February 3, 2023
Into the Future with Hydrogen—Electrifying and Sustainable
Green hydrogen is considered a source of hope in the decarbonization of industry and heavy-duty vehicles. Alongside the climate crisis, the current energy crisis is providing an additional boost to the development of green hydrogen as a sustainable energy carrier. Suitable sensor technology and components for electrical explosion protection are available for use in the hydrogen value chain.
The guiding principle of a healthy economy is growth, and growth means increased demand for energy. ‘It is precisely this increased energy requirement that should be broken down by electrification. This means that we need more electricity, but the overall energy balance should be reduced,’ explains Wolfgang Weber, Global Industry Manager for Renewable Energies at Pepperl+Fuchs. ‘What may sound paradoxical at first glance can be explained with a simple example: In a diesel-powered vehicle, the efficiency factor is around 40 %, while in battery-powered vehicles, it is around 80 % or higher. We are currently treading the path to an all-electric society, and coupled with the target of climate neutrality, this means there is huge demand for renewable energy carriers in the sense of a sustainable circular economy,’ explains Weber. Two decisive steps are paving the way for this: A significant increase in energy efficiency through automation and digitalization, and the production of green hydrogen as a main energy carrier, obtained from renewable sources such as wind power, photovoltaics, and hydropower.
There Are Significant Challenges
Green hydrogen is regarded as the key to the decarbonization of industry and heavy-duty vehicles, and a source of hope in the climate crisis. Until the energy policy objectives of climate neutrality and the necessary development of renewable energy production are achieved, gas should act as a transitory technology. However, the growing energy crisis caused by the shortage of fossil fuels—such as natural gas and oil—has thwarted this plan. Especially for energy-intensive production companies, such as chemical companies, steel and aluminum producers, porcelain and paper manufacturers, to name just a few, it becomes critical if there is not enough energy available for production or if, due to the current development of energy market prices, production costs for some companies become a matter of existence.
‘It is unlikely that we will be able to push ahead with the production of green hydrogen to the extent or level of urgency unless there is rapid relief or even a turnaround in this economic and ecological crisis. There is no shortage of lead projects and certainly no lack of technical expertise, but rather of timely implementation,’ says Weber, describing the current situation.
Major hydrogen projects have been launched worldwide, such as in Canada, Europe, Japan, New Zealand, and Australia. However, for the large-scale production and industrial use of green hydrogen, the development of renewable energy production must be promoted first and foremost—whether it be wind power, solar power, or hydropower. ‘For the most part, offshore wind turbines should provide the green electricity required. In sunnier regions, such as Spain and Australia, photovoltaic systems are used. Last but not least, the green electricity produced must be converted into hydrogen and transported or stored in intermediate storage,’ explains Weber.
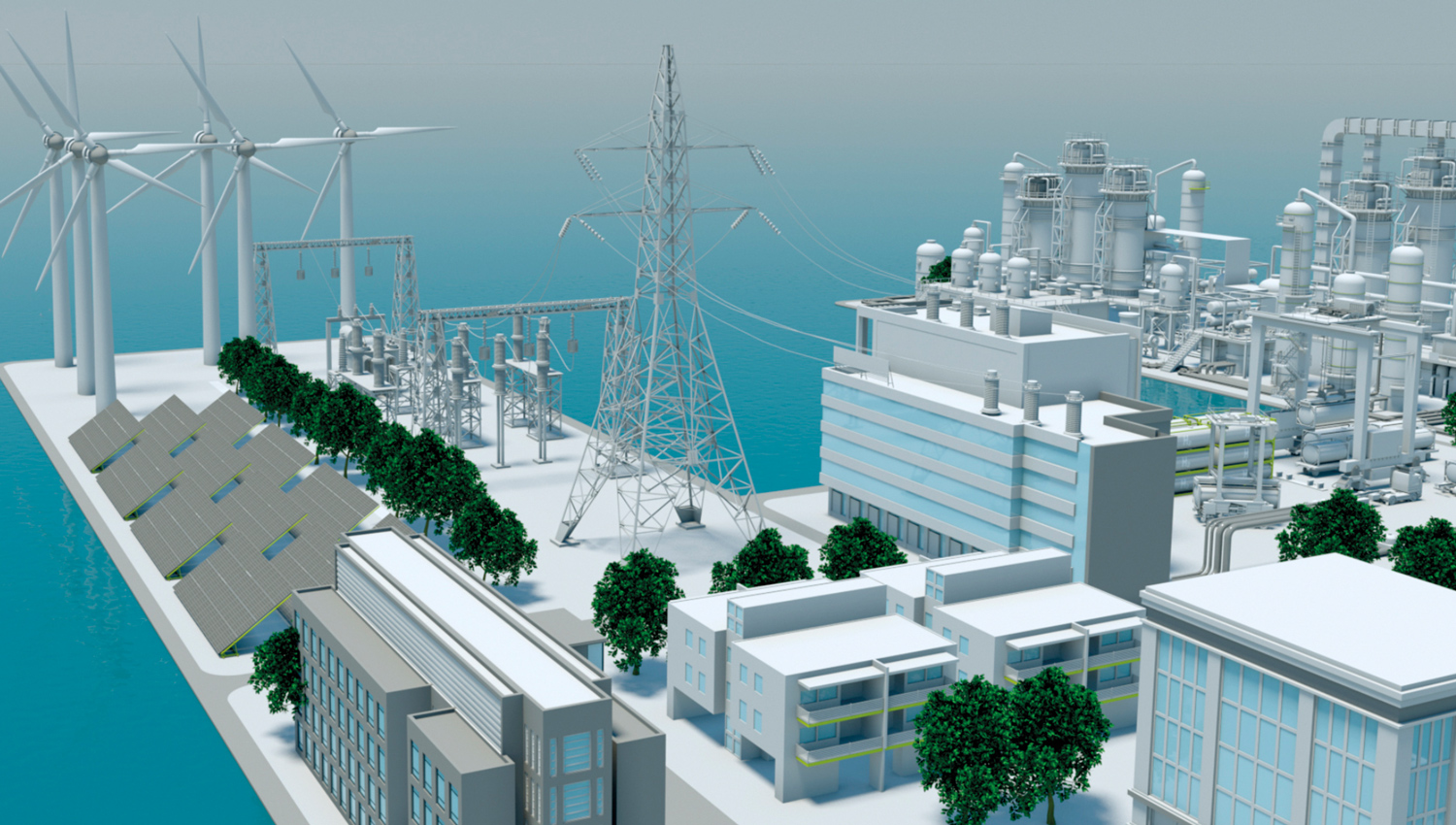
For the large-scale production and industrial use of green hydrogen, the most important thing is the expansion of renewable energy generation.
Pepperl+Fuchs offers suitable industrial sensors and components for electrical explosion protection for renewable energy production, and the transport and storage of hydrogen. “Our automation products are, so to speak, just waiting for the major starting point in the large-scale development of the hydrogen value chain,” adds Weber, with a wink. “Of course, Pepperl+Fuchs is also represented in various committees and working groups on the subject of hydrogen, for example at the VDMA e. V. (Verband Deutscher Maschinen- und Anlagenbau—German Mechanical Engineering Industry Association). As a specialist in sensor technology and explosion protection, we also maintain close links with research, including the Fraunhofer Institute and other hydrogen research projects,” says Weber, describing current developments.
Using Wind Power Efficiently
The best conditions for wind turbines prevail far out at sea, because wind blows continuously and it is much stronger than on land. According to the German Federal Ministry of Education and Research (BMBF), which launched the H2Mare lead project for research into the offshore production of green hydrogen, the average nominal power of land-based wind turbines is only around 3.5 megawatts, whereas the nominal power of offshore turbines is 5 megawatts, and rising.
Appropriate sensor technology is required to get the most out of wind energy. ‘For optimal wind yield, the rotor blades must rotate with the changing wind, and they must have the optimal inclination angle depending on the wind strength; the hub must be positioned facing into the wind,’ explains Weber. To adjust these efficiently, the controller must determine the current position of the hub and rotor blades. Absolute rotary encoders, such as those in the ENA58 series from Pepperl+Fuchs, are responsible for pitch and horizontal control.
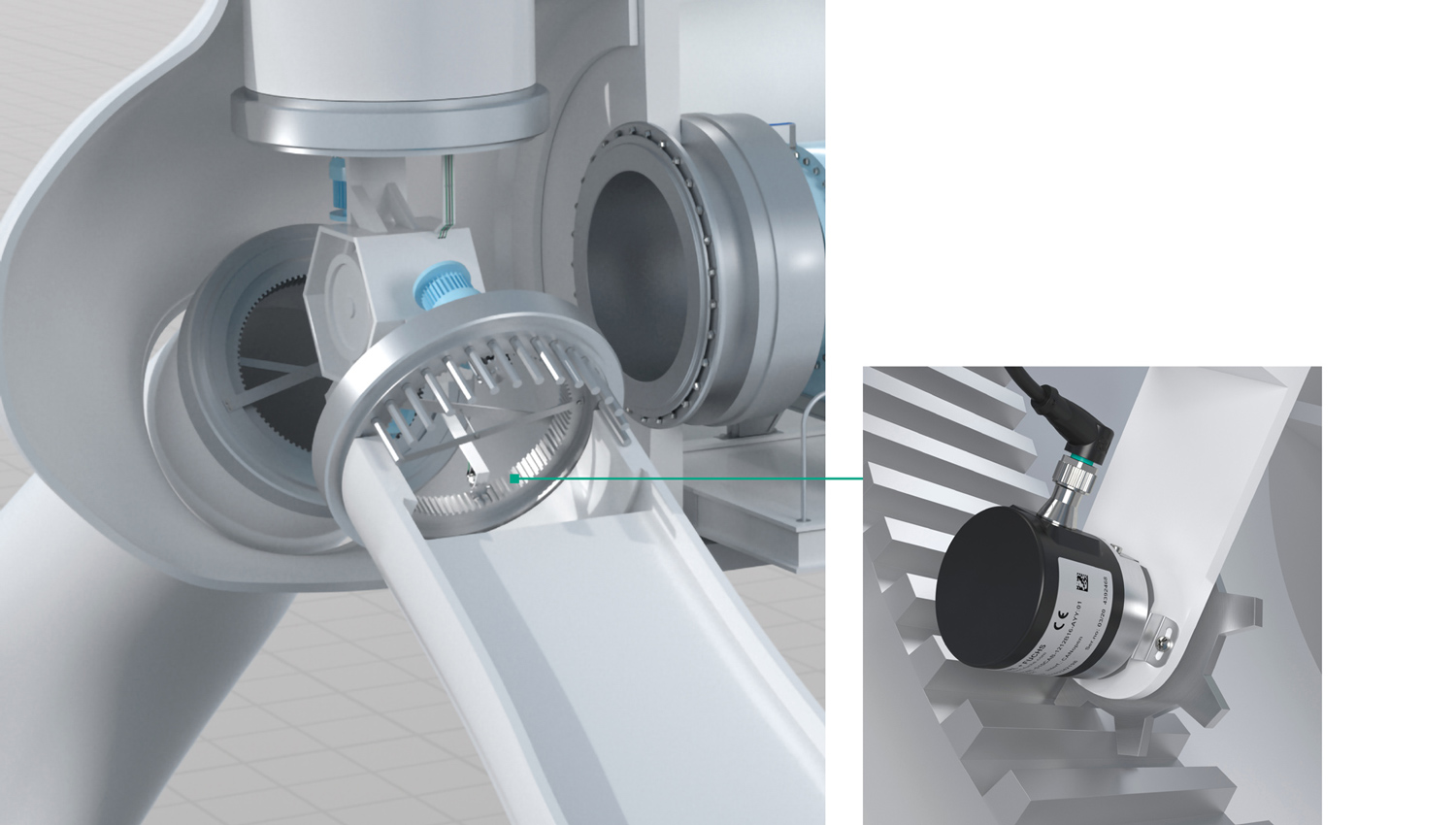
The ENA58 absolute rotary encoders from Pepperl+Fuchs ensure the optimal position of the rotor blades at pitch control in wind turbines.
Condition Monitoring of Wind Turbines
‘Wind power on the high seas can be very strong, and sometimes components must be moved into a protective position to avoid an impending overload. Condition monitoring of the wind turbine and individual components is essential for safe operation,’ says Weber. VIM series vibration sensors from Pepperl+Fuchs reliably monitor long-term vibration changes, while F99 series acceleration sensors detect short-term vibration changes. The F99 acceleration sensor measures nacelle vibration, while the VIM vibration sensor monitors the condition of the rotating components inside the nacelle, such as the vibrations of the generator shaft, and the shaft and hub connection. Combined together, both sensing modes reliably monitor the displacement of the nacelle and the condition of the system under the influence of wind.
Vibration sensors in the VIM8 series are approved up to SIL 2/PL d, have a wide measuring range up to 128 mm/s, and automatic status detection for ball bearings, meaning they are ideally suited for use in wind turbines. ‘The detection of long-term changes in vibration velocity or acceleration enables predictive and targeted maintenance. This saves the wind turbine operators both time and money, since offshore turbines cannot always be reached quickly for service operations,’ adds Weber.
One of the most common causes of electronic damage is overvoltage caused by lightning strikes or switching events. These can be a hazard to and lead to the failure of the entire system, which must be avoided. Surge protection modules from Pepperl+Fuchs protect control technology, signal transmission lines, and supply lines.
The Required Level of Safety for Transporting Hydrogen
The exact level of demand for green hydrogen that industrialized nations require to produce in a climate-neutral manner has not yet been defined. What is certain, however, is that the energy requirements of some countries will be several times higher than the amount they can produce themselves in terms of green hydrogen quantities. ‘Therefore, the import and export of green hydrogen will play a major role, and to do this, efficient transport infrastructures must be established,’ explains Weber.
Hydrogen is transported either by sea in gas tankers, by land in pressure cylinders in trucks, or, not least, via pipelines to industrial sites. The existing gas pipelines can also be used for the transport of hydrogen in the future, because a part of hydrogen is already bound in natural gas. It’s the mixing ratio that changes. Nevertheless, transporting hydrogen still poses some technical challenges, since its chemical properties make it highly explosive when combined with oxygen. ‘As an automation manufacturer and pioneers in electrical explosion protection, we are very familiar with the unique aspects of potentially explosive gas atmospheres, which also apply to hydrogen. Its affinity to oxygen makes the plants and means of transport in the hydrogen value chain hazardous areas that require special precautions with regard to explosion protection,’ says Thomas Schnepf, Sales Engineer for Explosion Protection and Process Automation at Pepperl+Fuchs.
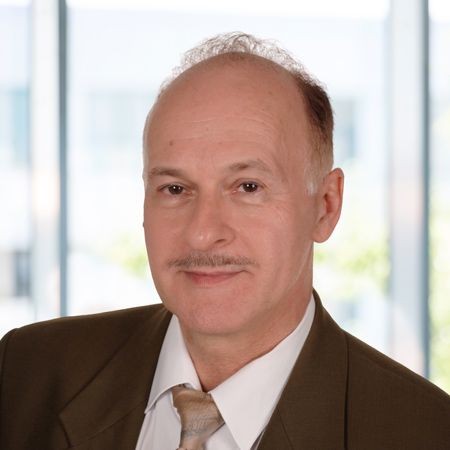
Explosion Protection in Gas Pressure Control and Measuring Systems
Hydrogen must be compressed for transport. Gas pressure control and measuring systems (GPCMS) ensure the correct pressure of the hydrogen for further transport, so that neither overpressure nor negative pressure occur. Various interface modules are used for safe signal transmission and protection against overvoltage in the GPCMS switch cabinet.
An SR series terminal box from Pepperl+Fuchs, for example, provides intrinsically safe signal distribution. Overvoltage protection modules are also used here to avoid overvoltages directly on the field device. The position of the valves within the GPCMS must also be monitored. Inductive sensors, such as the PMI position measurement system and the F31K2 dual inductive sensors from Pepperl+Fuchs—which are certified for use in hazardous areas—provide reliable feedback on the valve position.
The composition of the hydrogen is continuously monitored and analyzed. “The 6000 Series purge and pressurization system from Pepperl+Fuchs is ideal for reliably protecting devices for hydrogen analysis against the formation of an explosive gas atmosphere. It prevents the formation of an explosive gas mixture inside the enclosure or switch cabinet by purge and pressurization, therefore providing reliable explosion protection,” explains Schnepf.
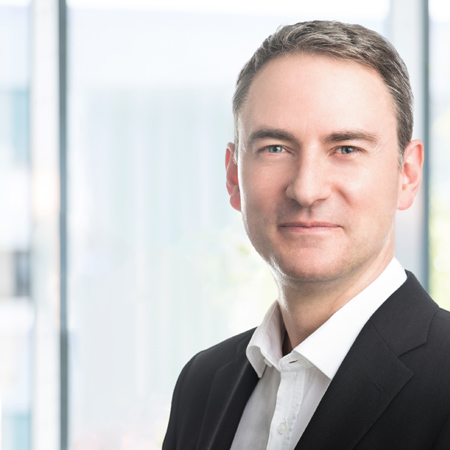
Overseas Transport—Safe Arrival at the Destination Port via Gas Tanker
In the future, large quantities of green hydrogen will cross the world’s oceans via gas tankers, whether from Canada, Africa, or Australia, and explosion protection must be ensured on board the tankers at all times. ‘Pepperl+Fuchs offers one of the largest portfolios for hazardous areas on the market and a whole range of solutions for transporting hydrogen by gas tanker,’ says Schnepf. To connect the field signals on the vessel, traditionally an LB remote I/O system—which is approved for marine applications—is installed in a rugged SR series stainless steel enclosure. But there is another way: ‘With Ethernet-APL, fast and digital data transfer with 10 Mbit/s via two-wire cable for the connection of field and control devices is entering the process industry. The Ethernet-APL rail field switch from FieldConnex® enables end-to-end digital communication from the field devices to the control system and higher-level management systems. The field devices are supplied with power via the two-wire cable, which can be routed intrinsically safe up to Zone 0. Authorized users can directly view data in real time via their smartphone. This not only speeds up planning and installation, but helps to diagnose and isolate the causes of faults. This offers a huge advantage for gas tankers, which are sometimes traveling in the middle of the ocean for days at a time,’ explains Schnepf, explaining the advantages of this modern communication technology.
To be able to operate the crane control of the gas tanker safely and reliably, Pepperl+Fuchs offers a flanged Ex de enclosure solution for electrical components that are not certified for hazardous areas. This solution combines the flameproof enclosure (Ex d) type of protection with the advantages of the increased safety type of protection (Ex e). Certified operating elements are still easily accessible in the Ex e enclosure. Pressure cylinders are identified by RFID components, which ensure accurate assignment and detection. Pepperl+Fuchs has a complete portfolio of RFID system solutions that enable communication with a PLC or other higher-level IT systems.
Monitoring Pipelines and Pipes
Once the hydrogen has arrived at the destination port or industrial plant, pipelines and pipes ensure the distribution and further transport of the hydrogen. Valves on the pipes that control the gas flow must be reliably monitored. The certified F31K2 dual inductive sensors or the inductive PMI position measurement system provide feedback on the valve position in hazardous outdoor areas. However, the inspection, servicing, and maintenance of the valves on the wide-branched and kilometer-long pipes and pipelines presents a challenge. ‘The intrinsically safe smartphone Smart-Ex® from Pepperl+Fuchs brand ecom provides mobile workers and plant operators with important information about the field devices during valve maintenance work in real time, and provide them with direct access to necessary data. For example, maintenance staff can upload the inspection report directly, or discuss the situation with a remote service technician via the smart glasses and receive technical support,’ says Schnepf, describing the advantages of modern mobile communication technologies for the process industry.
The explosion-protected components and industrial sensors required for renewable energy production and the storage and safe transport of hydrogen are already available, since the general protection measures for automated monitoring and control of industrial processes in hazardous gas atmospheres also apply to hydrogen. “In any case, as an automation manufacturer, we are ready to safely and efficiently design the processes along the entire hydrogen value chain worldwide. We have the technologies to do this,” summarizes Schnepf.
Strong Hydrogen Partnerships Worldwide
To advance the large-scale production of hydrogen and move toward climate neutrality worldwide, some countries are entering into strong partnerships in the research and development of the hydrogen value chain. In October 2022, Canada and Germany launched four major projects for the promotion of green hydrogen, including the minimization of costs in hydrogen production, the integration of hydrogen into industrial value chains, and research into advanced methods for producing hydrogen. The hydrogen agreement between Germany and Canada, signed in August 2022, aims to establish a transatlantic supply chain for green hydrogen.
A German-Australian consortium of business and science will also identify regulatory, technical, and economic obstacles to developing a supply chain along the hydrogen value chain. Together with New Zealand, Germany has also launched three projects related to hydrogen production, storage, and distribution.
In some parts of Africa, there is great potential for the production of green hydrogen, mainly from solar energy, but also from wind energy. With the Juelich research center, the German BMBF is focusing on strategic partnerships with countries in West and South Africa to meet the local energy requirements of the countries, and to be able to import hydrogen from Africa in the future.
Advances are also being made in the Far East: Japan is considered one of the pioneers in the field of hydrogen and, with Toyota and Nissan, leads the global ranking of companies in the application of patents on hydrogen in industrial applications. The Land of the Rising Sun is already working on developing a complete industrial value chain for hydrogen.