January 27, 2022
Automation and Digitalization Taking Us toward Climate Neutrality
We spoke to Dr. Gunther Kegel, CEO of Pepperl+Fuchs SE, to discuss sustainability and climate neutrality, as well as the current developments and challenges facing the automation industry and Pepperl+Fuchs over the coming years.
The topics of energy efficiency and climate neutrality are probably the defining mission of our time and confront us every way we turn—in the media, when buying large household appliances or new cars, and in industry and politics. COP26, the UN Climate Change Conference, in Glasgow, Scotland, where representatives from some 200 countries met to renegotiate targets and ways to limit global warming to 1.5 degrees Celsius, has just drawn to a close. Political parameters, social pressure, economic interests, changing customer expectations, new insights from research and development—all of them impact the climate tipping point. Most industries have long understood the need to act and are already drawing up action and investment plans with the aim of carbon-neutral production.
KegelFirst of all, we must be clear that transforming our economy and society into a sustainable circular economy with renewable power as the dominant energy source is not only necessary for maintaining a climate conducive to life. According to experts, around ten to eleven billion people will be living on this planet by 2050. The prosperity and quality of life for all these people can no longer be achieved using non-renewable resources. For the majority of people living in economic emerging countries like India, Africa, or China, the narrative of 'doing without' is not sustainable. After all, these people all want to achieve the prosperity enjoyed by Western countries. 'Doing without' also means a decline in gross value added and therefore a decline in social products. Meanwhile, the costs of restructuring society and the economy can only be paid for by growing prosperity—i.e., by growing economic output. The only solution is therefore to use innovation to secure growth and prosperity in a sustainable society and economy. Let us imagine that the ten billion people in 2050 want to be as mobile as today's societies in the industrialized countries. In 2050, a good five billion vehicles could be driven on this planet, compared to today's 1.3 billion. These vehicles will need to be made of virtually 100 % recycled material and only use electricity from renewable sources. The electric motor is two and a half times more efficient than an internal combustion engine—we are therefore dramatically increasing the energy efficiency of mobility. And this is precisely the mission faced by all other sectors: industry, construction, agriculture, trade and services, etc. Electrification and energy efficiency are the levers of the all-electric-society.
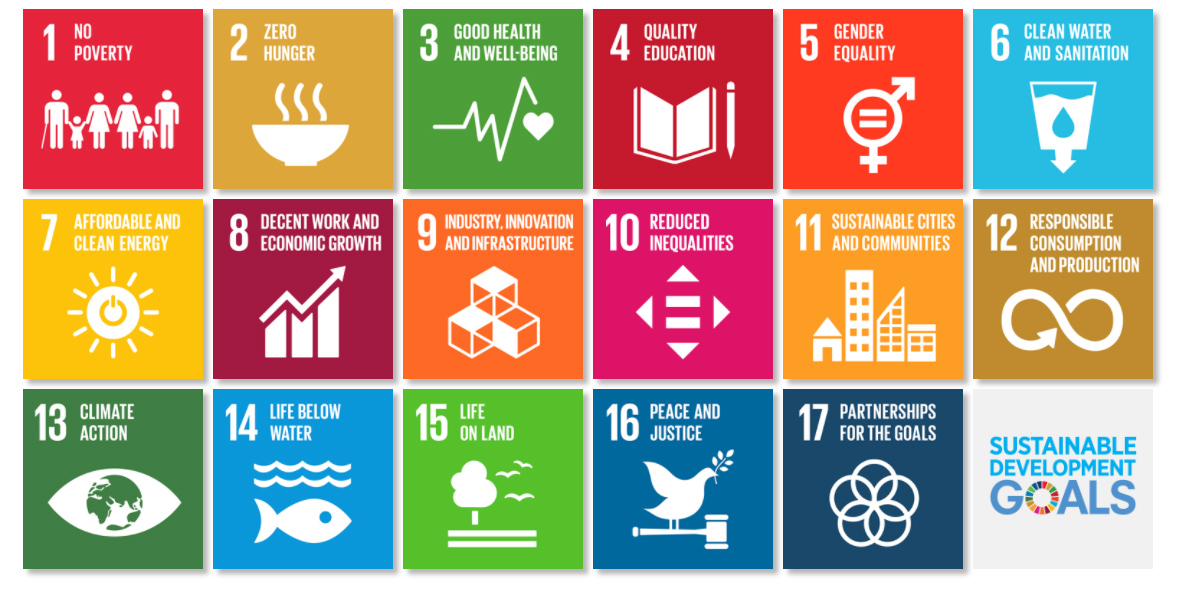
The transformation of society and economy towards a sustainable circular economy can only be achieved through growing prosperity and growing economic output. The 17 indicators of sustainability and prosperity of the United Nations Sustainable Development Goals, 2021.
KegelI want to cite a few examples. In 2019, our combustion engine fleet consumed around 500 terawatt hours (TWh) of fossil fuels in Germany alone. The same amount of driving could have been achieved with just 220 TWh of electricity. In buildings, an air heat pump is five times more efficient. 500 TWh of burned gas could therefore be replaced by 100 TWh of electricity. Suitable technologies can be employed in industry to realize significant reductions in energy consumption. In manufacturing, 40 % of the energy is consumed in electric motors, machinery, conveyor belts, etc. If all installed motors were to be replaced with the latest, energy-efficient servo drives and integrated into intelligent automation solutions, more than 80 % of the motors' energy consumption could be saved. That would equate to 32 % in savings for the manufacturing industry. Think of a conventional conveyor belt: few conveyed products move on the belt yet the entire conveyor belt, possibly hundreds of meters long, still moves. If the belt is divided into small autonomous sections, only the parts that must transport a conveyed product will move. This division makes savings of up to 90 % in energy possible. To synchronize the small conveyor sections and to identify transport materials, material handling manufacturers already use our RFID and AS-Interface system solutions.
KegelOur innovations form part of today's sustainable, energy-saving solutions in all areas of industry. Our products play only a very minor role in contributing to energy consumption. We are talking about 24 volts and a few milliamp in our sensors and isolators. Designing low-performance electronics is basically in our DNA. We have always been a tiny part of the problem but contributed greatly to the solution. The challenge is to automate new machinery and plants—to be both electrical, digital, and energy-efficient—for our customers. Whether our customers are in the chemical, metal, packaging, intralogistics, or automotive industries, supplying them with the right products for electrification and energy efficiency is the biggest and most direct factor we have.
KegelThe products and systems that we can integrate into our customers' energy-efficient plants stand out due to their generally improved functionality, efficiency, and reliability. However, we should view them as an enabling technology for energy-efficient and resource-efficient production processes. To achieve improved energy efficiency, it makes no sense to replace only the sensor technology in an old and outdated plant. The plant and its automation need to undergo a complete overhaul to enhance the efficiency potential.
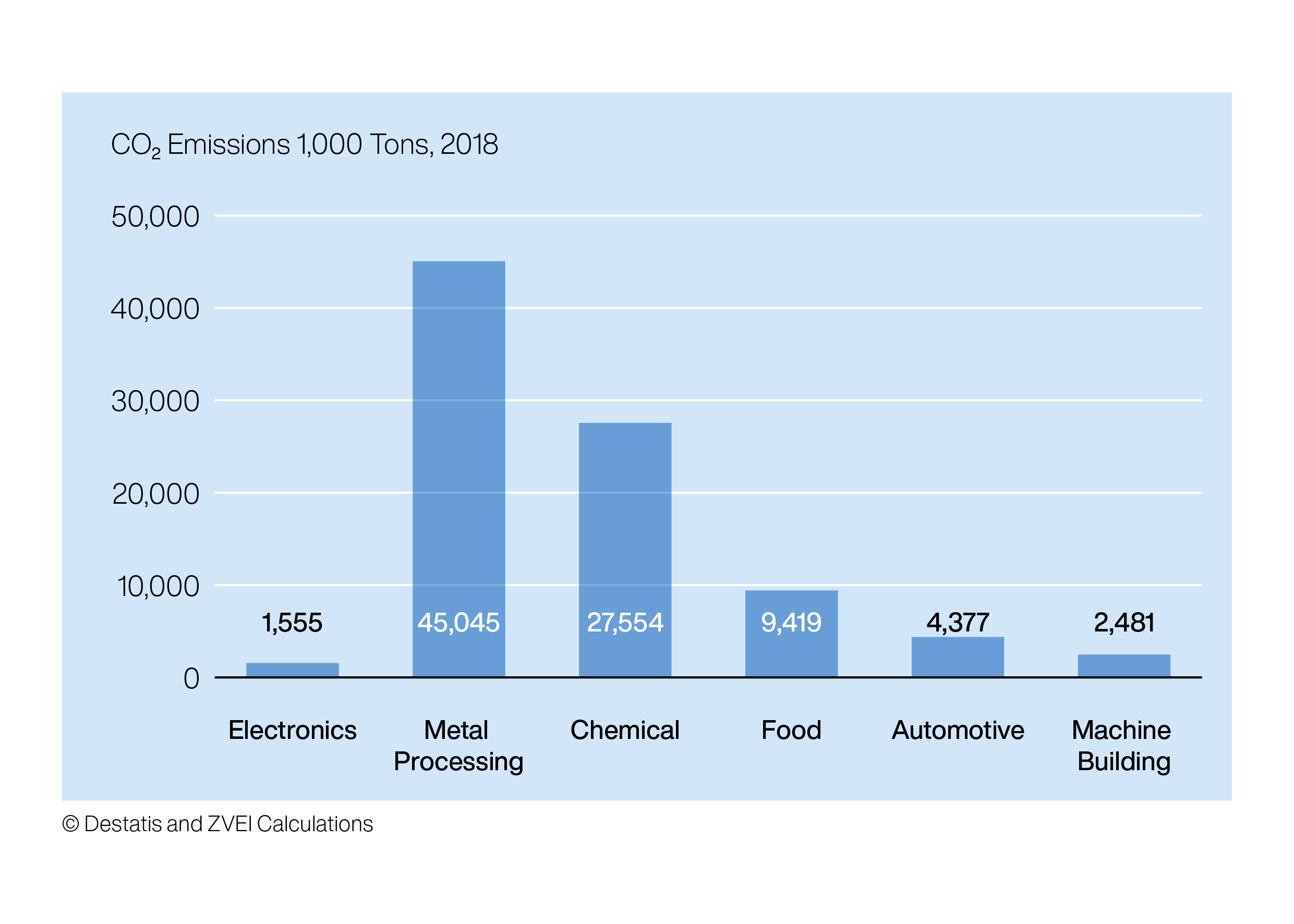
CO2 emissions broken down by industrial sector in Germany (source: Destatis and ZVEI). The share of the electronic industry in CO2 emissions is negligible compared to the metal or chemical industry.
KegelClimate neutrality will only be achieved by developing three major tracks: comprehensive electrification, the expansion of renewable energy carriers, and increased energy efficiency. Automation and digitalization are needed to make plants more energy-efficient. If you want to intelligently couple the energy production and energy consumption sectors, both worlds must first be digitized. The consumer can automatically negotiate his energy requirements with the producer and could therefore see significant flattening of any consumption peaks. Industry 4.0 is essential for this.
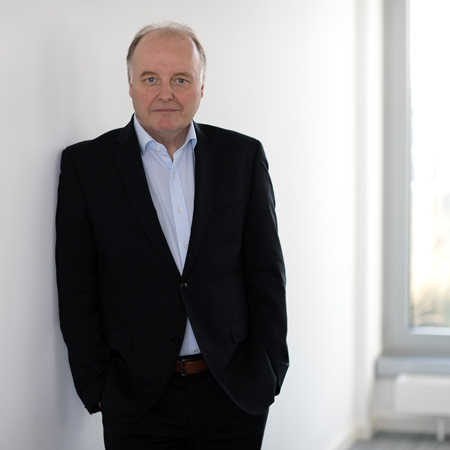
KegelTransforming energy production has an entirely separate and more pressing issue: planning and approval processes—especially here in Germany—take far too long. We cannot forge ahead with the planned wind capacity and pipeline extension due to the corresponding approvals sometimes taking several years.
KegelLet's not start singing the swansong of oil and gas until sufficient alternatives become available. Otherwise, we would be too quick to reduce capacity and would experience a real explosion in oil and gas prices, as at present. Hydrogen and power-to-liquid procedures play a major role in the German government's climate goals—all potential applications for our explosion-protection solutions and also sensors such as valve position feedback and identification systems are in use there. Business for process automation will continue to grow for some time in the field of standard explosion isolators. The more hydrogen electrolyzers and refineries are built for synthetic fuel, the more business will be created for us.
KegelOil and gas are transitory technologies, which are gradually being replaced as energy sources by electric energy sources, hydrogen, biogas, and synthetic fuels. Our products are being increasingly put to use during this changeover. We do not need a specially developed 'green' product. For the sensor or the 2-wire Ethernet technology, it does not matter whether they are used in a conventional plant with high CO2 emissions or in a plant for hydrogen electrolysis. However, the requirements of the new, green machines, plants, and processes will create new requirements for the functionality of our products, systems, and solutions in the future. The actual carbon footprint of our products plays such a minor role.
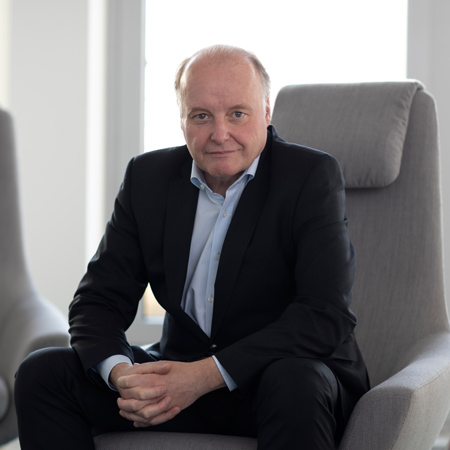
KegelIn the chemical industry, almost half of fossil fuels are used as a raw material for producing products. And the carbon usually remains bound in these products. It is technically possible to replace basic fossil products with renewable, organic raw materials, but this is not yet available at large-scale plant level. However, at the moment it seems better to completely recycle the resulting products. Doing so further reduces the need for gas and oil as a raw material. These fossil energy sources can be replaced in their entirety in many ways. The thermal processes can be directly electrified. The gas can be replaced by green hydrogen, or the renewable energy is used in power-to-liquid procedures to produce synthetic fuels. These options are possible but rarely implemented in large-scale plants, partly due to the cost of electricity. The transformation costs and challenges are much greater for these industries than for us in the electro industry. However, we, as automation specialists, need to work closely with our customers to develop new energy-efficient solutions together. Without our major users, we cannot make a measurable contribution to climate protection alone. Our proximity to the major chemical and pharmaceutical companies is crucial to our innovative strength.
KegelWhether in direct form, as hydrogen, or as a power-to-liquid, renewable electricity is a vital factor on the way to becoming carbon neutral. In Germany, the aim is for around 2000 TWh to come from renewable sources by 2050—precisely eight times as much as today. In addition, we want to buy 600 TWh from overseas in the form of hydrogen and power-to-liquid. This requires corresponding renewable electricity capacities all over the world. This represents a huge opportunity for us. Our businesses will grow along these expansion scenarios. We can therefore certainly triple our revenue in the wind energy and photovoltaics sector. We see great potential with our products along the entire hydrogen value chain, starting with energy generation, electrolysis, storage and transport, and ending with hydrogen filling stations and industrial applications.

Renewable energies, hydrogen and power-to-X processes are the building blocks of ecological transformation—and they are all potential applications for our explosion protection and sensor solutions.
KegelWe are, thankfully, much more part of the solution than the problem. Our worldwide production facilities and distribution centers are state-of-the-art and equipped with efficient automation solutions. At Pepperl+Fuchs, the majority of greenhouse gases listed in Greenhouse Gas Protocol emissions categories (scopes) 1 and 2 are accounted for by the diesel fuel from our service vehicle fleet and gas-fired heating plants. We have a few possible fields of action here. In the future, we will contribute more to the collection and recycling of our products. All components used in our products are recyclable and should be recycled. And we are drawing up the documentation on how to use materials. The recycling factor will need to be taken into account in our future development and construction processes.
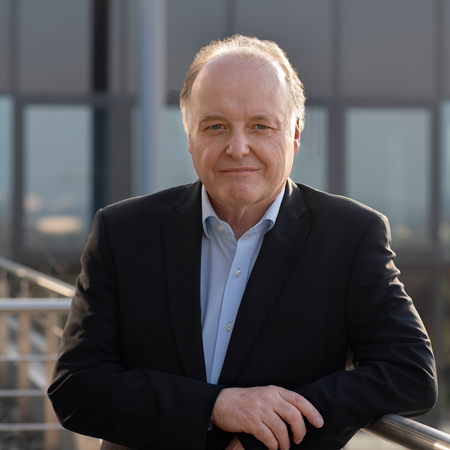
KegelYes, we are currently drawing up a 'Digital Agenda 2.0' and a 'Sustainability Agenda 1.0,' which lays out the CO2 emission and other targets. We want to generate our first sustainability report by the end of this year. The agenda is actually easy to define: This includes the conversion of all electricity contracts to 'green' electricity, the installation of charging stands on the factory premises, as well as switching leasing contracts for company vehicles to e-mobility. We would like to maintain the few positive effects that the Covid crisis has brought us, namely that online meetings can reduce air travel and business trips in the future. Wherever possible, our gas heating systems should be converted to heat pumps and, of course, the energetic refurbishment of our properties will also play a role. I am certain that we will achieve a good part of our targets over the next 15 years.
KegelThere are indeed. One example are the operating instructions that accompany each individual product. Last year we started to replace these instruction leaflets for the first product line with a lasered QR code on the sensor and on the packaging label so that all information can be called up digitally. If a customer orders one hundred devices from this series for his system, he normally only needs the instruction leaflet once and not a hundred times, the rest of the paper ends up in the garbage. This enabled us to save around eight tons of paper in 2021 with just one product line—and it takes an average of 24 trees and large amounts of water to produce one ton of paper. In addition, we reduce a not inconsiderable amount of paper waste on the customer side. Our goal is to gradually provide the instruction leaflets for all product lines only in digital form.
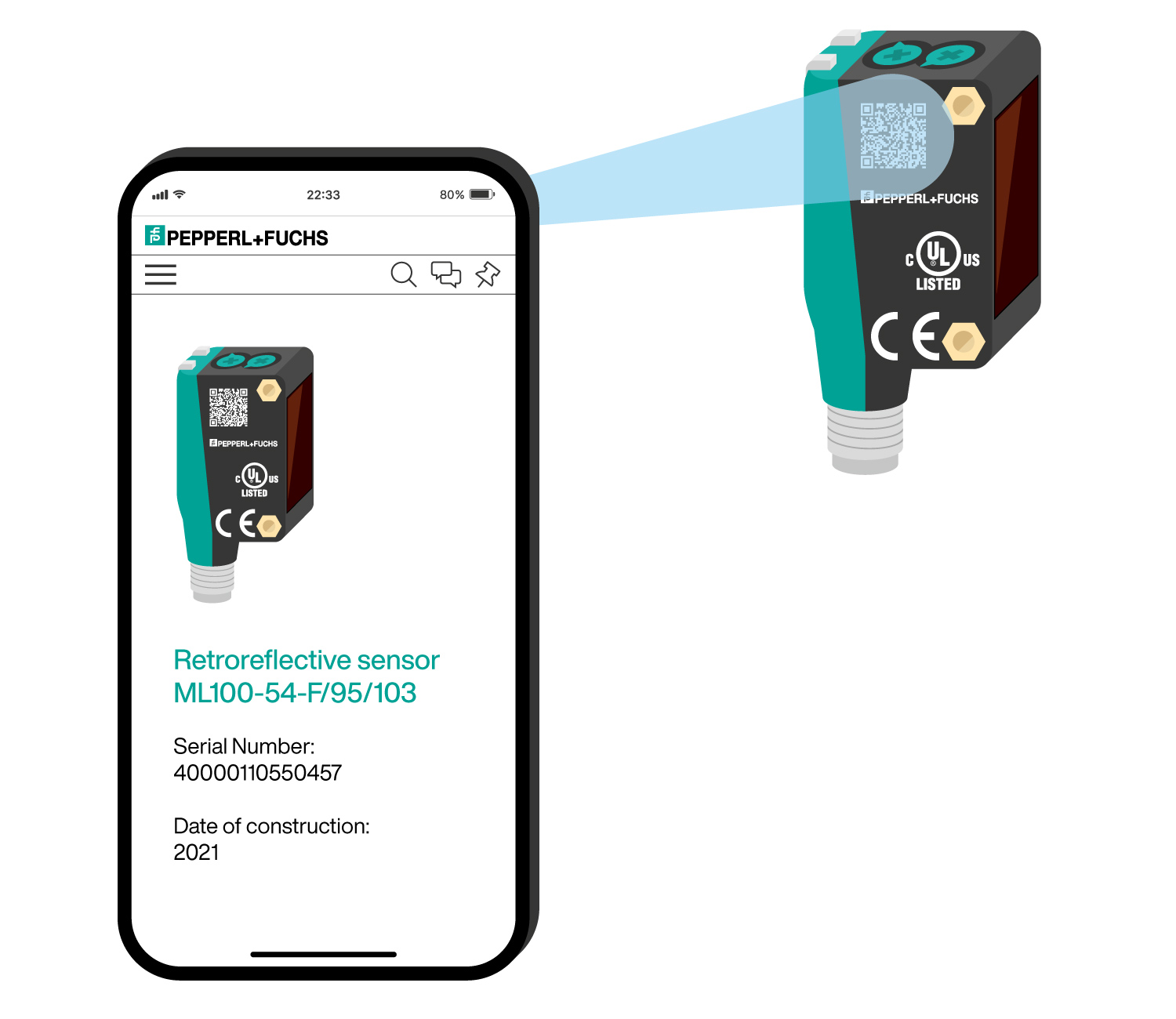
The user can call up all sensor information such as data sheet and operating instructions digitally via the digital type code, a lasered QR code on the sensor.
KegelYes, we will. The challenges for us are comparatively small. The much bigger factor for us is always working closely with our customers. But we, too, will play out part.