March 31, 2019
The Sweet Side of IIoT
Brazil’s 500-year old sugarcane industry is just as much a part of the country’s identity as World Cup wins and Carnival. To continue to produce 25% of the world’s sugar and ethanol, Brazilian sugarcane producers have come to rely on smart technologies that optimize sustainable production from harvest to sale.
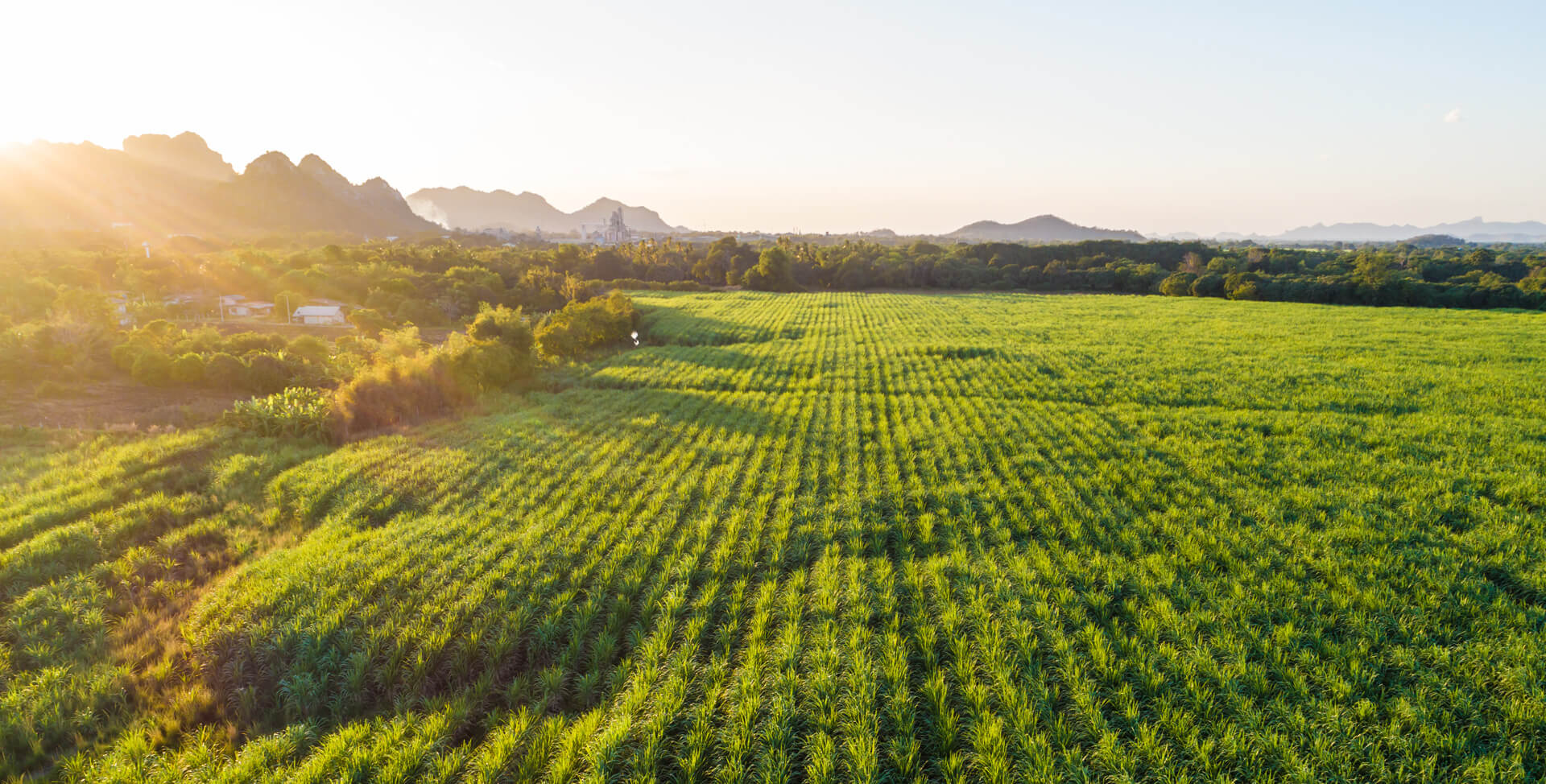
This push for smarter, cleaner processes has placed a broad spectrum of Pepperl+Fuchs products and solutions at the heart of sugarcane processing. Demand for such technologies has only increased since 2017, when the Brazilian government pledged to reduce its carbon footprint and accelerate work to build and expand the country´s IoT infrastructure.
Solutions for Every Stage of Sugarcane Production
Sugarcane sweetens coffee and cakes, is used to produce electricity, animal feed, and ethanol, and is fermented to make cachaça (pronounced kah-SHAH-sah), a liquor used in Brazil´s national cocktail—the caipirinha. But before you can indulge your sweet tooth, fuel your car, or mix yourself a drink, newly harvested sugarcane must first go through a complex production process.
Harvesting sugarcane requires the coordination of three distinct operation environments: the field, the road, and the mill. Cane shoots are cut and cleaned in the field and transported by truck to processing mills. When harvested cane shoots arrive at mills, sensors measure the volume of sugarcane moving toward extraction and the quantity of sugarcane waste, known as “bagasse,” going to be burned as fuel. R2000 LiDAR sensors from Pepperl+Fuchs are used for this task.
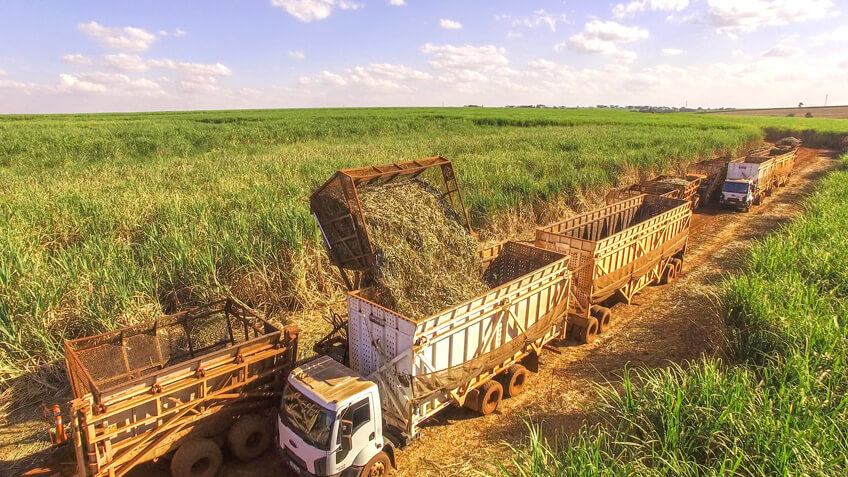
As the product moves toward the roller mill for extraction, ultrasonic sensors like those in Pepperl+Fuchs´ UC4000 series detect the presence of sugarcane on the conveyor belt. UC4000 sensors control the speed of the conveyor belt to ensure that the correct volume of cane is deposited in the roller mill. “This device in particular ensures consistent cane juice extraction while maintaining machine health,” says Lucas Santos, Sales Executive for Factory Automation at Pepperl+Fuchs Brazil.
Roller mills are used to extract juice from the raw cane. In this stage, durable sensing technology is necessary because it must withstand washdowns, dirt, and high temperatures over the course of the day. Rugged inductive positioning measurement systems (PMI) are used to measure the movement of the roller mill. These sensors ensure efficient juice extraction and prevent roll wear. Following extraction, the cane juice is cleaned while the remaining fiber is transported to the boilers to be used as fuel. Pepperl+Fuchs AS-Interface components control the valves that must be opened to transfer clean juice into steam-heated evaporators. These huge metal drums boil off water to produce a thick, sugary syrup. AS-Interface analog modules receive signals from temperature measurement and limit detection technologies in this stage. The steam produced during the boiling process provides power for other parts of the plant, while AS-Interface infrastructure monitors valve position to ensure that the correct valves open to direct the syrup to distillation to produce ethanol or to crystallization to produce raw sugar.
During crystallization, AS-Interface can be applied to receive digital and analog signals from machines like vacuum pans and sugar centrifuges. In the distillery, AS-Interface analog and sensor modules are used to receive signals that indicate tank temperature, tank level, and valve position. Since many of the production stages in distillation are hazardous, distilleries rely on NAMUR sensors to detect valve position and intrinsic safety barriers to ensure process safety during fermentation and distillation of cane juice.
Growing the Industry´s Future
As the sugarcane industry has become more automated, Pepperl+Fuchs in Brazil has grown to meet the demand for advanced sensor technology. “We started out with only three employees,” says Marilia Ferraioli Makarowits, Marketing Coordinator for Pepperl+Fuchs Brazil, “but sales have increased in the past few years, and now we have almost 50 employees working in process automation, factory automation, and central services, in addition to more than 60 sales channels.” To accommodate this growth, Pepperl+Fuchs Brazil moved its headquarters to a larger office space in 2018. As the team and sales channels continue to grow, Pepperl+Fuchs Brazil will be able to provide greater productivity, reliability, and safety to the sugarcane industry and others in the coming years.
In the sugarcane industry in particular, the Pepperl+Fuchs Brazil team is working to introduce enhanced online diagnostics, new variables for tracking and tracing goods, and real-time data on a larger scale. With the help of Pepperl+Fuchs technology, one of the largest single exporters of sugar and sugarcane ethanol in Brazil has made processes smarter. The company now monitors its 26 plants from its headquarters in São Paulo. “If a valve needs to be opened at a plant in another state, operating personnel can initiate the action from the company´s headquarters in São Paulo,” says Lucas Santos. The Pepperl+Fuchs Brazil team is also working on setting up an RFID-based system that will track sugarcane by type, lot, origin, and planting date during transport. Rafaela Franca, Product Specialist for Factory Automation at Pepperl+Fuchs Brazil, says “RFID technology will make transporting cane much more reliable and will be an efficient replacement for the paper logs that are currently used.” A chute level measurement solution designed to measure the presence of cane entering milling rollers is also in the works.
Just as the price of sugar and ethanol changes, so too will the needs of the industry. But, with Pepperl+Fuchs´ flexible technologies and support for innovation across Brazil, the sugarcane industry will continue to make the world a little sweeter by sustainably and efficiently producing and distributing products across the globe.