September 13, 2017
Material Flow with Vision
The stacker cranes are constantly in motion. They flit back and forth non-stop between the racks, where the constant stream of boxes briefly comes to a stop. The tireless machines in the Global Distribution Center (GDC), which opened in 2016 in Singapore, are more than just technical assistants.
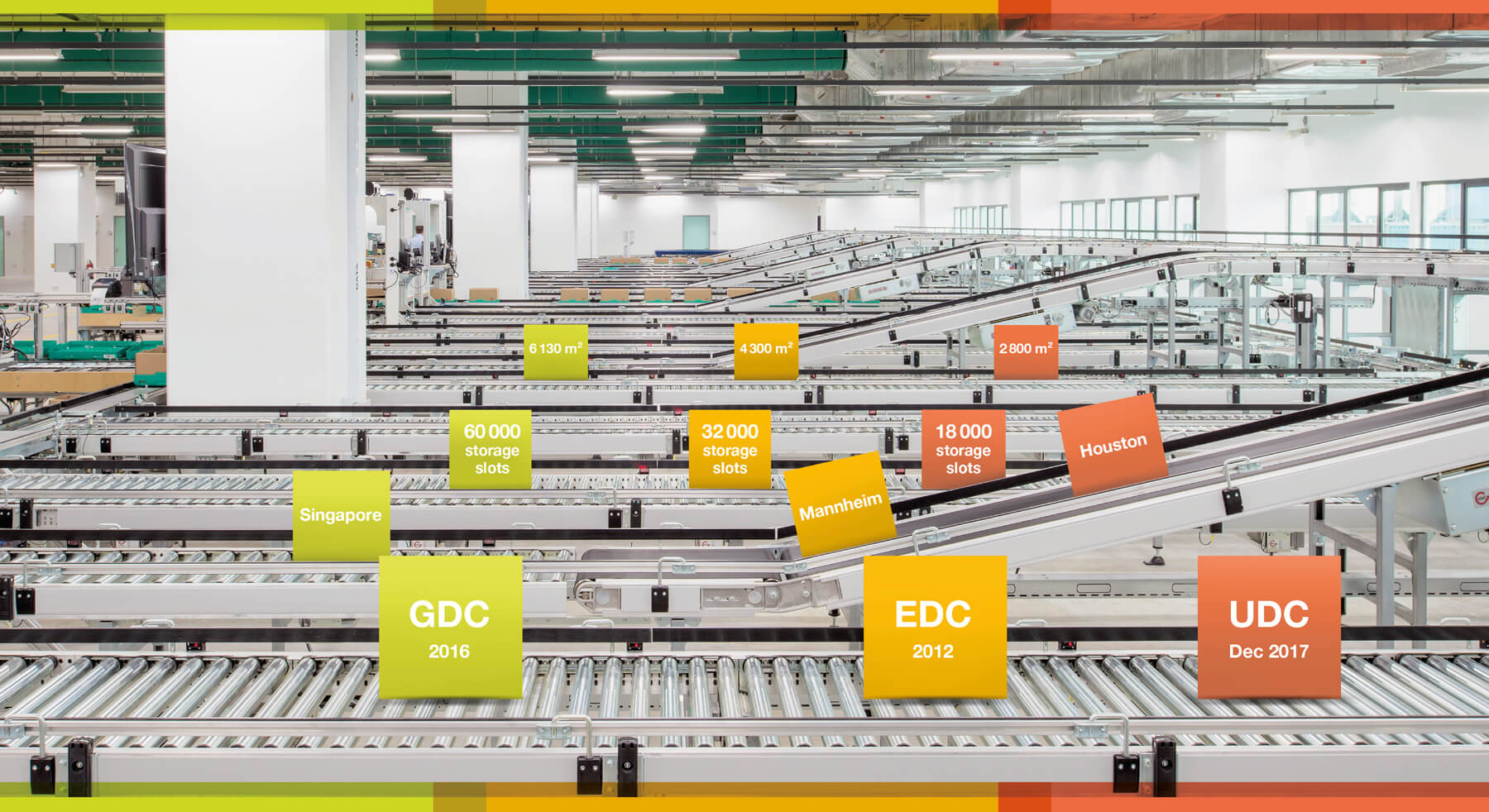
“Logistics automation in the Mannheim headquarters was a pioneering achievement over twenty years ago, but the technology from that time just reached its limit at some point,” explains Logistics Manager Markus Külken. “Also, more space was required, and procedures needed to get significantly faster to keep pace with the growth of the business. So we decided to build a new distribution center with the highest possible level of automation.” The tried-and-tested technology from Mannheim was subsequently implemented internationally with great success.
Same but Different
At first glance, you can hardly tell whether you are in Mannheim or Singapore, since the two distribution centers look amazingly similar to each other. The new American equivalent, the US Distribution Center (UDC) in Houston, will be opened this year with the same “look and feel”. The similarity of the centers is of course not a coincidence. Mannheim has served as a model for proximity to customers and reliable delivery. Based on this, the structure and technology were transferred to Singapore and Houston and developed further. An important component is automated small parts storage in high racks. There, the goods are stored in boxes on trays, which are transported by fully automated stacker cranes to the required place. Based on the goods-to-man principle, they go to the workspaces on roller conveyors. Of course, Pepperl+Fuchs products complete the central tasks of acquisition, control, data transfer, and testÂing in all distribution centers, and therefore prove their value again and again in logistics applications.
Fully Automatic Storage
In addition to the state-of-the-art automation technology, the main difference between the new and old storage systems is a comprehensive warehouse management system (WMS). It is integrated into the company-wide enterprise resource planning (ERP), displays individual processes in much more detail than in the past, and can control entire logistics processes. In addition, all Pepperl+Fuchs locations are now integrated into the material flow more consistently, as Külken explains: “Each box that leaves one of our production sites gets a ‘number plate´ in the form of a barcode. It stores the material and quantity and can be matched with the code in the system. If the box arrives at one of the three distribution centers, it is now automatically inventoried and stored.” Only in the case of deliveries from external companies is human intervention needed—for now, because we are in talks with suppliers about how their boxes can be incorporated into the automated system.
Humans in the Midst of Automation
Employees are primarily involved in picking the goods, where individual orders are compiled and packaged. Light signals, which indicate the requested parts, assist them in repacking the goods from warehouse boxes into the shipping boxes. This technical assistance, also called pick by light, reduces search times and the error rate, and supports the employees´ concentration. If possible, however, the full bin retrieval principle is used: even in production, the packaging sizes are matched to various customer requirements, without human intervention.
Ideal Conditions in Singapore
The amount of time saved just by automatic storage is explained by the director of the GDC in Singapore, Han Thanh Hong: “Previously, when a 40-foot container was delivered, we needed two days to inventory the goods and transport it to the racks. Today, we can do it in three hours.” The structure and technology of the Mannheim logistics center was not applied one-to-one in the GDC. “We used the experiences from Germany and developed the system further. The updated version was then transferred back to Mannheim after the introduction in Singapore, so that we are now at the same, improved level.”
The starting position in Singapore was similar to Mannheim. The old logistics center was bursting at the seams, and accelerating the processes was becoming more and more urgent. 80 percent of Pepperl+Fuchs products come from locations in the city-state as well as Vietnam and Indonesia. So it was obvious that the new global distribution center should be built in the southeast Asian region. 'Singapore, with its modern infrastructure and traffic connections, business-friendly regulations, and good conditions for import and export transactions, offered the best environment,' said Han Thanh Hong.
Refining What Has Been Tried and Tested
Structure, technology, and the “operating system” in Houston are in line with the other two centers. The new UDC there will first serve the North and also later the South American market. “We can also use it as a regional showroom for our logistics products,” says Külken. “We can demonstrate the performance of our sensors in operation to interested customers there.”
What will benefit customers most, however, will be quicker, more reliable delivery, which will be made possible by the optimized, high-quality logistics processes. Incidentally, these are subject to a continuous improvement process, known within the company as LOOP (Lean Operation and Organization in Processes). “This process may reveal that an additional tool at a specific workspace can save a lot of time,” explains Külken.
The storage facilities have also been able to take the next steps toward digital transformation. 'Thanks to the high level of automation, 'digital logistics' is tangible and can be integrated into ongoing processes. With constant access to all data and different possibilities for fine-tuning, the processes in our distribution centers also conform to the principles of vertical and horizontal networking. The dynamic maintenance management is already making real-time data available to intelligent systems—be it the information from motors and brakes on the stacker cranes or the photoelectric sensors on shuttle cars. These forecast models allow machine learning and thus pave the way for predictive maintenance, which will significantly reduce sudden failures,' says Külken.