Oct 11, 2017
Looking at the Bigger Picture Together
Extraordinary challenges are best solved as a team. Pepperl+Fuchs has been working with four companies from the IT industry, system automation, and process automation to develop a comprehensive solution that brings the Internet of Things and the benefits of digital Industry 4.0 technologies to the process industry.
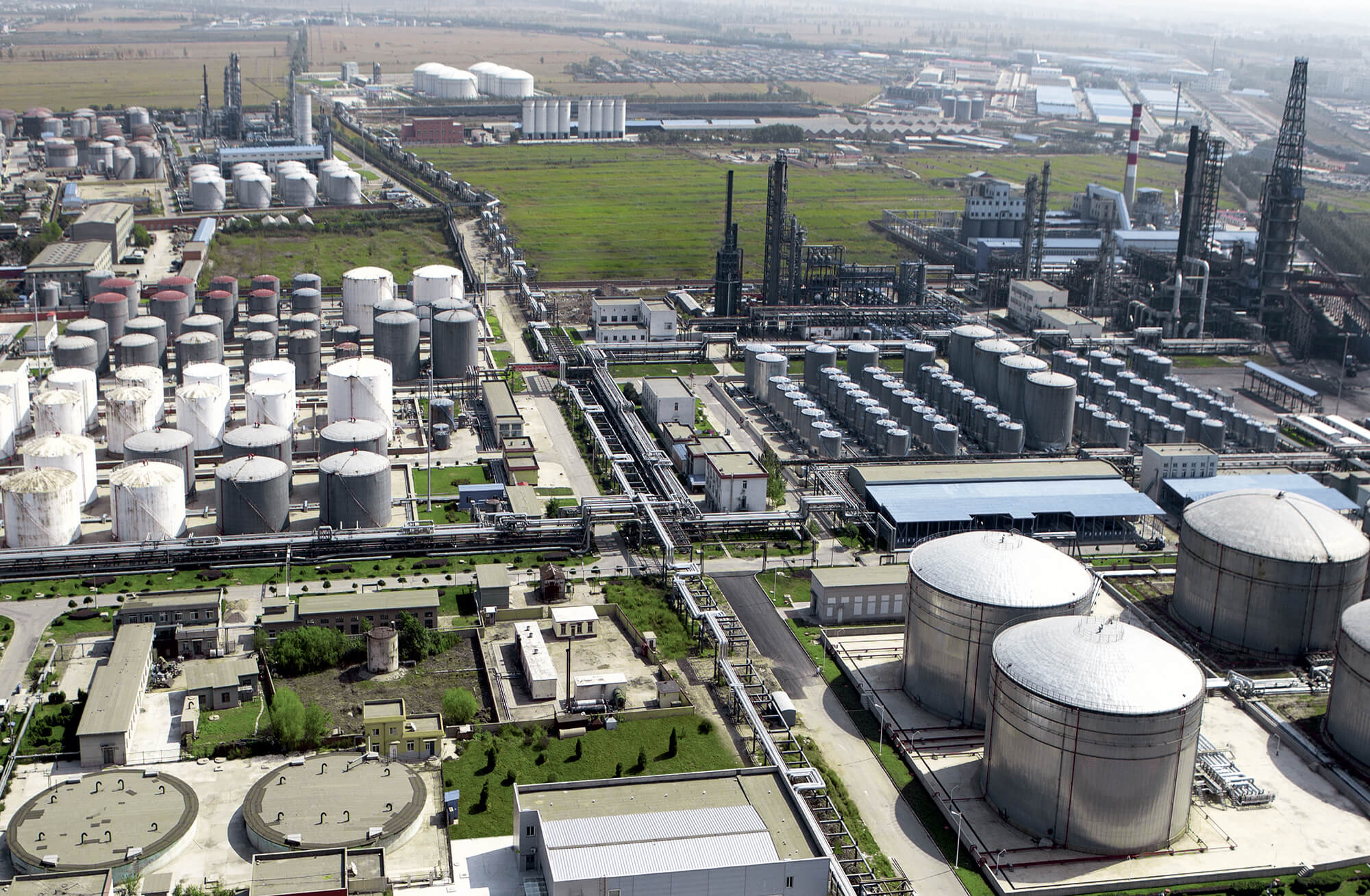
Temperatures, fill levels, flow rates—this is typical information that field devices in process plants generate every second. These devices also produce endless additional data about their environment and condition, but such data has previously gone virtually unused. That’s because, until now, most commonly used interface technology has not allowed such information to be transferred to the control room. How helpful would it be if all of this data were available centrally, and if it were used to automatically monitor field devices and plan condition-based predictive maintenance? In collaboration with four other companies, Pepperl+Fuchs is making this scenario a reality. Together with SAP, Hilscher, Endress+Hauser, and SAMSON, the company is paving the way for the Internet of Things (IoT) in the process industry. The aim is to improve the availability of plants with predictive maintenance and condition monitoring.
Greater Plant Availability with the Internet of Things
“In the process industry in particular, plant monitoring is associated with demanding requirements since this industry is already complex to begin with,” explains Benedikt Rauscher, Head of Global IoT Projects at Pepperl+Fuchs. “Take for example explosion-hazardous areas or non-interruptible production processes. Unplanned outages can be fatal.” The five companies are working together to counteract this with their joint development efforts: the interaction between the components and systems means that defects and impending failures can be detected before they arise, and the need for preventive action can be automatically signaled. The basis of the solution is comprehensive networking both within the plant and beyond.
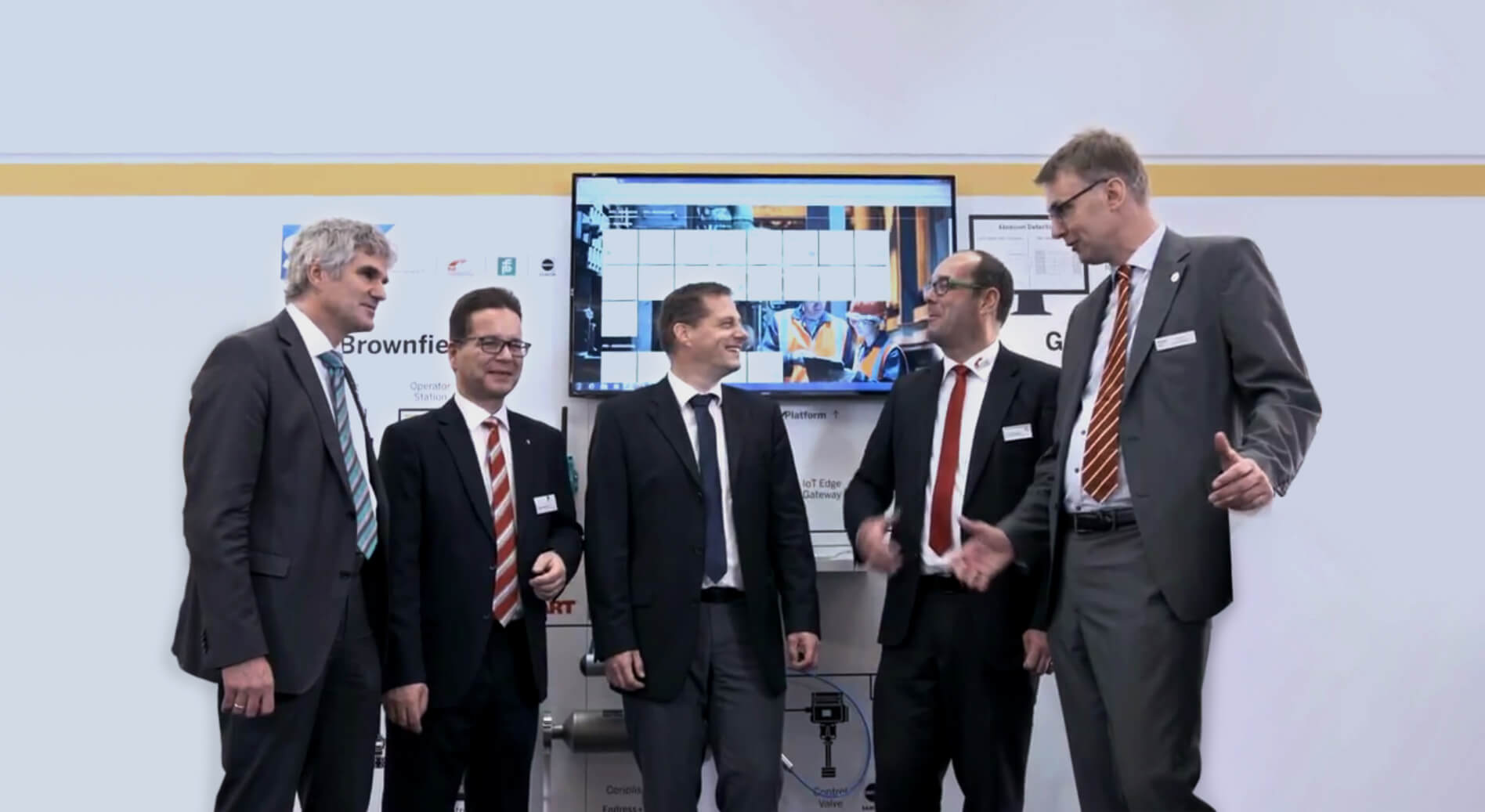

Left to right: Benedikt Rauscher, Head of Global IoT Projects, Pepperl+Fuchs // Guido König, Senior Technology Manager Business Innovation, SAMSON //Michael Bückel, Product Manager Platforms, Endress+Hauser //Armin Pühringer, Business Development Manager, Hilscher // Timothy Kaufmann, Business Development Manager Internet of Things, SAP
Full Cloud Cover
The hub of the solution is SAP Asset Intelligence Network (AIN) in the SAP cloud platform. All the relevant data and information is stored here for each component. This produces a digital image of the whole plant, and the image is available at a central point with all the key information. AIN regularly compares the saved structures with the actual condition so that errors and deviations are identified immediately.
Such condition monitoring and predictive maintenance requires the additional operating data from field devices. Flow measurement devices from Endress+Hauser and control valves from SAMSON, for example, continuously supply valuable additional information. This information allows conclusions to be drawn regarding coating formation, corrosion, or mechanical wear. But conventional 4 ... 20 mA interface technology only permits a single value to be transferred to or from a field device. An additional communication path that enables further information to be transferred is therefore needed.
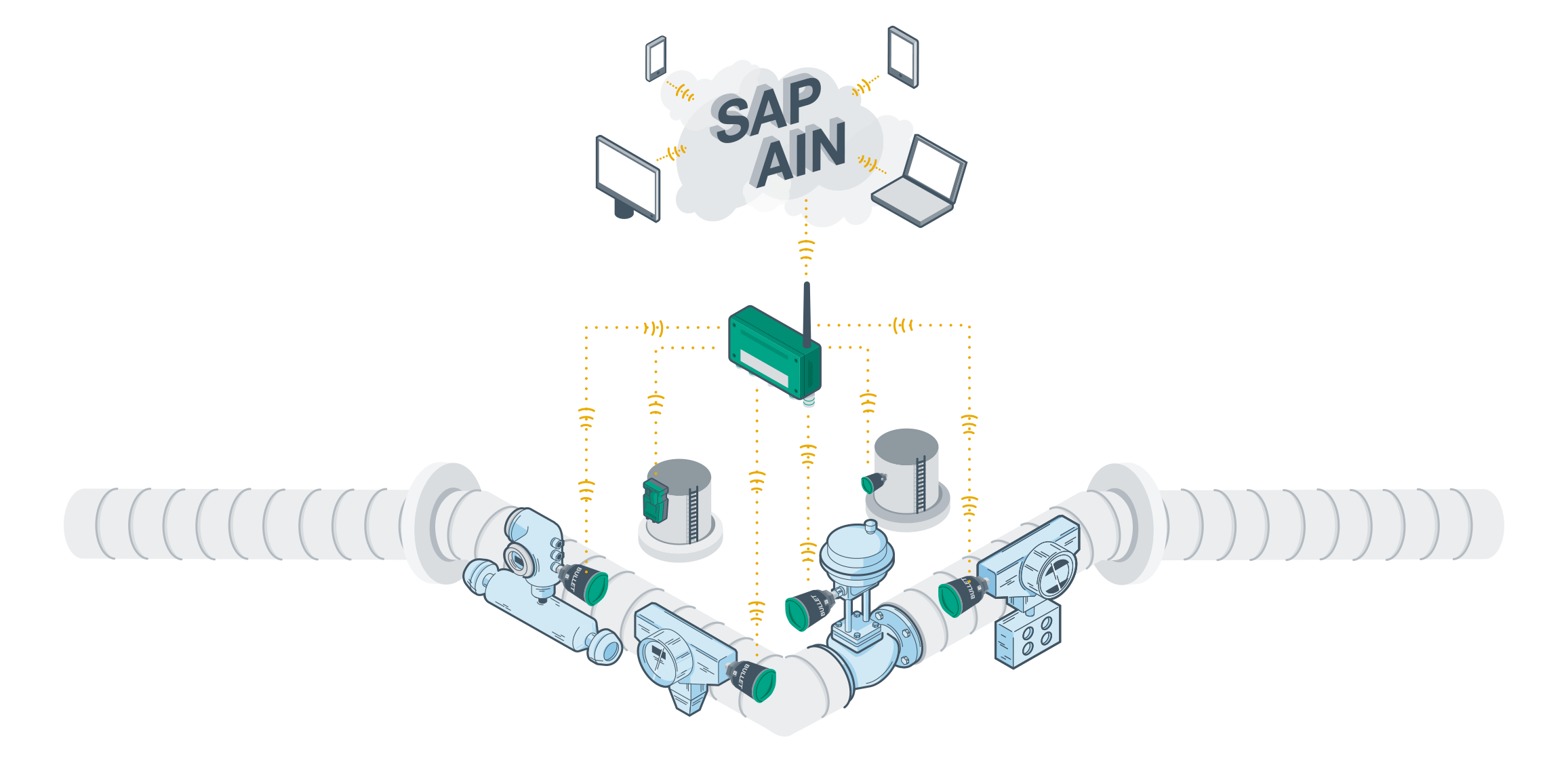
More Data and More Paths Mean Added Value
To make this possible, Pepperl+Fuchs equips field devices with the BULLET WirelessHART adapter, enabling wireless communication parallel to the 4 ... 20 mA current loop. The benefit for the process industry is that the BULLET in a robust Ex d enclosure is also suitable for explosion-hazardous areas. So it enables continuous communication through to the hazardous area. The adapter transfers the recorded data wirelessly to a WirelessHART gateway which in turn communicates directly with the SAP cloud via an MQTT protocol. The valuable additional data is therefore also transferred reliably to AIN and is available there centrally. Alternatively, the data can be transferred to the cloud using a wired connection via the netIoT Edge Gateway from Hilscher. AIN processes all the information clearly and signals a possible need for action to the user. Based on this, further applications can be added that process the data for other purposes, as required.
Limitless Networking
In addition to continuous communication from the field level through to the cloud, the developed solution offers the particular benefit of networking beyond the physical boundaries of the company. This is because not only the plant operator but also manufacturers and service providers can access certain areas of AIN. This enables new service models that could be used to better plan maintenance and inspection schedules or optimize delivery dates. At the same time, manufacturers can supply all the relevant information for the operator about the individual components within the network.
Minimum Work, Maximum Benefit
The joint solution fits seamlessly into the processes, with minimal installation work required. Existing plants can easily be retrofitted with the BULLET WirelessHART adapter without having to completely shut down the system. The particular benefit for customers in the process industry is clear: “The use of innovative Industrial IoT technologies such as this enables predictive maintenance and condition monitoring so that impending failures can be identified in time and appropriate preventive action can be taken,” sums up Rauscher. “This not only improves plant availability but also ultimately saves costs.” The comprehensive solution from SAP, Endress+Hauser, SAMSON, Hilscher, and Pepperl+Fuchs thus makes data continuously available and helps improve efficiency in process plants.
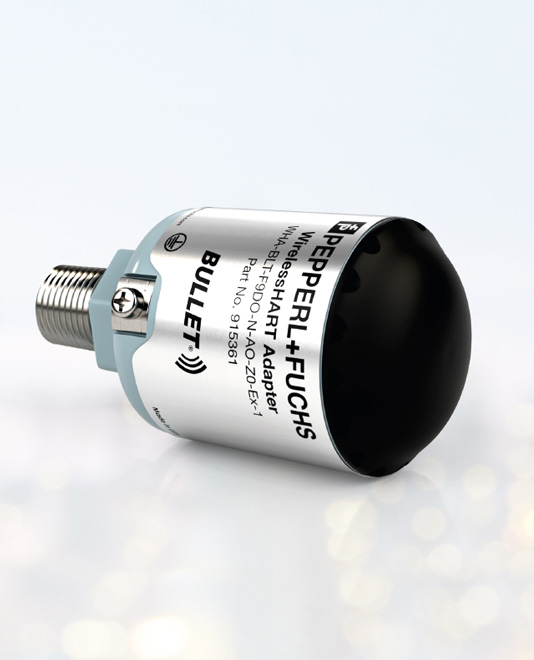
Find out more about the BULLET WirelessHART adapter.