Wasserstoff marsch! Mit der richtigen Infrastruktur ans Ziel
27.03.2024
SOLUTIONS
by PEPPERL+FUCHS
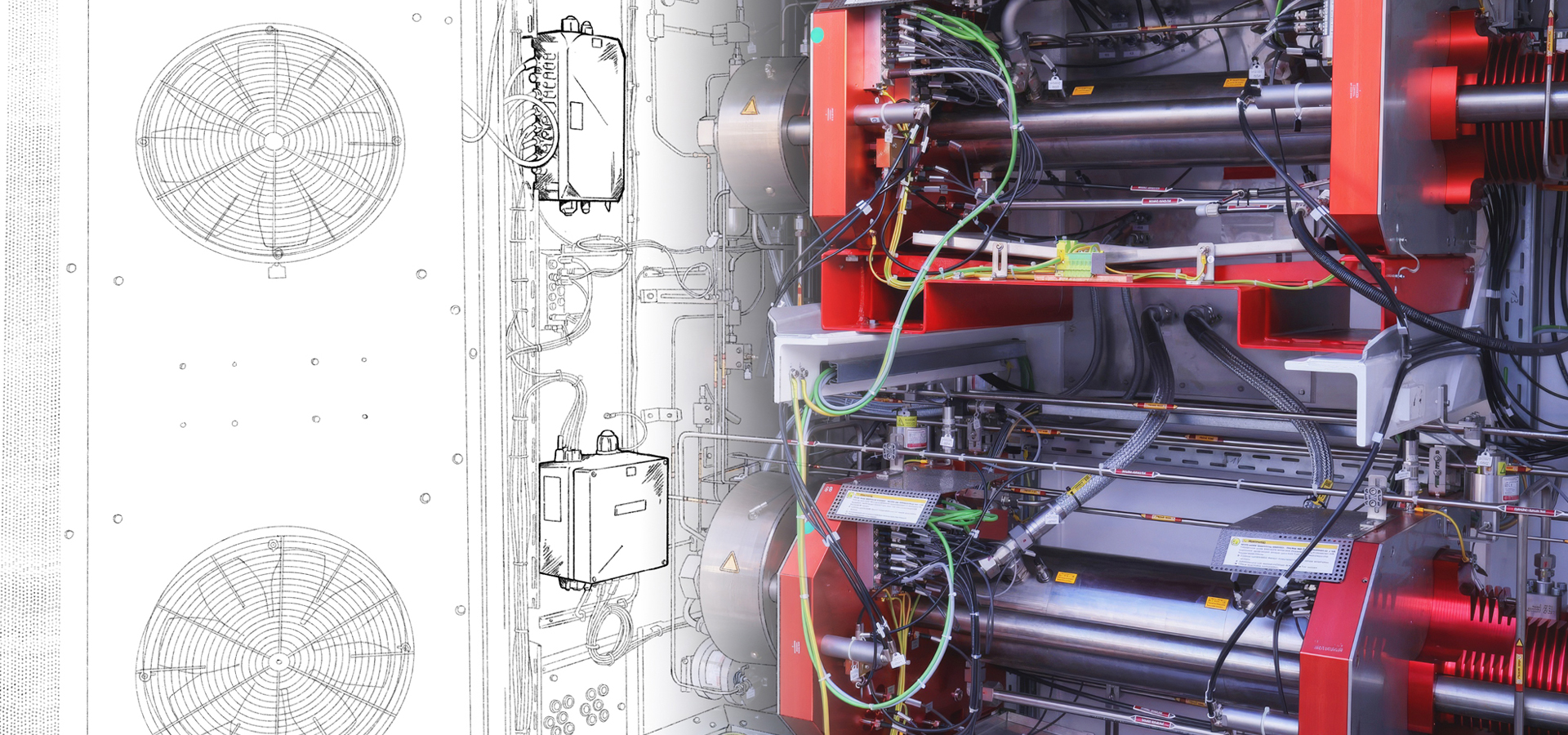
Mit Elektromobilität allein ist die Verkehrswende nicht zu schaffen. Vor allem im Nutzfahrzeug- und Schwerlastverkehr werden aufgrund von Reichweite, Nutzlast und langen Ladezeiten Alternativen zu batteriebetriebenen Elektrofahrzeugen gebraucht. Eine mögliche Lösung ist Wasserstoff: Eine sehr überschaubare Menge des Gases genügt, um auch große Motoren bzw. Brennstoffzellen auf weiten Strecken oder mit anspruchsvollem Höhenprofil mit Treibstoff zu versorgen. Wird der Wasserstoff aus erneuerbaren Energien oder natürlichen Vorkommen gewonnen, ist das Fahren komplett emissionsfrei. Für den breiten Einsatz des Gases im Kraftverkehr braucht es aber auch die nötige Infrastruktur und ein gut ausgebautes Netz von Wasserstofftankstellen, das einen durchgehenden Langstreckenverkehr ermöglicht. Die Maximator Hydrogen GmbH mit Sitz im thüringischen Nordhausen ist auf die Herstellung solcher Anlagen spezialisiert. Für den mechanischen und elektrischen Explosionsschutz in der Signalverarbeitung setzt das Unternehmen auf maßgeschneiderte Lösungen von Pepperl+Fuchs.
Kurze Tankzeiten, große Reichweite
Wasserstoff weist eine sehr hohe Energiedichte auf: Ein Kilogramm komprimierter Wasserstoff hat einen Energiegehalt von 33 Kilowattstunden und enthält damit rund dreimal so viel Energie wie ein Kilogramm Erdöl. Je nach Größe des Fahrzeugtanks sind bereits heute Reichweiten bis 600 Kilometer möglich. Im Schwerlasttransport schreiten die Entwicklungen der Brennstoffzellentechnik und Speichertanks voran, wo Reichweiten bis zu 1.200 Kilometer angestrebt werden. Das Tanken von Wasserstoff ist ähnlich wie bei Benzin und Diesel in wenigen Minuten erledigt. Besonders für Logistikunternehmen sind kurze Betankungszeiten, Reichweiten von über 500 bis 1.000 Kilometern bei vergleichsweise geringen Kosten und eine uneingeschränkte Nutzlast von entscheidender wirtschaftlicher Bedeutung.
Die meisten großen Nutzfahrzeughersteller haben ihr Portfolio inzwischen um wasserstoffgetriebene LKW und Busse ergänzt und entwickeln es stetig weiter. Entscheidet man sich für ein Fahrzeug mit Brennstoffzellenantrieb, setzt die Routenplanung allerdings eine gute Vorbereitung voraus. Das derzeit vorhandene Netz von Wasserstofftankstellen ist je nach Region bisher wenig ausgebaut. Nach Angaben von h2stations.org gab es 2023 auf der ganzen Welt nur etwa 920 Anlagen. Die dichteste Ballung an vorhandenen und geplanten Wasserstofftankstellen befindet sich in Europa sowie Japan und Südkorea, mit etwas größeren Lücken auch in China. Entlang der Küsten Nordamerikas und im Osten Australiens sowie in Neuseeland findet man bisher nur vereinzelt Wasserstofftankstellen. Es liegt also auf der Hand, dass hier Handlungsbedarf besteht. Das Potenzial ist groß.
Steigende Nachfrage nach Wasserstofftankstellen
„Beim Ausbau des Wasserstofftankstellennetzes stehen wir noch ziemlich am Anfang, aber die Kurve geht deutlich nach oben. Wir schätzen den absehbaren Bedarf an Neuanlagen auf rund 20.000 Tankstellen pro Jahr weltweit“, erklärt Erik Albrecht-Laatsch, Head of Engineering bei Maximator Hydrogen, und fügt selbstbewusst hinzu: „Davon möchten wir mindestens 20 % liefern.“ Im bereits gut ausgebauten Infrastrukturnetz der Schweiz hat das Unternehmen dieses Ziel übertroffen: Stand heute stammen 16 von insgesamt 17 Anlagen von Maximator Hydrogen. In dem flächenmäßig vergleichsweise kleinen Land waren es vor allem die Logistikunternehmen und großen Lebensmittelhändler, die sich als Vorreiter für den Bau von Wasserstofftankstellen für ihre Fahrzeugflotte entlang der Lieferketten entschieden und ein flächendeckendes Netz aufgebaut haben. Der Vorteil dabei: Die H2-Tankstellen sind für alle anderen Verkehrsteilnehmer ebenso frei zugänglich und nutzbar.
Die Schweiz verfügt bereits über ein gut ausgebautes Netz an Wasserstofftankstellen. 16 von derzeit 17 Anlagen stammen von Maximator Hydrogen.
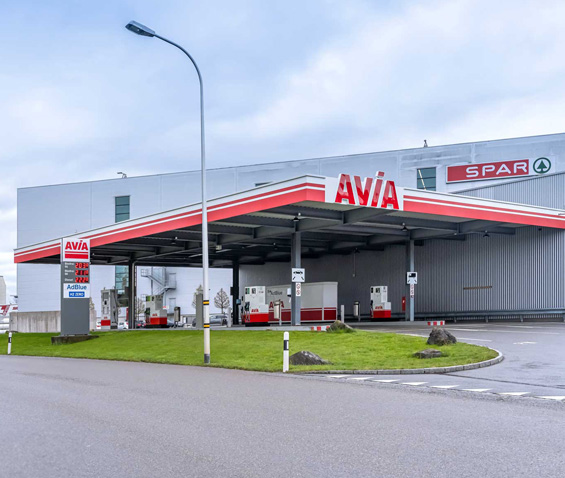
Die Wasserstofftankstellen von Maximator Hydrogen bestehen aus einzelnen Elementen, die individuell konfiguriert werden können. Für die Sicherheit seiner Anlagen vertraut der Hersteller auf explosionsgeschützte Lösungen von Pepperl+Fuchs.
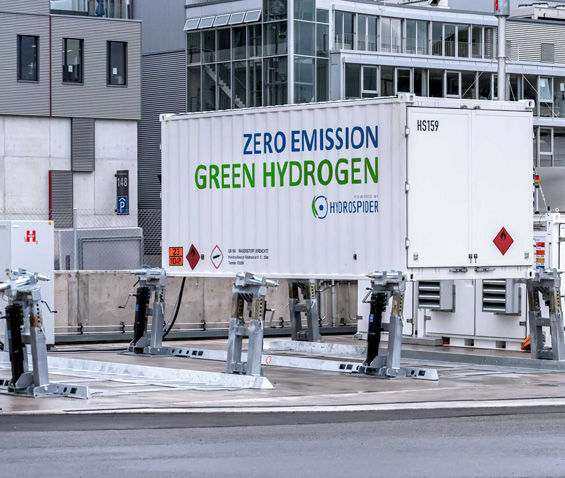
Die Betankung mit Wasserstoff geht schnell und einfach. In wenigen Minuten ist ein LKW vollgetankt und fahrbereit.
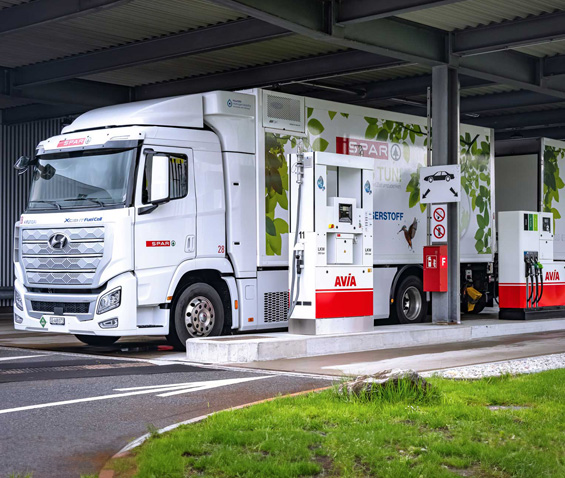
Von Skandinavien über West- bis Südeuropa ist der Anlagenbauer an mehreren Wasserstoff-Infrastrukturprojekten beteiligt. Das Unternehmen gehört zur Schmidt Kranz Group, die ihre Wurzeln in der Bergbautechnik hat. Das Know-how in der Hochdrucktechnik besteht in der Tochterfirma Maximator GmbH, die seit den 1970er Jahren in diesem Bereich aktiv ist. 2019 fiel die Entscheidung, mit Maximator Hydrogen einen Spezialanbieter zu schaffen, der sich ganz auf die Herstellung von Wasserstofftankstellen konzentriert. Im Hinblick auf die Technologie war dies ein naheliegender Schritt, denn auch beim Wasserstoff steht die Kompression, also Verdichtung eines Gases, im Mittelpunkt. Der Aggregatzustand des alternativen Treibstoffs macht nämlich den entscheidenden Unterschied zur klassischen Tankstelle für herkömmliche Kraftstoffe aus. Dort muss aus der Zapfsäule lediglich eine Flüssigkeit aus einem großen in einen kleineren Tank gepumpt werden. Der Tankvorgang mit Wasserstoff ist dagegen wesentlich komplexer, denn hier muss ein hochverdichtetes Gas von einem Druckspeicher in einen anderen gepresst werden.
Umfüllprozesse unter Hochdruck
„Hochdrucktechnologie spielt bei Wasserstofftankstellen in der gesamten Anlagenkette eine wichtige Rolle“, erklärt Albrecht-Laatsch. Aus dem Elektrolyseur strömt das Gas mit einem relativ geringen Überdruck von 30 bis 60 bar. Das Druckniveau des Speichertanks einer Wasserstofftankstelle liegt vielfach höher – bei einem Hochdruckspeicher bei rund 1.000 bar.
Der Transport von Wasserstoff via Pipeline, wo deutlich niedrigere Druckstufen ausreichen, spielt eher in industriellen Anwendungen eine Rolle. Für die Nutzung im Straßenverkehr wird das Gas wie herkömmlicher Kraftstoff vorrangig per LKW-Trailer angeliefert, wobei die Elektrolyse vor Ort immer mehr an Bedeutung gewinnt. Auf seinem Weg von der Erzeugung im Elektrolyseur bis zum eigentlichen Fahrzeugtank unterliegt der Wasserstoff mehreren Umfüllprozessen und Druckänderungen. Ein voller PKW-Tank kommt auf ca. 700 bar, bei Nutzfahrzeugen, sogenannten Heavy Duty Vehicles wie LKW, Traktoren, Zügen oder Schiffen, ist es etwa die Hälfte. „In der Regel reicht die Druckdifferenz des Wasserstoffs zwischen dem abgebenden Speicher und dem Fahrzeugtank nicht aus. Der Wasserstoff muss also verdichtet werden, damit die gewünschte Menge überhaupt und schnell genug dort ankommt, wo sie hinsoll“, erläutert Marcel Urban, Team Lead Electrical Engineering bei Maximator Hydrogen.
Wasserstoffverdichter mit Alleinstellungsmerkmal
Für die Verdichtung des Wasserstoffs hat Maximator Hydrogen das MAX Compression System entwickelt, das Herzstück ihrer Anlagen. Die eigentliche Arbeit leistet dabei ein hydraulisch angetriebener, zweistufiger Kolbenkompressor, der den Wasserstoff auf bis zu 1.000 bar verdichtet. Seine Kolben sind mit Dichtungen versehen, die durch das vorherrschende hohe Druckniveau einem unvermeidlichen, starken Verschleiß ausgesetzt sind. Ihre Lebensdauer beträgt rund 600 Betriebsstunden, danach müssen sie gewechselt werden. Das Verdichtersystem von Maximator Hydrogen weist hier ein Alleinstellungsmerkmal auf: Wo der Wechsel einer Kolbendichtung bei anderen Herstellern einen mehrtägigen Stillstand nach sich zieht – weil die Verdichtereinheit z. B. demontiert oder für den Dichtungswechsel komplett getauscht werden muss – erledigt die Anlage von Maximator Hydrogen diese Wartung innerhalb weniger Minuten vollautomatisch. Je nach Ausführung werden drei bis dreizehn Dichtungen in einem Magazin als Ersatzvorrat vorgehalten. Die „Automatic-Seal-Exchange“-Technologie erkennt, ausgelöst durch Sensoren, wann eine Dichtung verschlissen ist und tauscht diese automatisch.
Modulare Anlagen, explosionsgeschützte Signalverarbeitung
Eine weitere Stärke des Herstellers ist die modulare Flexibilität seiner Wasserstofftankstellen. Alle Elemente, von der Anlieferung über die Verdichtung und Speicherung bis zur Betankung, können nach den Anforderungen des Tankstellenbetreibers individuell konfiguriert werden. Hier spielen die explosionsgeschützten Komponenten und Lösungen von Pepperl+Fuchs eine entscheidende Rolle. Denn unabhängig von der jeweiligen Ausführung sind die Anlagen komplexe Systeme mit einer aufwendigen Steuerung und Signalverarbeitung. Da Wasserstoff eine sehr hohe Zündfähigkeit aufweist, muss die gesamte Signalgebung und -verarbeitung explosionsgeschützt sein. Die umfangreich bestückten Schaltkästen enthalten unter anderem Trennbarrieren und dezentrale Steuerungskomponenten in teilweise fehlersicherer Ausführung sowie Anschlüsse für Sensoren wie Temperaturfühler und Drucktransmitter. Bevor sie in die Anlagen eingebaut werden dürfen, müssen diese nach den Richtlinien für den Explosionsschutz zertifiziert sein. Doch nicht immer sind Standard-Explosionsschutzkomponenten für alle Anforderungen geeignet. Die modulare Flexibilität der Anlagen von Maximator Hydrogen erfordert auch flexible Lösungen hinsichtlich des Explosionsschutzes.
Flexibilität im Explosionsschutz – geht das?
„Hier treffen zwei Anforderungen aufeinander, die sich eigentlich nicht besonders gut vertragen“, sagt Matthias Ernst, regionaler Vertriebsleiter für Prozessautomation bei Pepperl+Fuchs. „Auf der einen Seite stehen die rigiden Vorgaben bei der Zertifizierung im Explosionsschutz, auf der anderen das Konzept der modularen Flexibilität der Tankstellenanlagen. Bei nachträglichen Veränderungen an einem einmal zertifizierten System ist ganz schnell der Punkt erreicht, an dem eine komplette Neuzertifizierung nötig wird. Dafür genügt schon das Hinzufügen zusätzlicher Schaltkreise oder eine Änderung des Temperaturbereichs“, erklärt Ernst.
Mit diesem Punkt verweist er auf eine Modifikation, die nötig wurde, als Maximator Hydrogen im vergangenen Jahr Aufträge aus Skandinavien erhielt. Die Anlagen müssen dort auch bei deutlich niedrigeren Außentemperaturen einwandfrei funktionieren. Daher werden die Gehäuse bei Bedarf beheizt. „Eine Heizung braucht relativ viel elektrische Energie, und das ist im Explosionsschutz alles andere als eine Kleinigkeit“, stellt Urban fest. „Neben dem Heizmodul können weitere Bausteine wie Trennbarrieren für zusätzliche Temperaturfühler und Steuerungskomponenten zum Einlesen der Signale benötigt werden – je nach Konfiguration entsprechend den Anforderungen unserer Kunden. So kommt in den Klemmenkästen oft eine sehr komplexe und vor allem individuell angepasste Bestückung zusammen“, führt Urban weiter aus.
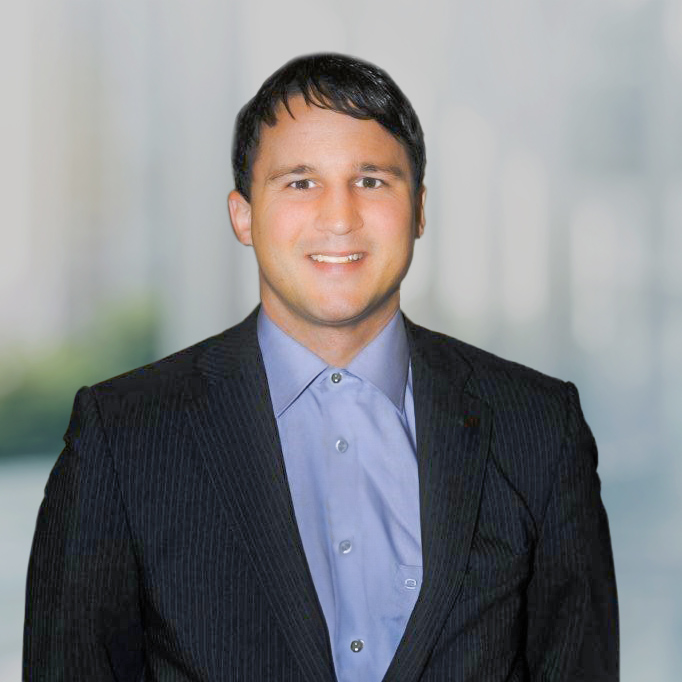
„
Auf der einen Seite stehen die rigiden Vorgaben bei der Zertifizierung im Explosionsschutz, auf der anderen das Konzept der modularen Flexibilität der Tankstellenanlagen.
Hinzu kommen weltweit Unterschiede bei den Zertifizierungen. „Werden die Wasserstofftankstellen in den USA errichtet, sind die Anforderungen an den Explosionsschutz ebenfalls andere. Während in Europa explosionsgefährdete Bereiche in Zonen eingeteilt werden, für die ATEX-Zertifizierungen vorgeschrieben sind, sind in Nordamerika entsprechende Zertifizierungen nach Class/Division nötig“, erklärt Ernst.
Ein einzelner Zertifizierungsprozess kann Monate oder sogar mehr als ein Jahr in Anspruch nehmen. Bräuchte man ihn für jede Produktanpassung, käme es zu enormen Verzögerungen. Daher entwickelte Pepperl+Fuchs in enger Zusammenarbeit mit Maximator Hydrogen ein flexibles Lösungskonzept für die explosionsgeschützte Signalverarbeitung in seinen Anlagen.
Zertifiziert flexible Gehäuselösungen bringen den entscheidenden Vorteil
Die zentralen Elemente, die Pepperl+Fuchs für die explosionsgeschützte Signalverarbeitung in den verschiedenen Modulen der Wasserstofftankstelle entwickelt, bilden Ex-e-Gehäuse. Ex e steht für die Zündschutzart „erhöhte Sicherheit“. Der entscheidende Vorteil ist hierbei die modulare Flexibilität: Die explosionsgeschützten Gehäuse erhalten ab Werk eine Mindestbestückung von ca. 70 – 80 % Gehäuseauslastung, sind aber bereits für eine maximale Belegung zertifiziert. „Maximator Hydrogen kann je nach individueller Konfiguration der Anlage die endgültige Bestückung der Gehäuse selbst vornehmen“, erklärt Ernst. Neben eigensicheren Barrieren wie dem K-System von Pepperl+Fuchs werden dort auch Steuerungskomponenten von anderen Herstellern in die zertifizierte Gehäuselösung integriert. Eine erneute Zertifizierung ist dafür nicht notwendig, diese ist bereits in der Konformitätserklärung und Zertifizierung der Lösung mit abgedeckt.
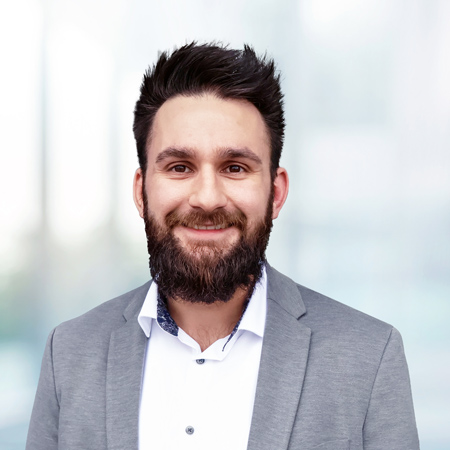
„
Andere Anbieter konnten diese Modularität nicht liefern.
„Andere Anbieter konnten diese Modularität nicht liefern. Dass wir die Ex-e-Gehäuse je nach Kundenanforderung selbst final mit Steuerungskomponenten bestücken können, bringt uns auch gegenüber unseren Wettbewerbern entscheidende Vorteile“, bestätigt Urban. „Die Ex-e-Lösungen von Pepperl+Fuchs kommen mittlerweile in fast allen Modulen, aus denen wir unsere Anlagen zusammenstellen, zum Einsatz. Die einzige Ausnahme ist das Speichermodul, das keine komplexe Steuerung benötigt“, berichtet Albrecht-Laatsch. Im MAX Compression System zur Verdichtung des Wasserstoffs, dem Herzstück der Anlagen, kommen gleich mehrere Lösungen für die Signalverteilung und eigensichere Stromkreise zum Einsatz. „An unseren Modulen zur Annahme und Abgabe des Wasserstoffs an die Trailer verwenden wir ein weiteres Ex-e-Gehäuse im Edelstahldesign, das zusätzlich mit einem Touch-Bedienpanel bestückt ist. Dort bekommt der LKW-Fahrer bei der Anlieferung oder Annahme von Wasserstoff konkrete Bedienungsanweisungen gezeigt und kann die einzelnen Schritte in der korrekten Abfolge starten“, erläutert Albrecht-Laatsch.
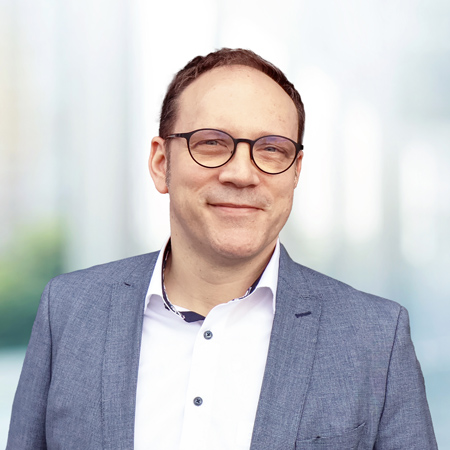
„
Die Ex-e-Lösungen von Pepperl+Fuchs kommen mittlerweile in fast allen Modulen, aus denen wir unsere Anlagen zusammenstellen, zum Einsatz.
Für die sichere Signalverarbeitung der Temperatursensoren kommt das K-System von Pepperl+Fuchs in einer zertifizierten Ex-e-Gehäuselösung zum Einsatz.
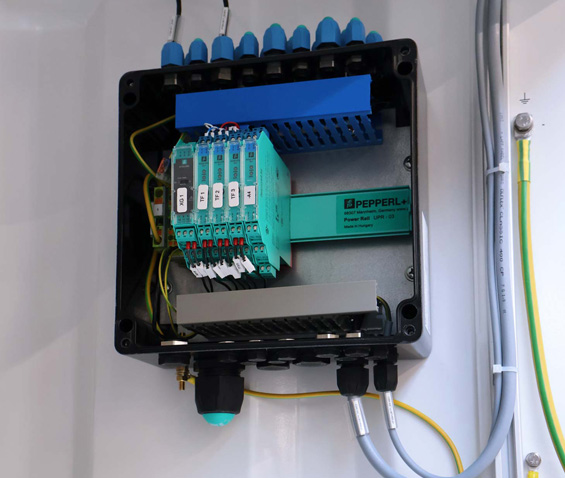
Im MAX Compression System zur Verdichtung von Wasserstoff werden mehrere Ex-e-Gehäuselösungen von Pepperl+Fuchs für die Signalverteilung und den Anschluss der notwendigen Temperatursensoren eingesetzt.
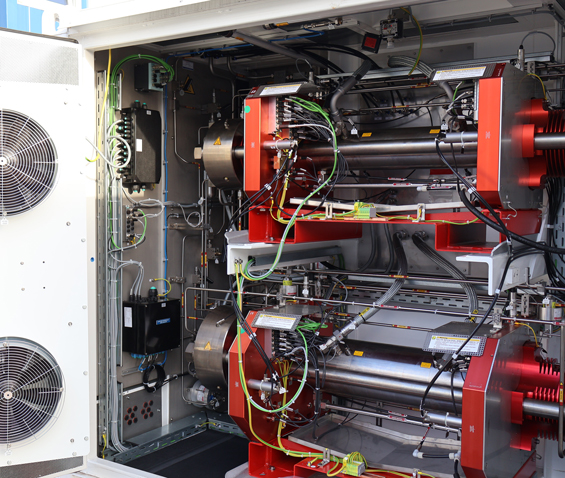
Auch die Klemmenkästen benötigen ein sicheres Gehäuse. Diese können individuell bestückt werden.
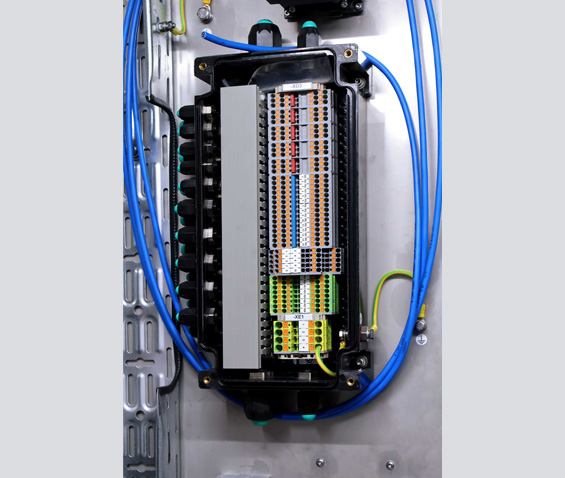
Eine weitere Ex-e-Gehäuselösung schützt die elektronischen Komponenten und sorgt für die sichere Signalverarbeitung bei der Verdichtung des Wasserstoffs.
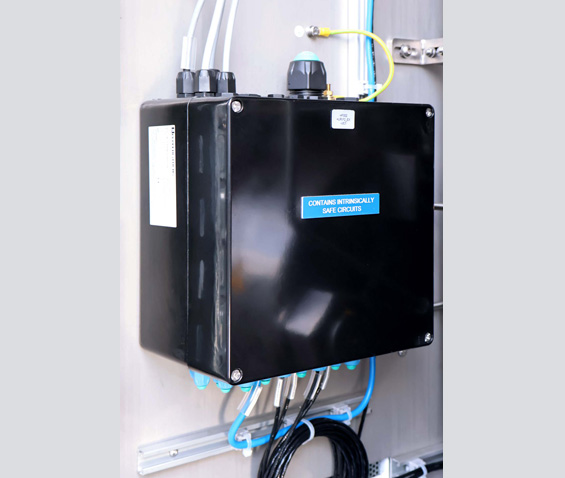
Für die sichere Steuerung des Umfüllprozesses an den Modulen zur Annahme und Abgabe von Wasserstoff von und an Trailer sorgt ein explosionsgeschütztes Edelstahlgehäuse mit integriertem Monitor und Schaltelementen wie Not-Halt-Taster.
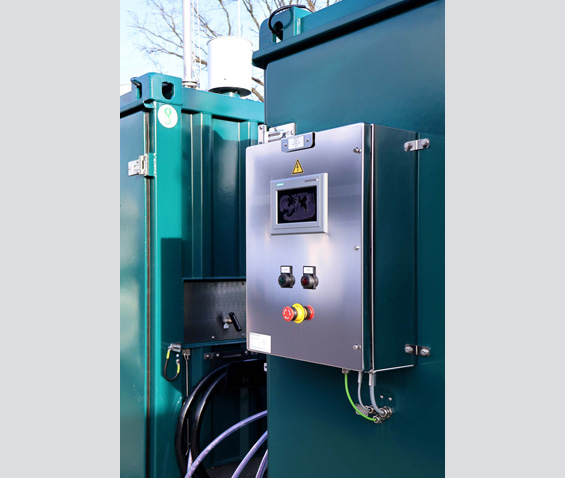
Der Anschlussschrank ist die Schnittstelle zur Versorgung der Gasbefüllstation mit Wasserstoff aus einem Trailer. Das Ex-e-Gehäuse von Pepperl+Fuchs schützt die Steuerungskomponenten der Anlage.
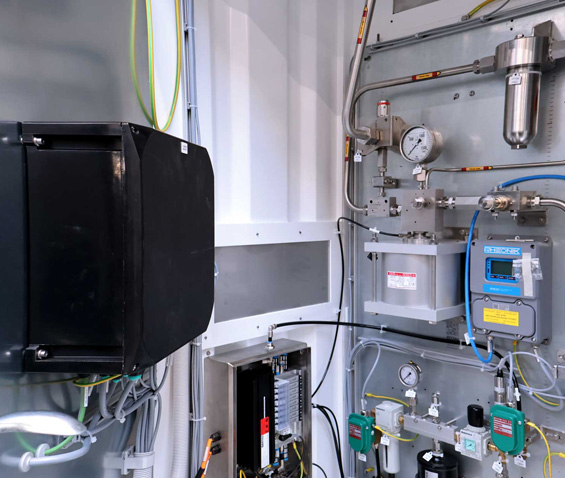
Entwicklung, Herstellung und Zertifizierung aus einer Hand
„Wir haben es zunächst mit einem anderen Anbieter versucht, aber bei der Zusammenarbeit hat es ziemlich geholpert“, erinnert sich Urban. „Dann haben wir uns an Pepperl+Fuchs gewandt – das Unternehmen war uns als Spezialist für Explosionsschutz natürlich bekannt. Und diesmal lief alles sehr reibungslos und lösungsorientiert ab.“ Dazu trug auch die Expertise des firmeneigenen Solution Engineering Center (SEC) in Bühl bei, auf die der Vertrieb von Pepperl+Fuchs zurückgreifen kann, wenn Standardkomponenten in bestimmten Anwendungen nicht ausreichen. Weltweit verfügt Pepperl+Fuchs über sechs SEC, die darauf spezialisiert sind, maßgeschneiderte Lösungen für explosionsgefährdete Bereiche zu entwickeln. Neben der Planung der perfekten Lösung und dem Engineering, überwacht es den gesamten Fertigungs- und Zertifizierungsprozess.
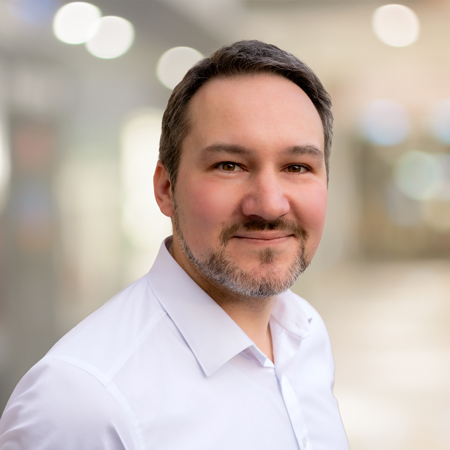
„
Wir bieten unseren Kunden maßgeschneiderte modulare und für sie standardisierte Engineering-Lösungen, die genau zu ihren Anwendungen passen.
„Bei Maximator Hydrogen war nicht nur technische Flexibilität gefragt, sondern auch Flexibilität hinsichtlich der Zertifizierungen und Normungen. Wir bieten unseren Kunden maßgeschneiderte modulare und für sie standardisierte Engineering-Lösungen, die genau zu ihren Anwendungen passen und in deren Anlagen weltweit verwendet werden können, mit allen Spezifikationen“, erklärt Mike Karcher, Leiter der Order Management Unit im SEC in Bühl. „Die Standardisierung der Lösung ist dabei der entscheidende Punkt, denn das bedeutet auch eine erhebliche Kostenersparnis für den Kunden“, führt Mike Karcher weiter aus.
Normenexperten von Pepperl+Fuchs sind dabei von Anfang bis Ende involviert. Sie prüfen die Fertigungszeichnung, das Angebotsengineering und anschließend die fertigen Lösungen, damit diese mit der entsprechenden Konformitätserklärung und der vorgeschriebenen Zertifizierung ausgeliefert werden können. Der Kunde erhält am Ende ein 100 % zertifiziertes Produkt.
Kooperative Entwicklung
Für die reibungslose Zusammenarbeit ist der Beitrag aller Seiten wichtig, betont Ernst: „Je früher wir in die Entwicklung der Anlage eingebunden sind, desto leichter und schneller finden wir die optimale Lösung. Unsere Ansprechpartner bei Maximator Hydrogen haben uns von Anfang an bei der Planung hinzugezogen. Unser erstes gemeinsames Projekt beinhaltete gleich mehrere solcher Lösungen und war bereits nach knapp einem Jahr abgeschlossen – inklusive Orientierungsphase und pandemiebedingter Verzögerungen. Bei der nächsten Anlagengeneration dauerte es nur noch gut drei Monate, bis die maßgeschneiderten Gehäuselösungen entwickelt, produziert und zertifiziert waren.“ Insgesamt sind in einer Anlagengeneration fünf bis zehn Lösungen von Pepperl+Fuchs im Einsatz. Einmal entwickelt, kann Maximator Hydrogen diese immer wieder nach Bedarf bestellen, genau wie ein Standardprodukt. „Die Zusammenarbeit mit Maximator Hydrogen ist absolut auf Augenhöhe und es macht Spaß, gemeinsam die passenden Lösungen für ihre Anlagen zu entwickeln“, berichtet Ernst.
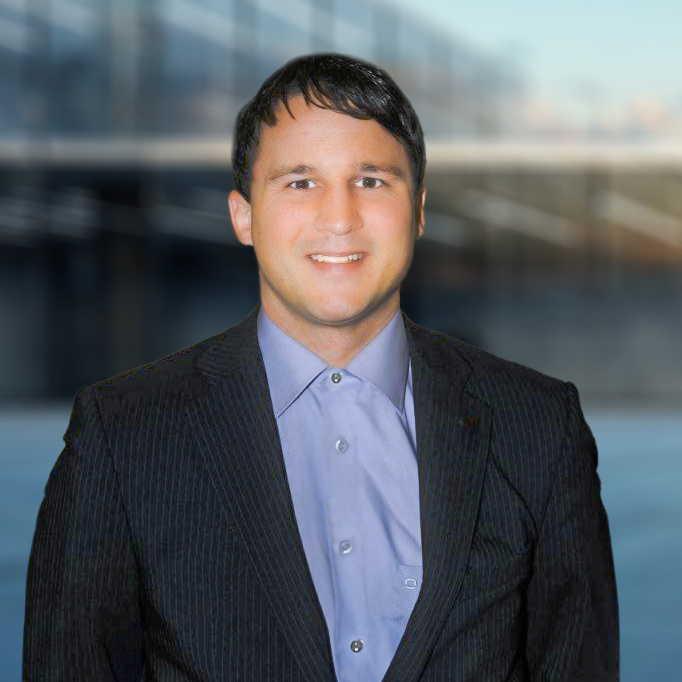
„
Je früher wir in die Entwicklung der Anlage eingebunden sind, desto leichter und schneller finden wir die optimale Lösung.
Qualität und Dokumentation überzeugen
Neben der guten Zusammenarbeit loben die Ingenieure von Maximator Hydrogen das hohe Qualitätslevel der Produkte von Pepperl+Fuchs sowie den kompetenten Umgang mit allen Fragen des Explosionsschutzes. „Das gilt nicht zuletzt auch für die Dokumentation, die im Ex-Bereich besonders wichtig ist“, unterstreicht Marcel Urban. „Wir haben unbeschränkten Zugriff auf alle Details, was bei anderen Anbietern keineswegs eine Selbstverständlichkeit ist. Insgesamt haben wir eine sehr produktive und erfolgreiche Partnerschaft, eine echte Win-Win-Situation. Derzeit arbeiten wir gemeinsam an weiteren Lösungen für die neue Anlagengeneration, um den dynamisch wachsenden Wasserstoffmarkt bedienen zu können.“