November 13, 2017
Perfect Positioning
From bird's–eye view, the hustle and bustle in a container port is reminiscent of Where's Waldo: in wind and rain, day and night, transport containers are removed and stacked, loaded and unloaded, shipped and sent on their way. Compared to the containers, the WCS position encoding system from Pepperl+Fuchs is minuscule—but for smooth processes, it is of great importance.
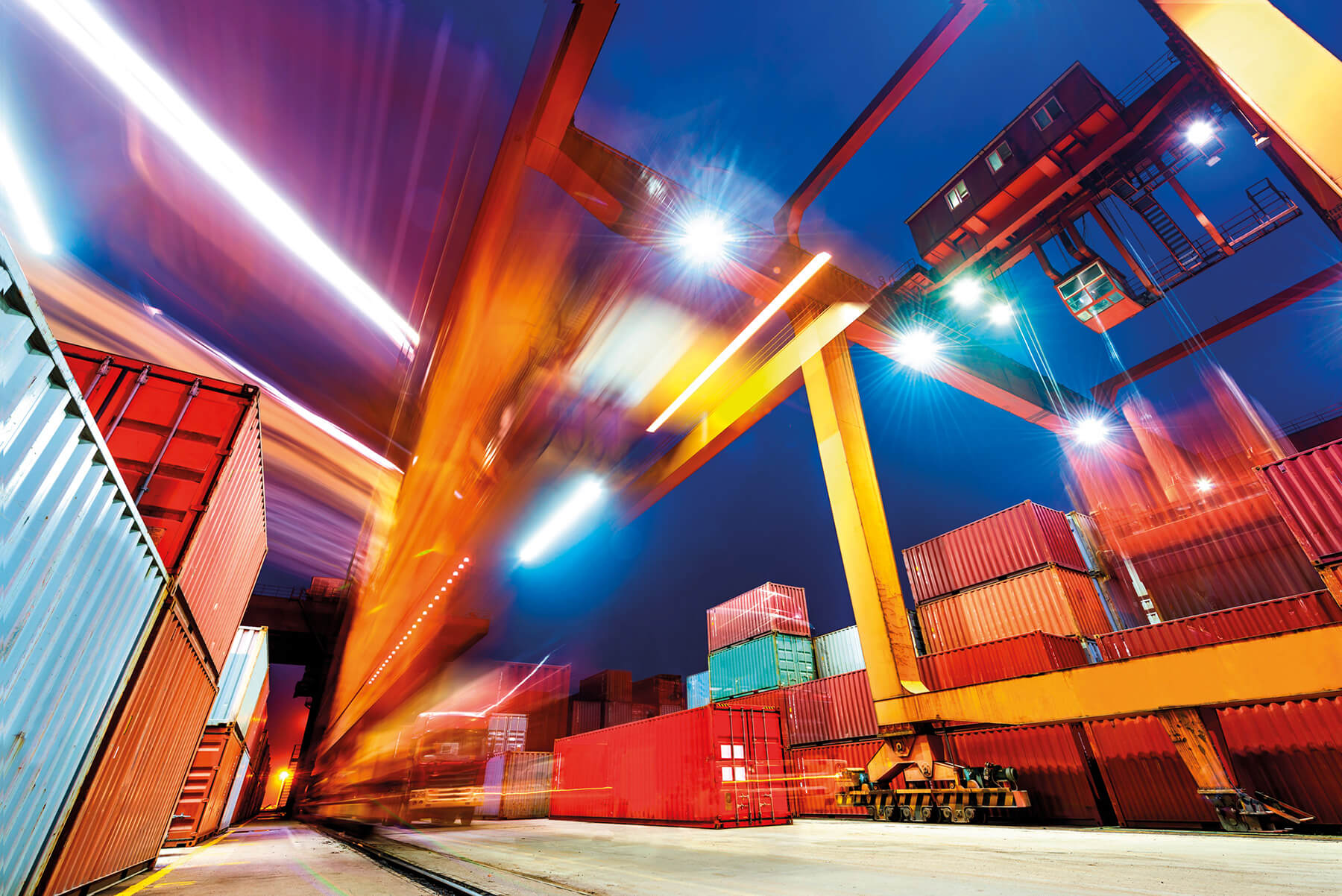
In 2015, over 36 million standard containers were handled in Shanghai, the largest port in the world—that's more than one container per second! In order to cope with such a fast pace, all processes must run smoothly. As soon as an oceanliner docks with up to 20,000 containers on board, the unloading cranes move into position at the quay on rails. They are also true giants: at over 50 meters high, their boom must span the waterside of the large ships, in order to be able to remove the last transport containers from the rearmost corner of the loading area. The cargo ship has barely moored when the container bridges begin their work. One container after another is packed by the gripper, hefted, moved to the landside while suspended and then set down there. Usually, it takes less than a minute until a pallet truck arrives, loads this container, and transports it to the loading area of a mobile portal crane. These so-called "gantry cranes" are smaller than the container bridges, but still big enough to make a 40-foot container look like a shoe box. As "rubber-tired gantry cranes" (RTG) they move back and forth on large rubber tires or on rails.
The Gateway to World Trade
In the work area of such an RTG, which looks like a gigantic gate, up to six containers can be densely stacked on top of each other and side by side in up to 14 rows. This is done quickly and to save space, because space and time are a rare commodity in the harbor, even more so when the vessel is larger. In modern major ports, processes controlled by people are already largely optimized. Further efficiency requires a higher degree of automation—a perfect scenario for solutions from Pepperl+Fuchs.
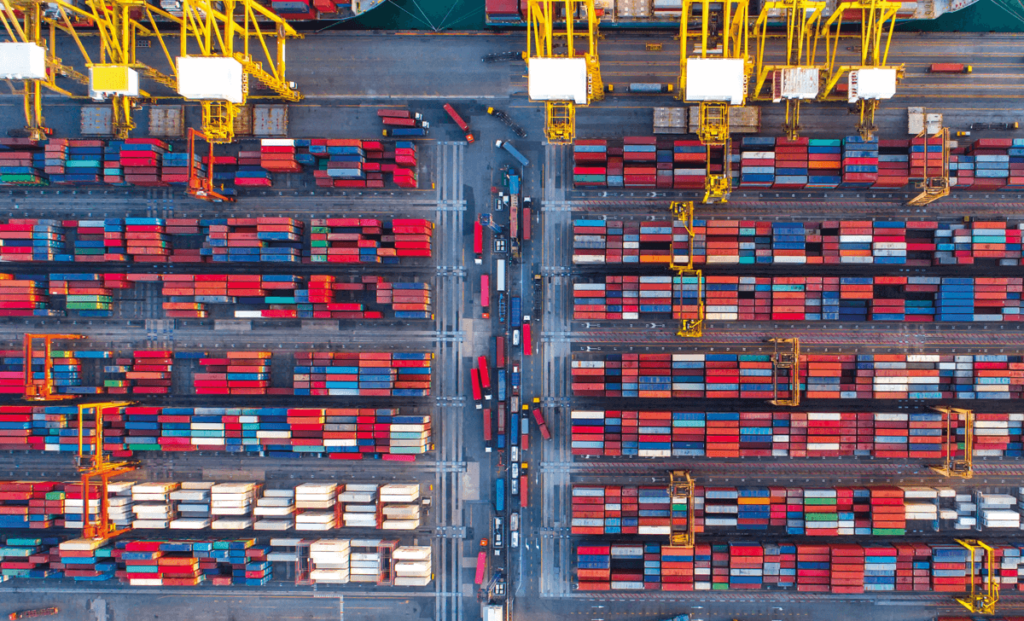
Crucial Position Determination
The gantry crane, for example, can be operated automatically. "The crucial prerequisite for this is that the crane recognizes its exact location at any time," explains Armin Hornberger, Head of Product Management for Industrial Vision Components at Pepperl+Fuchs. "Maximum precision really counts. The containers should be stacked as closely as possible; larger measuring tolerances add up to significant deviations across long stretches. The new version of our WCS position encoding system optimized for outdoor use offers ideal sensors that are accurate down to the millimeter for position detection of gantry cranes."
The new WCS consists of a pollution-resistant coding rail, made of stainless steel for outdoor use, and U-shaped thru-beam sensors with powerful infrared LEDs. The rail is mounted on the side of the path of the gantry crane, and the WCS reader is on the crane itself. The infrared light of the sensor falls through the slots in the rail, the reader collects the resulting code pattern and converts it into an absolute position specification with an accuracy of ±0.4 mm. Even at high speeds, the WCS works reliably in real time and over distances of up to 314 meters.
From Arctic Port to Tropical Heat
Detection is a noncontact process, the infrared spectral range excludes all ambient light irritation, and temperature fluctuations do not play a role. The major innovation in this version of the WCS is the double housing of the reader. "We have designed the system for use outdoors by providing it with an additional housing made of a highly stable, special plastic, which can also handle strong mechanical effects such as impacts and shocks or heavy hail," says Hornberger. The sensor corresponds to IP69 degree of protection, is heat-resistant, water-resistant, and dust-tight. It tolerates steam-jet cleaning, and resists even aggressive substances such as saltwater, acids, and alkalis. It is almost completely insensitive to weather influences. Thanks to the built-in heater, which is automatically engaged at low temperatures, temperatures down to -40 °C are possible. "This makes this device ideal for ports all over the world, from the Arctic to the hottest regions—and also for other applications under harsh conditions, such as in electroplating plants, in the chemical industry, or waste incineration," explains Hornberger.
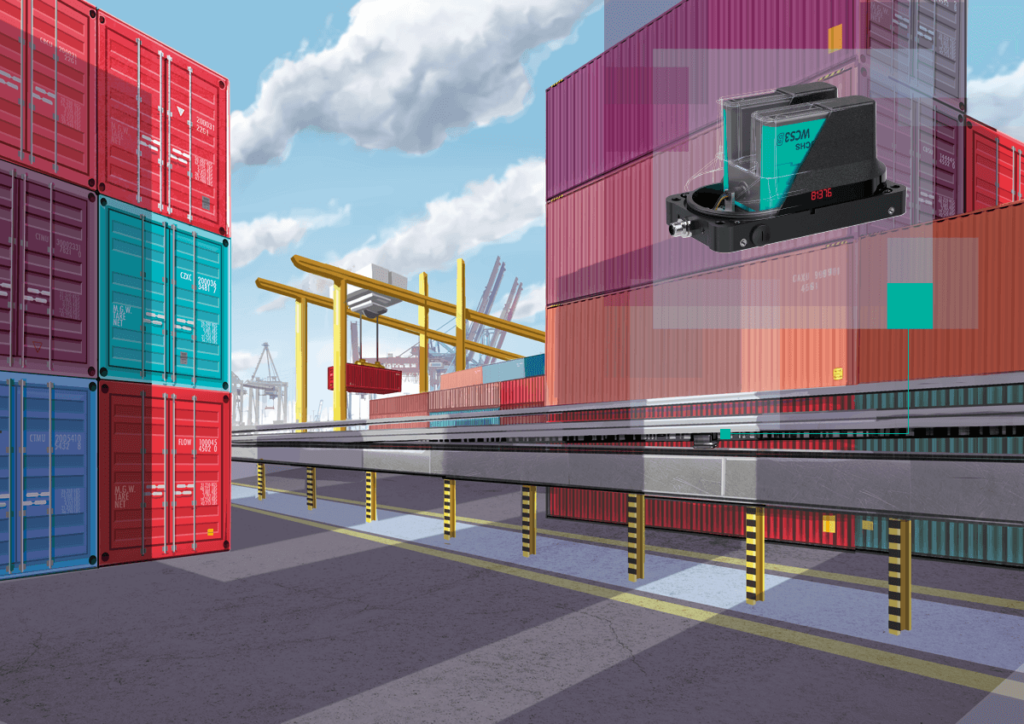
A Classic Revisited
Flexible connection options allow installation even in cramped conditions. The low total width of the system also saves valuable space. At the same time, the outdoor version of the WCS is compatible with all previous WCS components and can be connected with each control panel to which data is sent via a serial RS-485 or SSI interface. A wide range of interface modules are available for connection to bus systems. "The WCS came on the market in 1989 as the first absolute positioning system in the world. Since then, it has proved itself in numerous applications in intralogistics as well as in elevator technology, and in the automotive industry. The new outdoor version now lays the foundation to completely automate the operation of a gantry crane or similar large devices with long travel paths—even if salty sea air and spray challenge the WCS," stresses Hornberger.