17. Februar 2021
Qualitätssicherung nach dem Kaizen-Prinzip
Kein Unternehmen prägte die japanische Philosophie des Kaizen, dem Streben nach kontinuierlicher Verbesserung, mehr als Toyota. Bis heute setzt der japanische Automobilhersteller weltweit auf permanente Optimierung seiner Produktions- und Montageprozesse. Ultraschallsensoren und ein AS-Interface-Netzwerk von Pepperl+Fuchs ermöglichen effiziente Abläufe in der Qualitätssicherung bei Toyota.
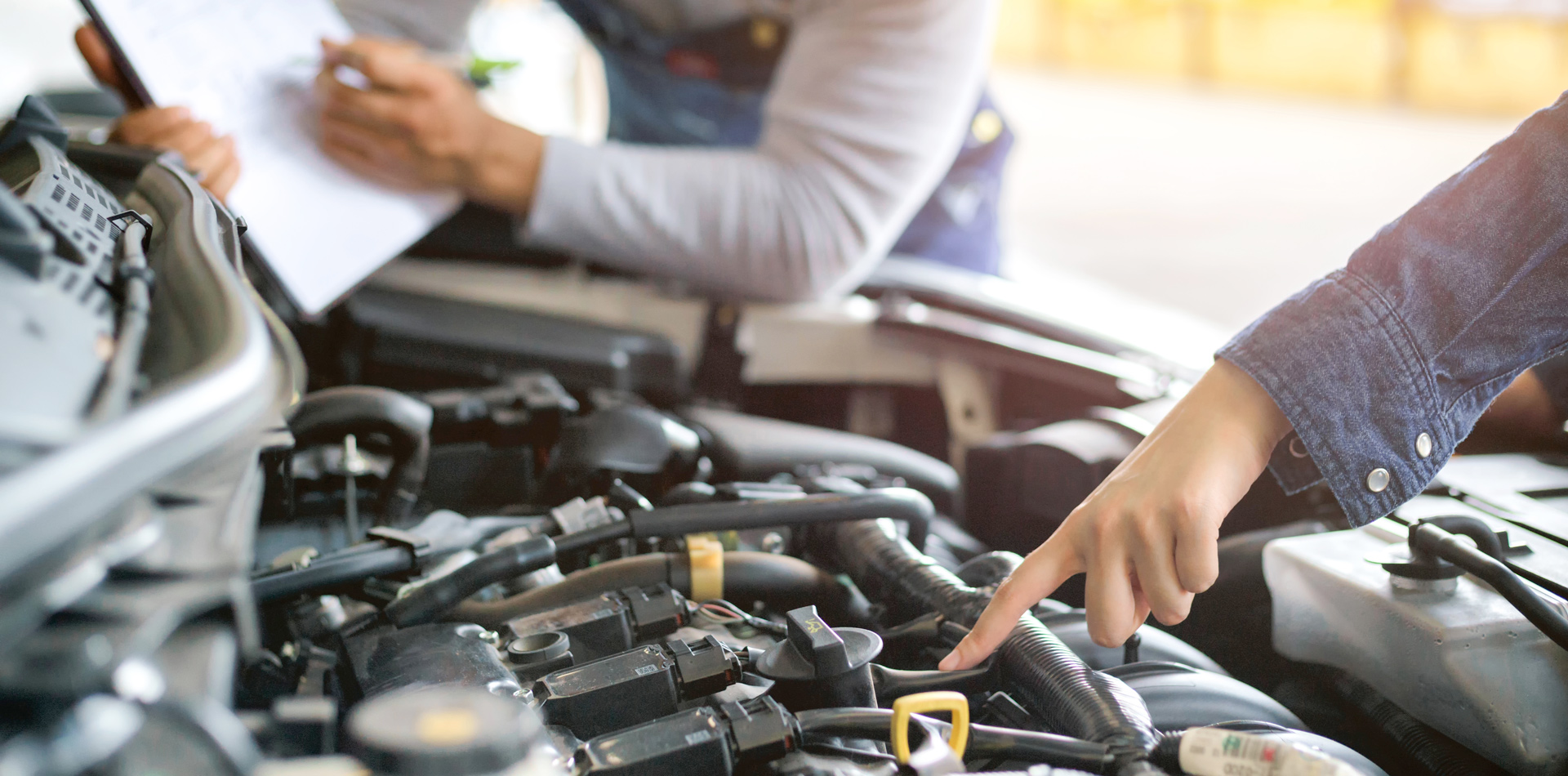
Rund 10.000 Teile müssen zusammengebaut werden, bis ein Fahrzeug vom Band rollen kann. Elektroautos brauchen zwar etwas weniger Teile als jene mit Verbrennungsmotor, die Montage bleibt dennoch in jedem Fall ein hochkomplexer Prozess aus Schweißen, Schrauben, Fügen, Kleben, Lackieren und Justieren. In modernen Automobilfabriken sind die meisten Schritte hochgradig automatisiert. Die Fahrzeuge entstehen entlang ausgeklügelter und verzweigter Fertigungsstraßen „am Fließband“ — auch wenn diese heute in der Regel keine Bänder sind, sondern Hängebahnen, elektrische Förderstrecken oder fahrerlose Transportsysteme. Doch ob Band oder Bahn: Am Ende rollt der fertige Wagen auf eigenen Rädern weiter.
Auf dem Rollenprüfstand
Mit einigen Liter Benzin im Tank gelangt das Fahrzeug aus der Montage zur Qualitätssicherung. Toyota Motor Manufacturing UK produziert in Burnaston bei Derby neben klassischen Verbrennern auch Hybride. Bei ihnen muss die Batterie ebenfalls geladen sein, damit man die umfassende Funktionsprüfung der Autos einschließlich der Antriebsstränge durchführen kann. Auf einem Rollenprüfstand werden Motor, Getriebe und Radlauf in allen Gängen und Geschwindigkeiten ausgefahren, die Bremsen getestet, zahlreiche Messungen durchgeführt und auch die im Fahrzeug eingebauten Sensoren werden dabei abgeglichen. Auch wenn die Prüfstände mit viel High-Tech ausgestattet sind, wird der Prüfdurchlauf von den Mitgliedern der Qualitätsteams individuell gesteuert.
„Die Autos kommen in einem definierten Takt aus der Montage bei uns an, und wir übergeben sie nach vollzogener Prüfung wieder an einen Fließbandprozess in der Endkontrolle“, erklärt David Waters, Group Leader Quality Assurance bei Toyota Motor Manufacturing UK. „Unsere Abläufe hängen sehr stark von der individuellen Arbeit der einzelnen Teammitglieder ab. Früher kam es vor, dass unsere Arbeitsschritte nicht immer im Takt mit den automatisierten Prozessen waren. Manchmal ging es zu langsam, manchmal auch zu schnell. So konnten gelegentlich Engpässe entstehen, die Übergänge zwischen den Prozessschritten verliefen nicht immer so reibungslos, wie wir uns das wünschten.“
In der Qualitätssicherung werden die fertig montierten Fahrzeuge zunächst auf zwei Linien mit je vier Stationen aufgeteilt. Neben dem Rollenprüfstand gibt es dort zum Beispiel eine schalldichte Kammer für Vibrationstests. An einer anderen Station wird geprüft, ob die Karosserie auch bei Starkregen wasserdicht ist. Damit die Abläufe optimal ineinandergreifen können, benötigen die Mitarbeiter in der Qualitätssicherung eine Rückmeldung über ihr Arbeitstempo. Die Grundlage dafür bieten Ultraschallsensoren vom Typ UC2000-L2 von Pepperl+Fuchs. Sie sind an jeder Station über dem Stellplatz des Fahrzeugs montiert und erkennen, ob sich dort ein Fahrzeug befindet oder nicht.
Zuverlässige Prozessabläufe mit Ultraschallsensorik
„Wir haben früher für ähnliche Zwecke mit optischen Sensoren gearbeitet, doch diese waren für diese Anwendung nicht optimal“, erinnert sich Waters. „Sie kamen zum Beispiel mit manchen Arten von lackiertem Kunststoff und bestimmten Farben nicht sehr gut zurecht. Das Licht der Leuchtröhren, die wir für die Inspektion nutzen, hat sie irritiert, ebenso die Panorama-Glasdächer oder Lichtreflexe von spiegelnden Oberflächen.“
Ultraschallsensoren werden von solchen optischen Eigenschaften nicht beeinflusst. Da sie zur Objekterkennung Schallwellen nutzen, haben Farbe, Transparenz und Spiegelung einer Oberfläche keinen Einfluss auf ihre Funktion. Ihr Messprinzip hat darüber hinaus weitere Vorteile: Die sogenannte Schallkeule — der kegelförmige Messbereich — deckt nicht einen kleinen Punkt, sondern eine größere Fläche ab. Das erlaubt auch bei unregelmäßigen Konturen eine sichere Erfassung. Der Durchmesser der Schallkeule lässt sich zudem an die jeweilige Anwendung anpassen.
Der Ultraschallsensor meldet immer zuverlässig, ob sich in seinem Messbereich ein Fahrzeug befindet oder nicht. Diese Information hilft der Qualitätssicherung auch, die Qualität der eigenen Arbeit zu kontrollieren, und zwar auf einen Blick: Eine Grün-Gelb-Rot-Signallampe zeigt an, ob der jeweilige Prüfdurchgang noch in der optimalen Zeitspanne abläuft oder bereits zu lange dauert. Die Mitarbeiter wissen jederzeit, wo sie mit ihrer Arbeit stehen, und die Abteilungsleitung hat immer einen umfassenden Überblick über die Abläufe und kann Engpässen schneller entgegenwirken.

An jeder Station über dem Stellplatz des Fahrzeugs erkennen Ultraschallsensoren vom Typ UC2000-L2, ob sich dort ein Fahrzeug befindet. Die Signallampe zeigt an, ob der jeweilige Prüfdurchgang noch in der optimalen Zeitspanne abläuft.
Nach der letzten Station werden die Wagen zwischengeparkt. Auch hier zeigen Signallichter an, ob in der linken oder der rechten Reihe ein freier Platz zum Abstellen des geprüften Fahrzeugs zur Verfügung steht. Bei dieser Anwendung genügen die Signalfarben Grün und Rot. Die Stellplätze werden ebenfalls von Ultraschallsensoren der VariKont-Baureihe L2 überwacht.
Netzwerkaufbau bei laufendem Betrieb
„Toyota hatte uns für die Einrichtung der Anwesenheitsüberwachung ein wichtiges Kriterium vorgegeben“, erinnert sich David Nield, Applications Development Manager bei Pepperl+Fuchs UK. „Die Installation sollte den laufenden Betrieb nicht stören und möglichst in den Arbeitspausen stattfinden können. Das war einer der Gründe, warum wir hier ein AS-Interface-Netzwerk empfohlen haben.“
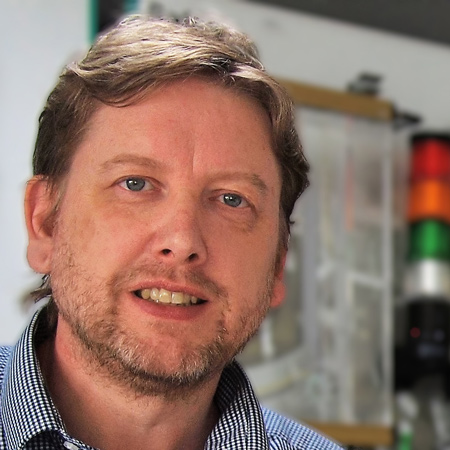
Das AS-Interface-System ist eine ebenso simple wie kostengünstige Verdrahtungstechnik für Sensoren und Aktoren. Zu seinen Vorteilen gehört, dass für die Stromversorgung und die Datenkommunikation ein einziges Flachkabel genügt. Der Anschluss erfolgt mit einer Piercing-Technik. Sie macht die Installation neuer Geräte zum Kinderspiel, da sich neue Geräte mithilfe der Piercingdornen einfach an das Flachkabel anbringen lassen. Auch deshalb ist AS-Interface zur Generierung dezentraler I/O-Daten konkurrenzlos kostengünstig, zugleich hocheffizient und sehr flexibel. Das System lässt sich in alle gängigen Steuerungslösungen mit standardisierter Datenübertragung integrieren.
„Unser Management war von der einfachen Handhabung sehr beeindruckt“, erzählt Waters. „Zusätzliches Equipment einzubauen war früher oft umständlich. Jetzt lassen sich zusätzliche Geräte einfach anschließen. Bei Bedarf können wir das Netzwerk problemlos erweitern und andere Bereiche leicht integrieren.“ Um noch mehr Prozessinformationen zu gewinnen, wäre eine Integration von beispielsweise induktiven, optoelektronischen oder weiteren Ultraschallsensoren denkbar — und das bei minimalem Installationsaufwand.
Daten statt Vermutungen
Bisher ist das AS-Interface-Netzwerk der Qualitätssicherung noch nicht mit übergeordneten Steuerungssystemen verbunden — was allerdings problemlos möglich ist und Toyota wäre nicht Toyota, wenn es nicht bereits Überlegungen zur weiteren Optimierung gäbe. Bis dahin werden die von den Sensoren generierten und im Netzwerkspeicher gesammelten Daten periodisch in Paketen abgespeichert und stehen offline für Analysezwecke zur Verfügung.
„Wenn es in den Abläufen irgendwo zu Verzögerungen kommt, können wir das Problem dank dieser Information eindeutig zuordnen“, betont der Gruppenleiter. „Tritt es in beiden Schichten auf, ist es dauerhaft oder sporadisch? Hat es mit einer bestimmten Station zu tun oder vielmehr mit einem bestimmten Automodell? Statt auf Vermutungen können wir uns jetzt auf konkrete Daten stützen. Wir erkennen die Zusammenhänge und können gezielt reagieren. Früher mussten wir einfach mit gewissen Schwankungen leben, heute können wir uns über sehr konstante und störungsfreie Abläufe freuen. Das wiederum hat uns erlaubt, die Gesamtleistung und den Durchsatz messbar zu verbessern.“

Pepperl+Fuchs hatte Toyota vor einigen Jahren bereits bei einer ähnlichen Überwachungsaufgabe die passende Lösung mit Ultraschallsensoren geliefert, damals noch ohne Netzwerk. „Es lag nahe, wieder die Experten von Pepperl+Fuchs hinzuzuziehen“, sagt Waters. „Die positiven Erfahrungen aus der früheren Zusammenarbeit haben sich wieder bestätigt. Wir haben umfassende und kompetente Unterstützung beim Aufbau des AS-Interface-Netzwerks erhalten; das ganze Projekt verlief nach Wunsch.“
Inzwischen stellte das Qualitätssicherungsteam um Waters das Projekt in konzerninternen Foren vor und es könnte auch bald in anderen Toyota-Niederlassungen zum Einsatz kommen — ganz nach dem japanischen Prinzip des Kaizen, dem Toyota weltweit als Unternehmensphilosophie folgt.