5. Februar 2019
Fit for Purpose
Nicht nur innerhalb der Gesellschaft hat sich das Bewusstsein für den Umwelt- und Klimaschutz sowie auch das Sicherheitsbedürfnis im Laufe der letzten Jahre stark gewandelt – auch bei Unternehmen und Institutionen, darunter auch die Chemie, Petrochemie und Pharmazie, sind diese Themen immer mehr in den Fokus gerückt. Wir haben hierzu mit zwei Experten von Pepperl+Fuchs gesprochen.
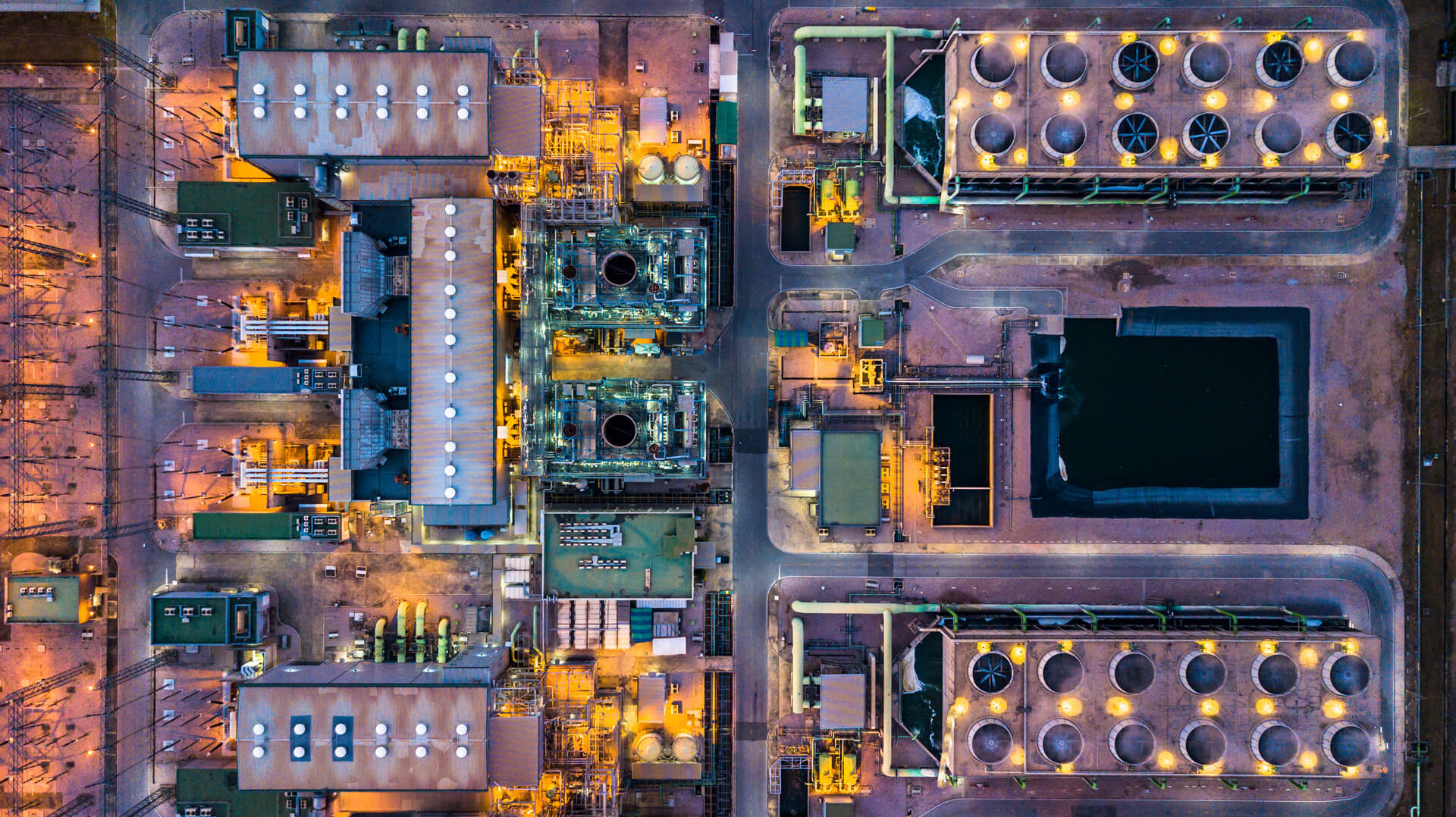
Um den hohen Sicherheitsanforderungen gerecht zu werden, erweitert Pepperl+Fuchs kontinuierlich das Portfolio an Produkten und Lösungen für den elektrischen Explosionsschutz, die Anwendern den Arbeitsalltag erleichtern und Anlagen noch sicherer machen. Herbert Schober, Executive Vice President Electrical Protection Equipment & Solutions Global und Rainer Nägle, zuständiger Produktgruppenleiter für den elektrischen Explosionsschutz bei Pepperl+Fuchs geben Einblicke in die Entwicklungen und Trends im elektrischen Explosionsschutz.
Herbert SchoberDer elektrische Explosionsschutz umfasst sämtliche Technologien des Explosionsschutzes mit den Zündschutzarten Eigensicherheit Ex i, erhöhte Sicherheit Ex e, druckfeste Kapselung Ex d und Ãberdruckkapselung Ex p sowie zahlreiche weitere Methoden, die weniger Relevanz haben. Im Bereich der Automatisierungstechnik ist Pepperl+Fuchs bereits seit über 70 Jahren aktiv. Um den Explosionsschutz in diesen Anwendungsbereichen sicherzustellen, kommen vorwiegend die Zündschutzarten Eigensicherheit und erhöhte Sicherheit zum Einsatz. In der Niederspannungstechnik hingegen werden zusätzlich zur Zündschutzart erhöhte Sicherheit auch die druckfeste Kapselung und die Ãberdruckkapselung verwendet. Dieses „klassische Explosionsschutzgeschäft“ hat Pepperl+Fuchs vor rund 15 Jahren als Ergänzung des bestehenden Portfolios mit den Zündschutzarten Eigensicherheit und erhöhte Sicherheit aufgenommen.
Herbert SchoberAls Marktführer im Explosionsschutz für die Automatisierungstechnik genießt die Marke Pepperl+Fuchs eine sehr positive Reputation und unsere Kunden kennen uns seit Jahrzehnten als starken, zuverlässigen, kompetenten Partner. Unser Know-how und die Erfahrung aus der Automatisierungstechnik haben es uns vor 15 Jahren leichter gemacht, im Bereich der Niederspannungstechnik Fuß zu fassen, mit unserem Produktportfolio zu wachsen und uns in diesem Marktumfeld behaupten zu können. Heute können wir aus beiden Disziplinen Synergien bilden, um optimale Kundenlösungen für den Einsatz in rauen Industrieumgebungen und explosionsgefährdeten Bereichen zu entwickeln.
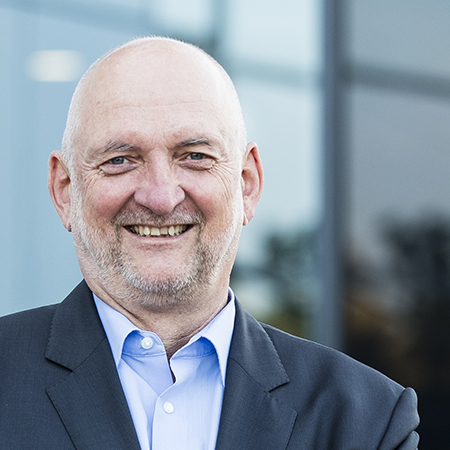
Herbert SchoberWir haben ein umfassendes Portfolio an elektrischen Komponenten und Systemen für den Explosionsschutz und legen großen Wert darauf, unseren Kunden eine Komplettlösung anzubieten, nicht nur ein Produkt — und das sowohl auf lokaler als auch auf globaler Ebene. Diese Lösungen werden applikationsspezifisch und in enger Zusammenarbeit mit unseren Kunden entworfen, besprochen und schließlich in unseren SECs, den sogenannten Solution Engineering Centern, gefertigt. Die Betreuung unserer Kunden reicht von der Projektspezifikation über den Bau der Kundenlösung bis hin zur Inbetriebnahme in der Anlage. Insgesamt sind wir mit sechs Solution Engineering Centern auf der ganzen Welt vertreten — zwei davon befinden sich in Europa, drei in Asien bzw. Australien sowie eines in den USA. Zusammen mit einem flächendeckenden Vertriebsnetz sowie eigenen Gesellschaften und Handelsorganisation an über 80 Standorten weltweit können wir die Bedarfe an elektrischen Explosionsschutzlösungen auf allen Kontinenten decken — sei es in der chemischen, petrochemischen oder pharmazeutischen Industrie. Unsere Produkte finden aber auch in der Lebensmittelindustrie Einsatz, etwa dann, wenn es sich um staubexplosionsgefährdete Bereiche handelt.
Herbert SchoberEs ist nicht die technische Grundlage des elektrischen Explosionsschutzes, die sich verändert, sondern vielmehr die Anwendung sowie die Erwartungshaltung der Kunden. Noch vor 15 Jahren hatten alle größeren Betriebe weitaus mehr Ressourcen zur Verfügung sowie eigene Fachabteilungen, die eigenständig planen und projektieren konnten. Es gibt zwar nach wie vor Fachspezialisten und Gremien, die sich hiermit beschäftigen; im Zuge der sich ändernden wirtschaftlichen Lage der letzten Jahre hat sich diese Aufgabe jedoch komplett auf die Hersteller verlagert. Wir stellen außerdem fest, dass Kunden vermehrt nach vorkonfektionierten, kundenspezifischen Lösungen suchen, wie sie beispielsweise in unseren Solution Engineering Centern entstehen.
Rainer NägleEine weitere einschneidende Entwicklung ist der Verfall der Öl- und Gaspreise seit 2011: Wenn üblicherweise zwischen 30 % und 40 % des Absatzes in die Öl- und Gasmärkte fließen, diese jedoch um ca. 50 % eingebrochen sind, zieht das Probleme für die gesamte Branche nach sich. Dadurch hat sich natürlich auch die Wettbewerbssituation innerhalb der letzten Jahre deutlich verschärft: Produkte und Lösungen müssen „fit for purpose“ beziehungsweise „fit for market“ sein — sprich Technik und Service müssen stimmen und nicht zuletzt der Preis.
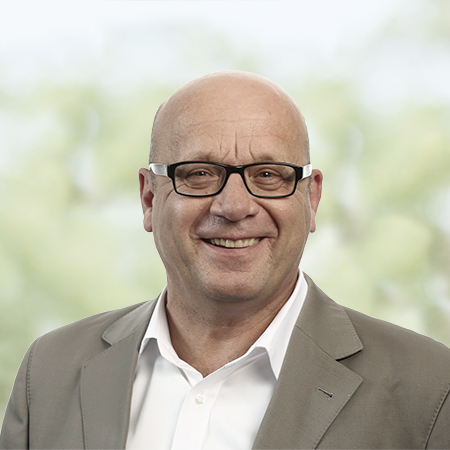
Rainer NägleDa wir bei Pepperl+Fuchs über ein sehr diversifiziertes Portfolio verfügen, sind wir nicht ausschließlich von den Entwicklungen in der Prozessautomation abhängig. Wir bewegen uns mit unserem zweiten Geschäftsbereich, der Fabrikautomation, in einem völlig anderen Branchenumfeld und können solche Schwankungen besser abfedern. Deshalb war es uns trotz der schwierigen Situation am Öl- und Gasmarkt möglich, in die Entwicklung neuer Lösungen für den elektrischen Explosionsschutz zu investieren und innerhalb der letzten fünf bis sechs Jahre deutlich offensiver zu agieren als andere Hersteller.
Herbert SchoberEin wichtiges Kriterium ist beispielsweise die Möglichkeit, mit kleineren, leichteren und robusteren Materialien arbeiten zu können. Aber auch im Bereich der Materialtechnik hat sich innerhalb der letzten 15 Jahre einiges getan — was Kunststoffe und glasfaserverstärkte Polyester anbelangt zum Beispiel. Erst kürzlich haben wir eine völlig neue Gehäuseserie aus glasfaserverstärktem Kunststoff für Klemmen- und Steuerkästen (Ex e und Ex i) auf den Markt gebracht, die Umgebungstemperaturen von -60 °C bis zu +65 °C standhält und über weitere Funktionalitäten verfügt, die sowohl die Anlagenplanung als auch das Handling maßgeblich erleichtern.

Herbert SchoberBei der Produktentwicklung und -verfügbarkeit, und das betrifft nicht nur den Explosionsschutz, geht es zunehmend um Schnelligkeit. Kunden erwarten von uns, dass wir in sehr kurzer Zeit für sie maßgeschneiderte Lösungen bereitstellen. Die Lieferzeit dieser Lösungen soll idealerweise so kurz sein wie die eines Standardprodukts. Aus diesem Anspruch heraus haben wir für den europäischen Raum eine sogenannte „5-Tage-Initiative“ ins Leben gerufen, um Klemmen- und Steuerkästen sowie Befehlsgeräte innerhalb von fünf Arbeitstagen zu fertigen. Auch wenn der Versandweg noch hinzukommt, verläuft die Auftragsabwicklung insgesamt deutlich schneller, als unsere Kunden es erwarten.
Herbert SchoberDieser Ansatz kombiniert leistungsfähige Hilfsmittel, um einen Kundenauftrag in eine technische Lösung umzusetzen: Fertigungsunterlagen werden automatisiert erstellt und gehen schließlich in eine sogenannte Zellenfertigung, in der ein Team von Mitarbeitern den Auftrag hat, den Kundenauftrag innerhalb von fünf Arbeitstagen komplett abzuwickeln. Auch wenn die Prozesse insgesamt sehr komplex sind, konnten wir durch diese Art der Produktion bereits nach einer kurzen Anlaufphase ein größeres Volumen umsetzen und sind damit sogar schneller als fünf Arbeitstage. Und das Wichtigste: unsere Kunden sind begeistert von dieser Lieferperformance.
Rainer NägleIn technischer Hinsicht zwar kaum, allerdings gibt es kommerzielle Grenzen. Der teilweise sehr hohe Engineering-Aufwand muss sich lohnen und letztendlich auch bezahlbar sein, besonders wenn es um Aufträge mit Stückzahl eins bis drei geht.
Herbert SchoberDarüber hinaus gibt es auch technologische Grenzen, was beispielsweise internationale Zulassungen betrifft, die teilweise sehr schwierig zu erhalten sind und einen hohen Aufwand erfordern.
In fünf Tagen zum Wunschprodukt
Mit unserem umfangreichen Angebot an Befehls- und Meldegeräten, Klemmenkästen sowie Sicherheits- und Lastschaltern erfüllen wir Ihren Kundenwunsch nach kurzer Lieferzeit – ohne Abstriche bei der Variantenvielfalt.
Rainer NägleEinen Aspekt, den wir zukünftig sehen, ist die verstärkte Zusammenarbeit mit dem Business-Bereich der Fabrikautomation mit der Zielsetzung, Sensorik vermehrt in explosionsgefährdete Umgebungen zu bringen und das Know-how aus beiden Bereichen bestmöglich zu nutzen. Dabei beschäftigen wir uns vorwiegend mit zwei Themen: Zum einen müssen wir die optische oder elektromagnetische Strahlung, die aus einem Sensor austritt, sicher machen — auch vor dem Hintergrund, dass es mittlerweile neue Normen und Limits gibt, ab wann eine optische Strahlung eine Gasatmosphäre entzünden kann. Zum anderen spielen in der Kommunikationstechnik Lichtwellenleiter im explosionsgefährdeten Bereich eine immer größere Rolle.
Herbert SchoberDie zukünftige Herausforderung besteht darin, Techniken, die es im nicht explosionsgefährdeten Bereich gibt, genau dorthin zu bringen. Unsere Kunden haben die Erwartungshaltung und den Wunsch, die Produkte, die sie aus dem privaten und dem Büroalltag kennen, auch im explosionsgefährdeten Bereich einsetzen zu können. Das umfasst natürlich nicht nur die Geräte, sondern auch die dazugehörige Infrastruktur — hier werden wir es in Zukunft vermehrt mit Antennentechnik und dem Thema Abschirmung zu tun haben. Fest steht jedenfalls, dass sich explosionsgefährdete und nicht explosionsgefährdete Bereiche in den nächsten fünf Jahren technologisch stärker annähern und weiter zusammenwachsen werden, weil das Anforderungsprofil der Kunden dasselbe ist. Deshalb müssen wir unsere Produkte aus der Sensortechnik so „verpacken“, dass sie zuverlässig und sicher in explosionsgefährdeten und rauen Industrieumgebungen betrieben werden können.
Rainer NägleUnd dabei steht die Anwenderfreundlichkeit an oberster Stelle — so auch bei unserer neuesten GR-Gehäuseserie aus glasfaserverstärktem Polyester. Hier liegt der Mehrwert in der Handhabbarkeit, wie der Tatsache, dass die Installation durch nur eine Person erfolgen kann. Die großen Entwicklungen im elektrischen Explosionsschutz werden die kleinen Dinge sein, die dem Anwender das Leben leichter machen.