November 9, 2023
Safety at the Highest Level
A train can travel hundreds of thousands of kilometers before its wheels need to be replaced due to wear. Regular maintenance is the only way that trains can travel such a distance without any faults. To protect personnel from accidents when performing maintenance work on lifting platforms, Kreitzler Industriebühnen GmbH relies on a safety positioning system from Pepperl+Fuchs.

Those traveling by train experience the pleasure of relaxing in their compartment and making their journey across the country in comfort, while enjoying unique panoramic views of the passing landscape through the window. Whether passing impressive rock massifs, heading through river valleys, or traveling along the coast of the deep blue sea—making these picturesque, relaxing journeys possible requires regular inspections and maintenance at service facilities to ensure that everything remains on track and trains perform their service reliably. To access all areas on the sides, front, and roof of the trains safely and without risky climbing procedures, or to access the train interior, service personnel use mobile lifting platforms, such as those offered by Kreitzler Industriebühnen GmbH. The company is based in Witten, Germany, and has developed an especially safe version of these platforms for the service facility of a railway company. Because although trains are a safe means of transport, their maintenance poses risks.
All-Around Protection
For service operations, the trains are placed on a 200 m long elevated track in the facility. This means that they can be easily inspected, maintained, and cleaned from all sides using the lifting platform. Outside of the maintenance area, the working platforms can be moved freely. However, since trains are regularly brought in and out, space is tight, and power lines run around the service facility, there is always a risk of collisions and accidents. For this reason, Kreitzler developed a solution for the railway company to ensure reliable protection of personnel, trains, and facilities by increasing the safety of the working platforms.

The company has achieved this by introducing camera-based track guidance within the working area using the safePGV positioning system from Pepperl+Fuchs. This means that the lifting platforms can no longer move freely in this area of the facility, but instead move along a laid track. "To achieve the maximum level of safety for our customers, we were looking for a positioning system for track guidance that would enable us to achieve safety level PL e," says Marcel Handge, Operations Manager at Kreitzler, looking back on the design and development. "Since safePGV achieves this with a single sensor, we quickly decided on the safe positioning system from Pepperl+Fuchs."
More Colors, Increased Safety
The safePGV safe positioning system is based on the combination of a 2-D read head with two-color illumination and a multi-color Data Matrix code tape. In the Kreitzler solution, the safePGV read head is located on the underside of the moving lifting platform, while the code tape is laid on the ground parallel to the elevated tracks. As soon as the moving lifting platform is located above the track, the read head detects the codes and the controller automatically takes over the steering movements. This allows personnel to move the platform along the trains, meaning they only have to control the direction of movement of the working platform and the speed. At the end areas, the speed is automatically reduced and the platform is stopped.
Facility operators also have the option of programming approvals and restrictions for various value windows on the code tape. For example, in certain positions on the track, personnel are not able to extend the platform to avoid touching open power lines. At the same time, thanks to safePGV, it is possible to position the lifting platform exactly in front of the entrance areas to the train, enabling safe and convenient access.
Safely Recessed
While mechanical guides for vehicles always present a tripping hazard, the plastic code tape is milled into the ground at the railway company's service facility and encapsulated to form a smooth surface. This prevents an additional risk of accidents at the facility and protects the Data Matrix codes against damage. This solution also eliminates the need for channels or joints in which dirt can accumulate. If the code tape at the service facility becomes dirty, the safePGV system still ensures safe positioning of the working platform, maintaining reliable protection of people and machines when working on the train. 'The safety version of our PGV system has the advantage of multiple redundancy,' explains Jan Schirweit, Sales Engineer at Pepperl+Fuchs. 'The data in the Data Matrix codes can be mapped redundantly, and the read head with a very large reading window is able to record five codes at once, making our safePGV system highly resistant to interference and extremely reliable.'
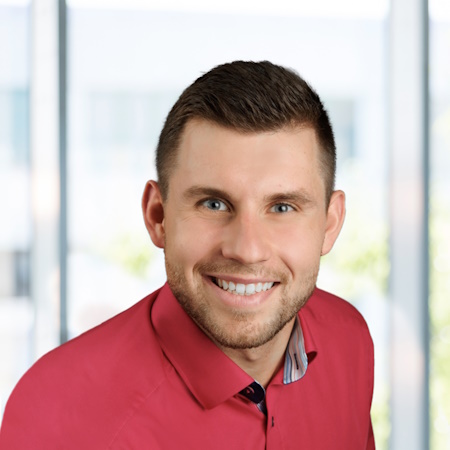
Safer Together
Currently, two Kreitzler moving lifting platforms with the safety version of the positioning system are in use at the railway company's service facility. Handge is confident that Kreitzler will manufacture and sell even more safe moving lifting platforms—and not just for service operations on trains. 'As soon as the safety of people and machines is at stake, reliable safety solutions are needed,' he explains. 'Pepperl+Fuchs has provided us with excellent, holistic advice as a safety expert. With the safePGV system, which is truly unique on the market, we can design our working platforms safely and thereby ensure increased occupational safety together.'
Safe Data Directly from the Sensor
The unique level of safety provided by the safePGV system is based on multiple colors. Each individual color code contains safety information that is made visible by the two-color lighting of the read head and is read by the camera. A safety algorithm in the innovative firmware checks the plausibility of the information detected in the sensor itself before the data is passed on to the safety-rated PLC as safe data in accordance with SIL 3/PL e. The safety version of the camera-based track guidance achieves a high level of safety with just a single device.