April 15, 2018
Panel Bending 4.0
Each one is larger and more impressive than the last: In the Salvagnini Maschinenbau GmbH plant in Ennsdorf, Austria, panel bending machines are lined up row by row. In a plant where countless machines are developed and manufactured every day to perform precision work the world over, new technologies are constantly emerging to make panel bending simpler and more efficient.
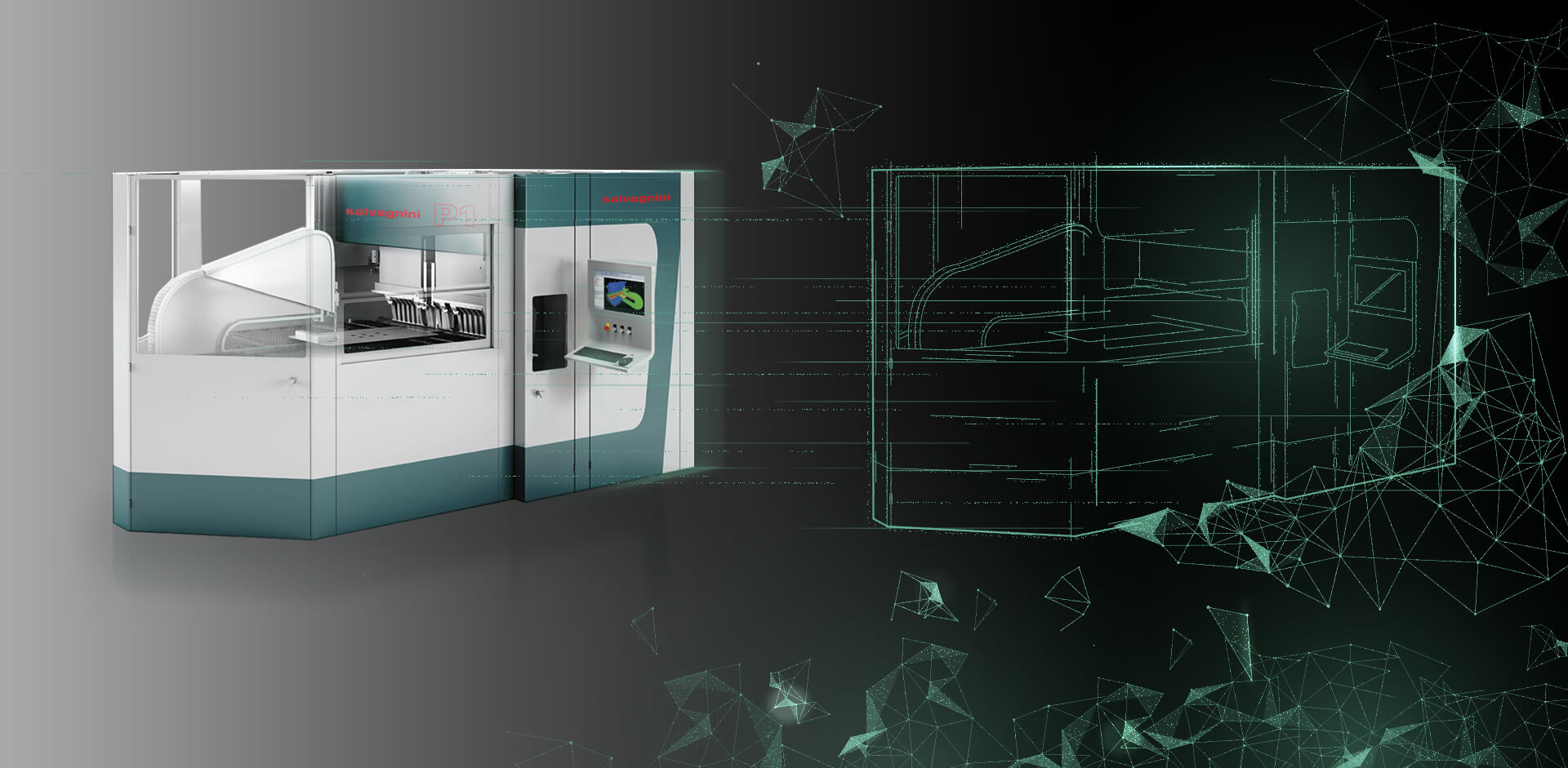
Interplay of Two Components
Before a simple panel is transformed into a finished product, a wide variety of different influences must be considered. 'When bending panels, there are two key factors,' says Wolfgang Kunze, Chief Technical Officer (CTO) at Salvagnini: 'Both the material and the machine itself are crucial in determining the bending result.' Of primary importance are the special material properties of each panel: 'Every material behaves differently—whether it's aluminum, steel, or stainless steel—and has a different tensile and flexural strength,' explains Kunze. Depending on the metal, the lot, and the strength of the workpiece, springback must therefore also be taken into account, otherwise the bending results may vary greatly. 'This means that the panel formed always deforms slightly to its former shape when there are no longer any forces acting on it,' he adds.
With conventional bending machines, manual corrections are often required to ensure consistently high quality. 'This added workload costs the company valuable production time and resources,' says Kunze.
Manfred Reiter, Head of Sales at Linz Center of Mechatronics (LCM) GmbH agrees: 'Unplanned plant downtime for reparameterization can get very expensive.' The Linz developers often work together with companies such as Salvagnini, which encounter similar manufacturing problems.
In addition, many of the metal processing companies manufacture small-scale batches alongside larger ones and would like to be able to control their production activities from anywhere in the world. 'As machine builders, that's exactly what presents us with new challenges on a daily basis,' admits Kunze, adding: 'This is why we are constantly working on innovative solutions for our customers and bring partner companies such as LCM on board for developments in the field of mechatronics.'
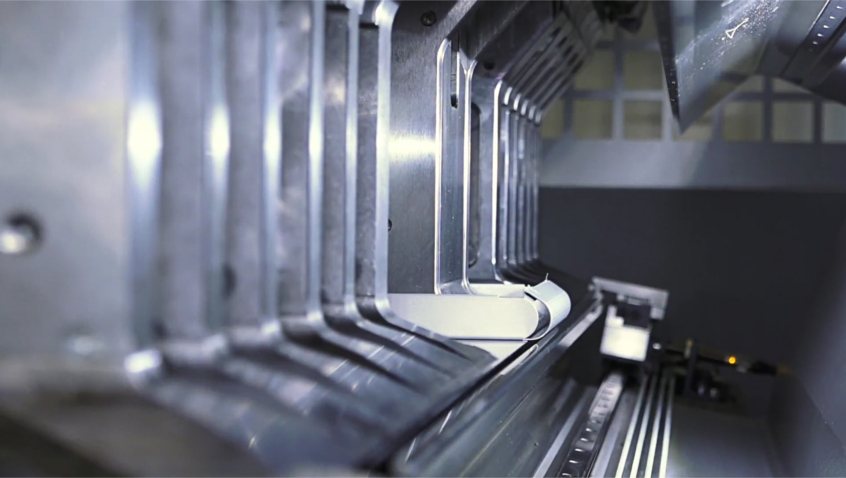
When Vision Becomes Reality
In order to meet the requirements of modern panel processing, Salvagnini has developed a solution with LCM that will signal a revolution, and not only in panel bending. The result is a completely new technology that has helped make a common vision become reality: the real-time material detection technology MAC 2.0, short for material attitude correction.
A Digital Twin Makes It Possible
But how exactly was the new technology developed? 'Using the finite element method (FEM), we have simulated both the machine itself and a wide range of panel properties, including the forming force that acts on the material during the bending process,' explains Reiter. 'In this way, we have created a digital twin of both material and machine, virtually mapping the entire bending process.' The developers at LCM have used all of this information to generate efficient simulation models by means of model reduction, which are then integrated in the MAC 2.0 software. 'With MAC 2.0, we are transmitting highly complex simulation models in real time to a software that automatically controls the complete bending process,' explains Reiter with pride. Using this information, the machine can simulate the bending process in real time based on the material properties, compare it with the finite element results, and compensate for any variations. This allows the machine to bend a panel perfectly—without material waste.
All of these steps are completed in a fully automated process. By using various Pepperl+Fuchs sensors for tasks such as positioning and detecting the thickness of the panels, all the important parameters for each individual bending process can be recorded precisely.
To determine the forming forces, the machine initially bends slightly more slowly than usual. Based on the determined values, the parameters of all actuators in the machine are automatically readjusted. As soon as the properties of material and machine are determined, bending occurs at the usual speed. And the result is clear: Bends are made with an accuracy of ±0.9°—regardless of the quantity, thickness, or quality of the panel. 'This is just half of the typical deviation on the market,' says Reiter. 'Only the type and thickness of the panel need to be defined in advance, and the measuring bend of the panel must be at least 40 degrees—for all other bends, the corrected tool paths are determined and the Salvagnini control system can be used,' says Reiter.
Companies will receive numerous benefits from the digital map of their plant. The software detects wear at an early stage and provides users with a precise overview of machine status at all times, meaning unforeseen parameterizations and follow-up work are now a thing of the past—a clear example of the advantages of predictive maintenance. 'With the development of the digital twin, customers can now manufacture without producing waste, be it for a quantity of one or for serial production,' says Reiter, adding: 'This allows us to solve problems in many areas of application.'
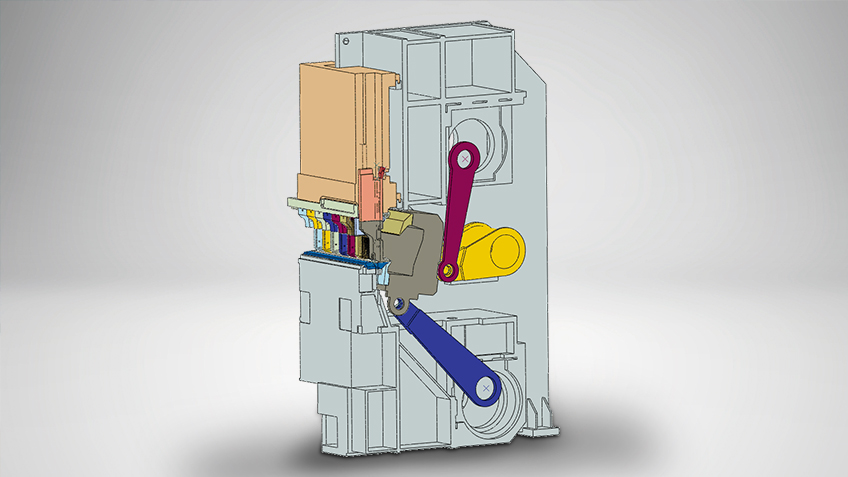
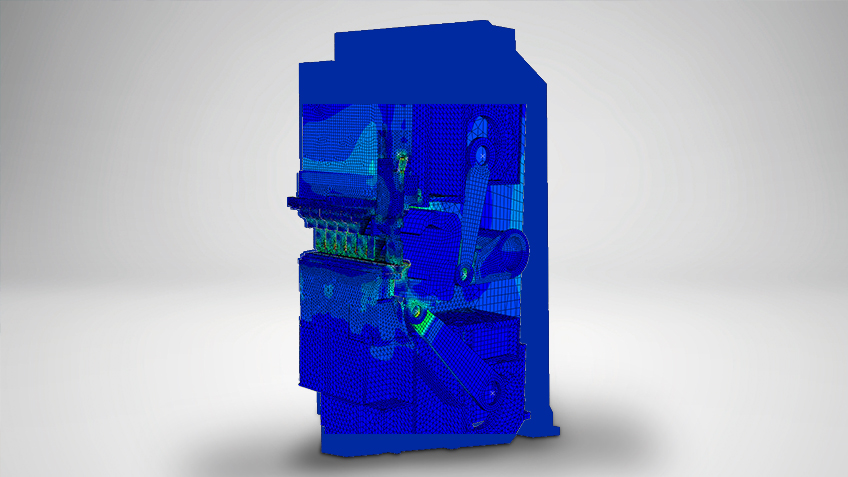
A Digital, Networked, and Flexible Factory
Building on shared expertise, LCM and Neoception have taken networking and global production one step further. The start-up, a subsidiary of Pepperl+Fuchs, is an expert in cloud connectivity and the Internet of Things, and has developed an interface that is already capable of establishing communication between the machine and the digital twin: 'To ensure continuous, cross-system data exchange, we have developed a cloud solution with Neoception that securely and reliably transfers order and process data,' says Benedikt Rauscher, Head of Global IoT Projects at Pepperl+Fuchs.
Starting with the order record through to the secure exchange of data between the machine and its digital counterpart, Neoception enables continuous, real-time communication between all systems involved. This allows sensor data to be transferred constantly from the machine to the virtual production map via the NeoNeon cloud, at which point the optimized process data of the digital twin can be securely transmitted back to the machine. 'This option provides the customer with a production solution that is networked and flexible, regardless of location,' explains Rauscher.
Engineering Expertise from Four Worlds
The interplay between networked production and the digital twin enables waste-free production and brings Industry 4.0 to life. 'Our customers receive a transparent, intelligent, and adaptive machine,' Kunze enthuses. 'Using the digital twin in panel bending is just one possible application,' continues Reiter. 'Every industry has its own unique problems and our technology can be transferred to a wide range of applications,' he adds.
'By pooling our expertise, we offer customers real added value and create transparency at all levels,' Kunze, Reiter, and Rauscher agree.
Finite Element Method (FEM)
Using the finite element method (FEM), virtual prototypes can be created to test components and solve engineering problems. FEM is based on a numerical method for the calculation of complex differential equations. Components are simulated and subdivided into a defined number of elements of a finite size that can be described with an endless number of parameters. These virtual prototypes help save development time and costs before the actual manufacturing starts, since design flaws can be detected and avoided at an early stage.