May 29, 2022
Finger on the Pulse—Between Science, Research, and Industry
Get an idea of how even small and medium-sized companies can set up smart industrial production and intralogistics tailored to their needs at Technology Center for Production and Logistics Systems at the Landshut University of Applied Sciences. On hand: state-of-the-art sensors and automation components from Pepperl+Fuchs.
The modern factory with intelligent production and logistics systems does not have to wait much longer—it already exists, in Dingolfing in Lower Bavaria, Germany. Contrary to what you might expect, however, it is not the factory of an internationally renowned automobile manufacturer. Anyone interested in state-of-the-art intralogistics should pay a visit to the Technology Center for Production and Logistics Systems (TC PULS) at the Landshut University of Applied Sciences and talk to the research director Professor Markus Schneider. The economist has developed precise strategies for the success of modern industrial production.
Working closely with automation specialists such as Pepperl+Fuchs, Schneider seeks organizational and technical solutions to form part of the perfect production and logistics processes. Schneider sums up his goal: “We want to help SMEs and support companies so that they can manufacture competitively even in a high-wage country like Germany.” This is not always easy, however, as he and his team tell us on a tour of TC PULS.
The Process is the Decisive Factor for Successful Automation
From the viewing platform you can see the complete, fully functional training and demonstration factory, which is a unique model in the German university landscape. Prof. Schneider is accompanied in the gallery by his scientific colleagues Lisa Schuler (M. Sc.) and Tobias Ettengruber (M. Eng.), as well as Rudolf Buchner, Factory Automation Sales Engineer at Pepperl+Fuchs.
“The machines and components on display here represent a complete internal value chain, from goods receipt to shipping,” explains Schneider. From here, trade visitors from all over the world can view a perfectly replicated value stream consisting of incoming goods, storage and picking zones, three production areas, and outgoing goods.
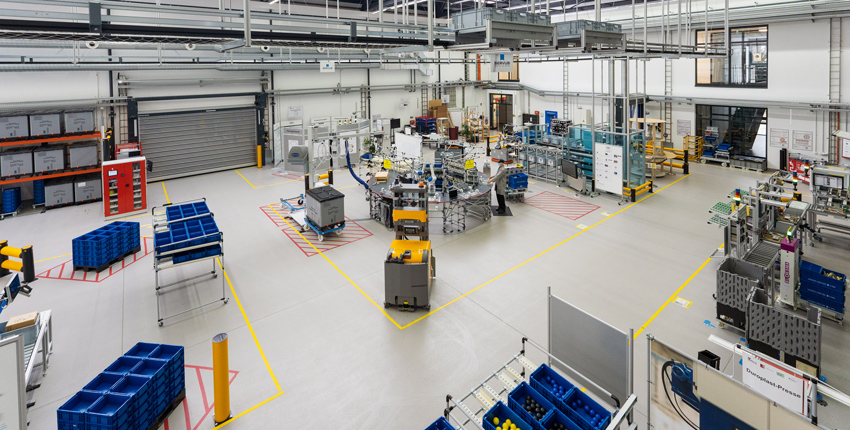
Schneider, himself a factory and logistics planner with many years of practical experience in the automotive industry, explains why he and his team designed the demonstration factory in this way. Experience from hundreds of consulting sessions and factory visits has shown him that the most important first step for manufacturing companies to take is to take a close look at the quality of their processes. In his opinion, Germany’s technological leadership is precisely where the biggest problems lie. Schneider explains: “Many companies approach their problems exclusively from the technical side and neglect the process aspect. If you digitize a bad process, you get a bad digitized process, and if you automate a bad process, you end up with a bad automated process.”
Viewing Processes Vertically
This is the first step in Schneider’s research. He is also able to consider issues such as sustainability and environmental protection because he looks at processes from a vertical perspective. In the long term, this could help companies not only expand their production, but increase it. For the economist and his team, one thing is crucial: “At TC PULS in Germany, we have created a secure base that any manufacturing company can take as an example of how best to organize its processes. With our lean factory, we meet companies where they are right now and show them how to create stable processes with simple structural and organizational measures.” After all, says Schneider, “We want to support SMEs, and they are very diverse.”
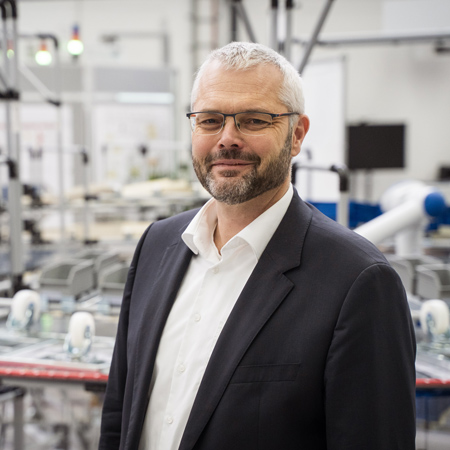
Designing Flexible Production Concepts and Sensor Technology
Schneider is keen to stress the importance of not just looking at the technical progress that can be made, but above all to consider how the process can be improved. The engineers at TC PULS therefore try to carry out their research in a way that is as close as possible to the actual working reality. “At this lean production plant in the demonstration factory, for example, we can efficiently produce 185,000 dollies. However, we can also convert this plant into a traditional workshop production setup and then, together with a customer, transform it into a flow production setup.” This is the best way to illustrate lean production concepts to customers. Schneider, Schuler, and Ettengruber are in agreement that “it does not make sense to simply install RFID components in an old process.” On the contrary, it is important for companies to align their processes with fundamental principles. “And these principles,” says Ettengruber, “can also be applied to technology.”
A wide variety of Pepperl+Fuchs technologies are used to implement the intelligent storage and logistics processes in the TC PULS factory. “Our partnership with TC PULS is a fruitful one for both parties. The best example is the TC PULS warehouse. This is where distance sensors are traditionally used. Nevertheless, we have worked together to experiment with using capacitive sensors and ultrasonic sensors in this area,” explains Buchner, adding: “Tests such as these are beneficial for both sides, because the intralogistics area shown here can be used in a live demo that is applicable to almost all areas and industries.”
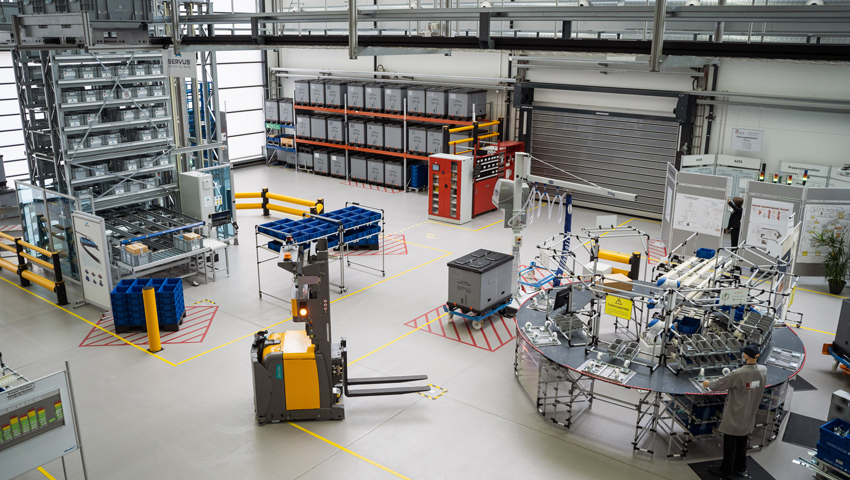
Why Exchanging Expertise Is So Important
For example, Buchner was able to connect one of his customers, a renowned German metrology company, to the experts from TC PULS. The result: The RFID solution that the company had originally wanted to use for its intralogistics processes was analyzed in the context of all of the company’s processes. Together with the customer and TC PULS, Buchner and everyone involved in the project developed an intralogistics solution that was precisely tailored to the company’s processes.
One aspect was particularly important to Buchner: “Working with TC PULS opens up real opportunities to transfer knowledge from research and sensor development to the industry. Our customers are extremely varied; not everyone can always imagine these new processes. Here at the TC PULS factory, they have the opportunity to experience modern intralogistics processesthat range from simple to very complex solutions.”
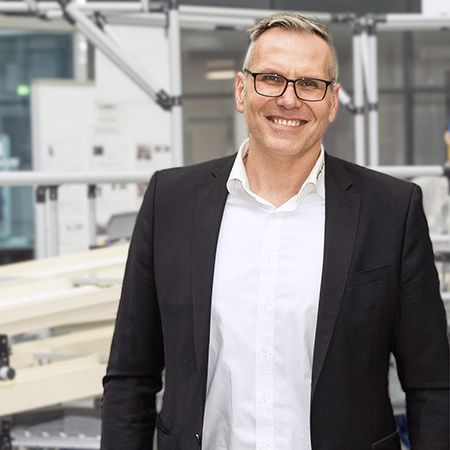
From a U-cell to an O-cell: How the Future May Look Like
Professor Schneider points out two other important “employees” on his team: Life-size mannequins in work clothes at the workbench and planning board. “We always put people at the heart of what we do—whether that be employees or managers.” This is also why he and his team removed the rigid U-cell production setup and transformed it into an O-cell. The goal is to automatically provide the employee with both material and information. Time-consuming picking and transporting of new parts is no longer necessary. Schneider emphasizes: “We make the most of the unique capabilities of humans and automate logistics instead.” No easy task, but possible— and supported by high-quality automation technology from Pepperl+Fuchs. An RFID system, photoelectric sensors, the R2000 2-D LiDAR sensor, ultrasonic sensors, inductive and capacitive sensors, and IO-Link masters from the ICE2 and ICE3 series—all of these components make it possible to skillfully juggle data at the meta level and therefore control all processes in the model factory.
Digitalized Manufacturing Processes
Lisa Schuler’s daily work is based on the principle of trial and error, or testing and optimizing. By programming an interface, the research associate has contributed to develop software that ensures employees are continuously supplied with material for production. “The result? Manual operations such as picking up new parts are no longer necessary. RFID components from Pepperl+Fuchs make this possible through modern interfaces and protocols,” explains Schuler.
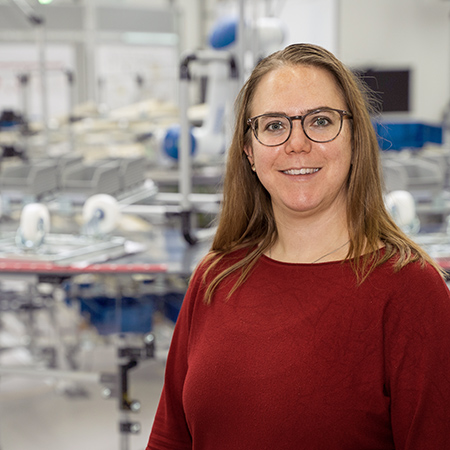
To understand the complexity of Schuler’s task, it is worth recalling the structure of the O-cell: Workers stand on the outside of the cell and assemble trollies at their workstations. A robot is positioned in the middle, inside the O-cell. In this scenario, if the employees run out of screws, they place the empty screw boxes into a Kanban rack underneath their workbench. The empty box is now detected using an RFID system: The data that makes up the product or object-related information is stored on an embedded RFID tag. An RFID read/write head identifies the identification number attached to the screw box and can forward the required information to the controller, which provides the transport coordinates. The six-axis robot in the middle of the O-cell now only has to deliver a new box of screws to the Kanban rack using the corresponding coordinates and place the empty box at the defined location. This allows the employees to concentrate fully on assembling the trollies.
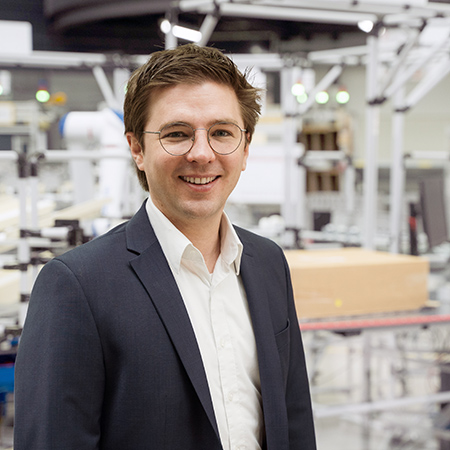
IO-Link Master: The Road to Digital Networking
Ettengruber emphasizes that “When we establish new processes, we should also look to the future. The IO-Link system solutions from Pepperl+Fuchs are paving the way to digital networking.” The sensor manufacturer with its headquarters in Mannheim/Germany, Twinsburg/USA and Singapore, offers a comprehensive portfolio, covering everything from sensors to the cloud. Of particular note is the IO-Link master with MultiLink™ technology. Based on the multiple access concept, sensor data can be transmitted in the conventional way to a PLC and simultaneously, for example, via MQTT to cloud-based systems, higher-level controllers, or to warehouse management systems. Existing systems can be expanded in this way without interfering with the actual automation control systems. The standards integrated into the IO-Link master, such as OPC UA and MQTT, make it easier to set up processes and keep the programming effort low. Lisa Schuler, who is responsible for integrating and networking the systems at TC PULS, demonstrates what Ettengruber means: With two clicks she navigates to her program, and can retrieve and process data from all the sensors installed in the factory.
Intelligent Intralogistics? Not without Automated Guided Vehicles
Jungheinrich’s automated guided vehicle (AGV), for example, is equipped with an R2000 2-D LiDAR sensor from Pepperl+Fuchs to reliably move and transfer large load carriers (LLCs). The R2000 is based on the PRT (Pulse Ranging Technology) measurement method and is ideal for precise and highly dynamic position determination. “With the help of the R2000, the forklift can move 360° freely in the hall. In addition, the very high angular resolution and the especially small light spot of the 2-D LiDAR sensor guarantee maximum precision and therefore a very accurate position value—perfect for modern and dynamic production and logistics processes such as here at TC PULS,” adds Buchner.
High-Bay Testing Ground
The AGVs operate with racks several meters high holding LLCs, and it is these racks that are of particular interest to engineer Ettengruber, as they demonstrate the diversity of automation options: “For test purposes, we have now installed many Pepperl+Fuchs sensors with different functional principles at various positions on the rack. Both conventional inductive proximity sensors and photoelectric sensors are used; ultrasonic sensors are also located on the struts. However, it is not necessarily the case that they remain in the same place once they have been installed.” Rather, Ettengruber tests placements, reinstalls them in a different location, and therefore opens up new ways of thinking about pioneering intralogistics and their processes for himself and his team.
The cooperation between science, research, and an automation specialist like Pepperl+Fuchs is therefore an example of how the exchange of expertise can make SMEs and industry as a whole more competitive and therefore more future-proof.