May 14, 2024
Powered by Expertise
The transformation to e-mobility requires high-performance automation technology in battery manufacturing. The companies of the Pepperl+Fuchs Group offer the right solutions for this—based on constant technological innovation and decades of experience in the automotive industry.
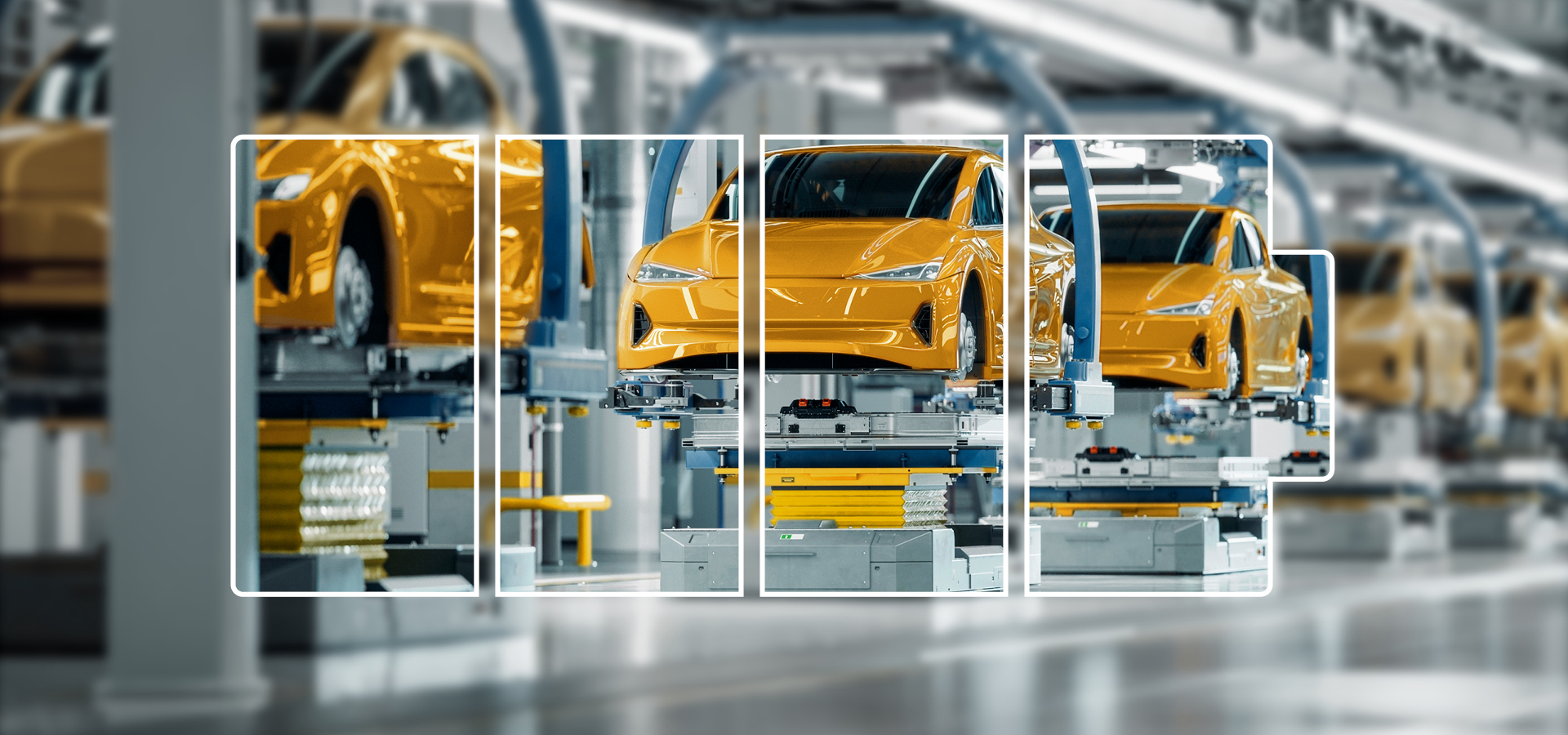
Although it may seem like it, the electric car is not just a contemporary trend. Long before diesel and gasoline cars conquered the market, Frenchman Gustave Trouvé presented the first electric car to the public in 1881. It had 6 hp and reached a speed of 12 km/h as well as a range of 14 to 16 km. Today's electric cars are a far cry from these figures: the sportiest models race along the roads with over 1000 hp and 300 km/h. Particularly powerful vehicles even manage ranges of over 700 km. A key part of this success story is the technical progress made with regard to the heart of the electric car—the battery.
The right automation technology is needed to maximize both efficiency and quality in battery manufacturing. Pepperl+Fuchs offers customized solutions for every step: from the electrodes and battery cells to the modules to the finished battery pack and installation in the car body. This is ensured by highly specialized subsidiaries within the company that work closely and trustingly with automotive manufacturers from all over the world. Selected solutions from Pepperl+Fuchs, VMT Vision Machine Technic Bildverarbeitungssysteme GmbH, and Polyplan GmbH show how plant operators can successfully automate their battery manufacturing.
Reliable Detection of Duplicate Films
The smallest unit of a battery cell consists of two electrodes and an electrode separator. Depending on the manufacturing process, the foils are either alternately stacked on top of each other or wound around a center pin or winding mandrel. The industrial sensors from Pepperl+Fuchs ensure smooth processes in all of these steps—for example, when it comes to the particularly challenging double sheet control when stacking the foils.
As the electrode foils are extremely thin, it can happen that two or more foils stick together. However, to ensure the quality of the battery cells, the vacuum gripper may only pick up one sheet of foil at a time so that the anode and cathode are always stacked alternately. Even if the gripper has not deposited a sheet, stacking must be interrupted and corrected.
IO-Link double sheet sensors are used for this purpose. They use ultrasonic pulses to monitor the material flow and detect whether a double layer has been fed. "Due to the noncontact detection, the sensitive films cannot be damaged," explains Michael Förste, Key Account Manager Automotive at Pepperl+Fuchs. "The robust ultrasonic measuring principle also ensures that neither the color nor the reflective properties of the films affect the detection capability." In addition, the integrated IO-Link interface enables simplified configuration, even during operation. The real-time monitoring of process data also opens up new potential for machine analysis and maintenance. This allows the double sheet sensors to be optimally adjusted, which reduces false detections and increases system availability.
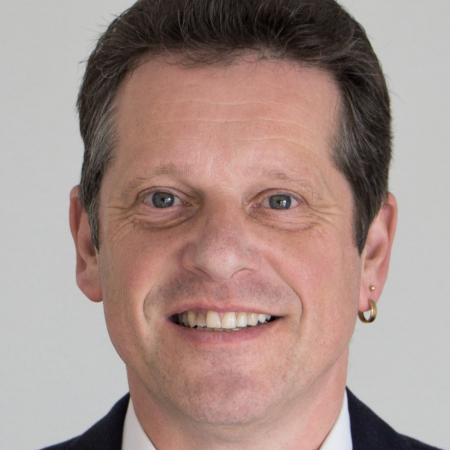
Focus on Quality in Three Dimensions
As soon as the foils are properly stacked or wound, the ion-conducting electrolyte is filled in and the cell is sealed. For the classic battery architecture, several cells are then joined together to form a battery module until the finished battery pack is finally created from several modules. Pepperl+Fuchs also provides support here with optimally coordinated sensor technology—for example, to check the quality of the assembled battery module.
'Before the module is processed further, it must be checked that all the required cells are present, aligned straight, and arranged without protrusion,' explains Michael Förste. 'To avoid delays in production, it is also important that this quality control takes place without delay while the module is being transported on a conveyor belt or roller conveyor.'
The SmartRunner Explorer 3-D offers an ideal solution for this task: with stereo vision technology, the vision sensor ensures fully automatic quality inspection during the running process. To do this, it generates a high-resolution 3-D point cloud image of the entire measurement area. The battery module and the individual cells are precisely mapped in all the necessary details. With the ViSolution software, the SmartRunner Explorer 3-D can be intuitively commissioned and parameterized using live data. The sensor itself pre-processes the measurement data in its integrated Field Programmable Gate Array (FPGA). "This provides our customers with all the data they need for quality testing the battery modules quickly and easily," summarizes Michael Förste.
Dissipate Heat Safely
Once the modules have been correctly assembled and sealed, they are inserted into packs. The application of heat-conducting paste plays a key role here. This is because heat is generated during every charging and discharging process, which must be dissipated to protect the battery from overheating. This is why strips of heat-conducting paste, known as gap fillers, are often applied to the battery tray before the modules are installed.
This process uses a vision solution from VMT Bildverarbeitungssysteme GmbH, which has established itself as a pioneering inspection system for adhesive bead control. 'With the VMT SpinTop G2, the continuity and correctness of the gap filler beads can be checked in parallel with the job, so that no additional evaluation time is required,' explains Joachim Kutschka, Senior Manager Sales & Product Management. The inspection system is attached directly to the robot arm. Two measuring units rotate with it and ensure three-dimensional detection of the bead-shaped material applied. An additional technology package enables simple communication with the robot controller so that the inspection system is aligned accordingly.
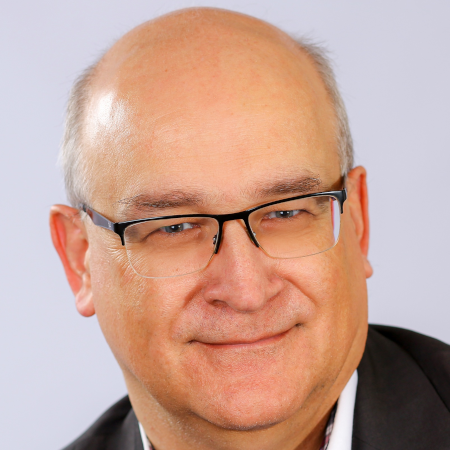
In March 2024, VMT launched the new generation of SpinTop onto the market: instead of the infrared lasers previously used, high-quality lasers with blue and red light in the visible spectrum are now used. "This significantly improves the recording quality at greater distances and on dark surfaces," explains Kutschka. In addition, the SpinTop G2 achieves a rate of up to 900 scans per second and twice the resolution, which significantly increases the quality of monitoring. This makes the solution suitable not only for inspecting the gap filler application, but also for other applications in battery manufacturing, such as checking the sealing beads that are applied to the edge of the tray before the battery pack is closed with a lid. "These seals are often only a few millimeters thick and therefore require high-resolution sensor technology," says Kutschka. "Especially thanks to the doubled resolution of the SpinTop G2, we can now solve challenging tasks like this even better."
VMT Bildverarbeitungssysteme GmbH has been offering its customers turnkey solutions for various applications for over 25 years, from the press shop to the body shop to final assembly. The SpinTop was originally developed to inspect adhesive beads during the assembly of windshields. However, the inspection system is also already being used successfully for battery manufacturing in several plants operated by international car manufacturers and dosing technology providers. "As the process sequences in battery production are changing rapidly, we see a lot of potential for further applications," says Joachim Kutschka, looking optimistically to the future
Lasting Protection against Corrosion
Corrosion prevention also plays an important role when closing and sealing the battery pack. For example, it must be ensured that the pack is well sealed and protected against corrosion at cooling connections or screw connections. Polyplan GmbH offers a particularly efficient and resource-saving solution to this challenge. The company, based in Strasslach, Bavaria, has been supplying complete production cells for processes such as acoustic foaming or door waxing for decades—and now also for corrosion prevention in battery manufacturing.
'The areas of the battery that need to be protected against corrosion are often very difficult to access,' explains Jan Jacobi, Head of Sales and Aftersales. With conventional automation solutions, too much wax is often sprayed for sealing, which not only wastes material but also contaminates the environment. As a result, the excess material has to be cleaned off and the resulting aerosols extracted. In contrast, Polyplan's solution offers numerous advantages: 'We use a patented airless/air mix process that produces no aerosols. The wax is applied with a precision of +/- 1 mm over a distance of 500 mm. As a result, we only need a minimal amount of approx. 1 g/m, so that we guarantee long-term corrosion prevention with minimal media consumption. As there is no need for time-consuming and cost-intensive cleaning and extraction, our customers also benefit from shorter cycle times.'
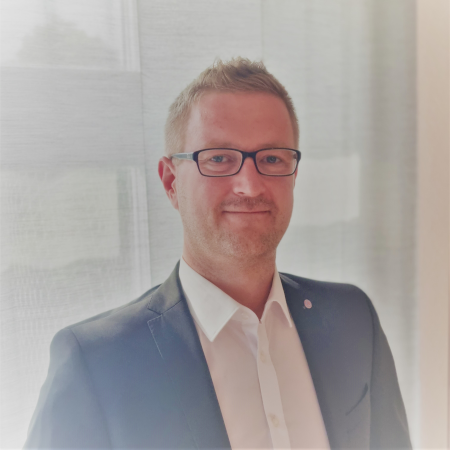
The technology on which this solution is based is already being used in over 20 production lines of major car manufacturers for door waxing. In the meantime, it has also proven itself with the first customers in battery pack manufacturing. From the industrial robot to the wax dosing system to the safety technology, Polyplan supplies everything that is needed for the turnkey robot cell—each tailored to the customer's individual system. "We also utilize synergies within the Pepperl+Fuchs Group," adds Jacobi. For example, the VMT LineRunner, a powerful laser triangulation sensor that delivers robust measurement results even in difficult lighting conditions and changing surface appearances, is used for object position correction.
Together on the Road to Sustainable Mobility
Once the battery pack has been sealed and carefully checked, it can be installed in the car body and from now on provide many kilometers of emission-free driving. In addition to double-sheet inspection of the electrode foils, quality inspection of the modules, gap filler monitoring, and corrosion prevention—Pepperl+Fuchs solutions are used in many other battery-related applications so that car manufacturers can continue to drive electromobility forward in the future.