June 26, 2023
Sun, Sand and Safety
With the solarROBOT pro, hyCLEANER brings to large-scale photovoltaic systems on roofs and outdoors what robot vacuums have done domestically for a long time now: The semi-automated cleaning machines reliably remove dirt from solar panels, therefore promoting the systems’ energy yield and longevity. Ultrasonic sensors from Pepperl+Fuchs play a critical role when it comes to safety.
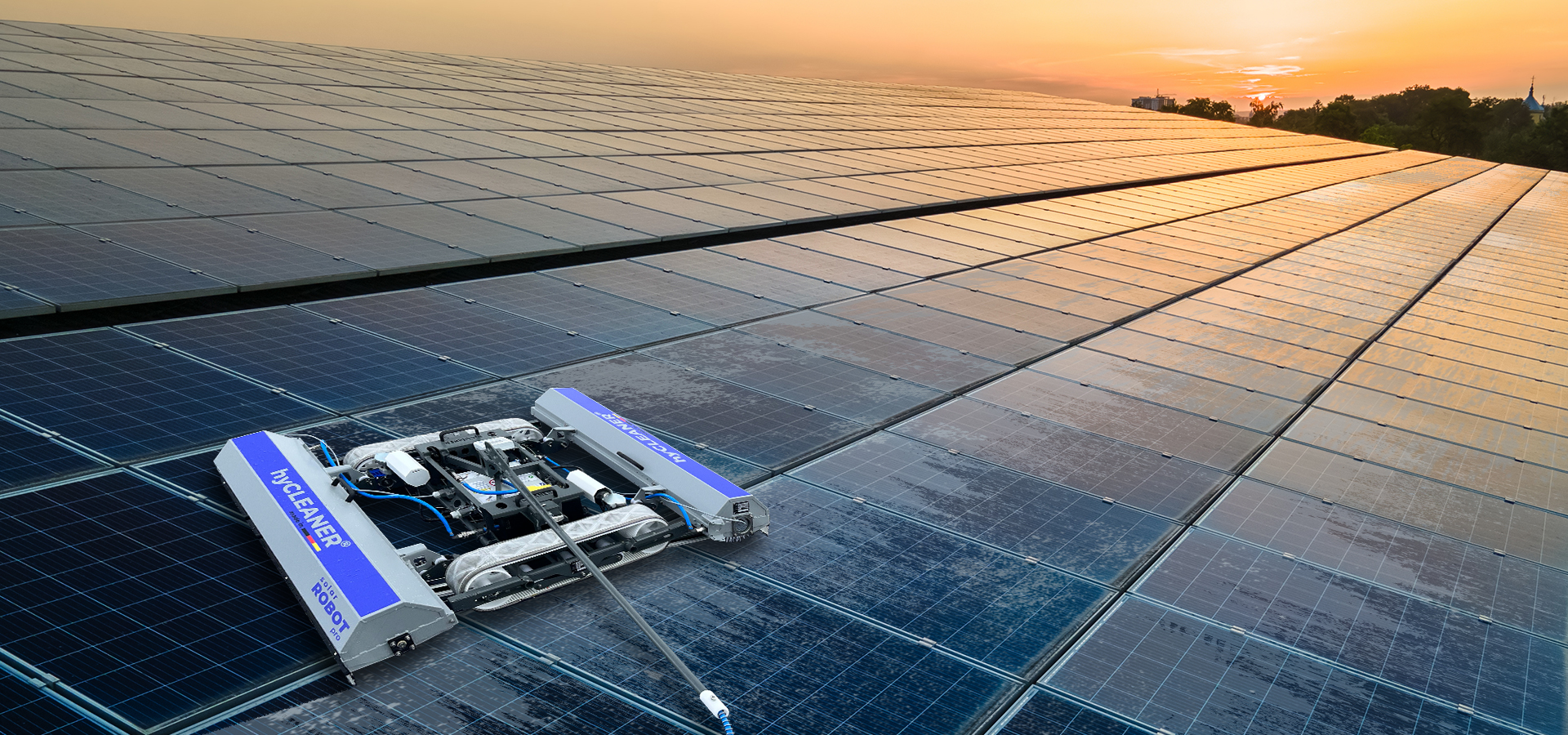
The sun has heated up the air and the ground throughout the day, and looking into the distance, you can only see a haze over the asphalt. This is not an uncommon sight, especially on warm summer days. The power of the glowing celestial body is enormous, despite the fact that it's almost 150 million kilometers from the Earth. This energy is used by solar power plants. In addition to hydrogen and wind turbines, generating energy using the power of the sun is regarded as an important measure in reversing climate change. Especially in sunny regions, large-scale photovoltaic systems with areas covering several thousand meters squared are therefore being developed to achieve the highest possible yields. The downside of this, however, is the time-consuming cleaning these large-scale installations require. This is especially applicable in dry regions or areas near agriculture where sand, dust, and dirt particles contaminate the solar panels. This dirt not only reduces energy yield, but also damages seals and surfaces. Regular cleaning is therefore required to optimize the energy yield and increase the longevity of photovoltaic systems.
hyCLEANER GmbH & Co. KG, headquartered in Gronau, Westphalia, has taken on the task of supporting plant operators and cleaning companies in this process, and has developed the hyCLEANER solarROBOT® pro. Originally designed for glass roofs, the innovative solarROBOT pro is now being adopted for cleaning large-scale solar plants with its partially automated and robot-supported system—contributing to greater energy yield and efficiency, and increasing safety during maintenance.
Effective Cleaning on a Large Scale
The solarROBOT pro can clean up to 2400 m² per hour and is therefore significantly superior to manual cleaning. The robot is battery-powered and operates using special driving pads so it has the necessary grip to move on the large glass surfaces of the photovoltaic systems. Integrated brushes take care of cleaning—with or without water. The hose for the water supply is attached directly to the solarROBOT pro, an optional retractable hose reel can also be integrated. With a water consumption of 0.5 l/m², the hyCLEANER cleaning robot requires significantly less water than a high-pressure cleaner and still effectively cleans the surfaces of dirt and dust—without chemicals.
In addition to efficiency and high-performance cleaning, another aspect was also very important to the creators during the conception: "The impetus for the development of the solarROBOT was not only to make the work easier, but also to increase safety for people and the environment," explains Celina Kneiber, Managing Director at hyCLEANER. For this reason, the company makes use of innovative ultrasonic sensors from Pepperl+Fuchs.
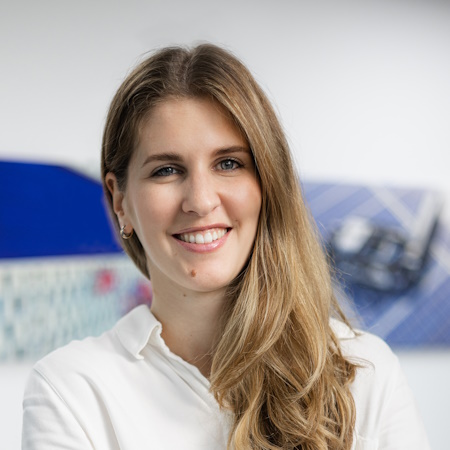
Safety First
'Working on slippery glass surfaces with set inclination angles or on high roofs always poses a certain risk to people,' explains Kneiber. 'With our cleaning robot, people are able to stay in a safe environment while the solarROBOT does the work.' The solarROBOT pro can be operated via a radio remote control. The Auto-Drive function with speed control and lane keeping system makes this especially convenient—the robot automatically moves across the surface without personnel having to continuously control it. However, to prevent the machine itself from falling off an edge and therefore prevent accidents and damage, hyCLEANER has equipped the cleaning robot with the very compact and precise ultrasonic F77 sensors from Pepperl+Fuchs. 'An ultrasonic sensor is installed at each of the four corners of the solarROBOT, which looks downward and always detects the surface of the solar panels,' explains Jan Schirweit, Sales Engineer at Pepperl+Fuchs. 'If one of the sensors detects that there is no longer an object in its detection area, i.e., the surface ends, the robot stops automatically and warns the operator with an acoustic signal.' The operator has the option of overriding the automatic stop and instructing the robot to continue to move—for example, if there is only a small gap—or to make the robot turn.
With the help of the ultrasonic sensors from Pepperl+Fuchs, this automatic edge detection prevents the robot from falling off the system, providing operating personnel with additional protection in the process. The user does not have to keep an eye on whether the robot is moving too close to an edge, but can trust the F77 ultrasonic sensors to monitor this. This has two benefits, firstly this makes operating the robots easier, and secondly it protects people who may be moving around the plant, while simultaneously avoiding financial ramifications by preventing damage to the robot or system parts.
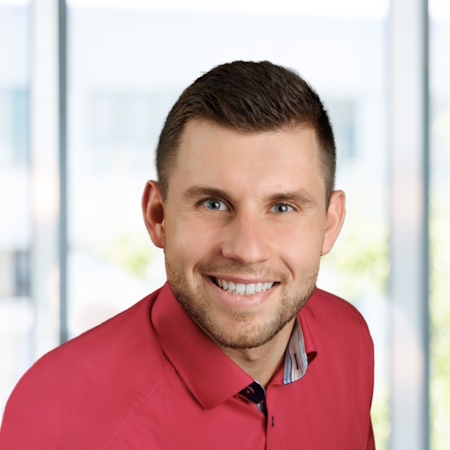
Rugged and Highly Precise: F77
'The F77 ultrasonic sensor is not just the ideal solution for use in the hyCLEANER solarROBOT due to its reliability,' emphasizes Schirweit. 'With a height of just 31 mm, it is especially compact and fits unobtrusively into the design of the cleaning robot.' Both at close range and at distances of up to 400 mm, the F77 detects objects with a high level of precision—in this case the surface of the solar panels in the plants. 'The level of accuracy—for maximum safety when operating the robot—and the compact design of the F77 were the deciding factors when it came to choosing the ultrasonic sensor from Pepperl+Fuchs,' says Kneiber, summarizing the advantages for the cleaning robot. The ultrasonic sensor is also quick and easy to configure and even offers the ability to hide obstructions.
However, this doesn't mark the end for the hyCLEANER solarROBOT pro just yet. "We already have plans to further develop our cleaning robot to make work even easier for our customers," says Kneiber, looking to the future. Safety will definitely be an important issue in future versions. "At Pepperl+Fuchs, we are also happy to support hyCLEANER in the further development of the solarROBOT with our expertise in the field of sensor technology and industrial automation," says Schirweit.