25. August 2019
Vernetzt bis in den letzten Meter
IO-Link gilt als die Enabling Technology für Industrie 4.0 schlechthin. Als weltweit erste hersteller- und systemunabhängige Technologie ermöglicht IO-Link eine durchgängige bidirektionale Kommunikation zwischen der Steuerungsebene und der untersten Sensor-/Aktorebene – dem „letzten Meter“. Experten von Pepperl+Fuchs geben Einblick in die vielseitigen Möglichkeiten und Vorteile der Schnittstelle.
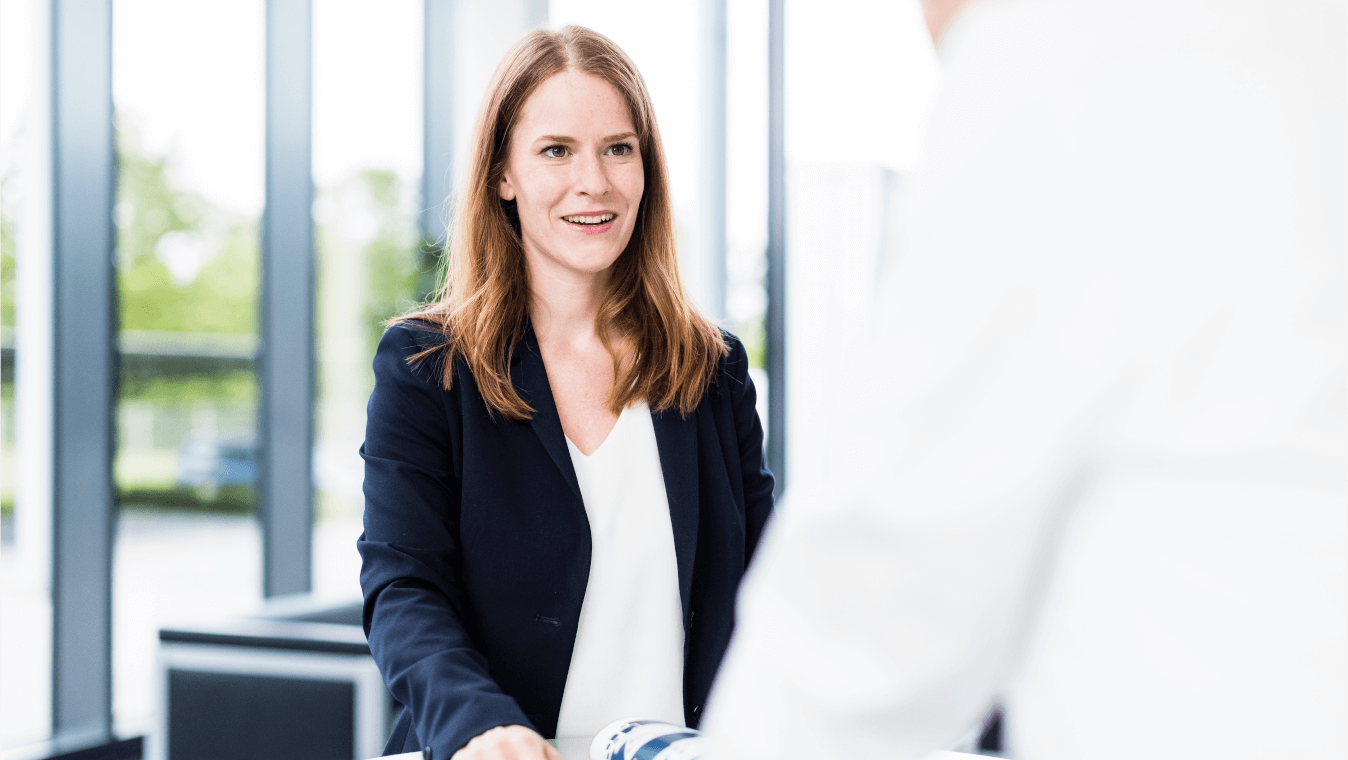
Der Erfolg von IO-Link spiegelt sich nicht nur in der steigenden Mitgliederzahl der IO-Link-Community wider, die den Kommunikationsstandard ins Leben gerufen hat und mittlerweile über 200 Mitglieder zählt. „Mit mehr als 15 Millionen Knoten im Feld hat die Punkt-zu-Punkt-Verbindung ihren festen Platz in der Industrie und ist gefragter denn je“, weiß Hartmut Lindenthal. Gemeinsam mit seinen Kollegen bei Pepperl+Fuchs beschäftigt er sich von Beginn an mit den Anforderungen an IO-Link-Geräte für eine zuverlässige, bidirektionale Kommunikation im Automatisierungsumfeld.
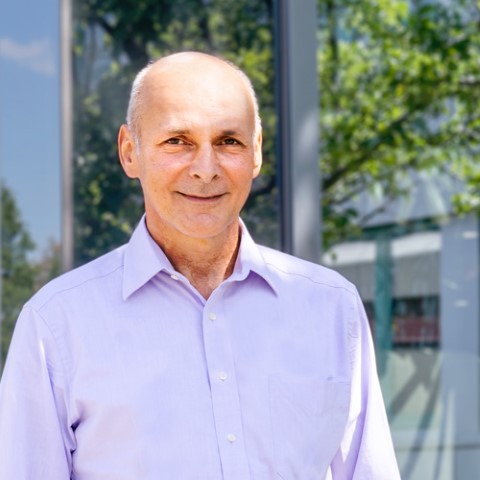
Von der Vision zum internationalen Industriestandard
Erste Bestrebungen in Richtung eines Standards für intelligente Sensorik und Aktorik wurden bereits 2005 im Rahmen einer herstellerübergreifenden Arbeitsgruppe der Profinet-Nutzerorganisation gemacht: „Damals hatte man den Anspruch, konventionelle und intelligente Sensorik an einen SPS-Port anschließen zu können“, erinnert sich Lindenthal an die Geburtsstunde von IO-Link und merkt an: „Doch bis schließlich eine enge und effiziente Zusammenarbeit zwischen den einzelnen Firmen entstand, hat es noch einige Zeit gedauert.“ Mit der gemeinsamen Vision, eine offene, systemunabhängige und gleichzeitig kostengünstige I/O-Technologie zu entwickeln, wurde 2006 die IO-Link-Community gegründet.
Nachdem sich inzwischen 40 Unternehmen dem Standard angenommen hatten, waren 2009 bereits zahlreiche Master und Geräte mit IO-Link-Schnittstelle der Systemspezifikation 1.0 auf dem Markt. Zwei Jahre später kamen mit der Version 1.1 weitere Anforderungen und Systemfunktionen hinzu — darunter auch die Datenhaltung, also der Parameterabgleich zwischen IO-Link-Master und -Gerät. Diese Spezifikationen bildeten wiederum die Grundlage für einen internationalen Standard, der IEC-Norm 61131-9. „Seither hat sich nicht nur der Bekanntheitsgrad von IO-Link erhöht, auch die Mitgliederzahl der IO-Link-Community hat sich mehr als verdreifacht“, so Sonja Armbruster, die das Thema IO-Link als verantwortliche Produktmanagerin im Bereich Industrielle Kommunikation bei Pepperl+Fuchs betreut und mit vorantreibt.
Internationaler Standard
Die International Electrotechnical Commission (IEC) führt IO-Link seit 2013 unter der Norm IEC 61131-9 mit der Bezeichnung Single-drop digital communication interface for small sensors and actuators, kurz SDCI.
Eine starke Verbindung
Da sich die leistungsstarke Punkt-zu-Punkt-Verbindung auf einer dreiadrigen Standardleitung betreiben lässt, ist mit IO-Link eine abwärtskompatible Schnittstelle für binäre Standardsensoren entstanden, die gleich eine ganze Reihe von Vorzügen mit sich bringt, wie Lindenthal bestätigt: „Dank identischer Verdrahtung können Anwender durch einen Mischbetrieb von digitalen und IO-Link-Signalen den Nutzungsgrad ihrer Anlagen optimieren. „Ein entscheidender Vorteil liegt darin“, so Lindenthal, „dass sich IO-Link-Geräte problemlos an herkömmliche Digitaleingänge anschließen lassen und kein zusätzlicher Verkabelungsaufwand anfällt.“
„Selbst wenn ein Gerät in ein bestehendes Netzwerk integriert werden soll, ist dies dank einheitlicher Gerätebeschreibungsdateien ohne weiteres möglich“, erklärt Armbruster die Plug-and-play-Funktion von IO-Link-Geräten: „Die Technologie ist bewusst so konzipiert worden, dass sie völlig hersteller- und systemunabhängig arbeitet.“ Somit bildet IO-Link eine ideale Basis für unzählige Anwendungen in der Industrie 4.0.
Transparenz für ein Mehr an Daten
Heute ist IO-Link als Kommunikationsprotokoll für den „letzten Meter“ der Sensor-/Aktor-Ebene auf dem gesamten Globus in nahezu allen Industriebranchen verbreitet. Auf dem Weg dorthin haben Sensoren und Aktoren eine rasante Entwicklung erfahren, um Daten nicht mehr nur über einfache binäre oder analoge Standardschnittstellen zu übertragen: „Seit Ende der 90er-Jahre sind in Sensoren standardmäßig Mikrocontroller verbaut“, erklärt Lindenthal: „Sie bilden quasi das Gehirn der Sensoren.“ Ausgestattet mit dieser zusätzlichen Geräteintelligenz sind IO-Link-Sensoren in der Lage, neben der Übertragung von Messwerten und Schaltpunkten auch Parameter zu speichern sowie vielfältige zusätzliche Informationen zu liefern — etwa über die Signalqualität und den Gerätezustand. Dies schafft eine nie zuvor dagewesene Transparenz für mehr Daten, die Anwendern umfangreiche Diagnosen erlauben und den Weg zur zustandsorientierten Wartung ebnen — wohlgemerkt während des laufenden Betriebs.
„All diese Informationen zur Prozessoptimierung und zur zielgerichteten Wartung hatten Anwender zuvor nur mit höherwertigen Sensorsystemen in geschlossenen Feldbus-Umgebungen“, betont Lindenthal. „Dass bereits alle Anforderungen für die bidirektionale Kommunikation zwischen Feldebene und übergeordnetem IT-Netzwerk gegeben sind, ist ein weiterer Pluspunkt für die Technologie“, fügt er ergänzend hinzu.
Brücke zur IT
Die in der Industrie 4.0 geforderte Datenkontinuität beginnt bei den Sensordaten und reicht bis hin zur intelligenten Cloud-Lösung. „Eine Anbindung von IO-Link-Feldgeräten an die übergeordnete IT-Infrastruktur lässt sich problemlos mit Master-Baugruppen wie den multiprotokoll- und multilinkfähigen Feldbusmodulen der Serie ICE von Pepperl+Fuchs realisieren“, erklärt Armbruster. Da die Kommunikation der IoT-Protokolle (z. B. MQTT, OPC UA) parallel zur Feldbuskommunikation stattfindet, wird der Datenaustausch auf der Feldebene nicht beeinträchtigt.
Ausgewählte Sensordaten lassen sich in Cloud-Anwendungen interpretieren und verarbeiten. Für dieses Zukunftsszenario ließe sich beispielsweise ein Software-Dienst entwickeln, der auf den unterschiedlichsten Plattformen nutzbar ist und dort die Interpretation von Sensordaten anhand der IODD übernimmt. Maschinenspezialisten könnten damit bequem via App von überall aus auf die Maschinendaten zugreifen, den Zustand ihrer Anlage überwachen und bei Bedarf Instandhaltungen durchführen, ohne sich in sensortechnische Details einarbeiten zu müssen.
„Dies würde Anwendern die tägliche Arbeit deutlich erleichtern“, so Armbruster über die Vorzüge eines solchen Software-Services, den das Pepperl+Fuchs Start-up Neoception problemlos entwickeln könnte. „Dies entspricht dem Predictive-Maintenance-Gedanken auf ganzer Linie, vor allem, wenn man bedenkt, dass aussagekräftige Analysen in Zukunft so wichtig sein werden wie die Produkte selbst“, fügt sie überzeugt hinzu.
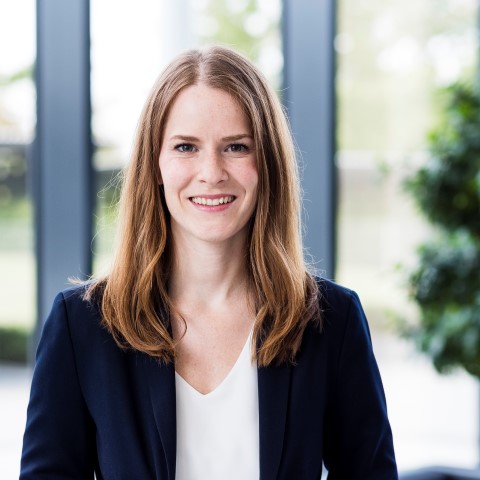
Längst keine Zukunftsmusik mehr: Safety, JSON und OPC UA
Während in der vertikalen Betrachtung der Schwerpunkt auf Cloud-Anbindungen und entsprechenden Apps liegt, stehen im Bereich der horizontalen Sichtweise Themen wie die Profilbildung oder die Spezifikationserweiterung zu IO-Link Wireless und Safety im Fokus.
So werden beispielsweise Feldgeräte, die IO-Link sprechen und über eine Sicherheitsfunktion verfügen, zukünftig in der Lage sein, einen sicheren Austausch von zyklisch übertragenen Ein- und Ausgabedaten (Prozessdaten) und azyklisch übermittelten Diagnose- bzw. Parameterinformationen (On-Request-Daten) herzustellen.
Gleichzeitig halten industrielle M2M-Kommunikationsprotokolle (kurz für Maschine-zu-Maschine) zunehmend Einzug in das System, wie Lindenthal ausführt: „Dazu gehört etwa auch die seit 2018 bestehende Kooperation mit der OPC Foundation, die sich unter anderem mit der Spezifikation für das Mapping von OPC UA für IO-Link beschäftigt.“
„Außerdem arbeitet die Community gerade an der Definition eines JSON-Austauschformats zur Umsetzung schlanker Sensor-zu-Cloud-Applikationen“, wie Armbruster mit Blick auf die Zukunft verrät. Auch Lindenthal ist sich sicher, dass die kommenden Jahre noch einige spannende Entwicklungen im Bereich IO-Link bereithalten: „Ich bin überzeugt, dass die Schnittstelle auch in Zukunft ein wesentlicher Baustein von Industrie-4.0-Lösungen sein wird und Anwender der Automatisierungsbranche zunehmend von den vielfältigen Möglichkeiten des Systems profitieren werden.“
Elektronische Gerätebeschreibung
Aufgrund der Kommunikationsfähigkeit stehen in den Geräten ein Vielzahl von Funktionen mit zugehörigen Einstellmöglichkeiten und Statusinformationen zur Verfügung.
Um diese Daten und Informationen benutzerfreundlich darzustellen und die Bedienung zu vereinfachen, wurde das IODD-Format, kurz für IO Device Description, als Standardbeschreibungssprache definiert. Diese Beschreibung beinhaltet unter anderem Details zur Parameterstruktur und —wertebereichen sowie Informationen zu unterstützten Produktvarianten. Für jedes IO-Link-Gerät steht eine IODD zur Verfügung, die sich wiederum auf allen IO-Link-fähigen Systemumgebungen interpretieren und darstellen lässt. Dadurch sind alle IO-Link-Geräte systemunabhängig bedienbar.