December 5, 2018
The Connections That Bind Us
Pepperl+Fuchs produces thousands of kilometers of cable every year, cables that stand up to almost every challenge. Learn more about our 20 years of connectivity experience and the versatile applications for sensor cables from Pepperl+Fuchs.
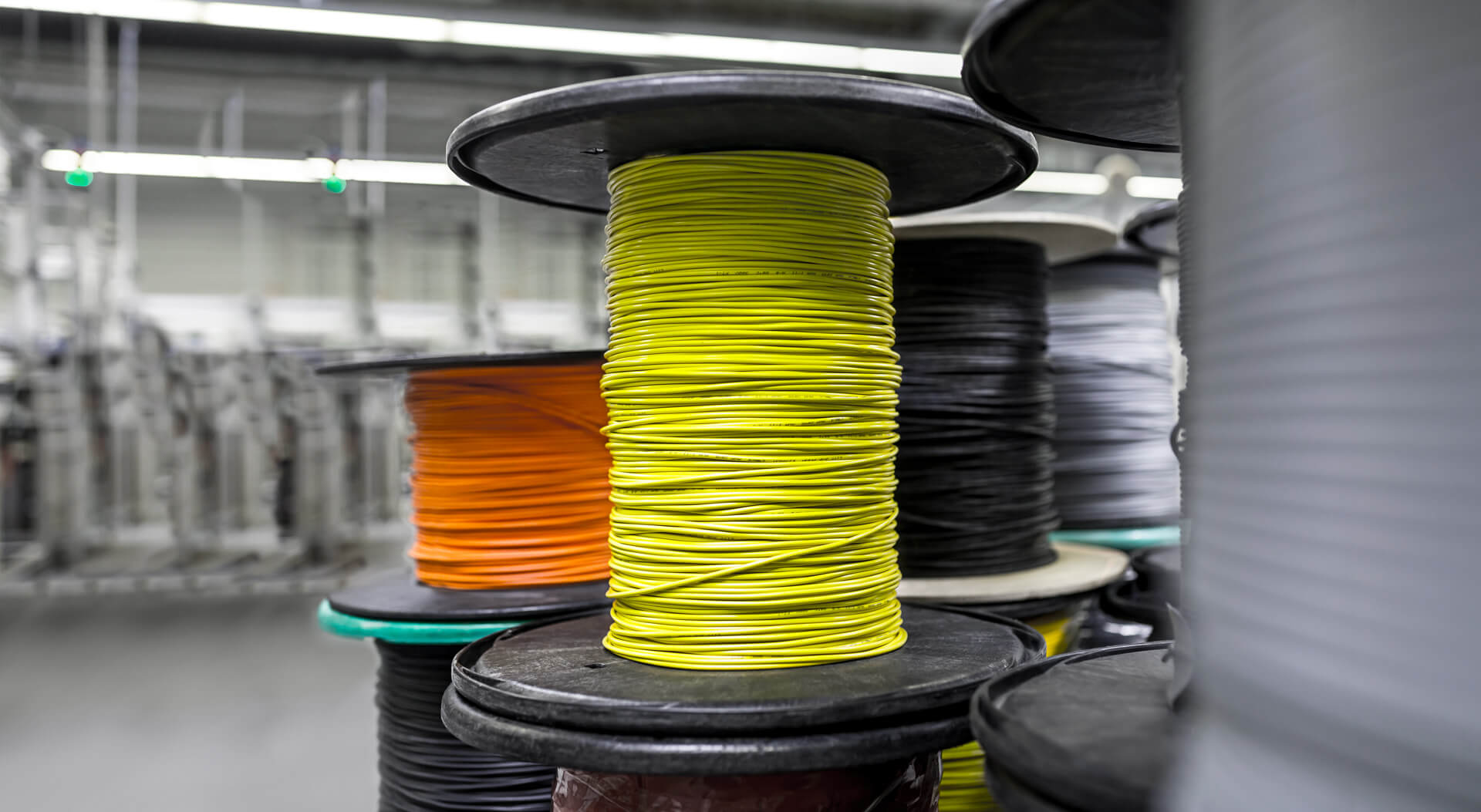
Connectivity Ensures Reliability
Over 150 years ago, communications pioneers undertook a daring and costly endeavor to establish a telegraph line between North America and Europe. In the process, a staggering amount of cable was laid over thousands of kilometers across the bottom of the ocean. Despite numerous challenges they succeeded in making the connection, but after just a few weeks, it was broken—partially due to the limitations of the cables. Like those pioneers, Pepperl+Fuchs produces thousands of kilometers of cable every year, but these cables stand up to almost every challenge.
Whether for machine building, welding, material handling, mobile equipment, or the process industry—'powerful sensor technology requires powerful and, above all, reliable connectivity,' explains Jürgen Chrobak, managing director of Pepperl+Fuchs Hungary. What sounds like a simple sensor accessory is, in fact, an important part of automation technology. Just one failed connection can lead to a failure across the entire plant and cause expensive downtime. 'Saving on connectivity generally results in increased maintenance costs,' says Roland Gubbels, business manager for connectivity at Pepperl+Fuchs. To protect users against these risks, more than 200 Pepperl+Fuchs employees in Veszprém, Hungary, have been developing, testing, and producing high-quality cable assemblies for automation for 20 years. What needs to be taken into account when developing connection technology? 'As in many other areas, there are certain challenges here, too. On the one hand, cables and connectors are highly standardized, which means that they are compatible with sensors regardless of the manufacturer. At the same time, Pepperl+Fuchs would like to offer more than just the standard,' says Gubbels. To achieve this, Pepperl+Fuchs places importance on extra features, such as vibration protection, knurled nuts for secure installation, an innovative catch design for snapping in protective loom, and 360-degree shielding. 'We know exactly which cable the customer needs for which application. Our many years of experience allow us to offer targeted, sector-specific solutions,' says Chrobak.
A Clean Design
In the food industry, hygiene safety is top priority. Products and packaging cannot be contaminated by contact with machine parts under any circumstances. Connector design plays a crucial role: surfaces have to be smooth and easy to clean in accordance with EHEDG (European Hygienic Engineering and Design Group) guidelines. Fittings are made of stainless steel to ensure that no food sticks to the surface. High-quality connectivity must also be able to withstand aggressive cleaning agents and procedures. 'That's why the four-pin and five-pin varieties of Pepperl+Fuchs´ M8 and M12 connectors are adapted to the strict requirements of spray and contact zones. They are also PVC- and halogen-free, FDA-compliant, and certified by ECOLAB. This combination ensures cleanliness and that hygiene safety can be fully maintained during machine and component cleaning,' says Gubbels.
Make or Break
Unlike food production, some industries involve work that is too dangerous or harmful for humans. For these jobs, robots are used to perform millions of repetitive processes. In certain areas, robot movement involves extreme bending and rotating. To prevent production downtime, the connections in use must ensure constant power and data transfer between the robot and the automation system. 'Pepperl+Fuchs PUR-R cables can be twisted ± 360° per meter over ten million times. That is why it is important that each individual component in these highly automated production processes works reliably, withstands high temperatures, and demonstrates resistance to oil and chemicals. PUR-R cables meet all of these requirements since they are highly flexible, suitable for drag chains, and can be twisted up to ten million times,' explains Gubbels.
All Fired Up
If, on the other hand, cables are used in an environment with smoke and flying sparks, they must work reliably despite tremendous direct or indirect heat. Fortunately, Pepperl+Fuchs has a long history as an automotive supplier and is more than familiar with the stringent requirements of the welding sector. PUR-A cables are designed for use in areas where cables come into contact with weld spatter and need a high degree of flexibility. However, special cables are necessary in extremely hot environments, like body shops, where cables can come into contact with streams of sparks. 'If you have an application where cables are in the immediate vicinity of welding, POC-coated cables are the right choice. With high mechanical strength, resistance to continuous service temperatures of up to 150 °C, and weld spatter resistance, these cables can be used in areas where other cable types cannot withstand the heat and exposure,' says Gubbels of the highly resistant special cables.
On the Move
Cables are not only exposed to extreme conditions in automotive plants, but also in mobile equipment applications. 'With the introduction of the specialized MEC (mobile equipment connectivity) portfolio, we are bridging the gap between the world of round plug connectors and the ‘automotive world.’ We are providing a rugged connector for mobile equipment with our proven sealing design.' says Gubbels. It is based on tried-and-tested mobile connectors from Deutsch, AMP, and TE Connectivity that have been optimized by Pepperl+Fuchs for mobile applications. 'The overmolded bodies of the mobile equipment connectors are resistant to harsh environments, provide long-lasting protection, and are fully operational from -50 to 105 °C. In addition, their slim design minimizes the space required during operation, and an innovative catch design allows protective cable loom to be attached quickly, reliably, and without an additional adapter,' adds Gubbels.
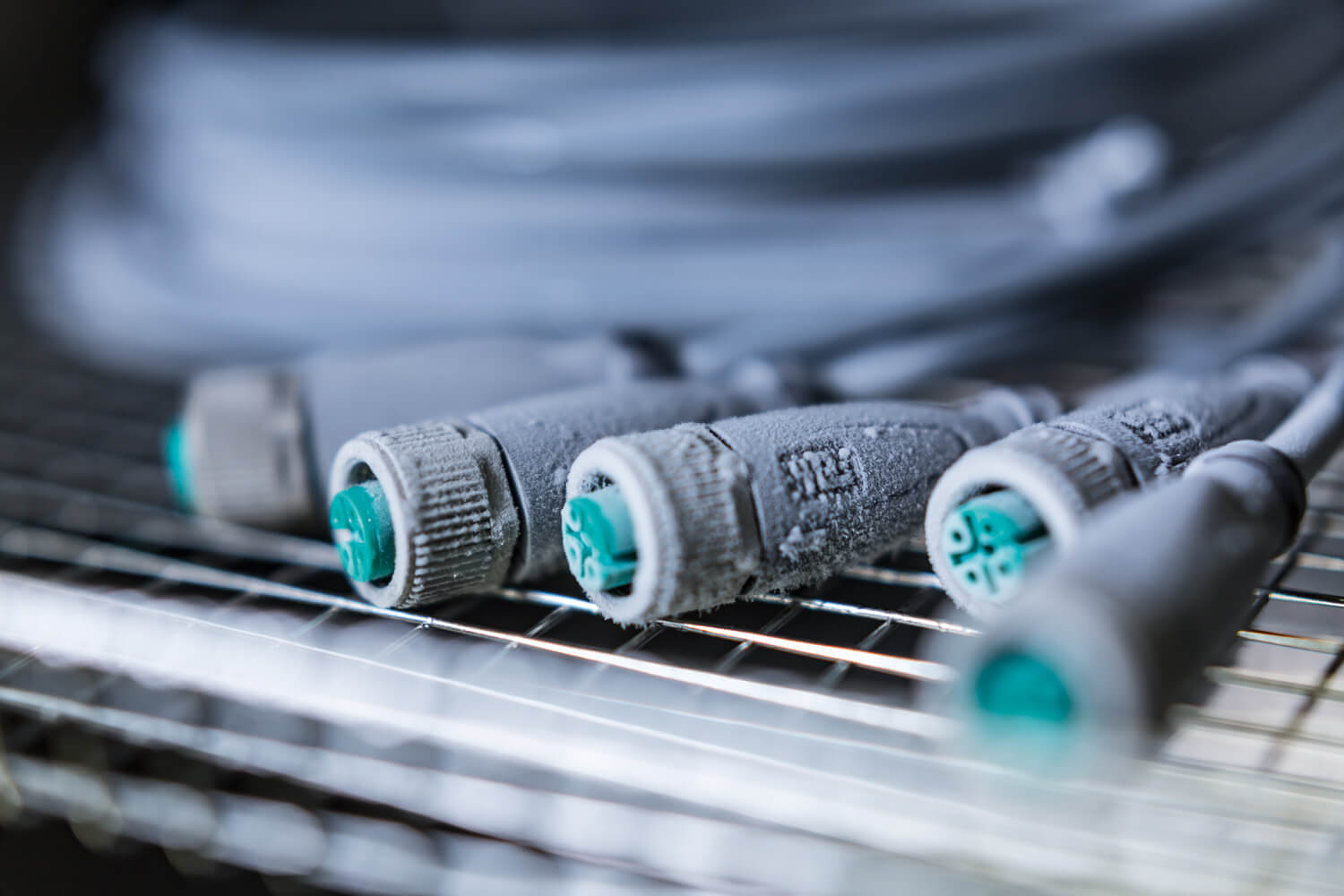
In order to guarantee absolute reliability in plug connections, the components are subjected to extreme testing. For example, the plug connections are shock-frozen in a cold chamber.
More Than Just Cables and Connectors
The variety of application-specific cables is also reflected in the sales figures. As Gubbels explains: 'In the last few years, we have grown steadily and have continuously expanded our market share. Today, we process more than 15,000 km of raw cable and produce over five million connector bodies per year.' The key to this success, aside from 20 years of experience in connectivity, is a well-stocked raw materials warehouse and advanced logistics processes in Veszprém. Before products are shipped, they undergo extensive electrical testing to keep the fault rate at zero. 'Nothing is more annoying than a faulty cable installed in a hard-to-reach place,' says Gubbels. Another factor that gives Pepperl+Fuchs a competitive edge in the market is its cohesive, single-source portfolio of connection and sensor technology. This combination ensures that users can always expect the greatest possible interoperability. 'Customers also receive the advice they need on demand when we're looking at an individual cable solution,' says Chrobak. What's more, the research and development department, also based in Veszprém, is already working on the solutions of tomorrow: 'Where in the past you had the sensor-actuator cable and parallel wiring, these days IO-Link and industrial Ethernet solutions serve as replacements. We are now developing connectors that will let you transport a current of up to 16 A in the plant. At the same time, we are focusing on connectors that will connect Gigabit Ethernet and, in the future, single-pair Ethernet to the machines securely, reliably, and impermeably and will replace RJ45 in the long term. With our integrated portfolio, we'll ensure ‘plug by plug’ that the world of automation becomes increasingly more connected,' says Gubbels of future developments in the field of connectivity.