13.09.2017
Warenströme mit Weitblick
Ununterbrochen sind die Regalbediengeräte in Bewegung. Pausenlos flitzen sie zwischen den Regalplätzen hin und her, in denen der stete Strom von Kartons kurzweilig zur Ruhe kommt. Die unermüdlichen Maschinen des 2016 eröffneten Global Distribution Centers (GDC) in Singapur sind hier mehr als nur eine technische Assistenz.
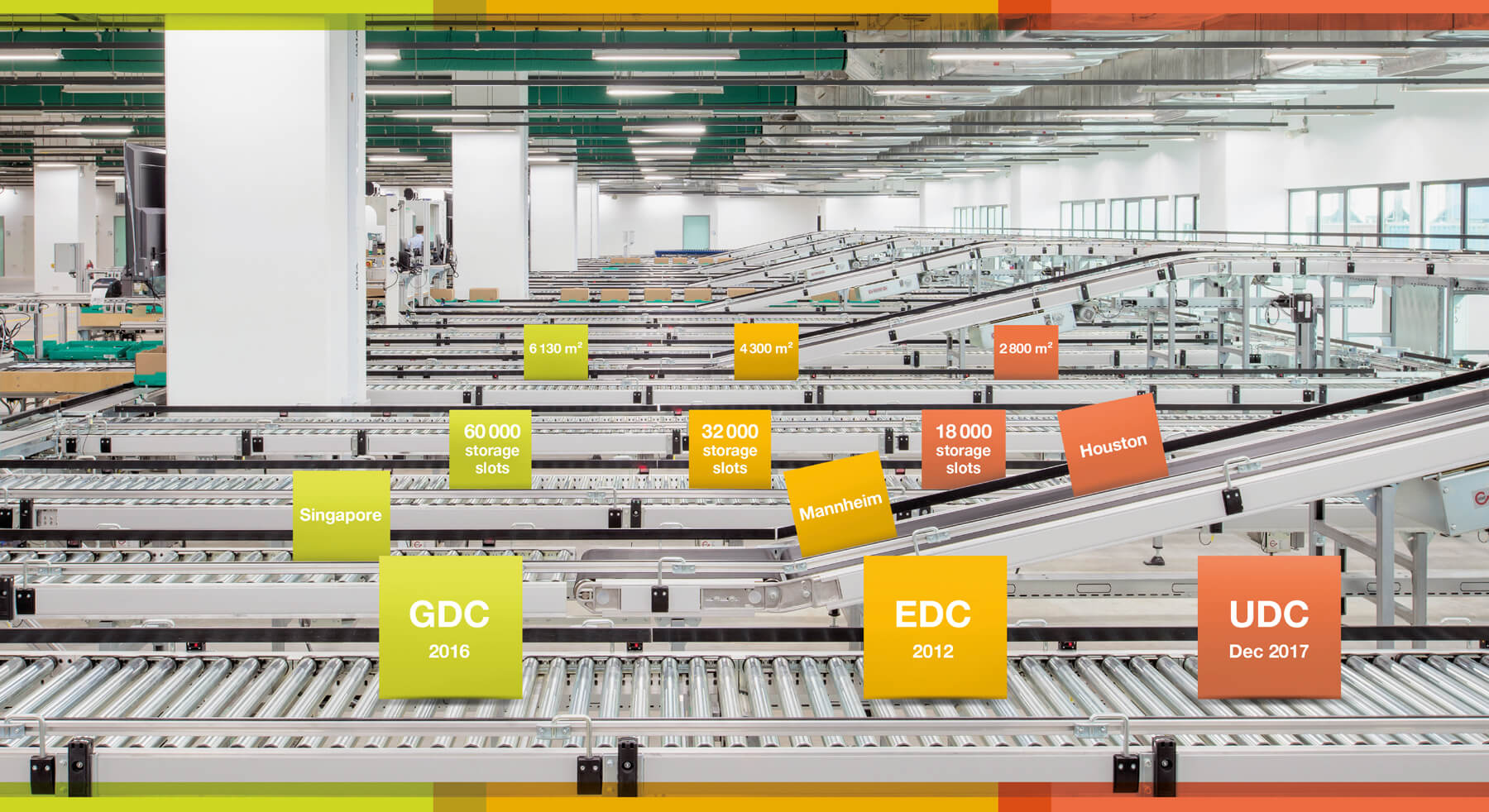
„Die Automatisierung der Logistik in der Mannheimer Zentrale war über zwanzig Jahre zuvor eine Pionierleistung, doch die damalige Technik hatte ihren Zenit irgendwann einfach überschritten“, schildert Logistikleiter Markus Külken. „Zudem wurde mehr Platz gebraucht, und auch die Abläufe mussten deutlich schneller werden, um mit dem Wachstum des Geschäfts Schritt halten zu können. Man beschloss also, ein ganz neues Verteilzentrum mit dem höchstmöglichen Automatisierungsgrad zu bauen.“ Was sich in Mannheim bewährte, wurde folglich international mit Erfolg umgesetzt.
Gleich und doch anders
Der erste Blick in die Halle lässt kaum erkennen, ob man sich gerade in Mannheim oder Singapur befindet. Denn die beiden Distribution Center sehen einander verblüffend ähnlich. Auch das neue amerikanische Pendant UDC in Houston wird noch in diesem Jahr im selben „Look-and-feel“ eröffnet. Die Ähnlichkeit der Zentren ist natürlich kein Zufall. Mannheim diente als Musterbeispiel für Kundennähe und Liefertreue. Basierend darauf wurden Aufgabe und Technik auf Singapur und Houston übertragen und weiterentwickelt. Ein wichtiger Bestandteil ist ein automatisiertes Kleinteilelager (AKL) mit Hochregalen. Darin liegt die Ware in Kartons auf sogenannten Tablaren, die von vollautomatischen Regalbediengeräten an die nötige Stelle transportiert werden. Nach dem Prinzip „Ware-zu-Mann“ gelangen sie auf Rollenbahnen zu den Arbeitsplätzen. Natürlich erledigen hauseigene Produkte in allen Distribution Centern die zentralen Aufgaben der Erfassung, Steuerung sowie Datenübertragung und erproben und bewähren sich so fortwährend in Logistikanwendungen.
Vollautomatische Einlagerung
Neben der hochmodernen Automatisierungstechnik unterscheidet sich die neue von der alten Lagerhaltung vor allem durch ein umfassendes Lagerverwaltungssystem (LVS). Es ist in die unternehmensweite Bestandsverwaltung (Enterprise Resource Planning, ERP) eingebunden, bildet die einzelnen Vorgänge viel detaillierter ab als früher und kann komplette Logistikprozesse steuern. Zudem sind nun alle Pepperl+Fuchs Standorte konsequenter in den Materialfluss integriert, wie Külken erklärt: „Jeder Karton, der eine unserer Produktionsstätten verlässt, bekommt ein ‚Nummernschild‘ in Form eines Barcodes. Material und Stückzahl sind hinterlegt und lassen sich mit dem Code im System zuordnen. Wenn der Karton in einem der drei Verteilzentren ankommt, wird er jetzt vollautomatisch erfasst und eingelagert.“ Lediglich bei Lieferungen von Fremdfirmen ist menschliche Intervention gefragt – noch, denn man ist mit den Lieferanten im Gespräch darüber, wie ihre Kartons in die automatisierte Erfassung eingefügt werden können.
Der Mensch inmitten der Automatisierung
Mitarbeiter sind vor allem in der Kommissionierung der Waren beschäftigt, wo einzelne Aufträge zusammengestellt und verpackt werden. Lichtsignale, die auf die angeforderten Teile zeigen, unterstützen sie beim Umpacken der Ware von den Lager- in die Versandkartons. Diese technische Assistenz, auch Pick-by-Light genannt, verringert die Suchzeiten, die Fehlerquote und unterstützt die Konzentration der Mitarbeitenden. Nach Möglichkeit kommt aber das Prinzip der Vollentnahme (Full-Bin-Retrieval) zum Einsatz: Schon in der Produktion werden die Verpackungsgrößen auf den Bedarf der verschiedenen Kunden abgestimmt, sodass ganze Kartons ungeöffnet und ohne menschliches Eingreifen weitergeleitet werden können.
Die weiten Förderstrecken im GDC erinnern an lange Autobahnen. Täglich transportieren sie Pepperl+Fuchs-Produkte, die von hier in die ganze Welt gehen.
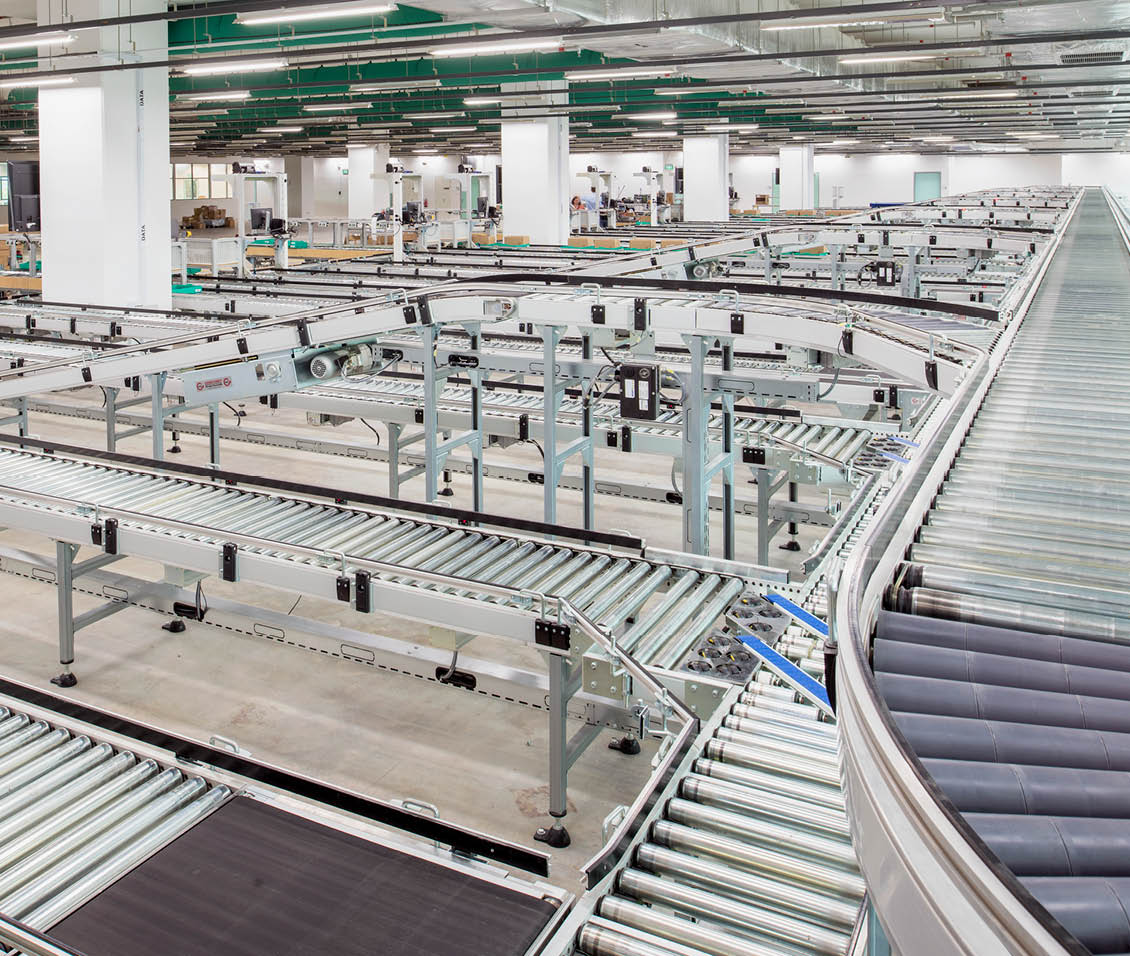
Im GDC kommt die eigene Automatisierungstechnik von Pepperl+Fuchs zum Einsatz: Verschiedenste Sensoren haben immer ein Auge auf das Transportgut und überwachen damit quasi ihren eigenen Versand.
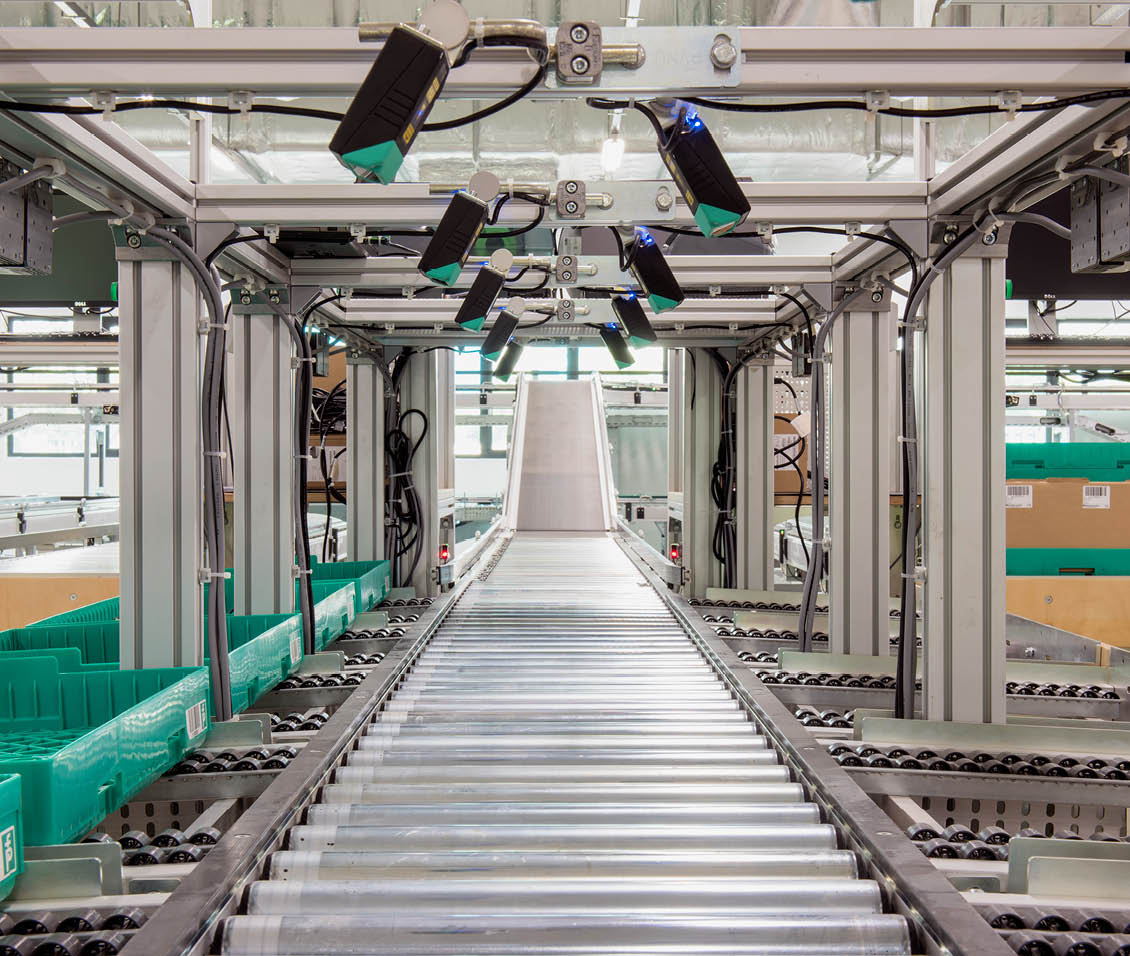
Unzählige Kisten mit Sensoren und Komponenten werden täglich automatisiert über die Förderstrecken im GDC transportiert.
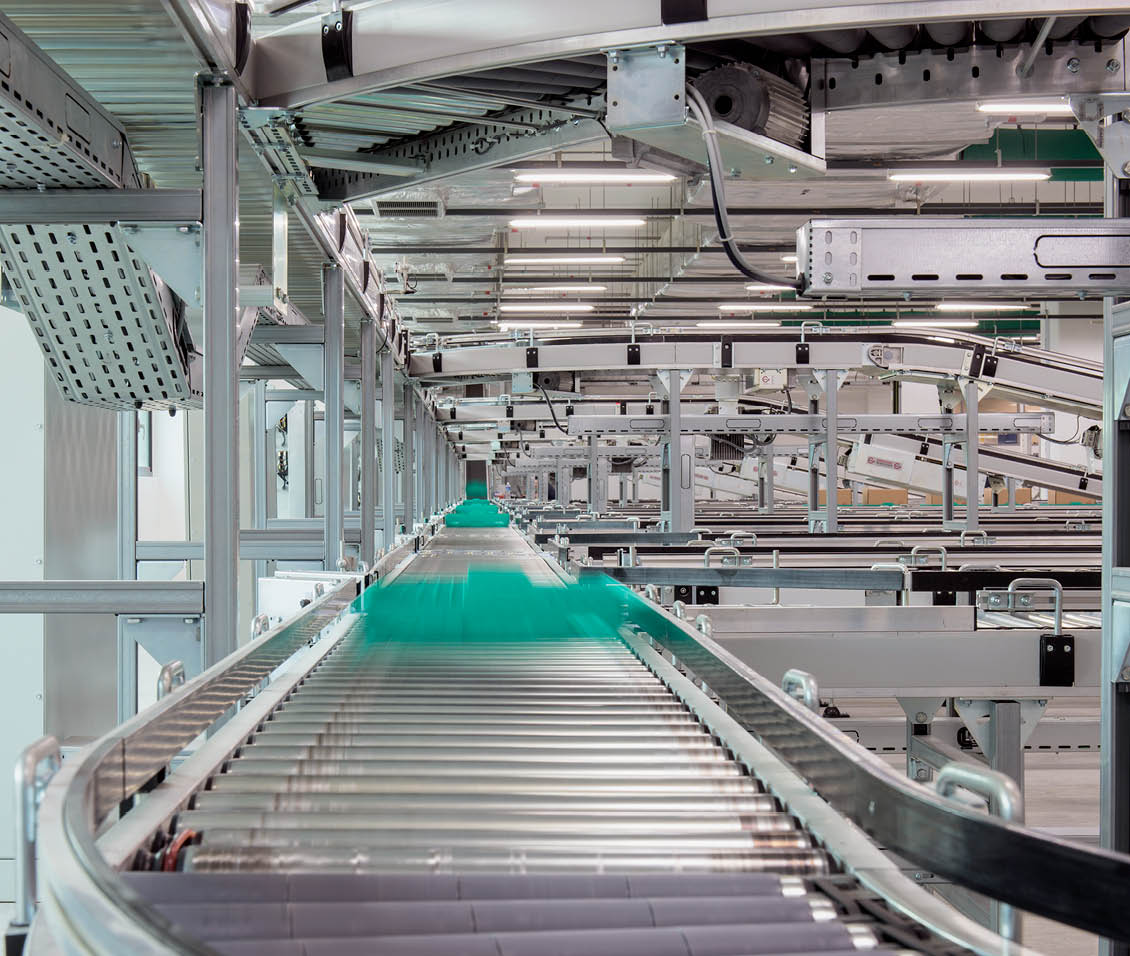
Die Datenlichtschranken von Pepperl+Fuchs stellen zusammen mit vielen anderen Pepperl+Fuchs Produkten einen reibungslosen Ablauf sicher
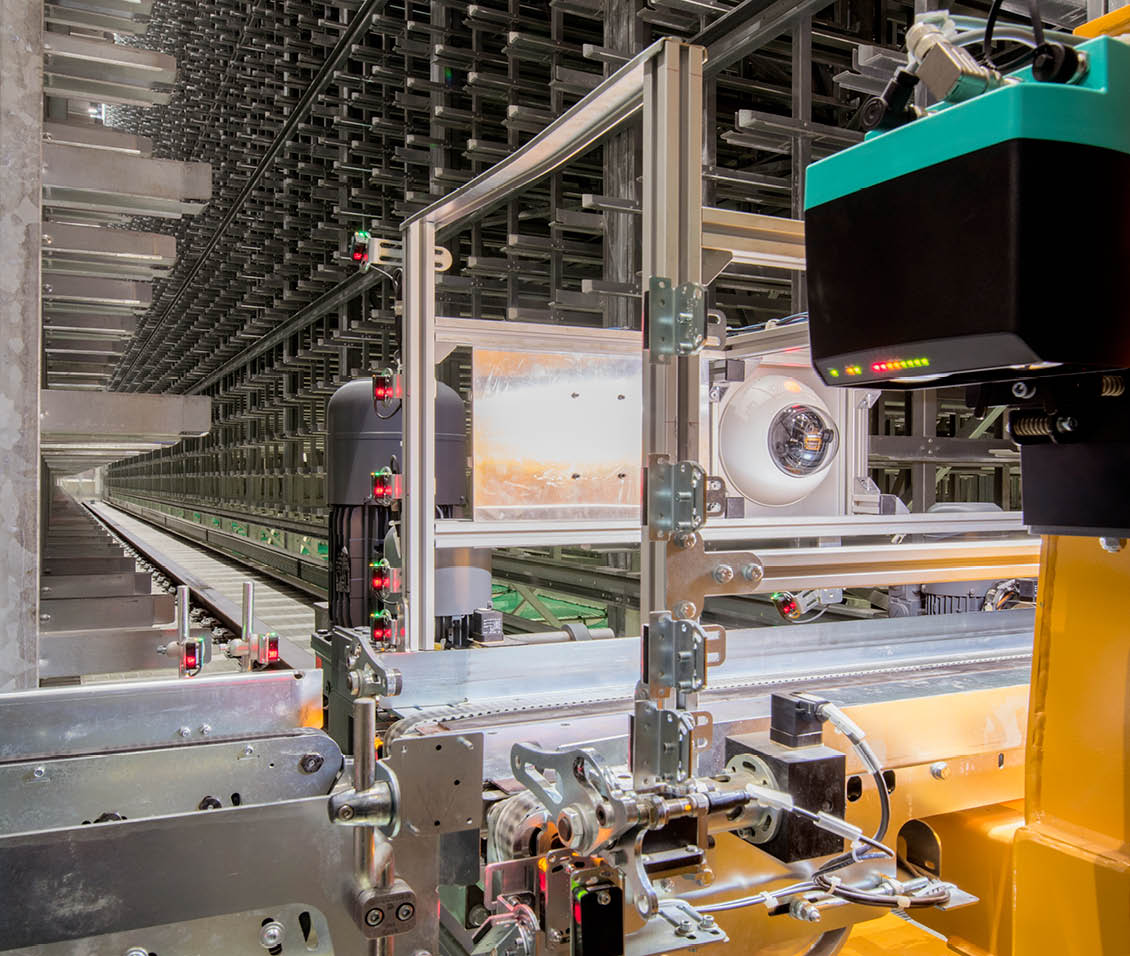
Der Laserscanner R2000 bietet eine 360°-Umsicht und stellt die Qualität bei der Kommissionierung der Produkte sicher.
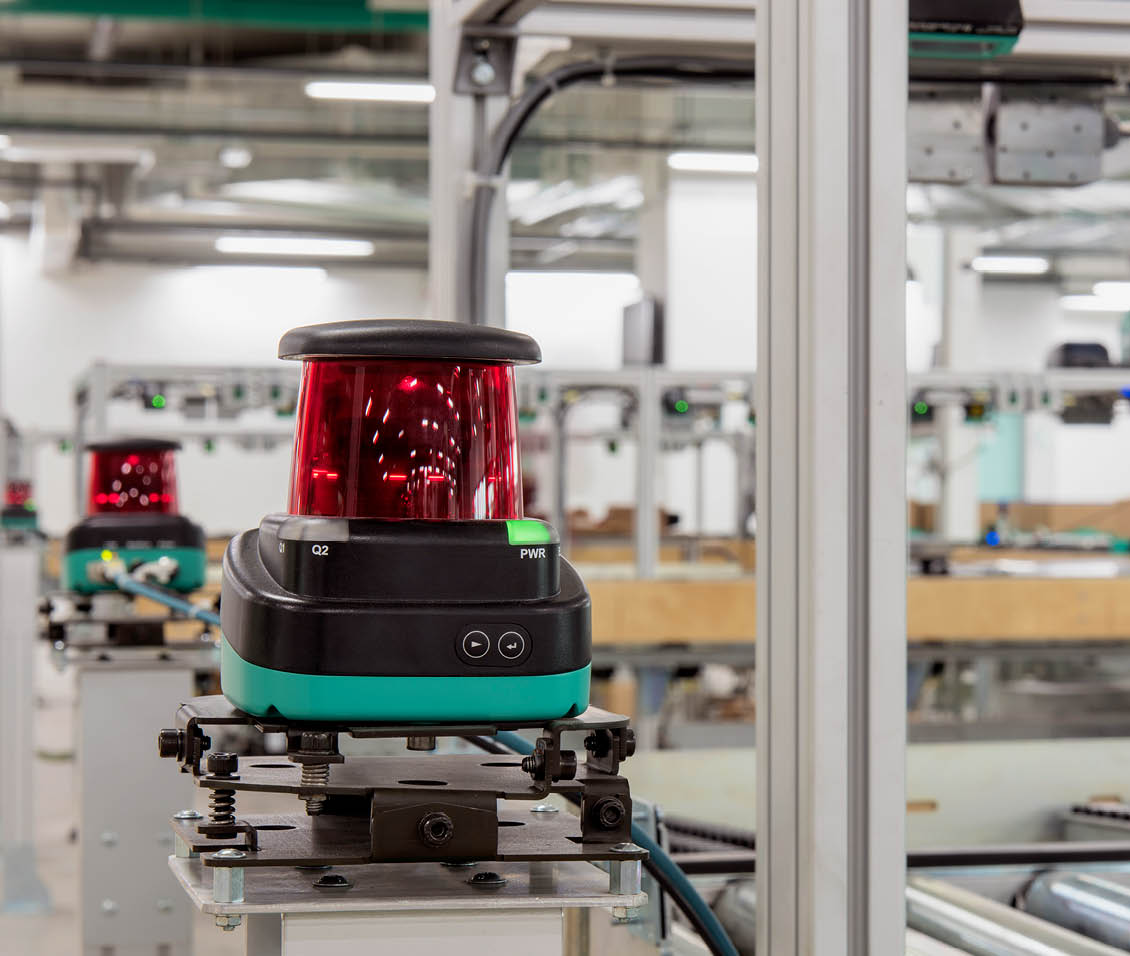
Das neue Lager im GDC bietet mit 32000 Regalplätzen viel Platz, sodass immer genügend Bestand an Produkten vorhanden ist, um eine optimale Liefertreue zu erzielen.
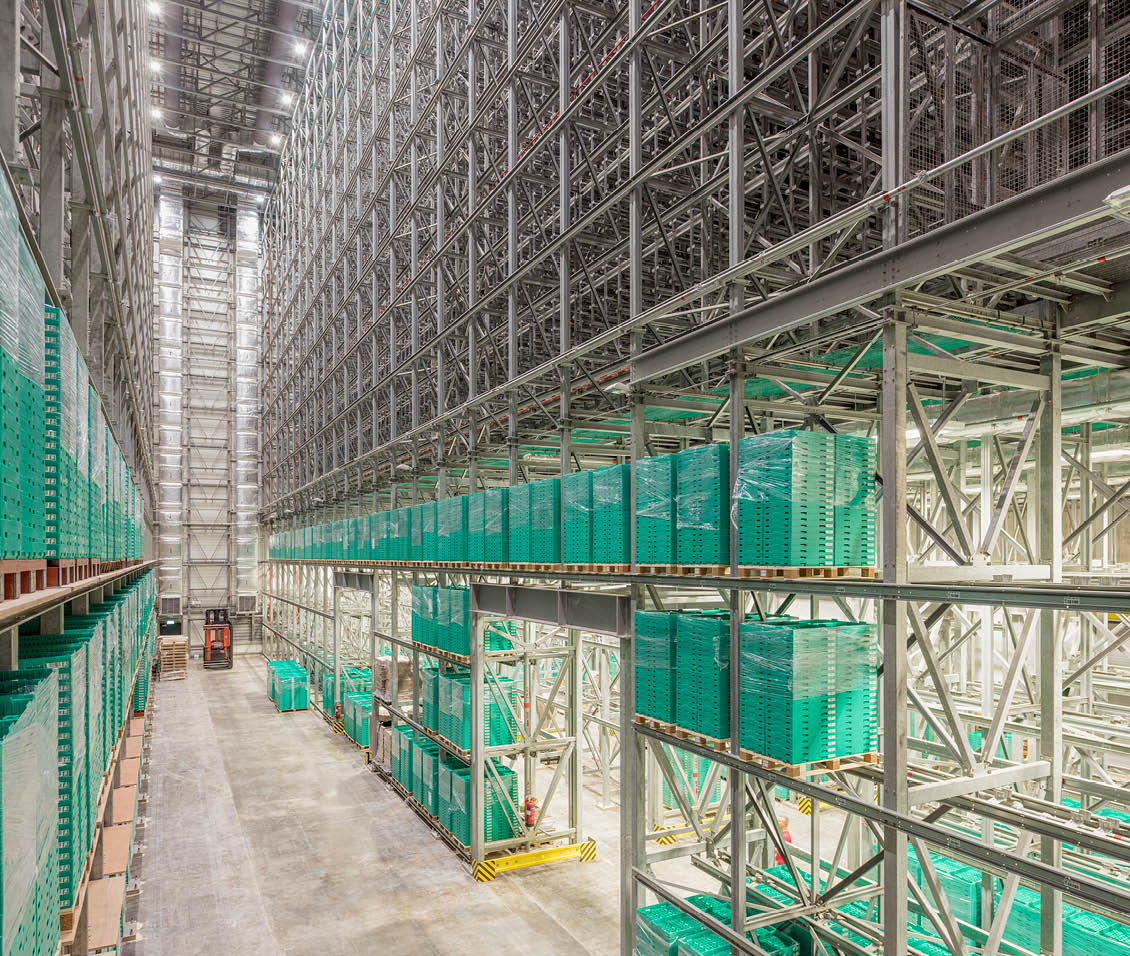
Das Lager des GDC beeindruckt auch aus der Vogelperspektive mit seinen Dimensionen.
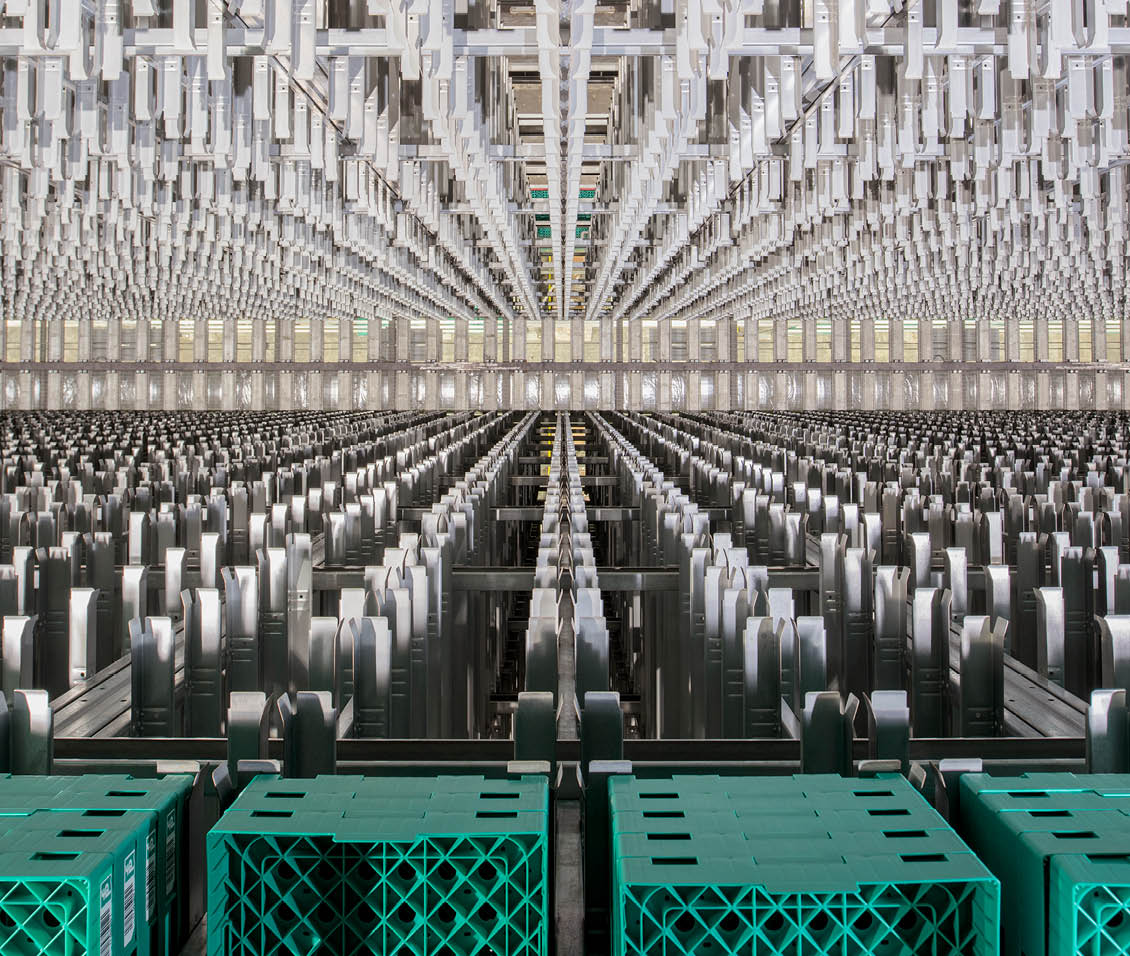
Ideale Bedingungen in Singapur
Welche Zeitersparnis allein die automatische Einlagerung bringt, erläutert der Leiter des GDC in Singapur, Han Thanh Hong: „Wenn früher ein 40-Fuß-Container angeliefert wurde, brauchten wir zwei Tage, um die Ware zu erfassen und in die Regale zu befördern. Heute schaffen wir das in drei Stunden.“ Aufbau und Technik des Mannheimer Logistikzentrums wurden im GDC nicht eins zu eins übernommen. „Wir haben die Erfahrungen aus Deutschland genutzt und das System weiterentwickelt. Die aktualisierte Version wurde dann nach der Einführung in Singapur auf Mannheim zurückübertragen, sodass wir uns heute auf demselben, verbesserten Stand befinden.“
Die Ausgangsposition in Singapur war ähnlich wie in Mannheim. Das alte Logistikzentrum platzte aus allen Nähten, eine Beschleunigung der Prozesse wurde immer dringlicher. 80 Prozent der Produkte von Pepperl+Fuchs stammen aus den Standorten im Stadtstaat sowie in Vietnam und Indonesien. So lag es nahe, das neue weltweite Verteilzentrum in der südostasiatischen Region aufzubauen. „Singapur bot mit seiner modernen Infrastruktur und Verkehrsanbindung, einem unternehmensfreundlichen Regelwerk und den guten Bedingungen für Im- und Exportgeschäfte die besten Voraussetzungen“, betont Han Thanh Hong.
Bewährtes fortwährend weiterentwickeln
Auch in Houston entsprechen Aufbau, Technik und „Betriebssystem“ den anderen beiden Zentren. Das dortige neue UDC soll zunächst den nord- und später auch den südamerikanischen Markt bedienen. „Darüber hinaus können wir es als regionalen Showroom für unsere Logistikprodukte nutzen“, freut sich Külken. „Wir können dort interessierten Kunden die Leistungsfähigkeit unserer Sensoren im laufenden Betrieb demonstrieren.“
Vor allem profitieren die Kunden aber von der noch zuverlässigeren und schnelleren Belieferung, die mit den optimierten Prozessen und der hohen Qualität der logistischen Abläufe möglich wird. Diese unterliegen übrigens einem kontinuierlichen Verbesserungsprozess, im Unternehmen auch als LOOP (Lean Operation and Organization in Processes) bekannt. „Dabei kann sich herausstellen, dass ein zusätzliches Werkzeug an einem bestimmten Arbeitsplatz viele Wege spart“, erläutert Külken.
Auch in Richtung digitaler Transformation können die Lager ihre nächsten Schritte aufnehmen. „Dank des hohen Automatisierungsgrades ist die ‚digitale Logistik‘ greifbar und in laufende Prozesse integrierbar. Mit dem ständigen Zugriff auf alle Daten und den differenzierten Möglichkeiten der Feinsteuerung entsprechen die Abläufe in unseren Distribution Centern auch den Prinzipien einer vertikalen und horizontalen Vernetzung. Das dynamische Wartungsmanagement verbindet schon heute Echtzeitdaten zu einer intelligenten Anlage – seien es die Informationen von Motoren und Bremsen der Regalbediengeräte oder den optoelektronischen Sensoren des Querverschiebewagens. Diese Prognosemodelle ermöglichen maschinelles Lernen und ebnen somit den Weg für eine vorausschauende Instandhaltung, die plötzliche Ausfälle deutlich verringern wird“, resümiert Külken.