April 15, 2021
Safely on Track
The innovative automated guided vehicle (AGV) from Staudinger GmbH Automatisierungstechnik performs well in a large automobile manufacturer’s axle assembly plant. For its latest AGV development, the Bavarian company relies on high-performance sensor technology from Pepperl+Fuchs.
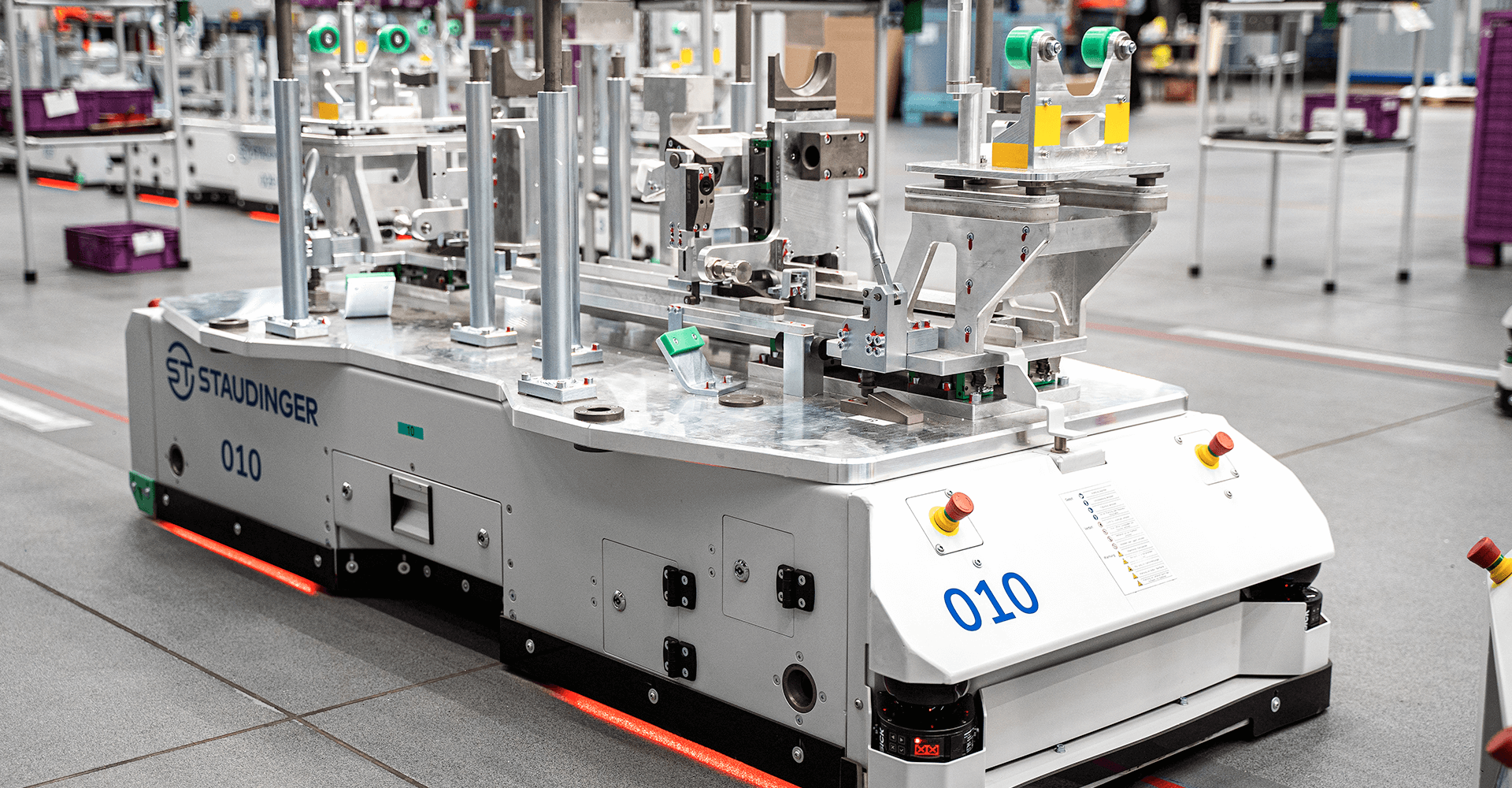
They are continuously in use, flexible, long established, and yet in the fast lane. The specialists for efficient, holistic intralogistics: Automated guided vehicles are indispensable in modern production and are used in numerous industries. The origin of these mobile all-arounders was in the automotive industry and it is undoubtedly a sector subject to some of the greatest transformation and automation. A large number of automated guided vehicles (AGV) perform different internal transport tasks and play a crucial role in optimizing speed, safety, and cost efficiency during ongoing operation. The AGV is being greatly hyped, especially in the context of Industry 4.0, and automotive manufacturers are not the only ones applying it in order to achieve lean, agile production plants. 'To achieve top performance in this demanding and forward-looking industry, we need future-oriented solutions and continuous development,' says Lothar Vohberger, Project Manager at Staudinger.
The Aim: An Innovative Masterpiece
Staudinger is a certified service provider of automation technology, whose product range includes a wide variety of systems, control technology, and automation solutions for various application areas. However, developing an AGV was something new for the specialist company based in Loiching, Germany. 'This project is completely new territory for us,' says Vohberger, who is currently on site at a production plant belonging to a major automobile manufacturer. The experienced project manager is surrounded by many specially developed AGVs, which are already reliably used in front axle and rear axle assembly.
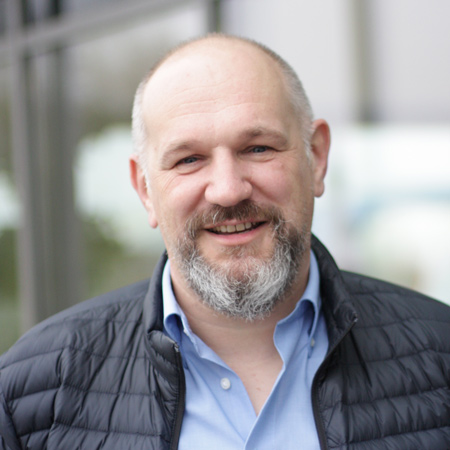
"We already have a number of years of experience in the automotive industry and the associated plant technology to draw on," explains Vohberger, adding, "The design of an AGV, on the other hand, was a completely new and exciting challenge." There was no equivalent standard solution from other manufacturers for the specific use required by the end customer. An AGV solution tailored to the requirements was developed in close cooperation between Staudinger and its customer.
Before beginning the development phase, various questions needed to be answered: Which specific tasks does the AGV have to complete? Are there any particular requirements for integrity and adaptability? What type of environment will the system be used in and what will be transported? "The integrated sensor technology plays a key role in all of these aspects," says Vohberger. "We had high expectations for the new developments. We did not want to rely on outdated technology. On the contrary, our main target was to develop an innovative AGV that was technically superior to our competitors," he explains, looking enthusiastically at the numerous mobile helpers autonomously making their way along the automobile manufacturer's production line. "In the field of sensor technology, we rely on the specialists at Pepperl+Fuchs."
Putting Practical Experience into Practice
Staudinger's AGV goes through about 100 work cycles until the front and rear axle have been fully assembled. It reliably transports the workpieces from one workstation to the next. For smooth navigation, the AGV is equipped with sensors from Pepperl+Fuchs. The focus is on the positioning system Position Guided Vision, or PGV for short. 'As the world's first DataMatrix positioning system, it combines color band tracking and exact positioning via DataMatrix codes in a single device, enabling impressive precision and efficient manufacturing processes,' says Thomas Menzer, Key Account Manager at Pepperl+Fuchs. The PGV read head, consisting of a 2-D camera system with an integrated lighting unit, reliably tracks the colored code bands on the floor of the automobile manufacturer's production hall. Even tight curves, reflective surfaces, and damaged or dirty code bands or tracking codes do not affect the sensor.
In addition, users can react quickly and flexibly to changing conditions. 'The PGV system has been developed by our application experts and puts experience into practice,' says Menzer. 'We are therefore very familiar with the special requirements in intralogistics and know about the required adaptability, which Staudinger has also demanded.' If required, the PGV can help amend routes or expand quickly and cost-efficiently using a wide range of color and code tapes.
Absolute Safety in Track Guidance
'While large parts of the assembly line are classified as 'non-safe' areas, in others the highest safety guidelines according to safety level SIL 3/PL e must be observed,' explains Vohberger, when describing the ambient conditions in his customer's production hall. 'We were thus faced with the challenge of ensuring that the AGV is correctly guided even in safety-critical zones to optimally protect people and machines.' Menzer adds: 'And we had the ideal sensor solution for this safety application at hand with our safePGV positioning system.'
Based on a multi-redundant technology, the sensor enables safe absolute positioning in accordance with SIL 3/PL e and supplies all values for reliable control of the AGV. 'The Y position and angle are output, allowing constant correction of track deviations. The exact positioning on the X axis means that the AGV adheres to the safety distance, thus guaranteeing the protection of all persons working on the line at all times,' the Key Account Manager says, explaining the function principle. A two-color DataMatrix code tape is installed on the floor of the hall to ensure safe track guidance. The 2-D read head of the safePGV is able to read out the different color codes. A safety algorithm in the firmware checks the plausibility of the information obtained in the sensor before the data is passed on to the safety PLC as safe data in accordance with SIL 3/PL e.

"This solution allows a high level of safety to be achieved with a single sensor, a global first," concludes Menzer, adding: "Of course, this has enormous advantages for Staudinger. Where previously different redundant systems had to be used, this is now possible with only one device. This not only saves effort and costs, but is also very efficient." In addition to the safePGV positioning system, Staudinger's AGVs are additionally equipped with a safe inductive sensor. This is used to detect floor markings in safety-relevant areas.
Symbiosis between Two Experts
'With the newly developed AGV, we are now able to supply our customers with a complete solution comprising the control and drive technology plus the vehicle itself from a single source, without any additional purchases,' says Vohberger, visibly satisfied and adding: 'Throughout the entire project, the collaboration with Pepperl+Fuchs was professional and both parties saw eye to eye.'
'I can only reiterate that,' Menzer agrees. 'Staudinger has a lot of experience in the field of automation technology, especially in the automotive environment. We have made the best use of our many years of expertise in the field of high-performance sensor technology. I would therefore describe it as a successful symbiosis between two experts.' 'The ideal prerequisite for further joint projects,' concludes Vohberger.
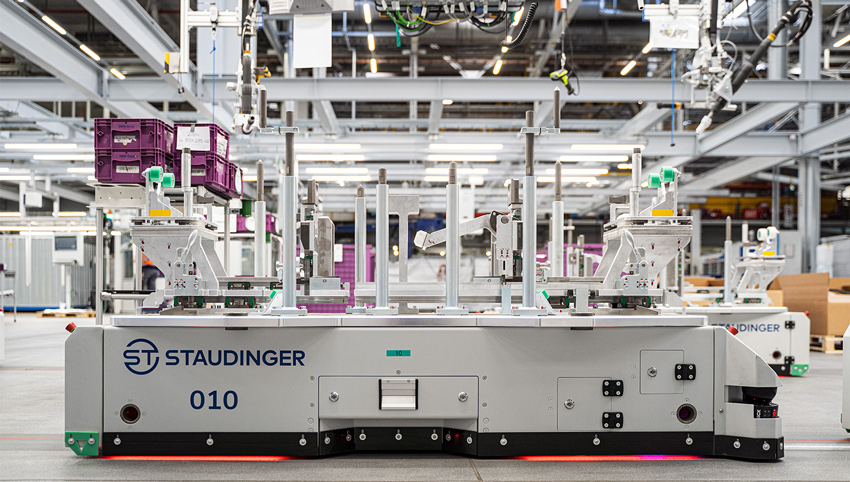