October 30, 2023
Mass Production Made to Measure
The industry is facing new challenges that arise when balancing the need for customization and cost-effectiveness. The technology service provider and electrical wholesaler Alexander Bürkle illustrates a potential solution wherein a manufacturing plant can produce batch size 1 under the conditions of mass production. An essential component of the system is the sensor technology from Pepperl+Fuchs.
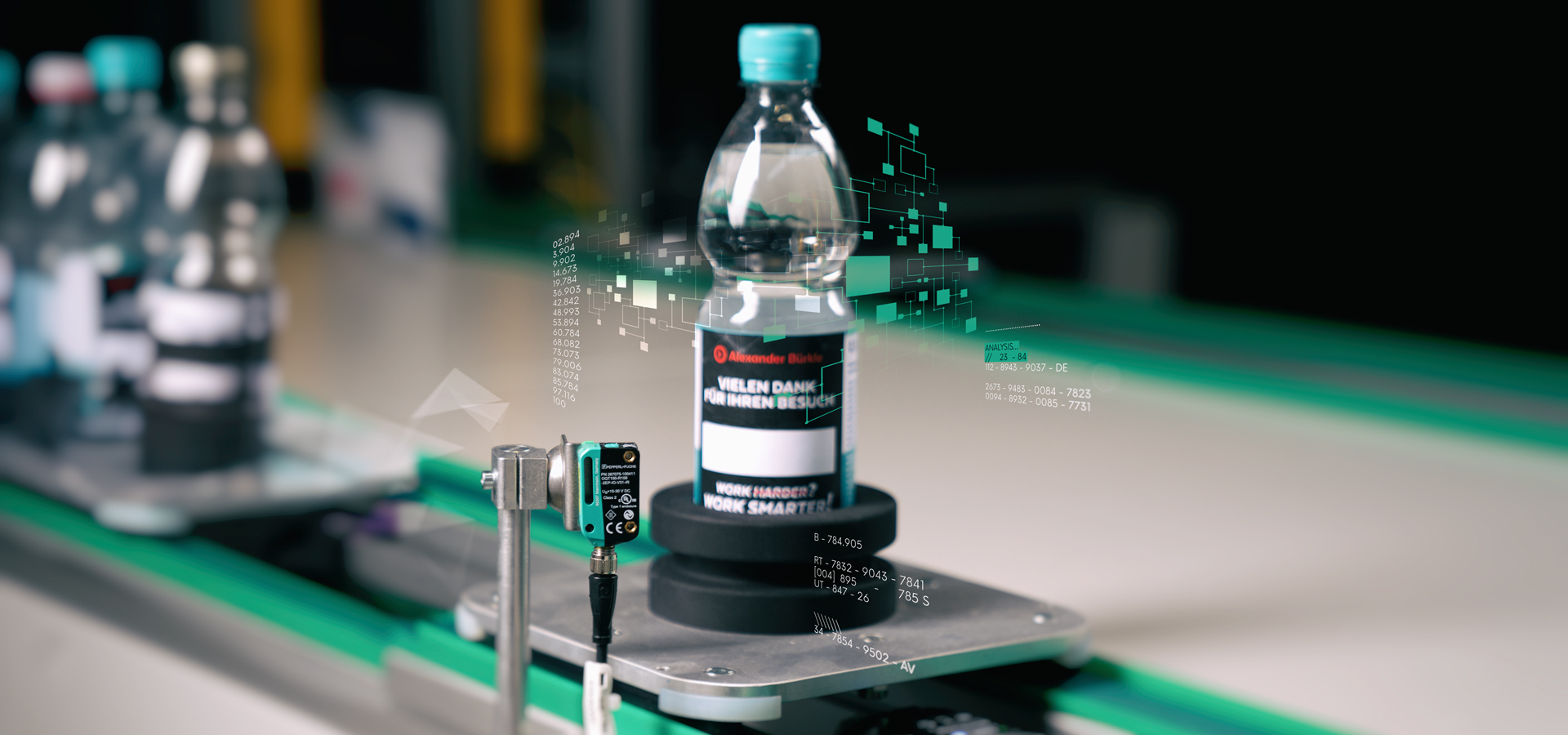
Specific customer requirements are becoming more and more important. 'Standard' is no longer standard. To meet individual customer requirements, production is increasingly being carried out on an order-by-order basis. However, this should be done to the greatest possible extent in accordance with the economic conditions of mass production, such as low costs and quick throughput times. But how can that work?
Customization and high cost-effectiveness can be achieved through innovative Industry 4.0 concepts. This allows production processes in industry to be digitalized and networked with each other.
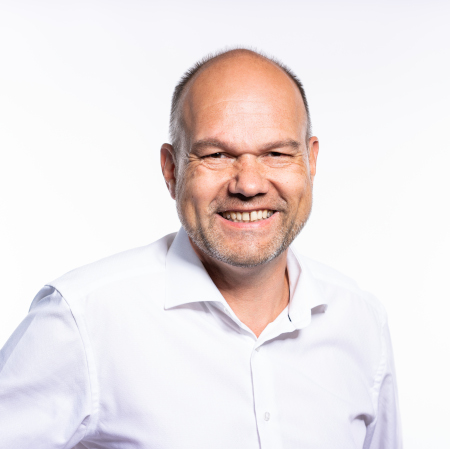
Through this networking, possible delays can be predicted, so that bottlenecks or faults can also be quickly detected and rectified. For example, robots and automated systems can help companies adapt their production lines flexibly and in real time. This allows the production lines to be individually coordinated so that production processes can be precisely planned. This also allows for more accurate forecasting of stock levels, minimizes waste, and optimizes delivery times. The concept of batch size 1 plays a decisive role here. While traditional mass production involves manufacturing a large number of products, batch size 1 is the production of a single product that exactly meets the customer's individual requirements—but under the conditions of mass production.
Batch Size 1: Personalized Water Bottles in Mass Production
As an example of a solution for 'mass production made to measure,' Alexander Bürkle presented a demo system that individually prints on water bottles as an example of a customer-specific product for the first time at electra 2022, making the entire production process transparent. The automation solution, which is not dependent on a particular manufacturer, illustrates the intelligent networking of machines, products, and people and impressively combines mass production with individual production. Visitors can order their own personalized water bottle on-site and have any text, such as their name, printed on the label. As soon as their water bottle is ready for pickup, they receive an email notification.
The production plant used as an example covers the entire electrotechnical value chain in all areas of application, from electrical design to control technology, automation to IIoT and robotics. The components in the system are networked and communicate with each other via PROFINET and IO-Link. The combination of Information Technology (IT) and Operational Technology (OT) creates a tangible, comprehensive solution. Alexander Bürkle relies on a wide variety of technologies and components from numerous manufacturers. Pepperl+Fuchs supplied the required sensor technology.
"We are very proud of the reliable cooperation we have had working with various manufacturers that makes this comprehensive solution possible in the first place," reports Bachofner. "Due to our long-term partnership and the wide range of sensor technology and components such as IO-Link masters and RFID components that Pepperl+Fuchs offers, it was only natural for us to use the products here as well as when planning the system."
Sensor Technology in Use
At the Alexander Bürkle plant, sensors and technologies from Pepperl+Fuchs ensure the reliable acquisition and transmission of production and order data in real time, therefore ensuring a smooth flow of information in the networked production environment. Custom production in large quantities requires the highest reliability of all components.
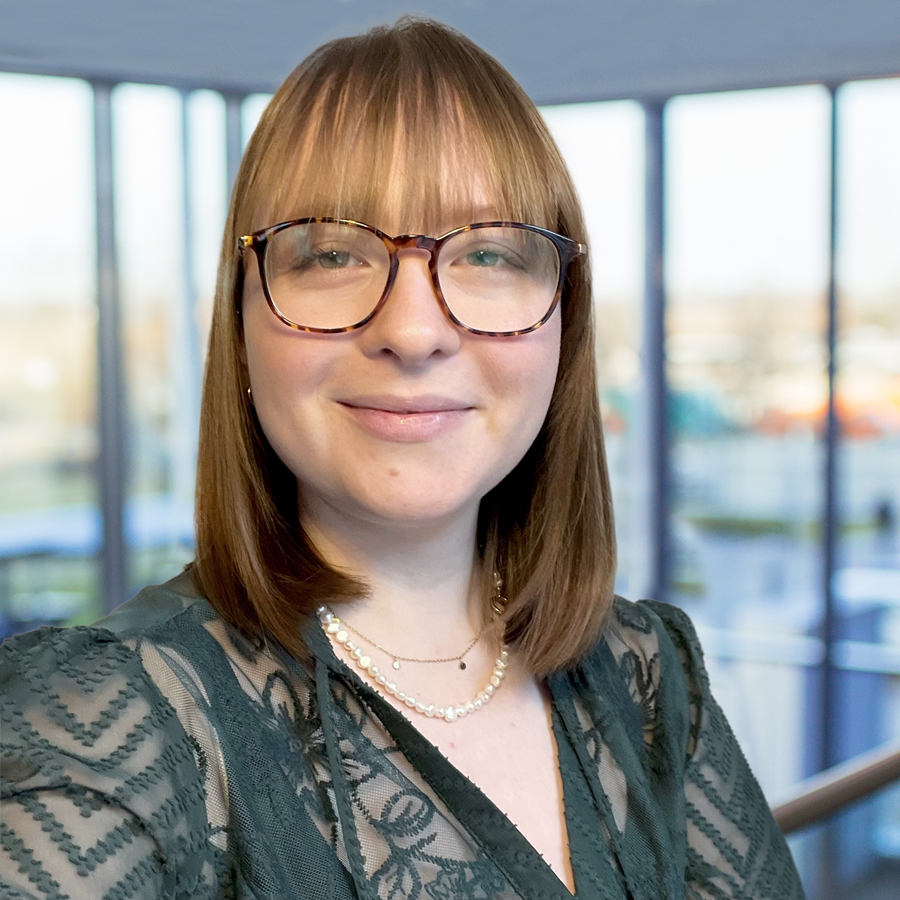
"Suitable and reliable components are also available for applications under harsh conditions." Inductive sensors and retroreflective sensors monitor storage locations and transmit information about the storage location allocation and positioning in the material handling system to the controller, while vision sensors ensure the right positioning of the bottles during the printing process and ensure that each customer receives their personalized bottle.
RFID tags can be used to continuously track the order status during production. For this purpose, they are mounted under the load carriers and are recorded by RFID read/write devices from Pepperl+Fuchs at various points in the production process. The data management enables the personalized allocation of the bottles to the shuttle. This means that the customer is always able to keep track of the status of their order.
In the pick-up notification, the customer receives a QR code that they can use to pick up the water bottle. To do this, the VOS2000 series vision sensor scans the code, ensuring that the customer receives the right bottle.
Innovation in Focus: New Opportunities for the Demonstrator
The demonstrator from Alexander Bürkle will continue to show what is possible with Industry 4.0 concepts and how manufacturers can produce products in batch size 1 under the economic conditions of mass production. 'We are constantly developing the system to continuously present the latest innovations,' explains Bachofner. 'The requirements of the future, such as sustainability, certainly play a role in this too.'
'We are excited about how the demonstrator will change and look forward to the challenge of providing new suitable solutions for Alexander Bürkle,' says Haller, looking toward the future. Products and technologies from Pepperl+Fuchs will continue to be represented in Alexander Bürkle's exemplary production plant. With the further development of the demonstrator, new technological opportunities for mass production made to measure can be achieved together.