with certification for ATEX Zone 1 means that it can be used for a variety of other applications in addition to conventional telephone calls via a connected headset. Employees can use the camera to identify barcodes on technical process equipment within pharmaceutical production plants and obtain relevant service and maintenance information, or receive specific work instructions via email. Mobile devices such as the Smart-Ex 02 or the Ex-Handy 10 featurephone also protect employees at the plant. Thanks to a programmable 3-D motion sensor that triggers an alarm if inclination, impact, escape, or lack of movement is detected, the control room can locate a casualty in case of emergency and take any necessary measures."
At Home in the Clean Room
Following the pharmaceutical process further to the production of the active substance, referred to as the “Active Pharmaceutical Ingredient” (API), there is a decrease in the frequency of potentially explosive atmospheres, accompanied by an increase of caution regarding contaminants. This caution is justified because, in the worst case, the remnants of a previous production process, contaminants adhering to shoes, or a single human hair can render an entire batch unusable. Such environments, which often include pharmaceutical clean rooms in accordance with GMP directives, require operator workstations for interacting with the process or production control system that are designed specifically for chemical and mechanical robustness and can be properly cleaned. With the VisuNet GMP, Pepperl+Fuchs provides a product family that—as the name suggests—has been developed specifically for these operating conditions. “Ease of cleaning, chemical resistance, and an antibacterial keyboard make the VisuNet GMP a specialist for clean-room environments in the production of APIs. To meet the different conditions at our customers’ locations, it is available in two basic versions: either as a remote monitor equipped with RM Shell 5 in a slim, stainless-steel housing with a foot or a wall bracket or as a panel-mount version for installation either in wallmounted control panels or machine-operating panels,” says Sittel of the supplement for the VisuNet GXP, which is also suitable for clean rooms. He adds: “If a potentially explosive atmosphere is present in special cases, the VisuNet GMP can also be used in a version that has been certified for Zones 2 and 22.” Integrating mobile devices into the process also offers the potential for particularly efficient working practices. Seißler outlines an example: "Using both a handheld scanner and tablet from ecom is of great help when it comes to identification tasks during production of APIs. Employees can read the recipe on the tablet and identify the ingredients using the scanner before confirming the composition and quantity of the lot via the device."
The Solution in the Box
According to Sittel, there is also a high demand for information in the nonclassified production areas and on the periphery of active substance production, such as in the controlling laboratories: “Anyone looking for a lean industrial solution for workplaces with visual displays in a production or laboratory environment would be well advised to use our industrial box thin client ‘BTC.’” A glance at the handy BTC unit supports his recommendation: enclosed by a metal housing, it combines the advantages of a narrow footprint without fans or hard disks with extraordinary robustness in the face of ambient temperatures of up to +60°C. The housing, which is IP4x rated, also protects the interior from dust. “The BTC can be used either as a conventional desktop solution or attached to a mounting wall inside a housing. Without needing much installation space, a device could be mounted in a workspace drawer, for example, and visualize process-relevant information on four screens in the laboratory rooms at the same time. It is difficult to imagine providing information in an industrial environment in a more cost-effective and space-saving way,” Sittel explains. Like the VisuNet Remote Monitors, the BTC is also equipped with the RM Shell 5, which means it can be set up very quickly. And users who prefer other management software for thin clients can still rely on the BTC: “To ensure maximum flexibility, we also offer the BTC in a version that is compatible with the ACP ThinManager, which is used particularly in large American pharmaceutical plants,” says Sittel, emphasizing the customer focus in the development of the BTC.
Downstream to the Finished Medication
This focus on the customer is also apparent in the final process steps in the pharmaceutical industry: once production of the active ingredient is complete, it is still not ready to be given to patients. “This ‘downstream section’ involves additional physical process steps, for which highly specialized machines from OEM companies are often used,” explains Sittel. Accordingly, Pepperl+Fuchs provides VisuNet solutions in stainless-steel housings for machines and plants from these OEM suppliers, as well as panel-mount remote monitors that can be integrated for DCS/MES operation or panel PCs for PLC connection. These visualization systems and operating devices, which are often based on the GMP product family, are needed to display information in the subsequent, complex process steps and to control recipes. Through centrifuging, chromatography, and drying, the carriers are removed in these stages and the active substance is further processed—for example, by grinding it, dissolving it in liquid, or by granulation and applying the “coating” to the carriers. Here, the portioned medication is given the form we are familiar with as a tablet, salve, or solution, before being packaged for shipping in blister packs, tubes, ampules, syringes, or packets.
Close to the Industry
Whether Pepperl+Fuchs is commissioned by the pharmaceutical manufacturer itself or by its integrator or a machine-and-plant manufacturer, the crucial factor is that not only components are required but complete GMP-capable, functional systems. This requires specialists who bring with them equal amounts of practical experience, advisory expertise, and engineering know-how. Sittel provides an example: “With pharmaceutical production becoming increasingly paperless, we experienced on-site that our customers have to display both MES and DCS functions on monitors in the field ever more often. This can be resolved in the first instance using an HMI solution with dual display—which our VisuNet GMP offers in the duplex version. However, we also discussed this with our software experts. They then enhanced RM Shell so that our customers can now switch between DCS and MES on a single monitor.” Marc Seißler summarizes: “As in pharmaceutics itself, there is no universal panacea for operating and monitoring systems. By using different connection and protocol types for connecting with control panels and PCs, as well as different housings, keyboards, mice, or mounting components, the Pepperl+Fuchs HMI systems can be flexibly adapted to individual application requirements. Our industry experts and the worldwide Solution Engineering Centers are well positioned for this. The VisuNet product families, intrinsically-safe mobile devices from ecom, BTC, RM Shell 5, and VisuNet Control Center, provide unique operating and monitoring solutions, which are an ideal fit for modern, networked pharmaceutical production in the truest sense of the word.”
With the rugged tablets from ecom, you can access your data and applications even in hazardous areas. The Tab-Ex® 02 is the latest version.

With its modular head system, the i.roc® Ci70 -Ex can be used for all kinds of data logging, providing highest flexibility.

The VisuNet IND remote monitors are suitable for outdoors as well, even in extreme temperatures between -20 and +50 °C.

Truly light: the modular VisuNet GXP remote monitor comes with a weight of under 25 kg.

The VisuNet GMP remote monitor is made for clean rooms according to GMP guidelines ...

... and also available as double screen solution.

The explosion-proof smartphone Smart-Ex® 02 offers unlimited flexibility in hazardous areas.
