November 28, 2022
Every Package at a Glance
Identifying the utilization of conveyor belts at any time: Together with a customer, Pepperl+Fuchs has developed the Contour2D sensor system to carry out this task. A single state-of-the-art LiDAR sensor combined with an intelligent control interface allows efficient monitoring of conveyor system utilization.
Package volumes around the world are continually increasing. More than 131 billion packages were sent in 2020, a figure that is predicted to double by 2026. For intralogistics, this poses the challenge of coping with ever larger quantities of packages. A leading supplier of material flow systems turned to Pepperl+Fuchs in search of a solution that would enable them to monitor the utilization of conveyor belts at all times. To achieve this, Pepperl+Fuchs worked closely with the customer to develop the Contour2D sensor system. With this system, which is now available to everyone in the material handling and intralogistics industries, the utilization of a conveyor system can be monitored more efficiently than ever before.
‘In the customer-specific application for which we developed the sensor system, we found ourselves at a distribution center where trucks were depositing entire loads full of packages onto conveyor belts,’ explains Marcel Tibosch. As Sales Manager for the Factory Automation division in the Netherlands, he was the first point of contact for the loyal Pepperl+Fuchs customer. The Dutch conveyor system manufacturer was looking for a solution for monitoring conveyor belt utilization for a world-leading e-commerce company.
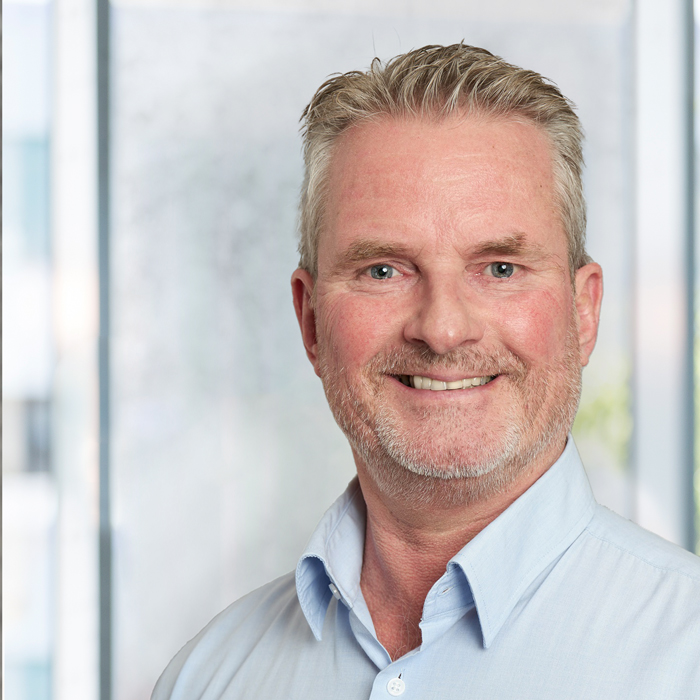
The e-commerce company’s conveyor belts handle a large number of packages of different sizes, with different types of packaging. These packages are unsorted, arrive in large quantities, and are sometimes stacked on top of each other. ‘The customer was therefore looking for a solution that would provide an overview of the current utilization of the conveyor belt at any time,’ reports Marcel Tibosch. This information is essential to keep the flow of packages running smoothly and to ensure that individual packages are distributed at regular intervals.
Turnkey Systems for Specific Challenges
To find an optimal solution for this specific challenge, Tibosch turned to the Pepperl+Fuchs Smart Systems department, which develops turnkey systems for practical problems in various applications. Project engineer Patrick Ukas’s team looked at how the customer’s task could best be solved using products, technologies, and expertise from Pepperl+Fuchs. ‘What makes monitoring conveyor belt utilization especially difficult is the shadows that occur on the belt,’ Ukas reports. ‘That was the technical challenge we needed to find the most efficient solution for.’

The problem is that packages transported along a conveyor belt cast a shadow on the belt, making their contours appear larger than they are. To compensate for this effect, existing solutions use several laser scanners that look at the conveyor belt from different sides. However, these solutions are highly expensive, both to purchase and to install. “Our goal was to use only a single LiDAR sensor mounted over the center of the conveyor belt,” says Ukas. The customer benefits from reduced hardware costs and reduced installation and commissioning time. In contrast to other systems, there is no need for the complex configuration required to align multiple sensors with each other
Using a Single Sensor to Combat the Effect of Shadows
But how did the sensor specialists at Pepperl+Fuchs manage to develop a system that compensates for the effect of shadows on the conveyor belt using only one sensor? ‘To achieve this, the outstanding performance of the R2000 2-D LiDAR sensor was crucial,’ explains Ukas. In comparison to similar products, the sensor at the heart of the Contour2D system has the highest possible angular resolution of 0.042° and an especially high scan rate of up to 50 Hz. This allows the R2000 to detect the contours of the packages on the conveyor belt with maximum precision.
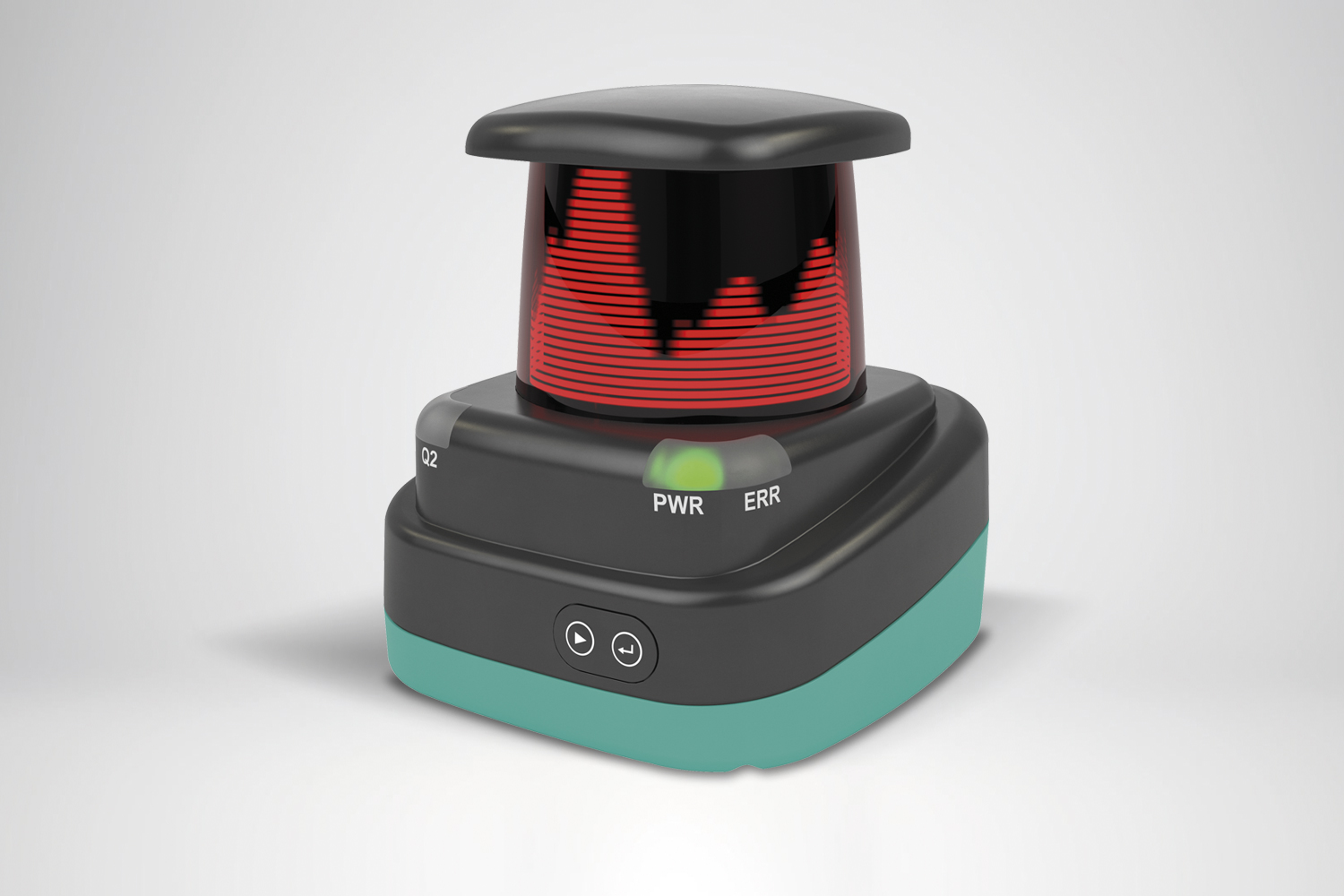
An angular resolution of 0.042° and a scan rate of up to 50 Hz make the R2000 2-D LiDAR sensor a precision pro.
From the beginning, however, it was clear that powerful sensor technology alone was not sufficient to compensate for the effect of shadows on the conveyor belt. “We also needed to develop an intelligent control interface, which is why we brought the software experts from Espace 6D on board,” Ukas says. As part of VMT, a Pepperl+Fuchs company, Espace 6D is a hub for in-house expertise in 3-D measurement technology, laser scanners, and software development. “For Contour2D, we developed application-specific algorithms that reliably calculate the effect of shadows on the conveyor belt, so that we can accurately capture the contours of the packages using just one sensor,” explains Dr. Adrian Krzizok, Head of Software Development at VMT/Espace 6D.

Powerful sensor technology and intelligent algorithms mean that the effect of shadows on the conveyor belt is no problem for Contour2D.
All Characteristic Values in One Application
However, software development for Contour2D was not just about compensating for the effect of shadows. In addition, further customer-specific requirements had to be considered, as Krzizok summarizes: ‘Our software processes and interprets the raw data of the sensor to output four characteristic values: The proportion of the conveyor belt that is occupied, the average height of the transported goods, the maximum height of the transported goods, and a height profile.’ The software is integrated in the control interface, which is installed near the conveyor system. At the customer’s request, the measurement results are forwarded directly to the PLC via a TCP/IP interface. They can be visualized graphically in a Windows application at the same time.
Another important requirement was that the system should be quick and easy to commission. The experts at Espace 6D therefore developed an intuitive Windows application, in which Contour2D can be easily configured—from adjusting the sensing range to teaching in the conveyor belt contour. The set values can then be transferred from one system to another. “If a total of 150 Contour2D systems are used in one hall, only one of these systems has to be set up,” explains Krzizok.
Won over by a Complete System
‘The convenient, easy-to-use software was one of the reasons why the sensor system from Pepperl+Fuchs won the contract over other offers,’ Sales Manager Marcel Tibosch reports directly from the customer. ‘Contour2D impressed the customer because it is a complete system that combines sensor technology for measurement with software for analysis and visualization—while being cost-effective and easy to install at the same time.’

Looking back on the customer project, software expert Adrian Krzizok strongly emphasizes that: “The development of the sensor system and the findings gained from it will also benefit future customer projects.” In recent years, Pepperl+Fuchs has received more and more requests for custom solutions. To enable such projects to be implemented quickly and cost-effectively, core software with basic interfaces and algorithms is required. “This means that new sensors can be connected without too much effort and application-specific requirements can be met. Further custom orders are already benefiting from the basic software we developed for Contour2D.”
Growing Popularity
From Tibosch’s point of view, the Contour2D project was a complete success: ‘The customer reported that the sensor system works perfectly for the application.’ Since spring 2021, around 150 Contour2D systems have been in daily use in a large distribution center of the e-commerce company. ‘In addition, we have already received several repeat orders for different locations and expect demand to continue to grow.’
Contour2D is now available for any company that wants to use the sensor system from Pepperl+Fuchs to get a better overview of how its conveyor belts or roller conveyors are being utilized. Thanks to the in-house modular software platform, individual customization is also possible. ‘Whether different output messages or varying output sizes are required,’ says project engineer Patrick Ukas, ‘we’re looking forward to discussing it with our customers!’