April 16, 2018
Up in the Cloud(s)
Jump onto an airplane for a few hours and find yourself thousands of miles away: planes take us almost anywhere around the world, and traveling above the clouds is becoming more and more popular. Innovative scanning technology from Pepperl+Fuchs helps ensure that an aircraft is comfortable and, above all, safe.
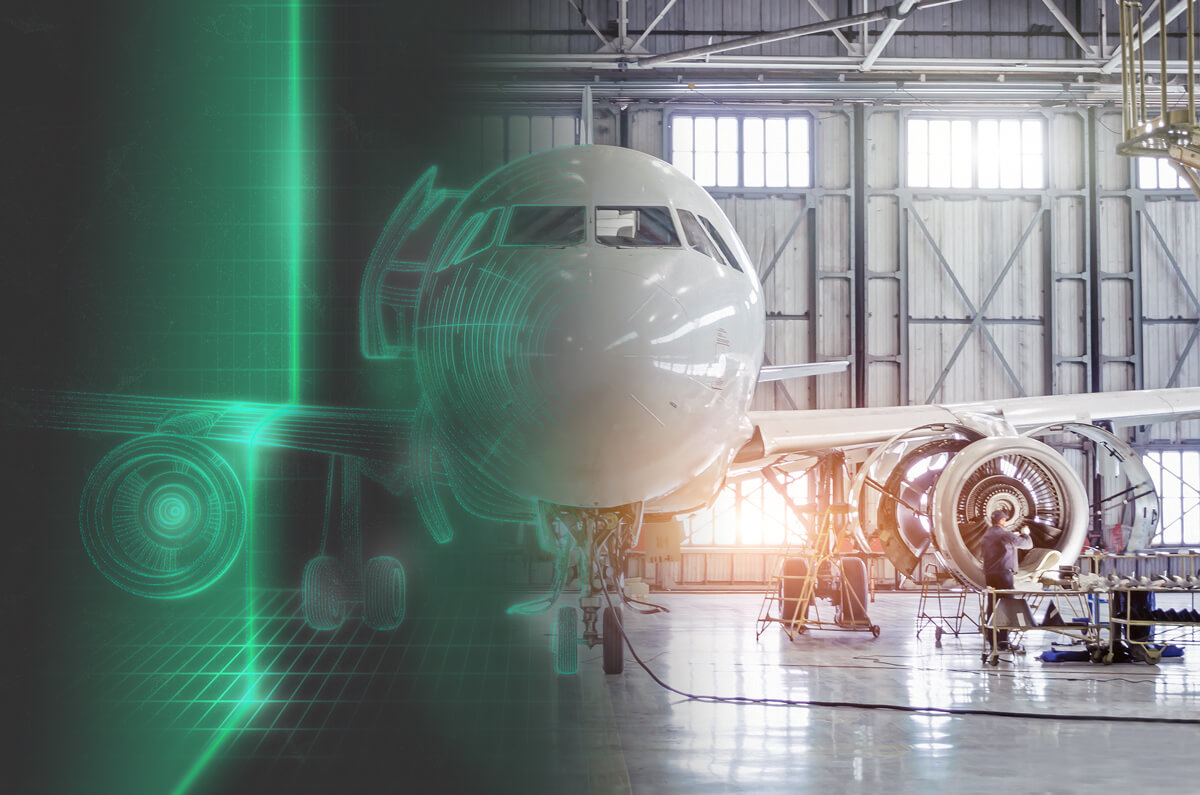
Frankfurt International Airport, 05:00 am: many passengers on board are still rubbing their eyes—it's been a long flight. The day before, they were all still in Shanghai; today they're back on German soil. Every day, countless people just like them use the skies to travel quickly and easily to other countries and distant continents.
Never before have so many people traveled by plane—whether for business or for pleasure—as they do today. The aviation industry is booming. At major airports across the world, the enormous machines take off in minutes—nearly one per second. They carry everyone and their baggage to all four corners of the world. But people don´t just fly to save time: it is still regarded as the safest mode of transportation there is. To keep it that way, aircraft are strictly controlled and tested on a regular basis. Not even the tiniest component can be faulty, because the consequences of a failure or malfunction in the air can be fatal. This applies to the electronic components that are installed on and in the aircraft in large quantities, as well as to the individual parts of the overall design.
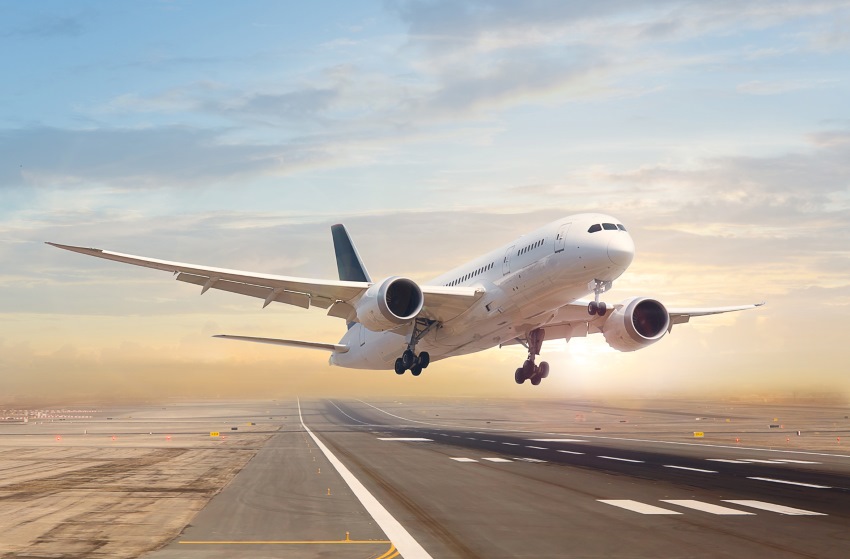
By No Means Simple
Before a bird of steel weighing several hundred metric tons can rise into the air, it has to be manufactured with the greatest engineering skill and the highest level of precision. Many conditions must be fulfilled to create the aerodynamics necessary for an airplane to fly at all. For this reason, the design must be error-free and the condition of the aircraft flawless. For instance, external cracks and dents can have a disastrous impact on the aerodynamics of aircraft, and should be avoided at all costs.
The sheer size of an aircraft presents a particular challenge. A single component such as the wing is many meters long and the fuselage even longer still—not to mention the enormous engines. This makes even the assembly of the aircraft components an extremely challenging undertaking, in which millimeter precision is required. Technologies that are capable of scanning the entire height, width, and length of such large components can provide significant support to aircraft manufacturers and maintenance staff in terms of correct assembly, quality control, and regular checks.
Nothing Gets Past Us
Pepperl+Fuchs offers the right technology for this task: a combination of several 2-D LiDAR sensors enables accurate detection of the assembly and maintenance halls, as well as the aircraft and components within them. Precisely calibrated, high-precision sensors are positioned at different locations to record the objects from different angles. The data from all of the 2-D LiDAR scanners is combined to form a three-dimensional point cloud, creating a precise digital image. Staff can use this image to recognize exactly how the components are constructed and positioned. This is useful when machines and parts need to be in exactly the right position to avoid collision during assembly of individual components.
But even before the individual parts of an aircraft come together to form a whole, the system of multiple 2-D scanners support the manufacturers and their mechanics. After all, it is not uncommon for the individual components of an aircraft to be manufactured at different locations—the fuselage in Germany and the wings in France or the USA, for example. In order to ensure that the components fit together during the final assembly, the scan data and resulting 3-D image can be compared with plans and models at any time.
On Cloud Nine
The data collected from multi-sensor systems is immediately available in a standard data format on the NeoNeon Cloud provided by the Pepperl+Fuchs subsidiary Neoception. This means that the three-dimensional image of the airplane or its individual parts is available anywhere in the world. This is a decisive advantage in the context of globally distributed production facilities. Now it's not just the manufacturer of the wing that can compare its design with the plan. The locations where the other components are produced also have access to the object scan, and can use the 3-D data for further processing to optimize components, or even form the basis for their own production.
Transferable to Many Areas
What works in aircraft construction can also be useful in many other areas of application. Intelligent multi-sensor systems with scanning technology from Pepperl+Fuchs are not only able to capture large components and entire rooms, but they can precisely scan and capture small objects, large objects, machines, and even people. The 3-D clouds of accumulated data points are immediately available for further processing via the NeoNeon Cloud. They are available all over the world and can be used directly in production, even individually in batch size 1. This allows customer wishes and requirements to be implemented flexibly and puts companies with globally distributed production facilities in a position to optimize plant utilization and increase efficiency.
3d.aero
Because there are many more aviation tasks waiting to be solved with automation technology and innovative software, Pepperl+Fuchs and Lufthansa Technik have bundled their competencies in the joint venture 3d.aero.