May 3, 2021
The Original: The Evolution of an Everlasting Technology
The proximity sensor was Pepperl+Fuchs’ very first product whose invention underpinned the company’s success and harks back to the beginnings of both pioneers and company founders. A new chapter is now being written in its success story: With the innovative, modern range of inductive cylindrical standard sensors, Pepperl+Fuchs is elevating “the original” to a new level of quality.
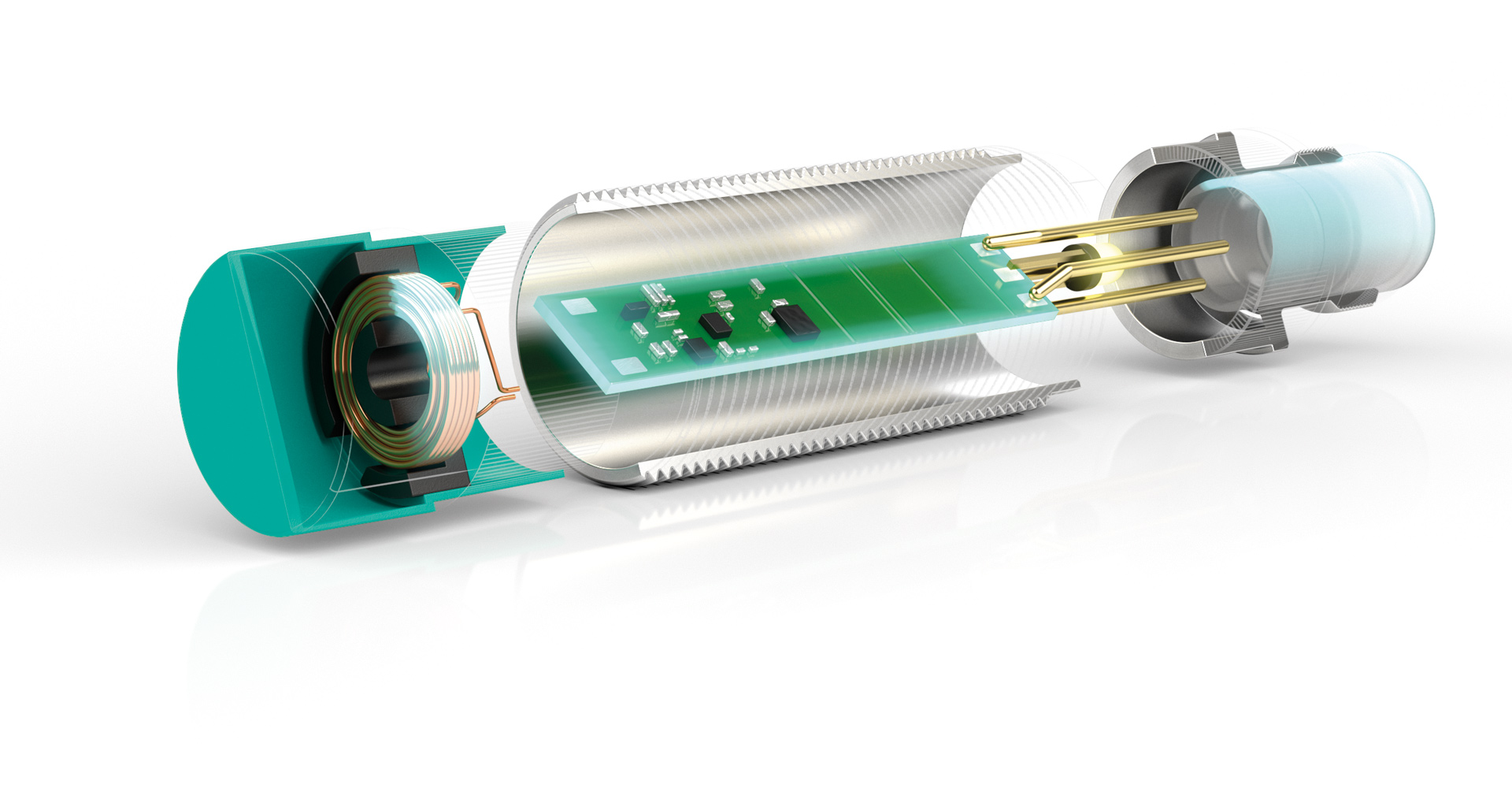
It is hard to believe that the inductive sensor—which is now 63 years old—is still as much in demand as it was at its peak. It is quite literally a true evergreen owing to the green end cap on the latest Pepperl+Fuchs generation. This range of sensors has since grown to be one of the most extensive. That reflects not only the huge importance Pepperl+Fuchs places on the proximity sensor. It also proves that the founding innovative drive still characterizes the corporate culture. Even today, Pepperl+Fuchs proximity sensors are regarded as technologically state-of-the-art and are a permanent feature in countless industries and markets the world over.
The question of how this technology has been developed over the decades and how it has mastered every stage of the automation evolution is even more exciting. Or what its role will be in the age of Industry 4.0 and digital transformation, which are conquering the automation industry.
We discussed this with two 'movers and shakers' who were heavily involved in developing the new inductive standard sensors. Two developers from two generations offer exciting insights into their work and perspectives: Johann Elter, Dipl. Ing. (FH), R&D Team Leader for Customer Applications & Lifecycle in the Electromagnetic Sensors Innovation Unit and product developer at Pepperl+Fuchs in Mannheim since 1986, and his colleague Patrick Drebes, M. Eng., R&D Engineer for Mechanical Design in this team and a Pepperl+Fuchs employee since 2013.
Johann ElterWe boast a long history in this technology, a history that means a variety of products in different technical versions—some outdated, some up to date. These were difficult to maintain due to the inconsistency. If you have sensors with item numbers in the lower 10,000, which means products that have been in our portfolio for a long time, components for this may no longer be available, or the technology may have undergone significant changes. It was crucial for us to consolidate all the various versions. Where does it make sense to consolidate? And above all: How can we enhance the customer benefit? Essentially, we summarized and reviewed all experience from the last 30 years. We looked at which technologies had come to a natural end and which technologies promise success. We combined these, while further developing the technology. Based on customer requirements and requests made in recent decades, we concluded that an extended temperature range may often be required or there were occasional requirements for high switching frequencies. Above all, we wanted to serve customers that use our sensors to pursue unusual solutions. One example is the sensors being operated directly at 5 V. Not every customer works in the industrial sector. These users usually build their own control system; our sensors can now be operated on those from 5 V upward. This is a true novelty compared to predecessor products.
Johann ElterOne customer is a company that we supply with sensors for its 3D printers. We supply this customer with between 150,000 and 200,000 sensors per year. All in all, an exceptionally good customer for us. The customer needs the sensors to be operated at 5 V, which is a common requirement. We responded by developing this new line and integrating operation from 5 V supply voltage on. The high switching frequency is important in the new range. We wanted to appeal to these customers, since not everything runs in slow cycles with an object passing by only every few seconds. Our new product family therefore now has consistently high switching frequencies. These play a role when highly dynamic objects need to be captured. Rollercoasters are a very familiar example of this from the Pepperl+Fuchs world. Our square-shaped products are predominantly used in this application, with cylindrical sensors making a rare appearance. Timing and, of course, reliability are all important. An important sector in which the high switching frequency plays a role is material handling, owing to some items being extremely quick and dynamic. High switching frequency in the sensor benefits speed detection. Another important feature is the temperature range: Some of our customers use the sensors on forklifts that travel in and out of a cold store. Inside the temperature is -25 °C, outside it is bright sunshine. Corrosion resistance is borne out from this, since outdoor applications mean heavy-duty use of the sensors, which weather very easily. A rugged coating is a major benefit for customers.
Patrick DrebesThis is exactly why we have chosen a housing coating of white bronze. This has a higher corrosion resistance for these sorts of applications. We have not forgotten about attacks caused by chemicals like cleaning agents—we still utilize our well-known plastic materials in the proven Pepperl+Fuchs quality.
Johann ElterThere was one factor that proved to be of almost overriding importance. We found that our previous projects were sometimes extremely difficult to adapt to customer requirements. Which is why our goal was to achieve flexibility for the benefit of the customer, by being able to produce versions very quickly. Customized versions make up a large proportion of our range, and that is not always just another cable. Sometimes it is cable connector versions, housing lengths, etc. Aspects that we could not cover so easily in previous products. The automated configuration with an enormous number of possible versions solves this issue. In the past, each variant was modified individually, the corresponding structures were created, and it was essential that each component had the corresponding objective evidence document etc. These tasks required an enormous amount of effort and, unfortunately, there was no standardized technical state. If a field service employee wanted a product version according to the older technical state, this brought with it limited technical features that did not correspond to the latest state-of-the-art. We have now designed a completely new range that is compliant with the latest versions of the standards and corresponds to the current state-of-the-art. In addition, we have significantly improved sensor performance. The electronic features already mentioned run alongside purely mechanical factors, in which we have set ourselves higher quality targets to go beyond the standard, as with our coating and housings.
.
Patrick DrebesWe have tried to follow the most uniform path in terms of the mechanics. We used to have different concepts, different structures, and different casting resins, which had different properties and therefore had different levels of performance. Now we have a standardized design with a new coating, which offers us significant advantages both in terms of sensor features and corrosion protection. Changing from the old nickel coating to a white bronze coating to create a high degree of corrosion protection is certainly the main benefit for customers. What's more, we picked the best aspects from existing designs to further optimize them. We now have a concept that can be used up to an impermeability rating of IP68. This was already present in individual products, but not to a large extent. Now even our standard sensors meet the IP68 rating. Sensors with IP69 to meet more stringent requirements are also featured. And this has led to a higher technical state across the entire range. Our new Pepperl+Fuchs green end cap for cable sensors is visible externally and directly to customers. The cap boasts a modern, fresh design, and a clearly separated, transparent LED window. This enables you to see instantly which spot will be lit as soon as the switch state is displayed. Size and brightness have undergone significant improvements to create a huge benefit for customers: The LED is very visible, and from all sides. We worked together with an industrial designer to develop the end cap—a process that I found fascinating! He developed different design languages for us, which we evaluated together and determined a standardized line to pursue in the future for this component. That was the only design element we had at this point, and we wanted to make the most of that. It was a new experience in this form. Another point is the different length versions featured in the new range. Having these allows us to quickly generate engineered sensor lengths.
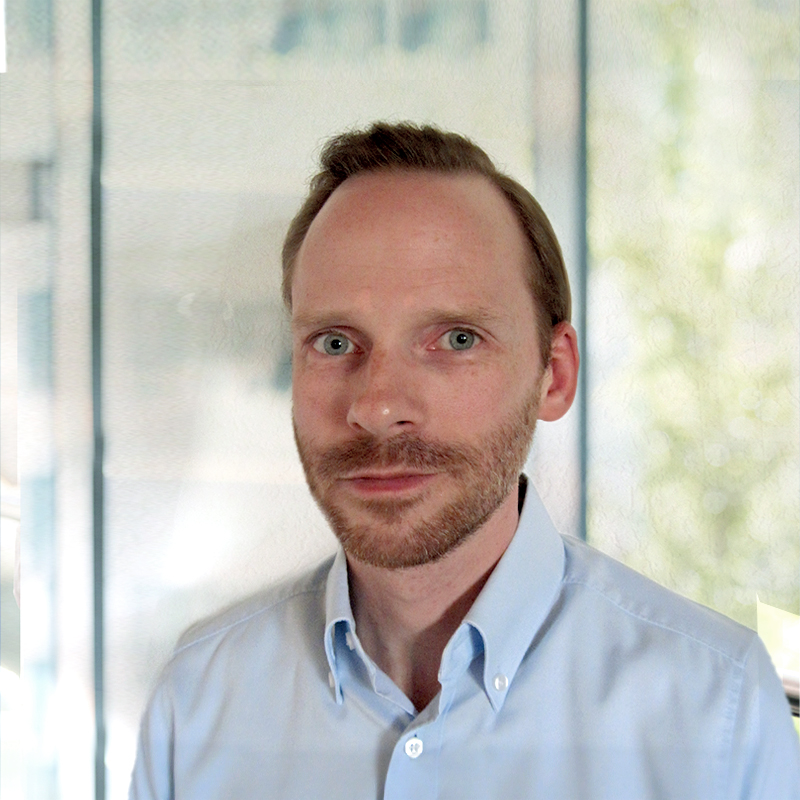
Johann ElterIn terms of sensor marking, we focused on a new technology. To replace the usual printing, we now boast a much more rugged laser marking on the housings. The previous sensors were mainly printed on the face—often difficult to access in customer applications and therefore difficult to read. We took customer benefits into consideration here. I want to return to the different length versions in our new range. This aspect was tricky to implement with our old sensors, since we always had to develop new electronics. They had to be requalified in the test lab. Essentially, we were realizing a new development with each product. Overall, this created longer reaction and development times. Our new concept enables us to be prepared for customized lengths. Owing to certain design measures, we can quickly generate different length versions in the 5 mm grid. Extremely compact electronics have been developed with this in mind. The entire production concept is highly flexible and harmonized with the new product family. We can say that we can now map customer requirements from length x to length y with the electronic features required by the customer.
Johann ElterDefinitely, especially with our Asian customers. Customer requests pretty much always relate to speed. European customers are patient and are used to waiting. Asian customers expect a solution on their desk within two weeks. For this reason, our sales teams in countries like China must always be very clear that they are presenting just a sample to customers and not a ready-to-use, quick-to-launch series product. It is difficult to convey that all our testing and certification measures create delays. The new processes ensure that customer versions can now be generated and delivered much quicker.
Patrick DrebesIt is not that simple to quantify. There are competitors with in-house manufacturing technology that is not as flexible because it is fixed to the length.
Johann ElterI have yet to find competitors offering sensor length versions like we do. And this is the field where we receive surprisingly frequent requests. Notwithstanding exotic requests, which we could realize, we can say: We can always produce all housing lengths from 30 to 70 mm. The typical Pepperl+Fuchs lengths were always the traditional 50 mm, as offered by the competition. Then came the short housings of 40 mm, and that was it. We have now expanded the range significantly in both directions to better meet the needs of our customers. We should therefore be a huge step ahead of the market, if not the only ones with this degree of flexibility.
Patrick DrebesI also think that there is no better competition out there. There are solutions that rely on flexible connections, but the handling is much more complex. The new concept is a fantastic, unique solution, especially with regard to length versions, which makes us extremely flexible.
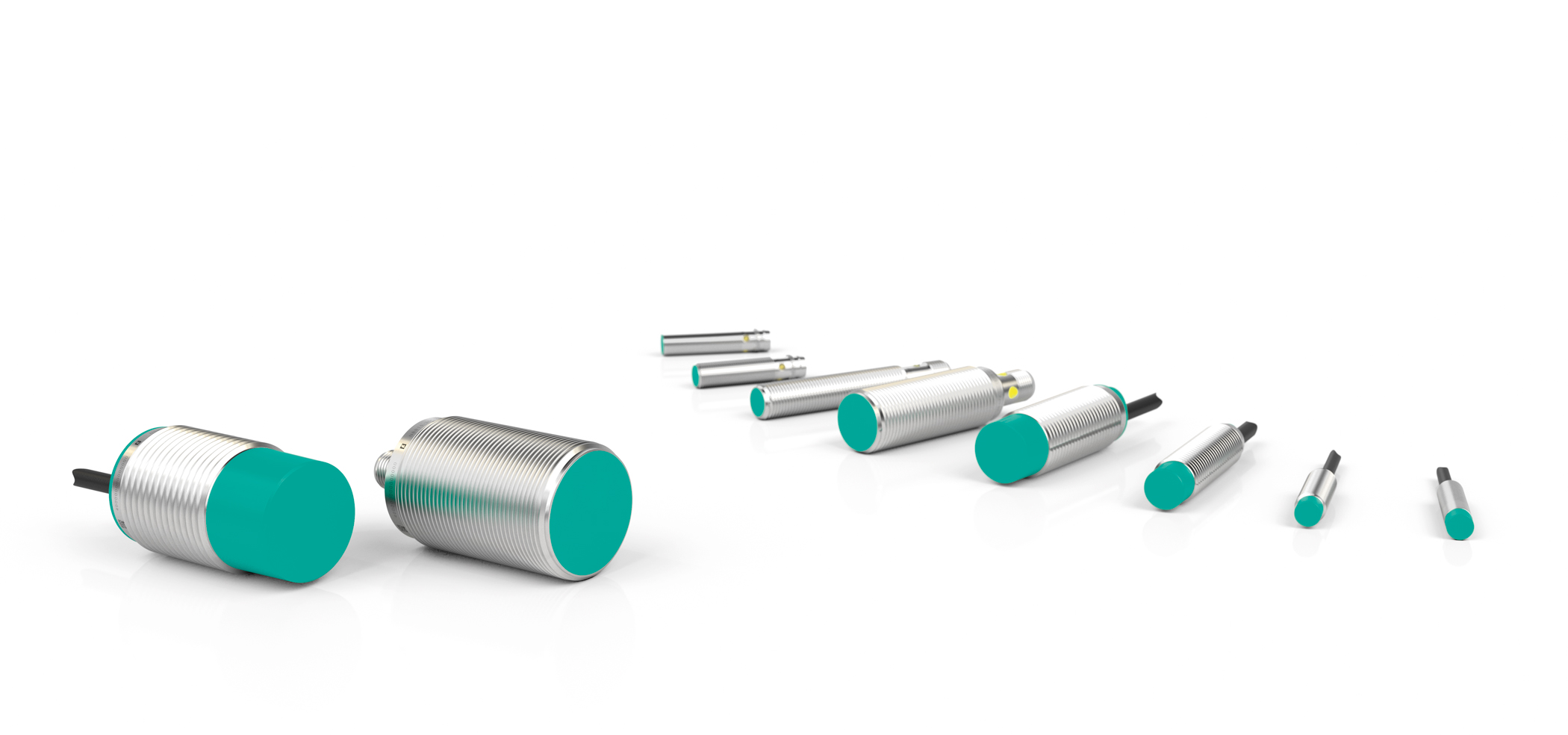
State-of-the-Art: The innovative portfolio of inductive cylindrical standard sensors with more than 200 000 variants.
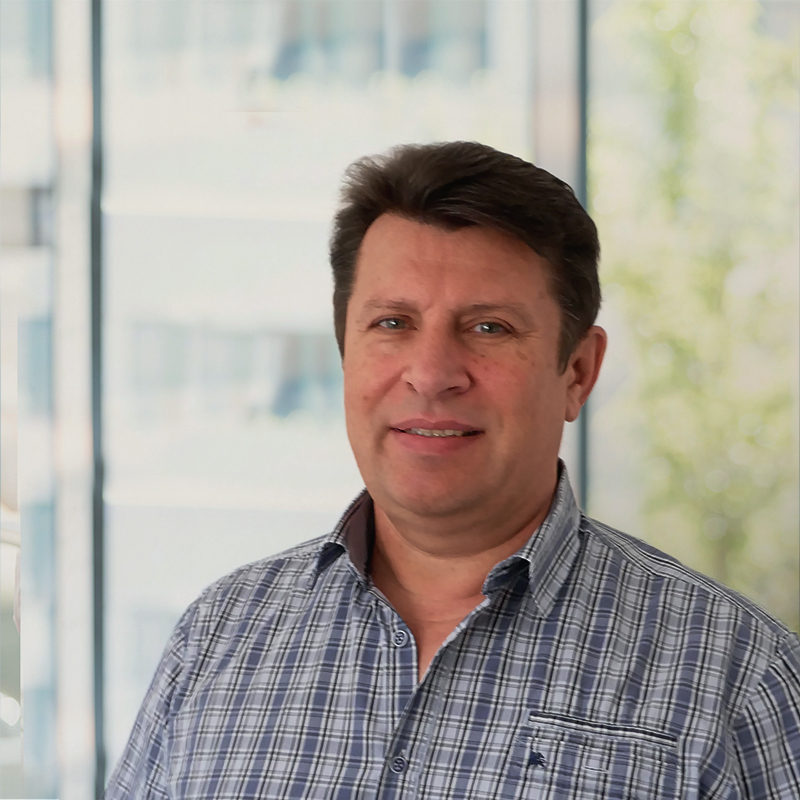
Johann ElterKeeping the future in mind is a must. Currently, we are developing a new sensor generation to serve Industry 4.0. This is a solution with IO-Link based on the same mechanical concept. Saying that, however, the inductive sensor is not going anywhere in its current form. This is due to high demand and the fact that the current trend is swinging to traditional sensor technology. Not every customer wants to work with digital communication or needs to integrate digitized applications into their manufacturing processes. A fair number of our users are electrical installation engineers, who want to screw on the sensors and adjust the switching point by turning it in or out. Then the sensors need to operate reliably. One of our customers produces wind turbines and wanted to measure the wear of its pitch bearing in the generator with an analog signal. We offered to provide the signal digitally via an IO-Link interface. But the customer wanted the raw signal to evaluate it using in-house algorithms. Intelligent sensors are not required in these instances—the intelligence comes from the user's control system. The camps are split as far as IO-Link is concerned, something that I think will remain the case. Some find it great, while others prefer traditional technology.
Patrick DrebesWith the current design, we are a bit limited; it is a very replaceable product. This is common to all manufacturers, including in this design. There is not much room for maneuver. But with the steps we have taken—new coating, new materials, improved visibility of the LED—I can see us continuing to drive that forward. But it will not be this design to undergo a huge revolution. Ultimately, it is a cylindrical sensor with a threaded sleeve. It will continue along the path we are on now, but will evolve.
Johann ElterI am of the same opinion. It was an essential goal to once again enhance the standard of quality to ensure we are a cut above cheaper competitors. A clear example of this is a Chinese customer that built a solar power plant in the Gobi Desert. Originally, we were supposed to receive the full order, which, ultimately, became a third of that. We did manage to secure repeat business, meaning our quality impressed. Quite simply, our sensors performed better in this harsh environment than those of other manufacturers. I think we need to push further in this direction by having an elevated, improved standard of quality that will leave the competition behind. Our technologies and the name Pepperl+Fuchs are synonymous in the market with precisely that.