When Customers Become Partners
October 22, 2019
For a company to ensure its long-term survival in the market, it must understand its customers, their needs, and their wishes. The company must tailor its products and services to the specific requirements and preferences of each customer. Since no one knows what these are better than the customers themselves, why not involve customers directly in the development of their customized solutions? Pepperl+Fuchs has taken this exact approach in partnership with the company montratec.
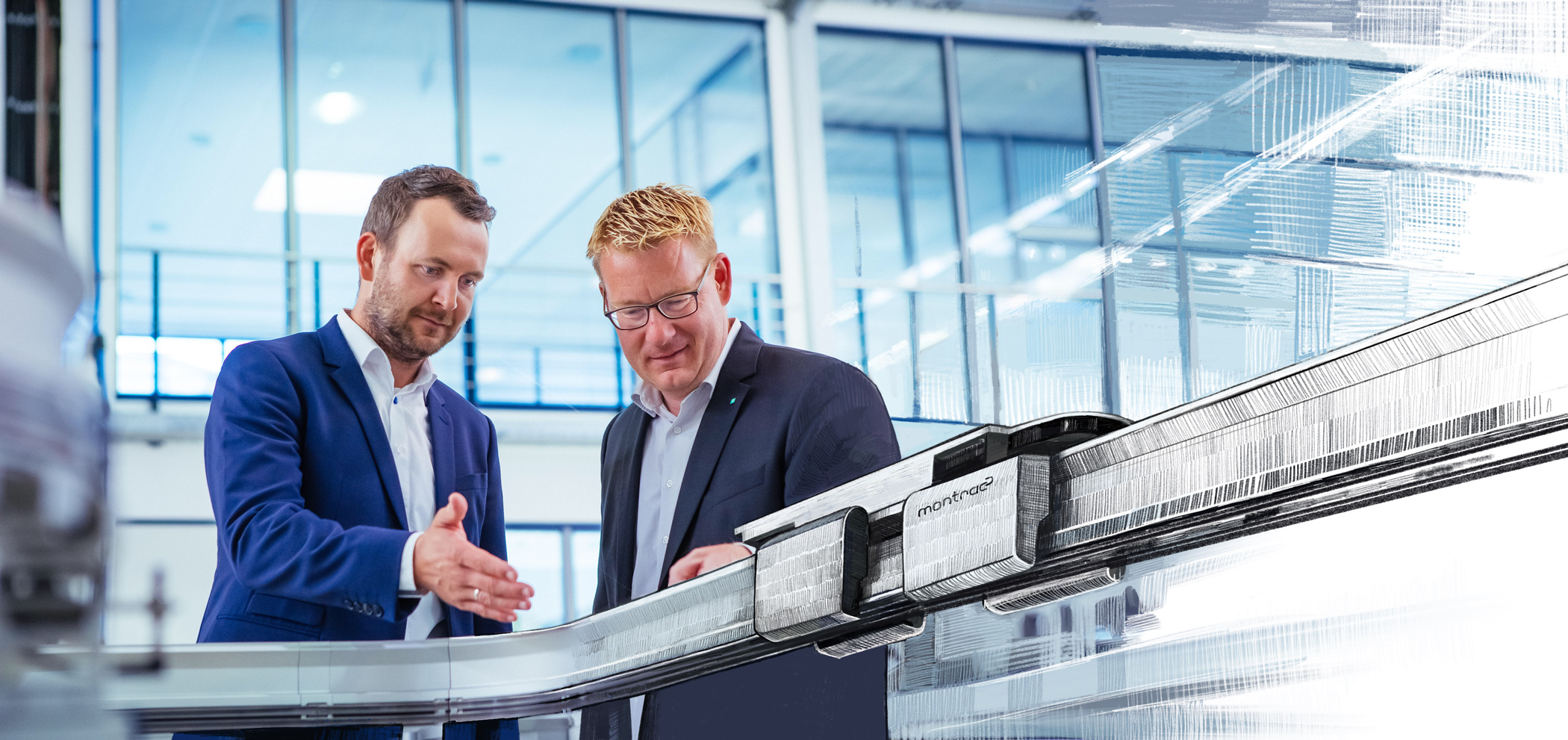
Digitalization is changing our everyday lives, both at home and in industrial environments. With this in mind, customizable products and systems are more important than ever for many companies. This trend of offering customer-specific solutions rather than a limited catalog of products is also noticeable at Pepperl+Fuchs. 'As market conditions change, so do our customers' requirements,' explains Andreas Dereux, Key Account Manager at Pepperl+Fuchs. 'Plant operators are less concerned with standard products and are instead asking for solutions that are tailored precisely to their needs. In collaboration with montratec, we have developed one such sensor solution from scratch.'
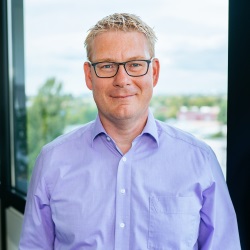
The Key Feature
Based in Niedereschach, Germany, montratec manufactures modular monorail systems for internal transport operations and assembly processes. The development of their new montrac® Shuttle MSH5 was highly ambitious. 'The MSH5 was not about simply enhancing the previous model, but instead about making a big technological step—if not a leap—forward,' emphasizes Michael Haug, Product Manager at montratec. The sensor technology integrated in the previous shuttle generation was based on a one-dimensional, photoelectric sensor with energetic signal evaluation. This sensor emitted a simple switching signal and detected shuttles ahead using a single beam of light. This meant that the sensor could not distinguish between fixed route components, such as tunnels, shuttles ahead, and even bends in the track. This will no longer be a problem with the new generation.
'There was a long list of requirements for the new sensor as the key feature of the shuttle, and I soon realized that we could not meet them with the products available on the market. We needed to find a partner with whom we could design a solution tailored to our application,' says Rolf Wiechert, Vice President of Engineering at montratec. 'It wasn't easy,' says Haug. 'Only Pepperl+Fuchs met all of the requirements for this collaboration with its experience, technological expertise, and its readiness to use the products in its portfolio to create something completely new.'
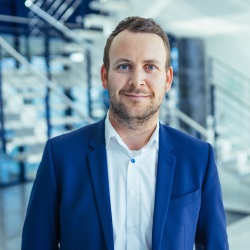
A Milestone in Intensive Collaboration
Mutual trust, understanding, and a clearly defined goal are key to successful collaboration—both at home and in the workplace. 'We are both specialists in our fields: montratec understands the ins and outs of industrial intralogistics, and Pepperl+Fuchs knows the benefits that high-performance sensor technology can bring to this field,' says Dereux. 'We have combined these two perspectives.' Before the actual development work began, various meetings were held at both montratec and Pepperl+Fuchs to establish a clear understanding of the application, the ambient conditions, and the shuttle and desired functionalities. Thorsten Schroeder, Product Manager at the Pepperl+Fuchs facility in Berlin, the competence center for photoelectric sensors, oversaw the project. 'The collaboration with montratec was very intensive throughout the various project phases,' says Schroeder, adding: 'As a Product Manager, I was particularly involved in the first phase—the development of a comprehensive specification.' The specification is the basic framework for all subsequent stages, which makes it a crucial phase in the overall project. The actual development work can only begin once all requirements are specified in enough detail.
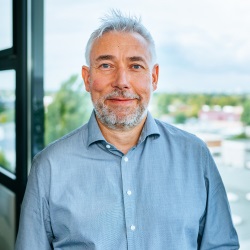
Based on Pulse Ranging Technology
'The crucial starting point for this development was the decision to use measurement technology, because in contrast to the sensor installed in the original shuttle, the new technology outputs distance values that can be used for further processing,' explains Wiechert. Pepperl+Fuchs uses innovative Pulse Ranging Technology, or PRT, to carry out a specially developed time-of-flight measurement that measures distances from a few inches to hundreds of yards with millimeter precision using a direct measuring method. PRT has already proven itself in many products in the Pepperl+Fuchs portfolio, as has the R2100 2-D LiDAR sensor, which was used as the basis for the new sensor solution for montratec. 'The biggest technical challenge was to tailor this core technology to the conditions in the shuttle,' explains Schroeder, who goes on to specify: 'The construction, hardware, and software all needed to be adapted.'
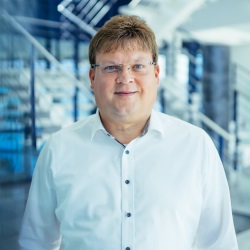
Tailor-Made in Many Ways
If you compare the sensor solution developed for montratec with the R2100 portfolio sensor, which was used as a starting point for the montratec solution, it is immediately clear that the two products now look very different. A completely new end product is now being produced on a production line set up especially for this project and processed using special calibration and testing devices.
The housing has been tailored to the shape of the shuttle so that it fits seamlessly into the shuttle design. This required a complete redesign of the measurement electronics. Individual sensors in a semi-circular arrangement now provide distance and intensity information from five different measuring points. 'Dealing with a multi-channel sensor solution affected how measurements were evaluated, meaning that the software also needed adjusting,' says Schroeder, outlining the additional customization processes required: 'For the first time, we have completely modified a two-dimensional solution to resolve a customer's problem.' His colleague Dereux, visibly proud, adds: 'And that's what makes this solution special! Working together with the customer, in this case montratec, to use existing, high-performance technology to create something completely new—a technically perfect and efficient solution for both sides.'
When the first prototype was ready to be implemented in the shuttle, both companies were equally delighted. 'After so many months of close and intensive collaboration, seeing the successful use of the sensor in the application for the first time was certainly an emotional moment,' a sentiment shared by everyone.
Real Added Value for Intralogistics
The advantages of the new five-channel sensor technology cannot be overstated. With five measurement beams, the new Shuttle MSH5 has an additional, peripheral field of view, which enables it to reliably detect shuttles ahead and obstructions at any time—on both straight and curved tracks. In addition to better route monitoring and optimized collision avoidance, the wider beam angle of the five emitter LEDs makes it possible to transport wider workpiece carriers. If an additional sensor is used at the rear of the shuttle, reverse travel with sensor monitoring is also an option. 'We now use a high-quality industrial sensor that is far superior to a switching solution due to its measurement technology,' says Haug, satisfied. 'With the new features, we create real added value for our customers in intralogistics.'
Watch videos
In partnership with the customer montratec, Pepperl+Fuchs developed an individual sensor solution. Learn more about the solution and the collaboration …
Find out how modifications to the design, hardware, and software have transformed a portfolio sensor into a solution that is tailored precisely to the shape of the shuttle …
Our Solutions,
as Individual as You
Subscribe now
Would you like to find out more about customized solutions from Pepperl+Fuchs? Register via the form below to receive regular updates.

Receive regular updates on customized solutions from Pepperl+Fuchs!
Subscribe now