21. November 2017
Kein Sand im Getriebe
In der Produktionshalle herrscht gleißende Hitze – wenn flüssiges Metall zu einem Motorblock für ein Auto gegossen wird, erreicht es Temperaturen jenseits der 1.000 °C. Der Gussvorgang ist nicht nur schweißtreibend, sondern auch zeit- und kostenintensiv. Um fehlerhafte Güsse zu vermeiden, setzt das SpinScan3D-System der Pepperl+Fuchs Tochter VMT Vision Machine Technic Bildverarbeitungssysteme GmbH bereits bei der Qualitätskontrolle der Gussformen an.
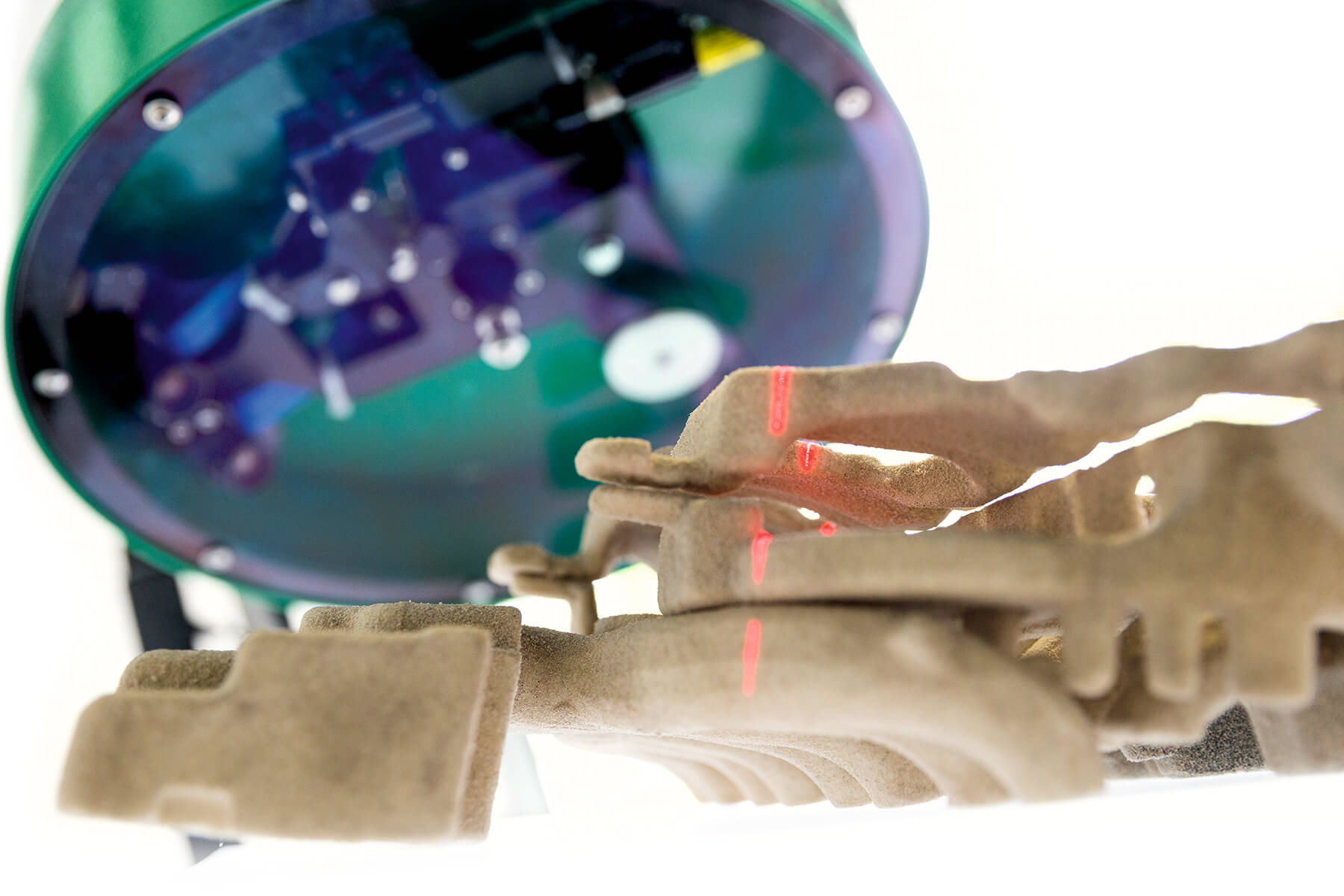
Ob auf Knopfdruck oder mit dem klassischen Schlüsselumdrehen im Zündschloss — wenn der Motor anspringt, kann der Fahrspaß beginnen. Am Auto zeigt sich Ingenieurskunst vom Feinsten: immer leistungsfähigere Motoren, stetig neue Innovationen, die das Fahren noch komfortabler machen. Doch bis ein Auto über Autobahnen und Landstraßen rollt, hat es einen langen Weg durch die Produktion hinter sich. Die Herstellung ist aufwändig und unterliegt höchsten Präzisionsansprüchen: Von der kleinen Schraube bis zur ganzen Karosserie muss alles bis ins letzte Detail stimmen.
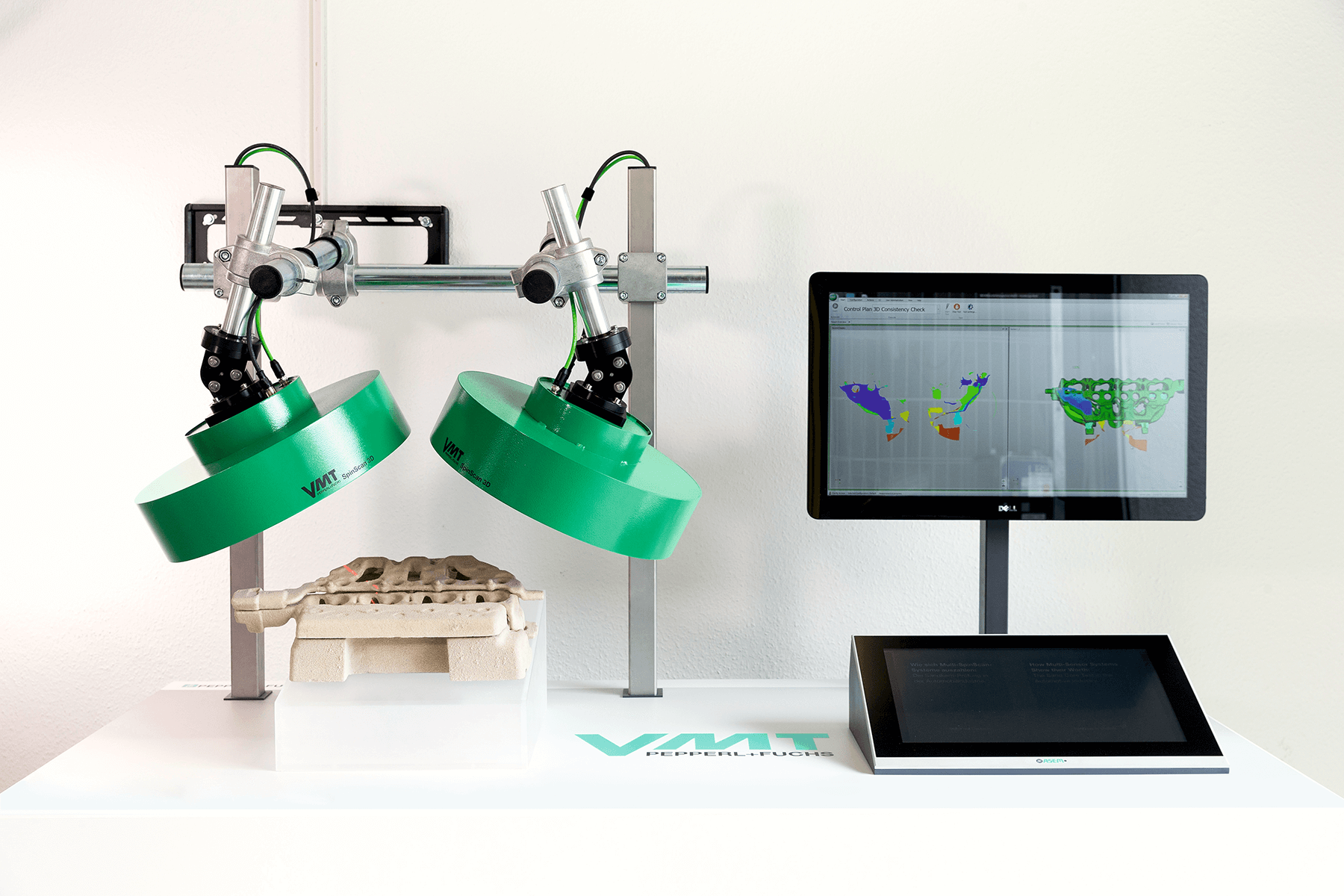
Bis ins kleinste Detail: Mit rotierenden Bewegungen erfassen vier perfekt aufeinander eingespielte SpinScan3D-Sensoren das exakte Abbild eines Sandkerns für den Motorblockguss.
Herzstück Motor
Der Motor ist zentraler Bestandteil des Autos und muss in seiner Qualität zu 100 % den Konstruktionsdaten entsprechen. Essentieller Baustein dieses Herzstücks ist der Motorblock. Ob aus Gusseisen oder Leichtmetall, die Herstellung erfolgt in der Regel im Gussverfahren. Ist das Gussmaterial einmal ausgehärtet, gibt es kaum Möglichkeiten, das Ergebnis noch anzupassen. VMT entwickelte daher eine Lösung, die schon vor dem teuren und aufwändigen Gussvorgang die Qualität der Form mithilfe moderner Bildverarbeitungstechnologien überprüft. Damit stellt das Unternehmen der Pepperl+Fuchs Gruppe sicher, dass fehlerhafte Motorblöcke erst gar nicht gegossen werden.
Feine Körnchen, große Blöcke
Grundlage des Gussvorgangs ist ein Naturmaterial, das wir sonst mit Wüsten und weiten Stränden verbinden: Sand, gepresst und mit Bindemittel angereichert, dient als sogenannte verlorene Form für die Herstellung der schweren Motorblöcke. Solche Sandkerne stellen ein Negativ des Motorblocks dar und füllen beim Guss die späteren Hohlräume. Nach dem Aushärten des Gussmaterials werden sie wieder zerstört und dienen der Produktion neuer Formen. Jeder einzelne Motorblock entsteht also mit einer eigenen Sandform.
Da die Qualität des Sandkerns die Beschaffenheit eines Motorblocks maßgeblich beeinflusst, muss die Qualitätssicherung bereits vor dem Guss ansetzen. Bei der Vielzahl an täglich gefertigten Motorblöcken bedeutet es jedoch einen großen Aufwand, jeden Sandkern einzeln zu prüfen. Gefragt ist daher eine Lösung, welche die Sandkerne automatisiert präzise betrachtet und gleichzeitig feststellen kann, ob sie zum Guss taugen oder nicht.
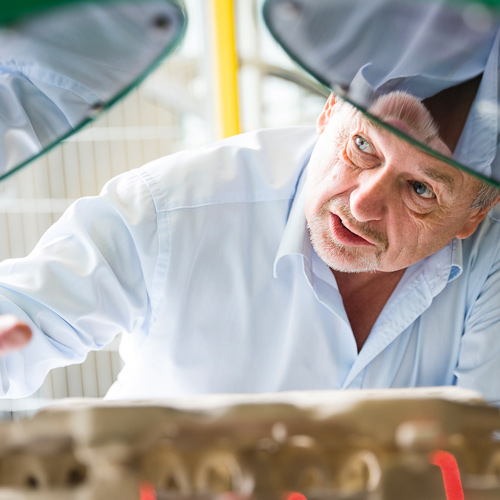
„Die Inspiration kommt mit dem Problem.“
Dr. Werner Neddermeyer, Projektleiter bei VMT, erkannte die Problematik bei der Motorblockproduktion und entwickelte eine Idee. „Wir haben uns überlegt, was man erfassen muss und wie wir das mit unseren Sensoren lösen können“, schildert er die Anfänge. „Jede Stelle eines solchen Sandkerns muss hochgenau überprüft werden, um Aussagen über die Qualität zu machen. Das ist nicht einfach, wenn man bedenkt, dass es sich bei Sandkernen für Motorblöcke um komplexe Formen handelt.“ Das bewährte Lichtschnittverfahren stellte sich schnell als die geeignete Technologie für die exakte Betrachtung der Sandkerne heraus.
Ein herkömmlicher Lichtschnittsensor reichte jedoch nicht aus, um einen Sandkern in all seinen Details zu erfassen und darzustellen; die Komplexität eines Sandkerns erforderte ein komplexeres Sensorsystem, das jeden Winkel betrachten und prüfen kann — eine Herausforderung, die Neddermeyer gemeinsam mit Dr. Michael Kleinkes, Entwicklungsleiter bei VMT, annahm. Das Ergebnis ist ein ausgeklügeltes Zusammenspiel mehrerer Sensoren, die ein genaues 3-D-Bild jedes Sandkerns liefern und automatisch mit den CAD-Konstruktionsdaten abgleichen.
Sensorsymbiose SpinScan3D
Zum Einsatz kommen vier parallel arbeitende SpinScan3D-Sensoren. Die Bewegung und Interaktion der einzelnen Komponenten dieses Multi-Sensor-Systems sind es, die das exakte Abbild der komplexen Formen ermöglichen. Ein Blick ins Innere des SpinScan3D verrät, wie VMT die Laserlinien-Triangulation für diese Aufgabe modifiziert hat: Durch ein optisches Prisma wird, wie beim klassischen Lichtschnittverfahren, der Lichtstrahl eines Lasers zu einer gleichmäßig leuchtenden Linie ausgeweitet. Zwei parallel arbeitende Kameras im SpinScan3D betrachten jeweils einen spezifischen Teil der Laserlinie und erfassen das Höhenprofil entlang derselben. Diese doppelte Laserlinien-Triangulation ermöglicht einen erweiterten Messbereich ohne Einbußen bei der Messgenauigkeit. Die besondere Innovation des SpinScan3D steckt schließlich in der Erweiterung des Sensors um eine Bewegungsachse. Durch eine Rotationsplattform wird er gedreht, sodass der Laser im Inneren um seine eigene Achse kreist und die projizierte Linie ununterbrochen über das Objekt läuft. Die beiden Kameras pendeln dabei um den Mittelpunkt des Sensors und erfassen kontinuierlich die Veränderung der Laserlinie.
Alles eine Frage des Blickwinkels
Aufgrund der rotierenden Bewegung des SpinScan3D ändert sich stetig der Betrachtungswinkel auf das Objekt — bei einer Messrate von 300 Lichtschnitten in der Sekunde entsteht so eine Vielzahl einzelner Momentaufnahmen. Die intelligente Software von VMT verarbeitet alle erfassten Daten und setzt diese unzähligen Einzelbilder zu einer Punktewolke zusammen, sodass ein dreidimensionales Gesamtbild der komplexen Form entsteht. Die Abbildung ist dabei nahezu abschattungsfrei. Das heißt, dass der SpinScan3D annähernd jeden Millimeter genau erfasst und darstellt. „Während bei der klassischen Laserlinien-Triangulation Teilbereiche eines Objekts unter Umständen nicht erfasst werden, weil sie im Messschatten liegen, kann der SpinScan3D durch die unterschiedlichen Betrachtungswinkel mehr Stellen erkennen“, erläutert Kleinkes. „So liefern wir einen viel umfassenderen Datensatz und damit ein hochgenaues 3-D-Abbild komplexer Objekte.“ Dank der vier parallel eingesetzten und perfekt aufeinander eingespielten Sensoren kann das System von VMT selbst die großen Sandkerne für den Motorblockguss in ihrer Geometrie exakt erfassen. Das System arbeitet dabei so schnell, dass es den Produktionstakt nicht aufhält.
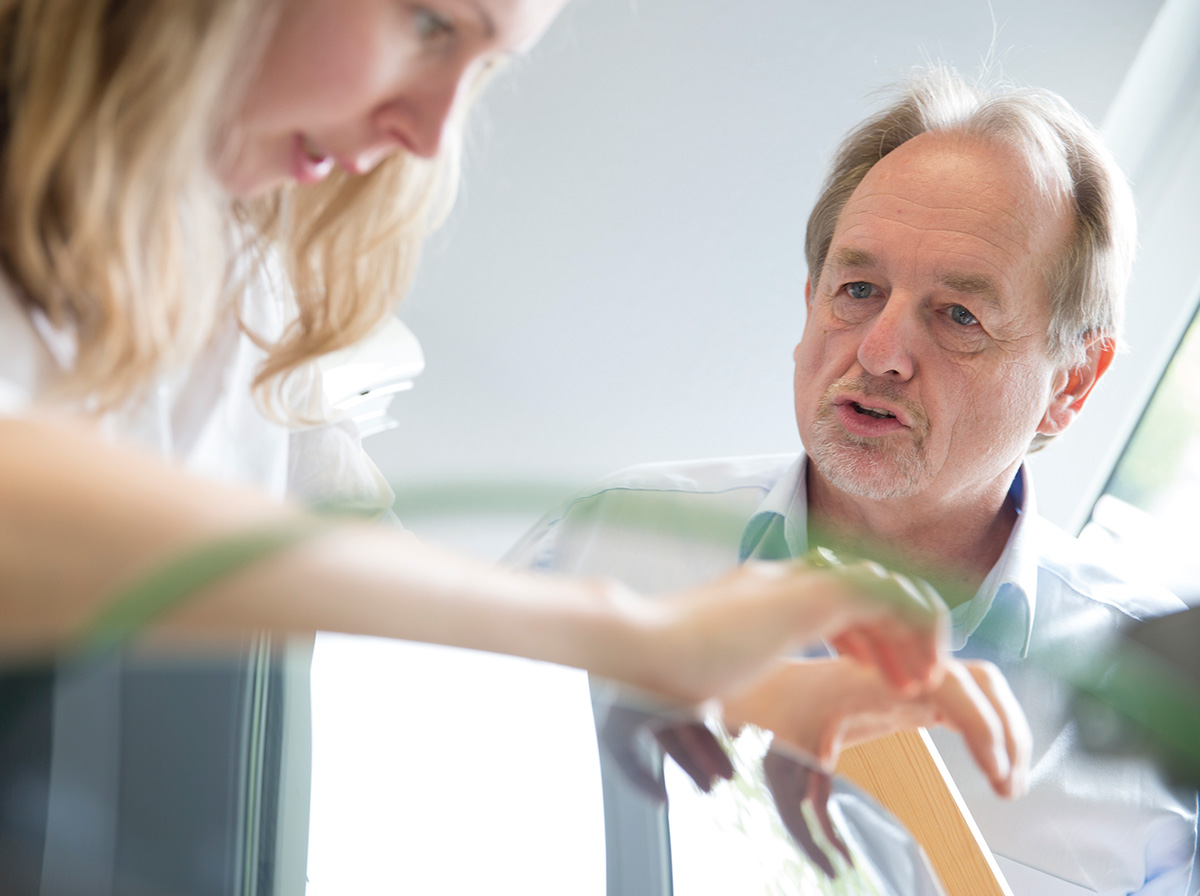
Dr. Neddermeyer und sein Team arbeiten mit Expertise und Leidenschaft für die Automation an der richtigen Lösung.
Die Datenverarbeitung ist die Kür
Basis der präzisen Überprüfung ist die Software von VMT. Sie meistert die Verarbeitung der großen Datenmenge und liefert dem Nutzer nicht nur das detailgetreue Abbild des Sandkerns, sondern nimmt automatisch einen Abgleich mit den CAD-Konstruktionsdaten für die Gussform vor. Möglich ist das insbesondere durch das Festlegen von Referenzpunkten für kritische Stellen des Sandkerns. Die Software gleicht die erfassten Sensordaten mit den definierten Sollmaßen ab und errechnet daraus, inwieweit virtueller Plan und reelle Bauform übereinstimmen. „Dieser Vorgang, bei dem virtuelle und reale Welt zueinander in Bezug gesetzt werden, entspricht der Anforderung an Industrie-4.0-Komponenten, Daten aus allen Phasen des Produktlebenszyklus elektronisch lesbar zur Verfügung zu stellen“, erklärt Neddermeyer. Weicht die Qualität des Sandkerns in zu großem Maß von der CAD-Zeichnung ab, geht automatisch eine Warnmeldung an die Kontrollstelle, sodass die fehlerhafte Gussform noch vor dem Gussvorgang entfernt werden kann. Damit liefert das System dem Nutzer alle vor dem Gussvorgang relevanten Informationen — und zwar so aufbereitet, dass notwendige Maßnahmen direkt abgeleitet werden können.
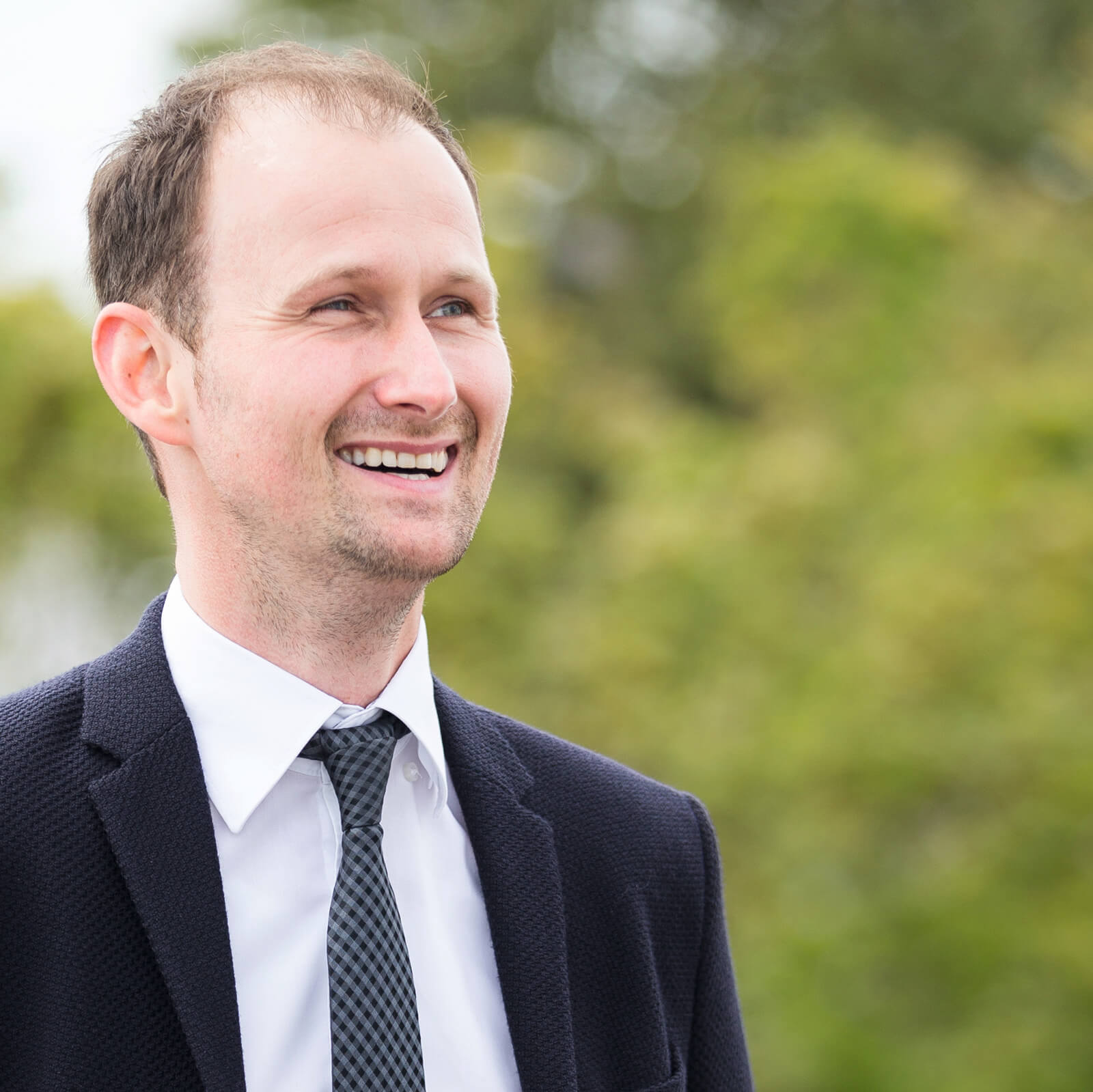
Sensorik4.0® — Mehrwert für Industrie 4.0
Sensordaten so aufzubereiten, dass sie den Nutzer effektiv unterstützen und Produktionsabläufe optimieren, ist eine essentielle Aufgabe von Industrie 4.0. Die Sandkernprüfung zeigt, wie VMT große Datenmengen gezielt nutzt, um sie für Anwender in der Praxis zu relevanten, verständlichen Informationen zu verarbeiten. Entscheidend sind dabei kommunikationsfähige Sensoren, welche „Big Data“ aus der Feldebene über alle Hierarchieebenen bis in übergeordnete Informationssysteme durchgängig verfügbar machen. Bei Sensorlösungen wie diesen spricht Pepperl+Fuchs von Sensorik4.0®. Denn durch die Bereitstellung relevanter Informationen und deren Visualisierung leistet Sensorik4.0® einen wertvollen Beitrag in Industrie-4.0-Szenarien — heute wie morgen. Diese Informationen helfen dabei, Prozesse entlang der gesamten Wertschöpfungskette so effizient wie möglich zu gestalten und gleichzeitig Personal zu entlasten. Gemeinsam mit Partnerunternehmen arbeiten VMT und Pepperl+Fuchs stetig daran, solche Sensorik4.0®-Lösungen auszuarbeiten und immer weiter zu optimieren.
Wer rastet, rostet
Vom allerersten Prototyp des SpinScan3D bis zur heute genutzten Multi-Sensor-Symbiose wurden bereits zahlreiche Aspekte weiterentwickelt. Auch mit dem jetzigen Einsatz des SpinScan3D-Systems beim Kunden ist das Projekt für Neddermeyer und Kleinkes noch nicht beendet. „Es gibt immer noch etwas, das man verbessern kann“, berichtet Kleinkes. „Wir arbeiten stetig weiter daran, das System auszufeilen und unseren Kunden eine noch bessere Lösung anzubieten.“ SpinScan3D soll nicht nur auf die Sandkernvermessung begrenzt bleiben. So haben sich Neddermeyer und Kleinkes zum Ziel gesetzt, das System zur Serienmäßigkeit weiterzuentwickeln und auch für zahlreiche andere Anwendungen, die exakte Messungen erfordern, nutzbar zu machen. „Das ist es, was unsere Arbeit ausmacht und uns anspornt, die ideale Lösung zu finden. Wir haben immer unsere Kunden und ihre möglichen Herausforderungen von morgen im Kopf — in Zeiten von Industrie 4.0 mehr denn je“, schließt Neddermeyer.