December 4, 2019
Digital Approaches to Hydraulics
To make the processes in hydraulic applications even leaner, more transparent, and more energy-efficient, the Austrian company LCM GmbH, a Pepperl+Fuchs Group partner company, has developed a sophisticated digital hydraulic system.
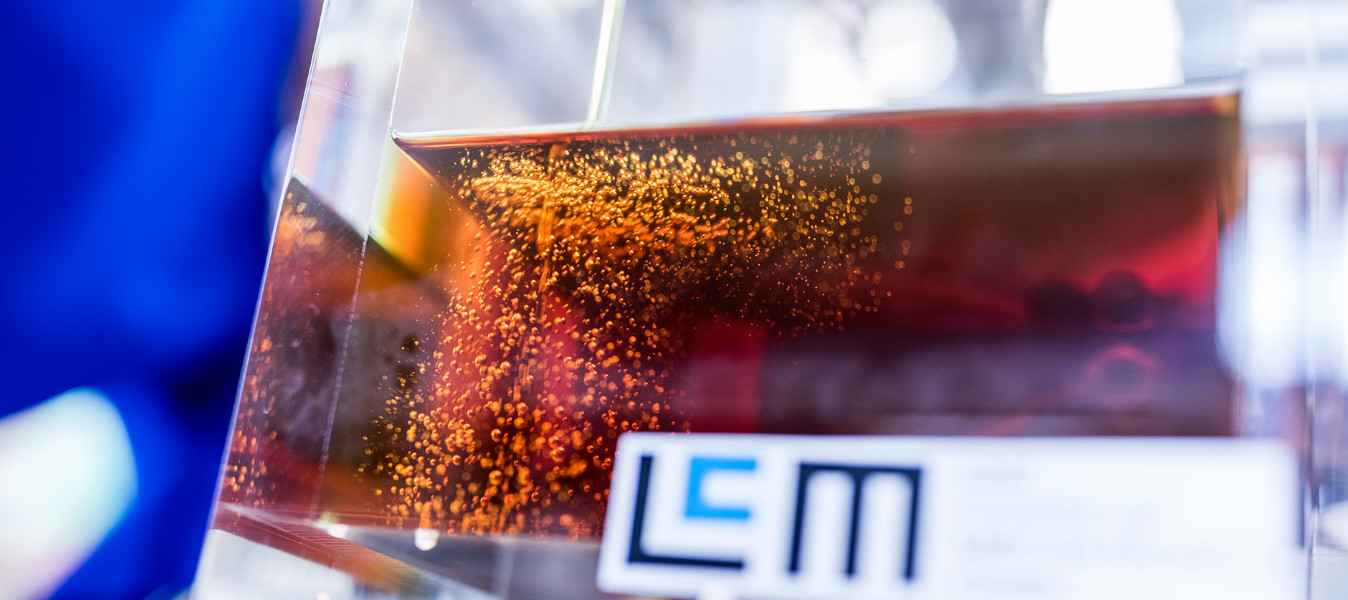
Since as early as the 18th century, humans have understood and made use of hydraulics to move large loads while exerting as little force as possible. 'In its simplest form, the same principle can be seen at work on a bicycle during the braking process,' explains Dr. Bernd Winkler, Business Area Manager Drives at LCM. 'A small cylinder on the brake lever is connected to a large cylinder on the brakes themselves, with hydraulic oil located between the two. Relatively little force must be applied to the small piston to be able to generate the required braking force with the large piston. The force the rider exerts on the brake lever using just one finger is sufficient to bring the bicycle to a stop, even on a steep hill.' In addition to bicycles, hydraulics can be used in many other application areas, including everything from construction machinery and motor vehicles to large industrial presses.
Hydraulic presses are essential for companies such as automotive suppliers, who use them to manufacture plain bearings and brake pads. These presses take up a lot of room in the production area and consume a considerable amount of energy. The energy consumption of a single hydraulic press can cost manufacturers several thousand euros per year. A significant amount of this energy is used during the static pressing of sintered components. In addition, areas where movement takes place under high loads are subject to excessive wear; these include hydraulic components, the pump, and the oil itself—the medium that is used to transfer the force.
LCM GmbH, which is based in Linz, Austria, has developed a system that can help solve exactly this type of problem. The company has combined this system with smart sensor technology and the corresponding infrastructure from Pepperl+Fuchs to create a digital hydraulic approach that allows large presses to be modernized and optimized using efficient components.
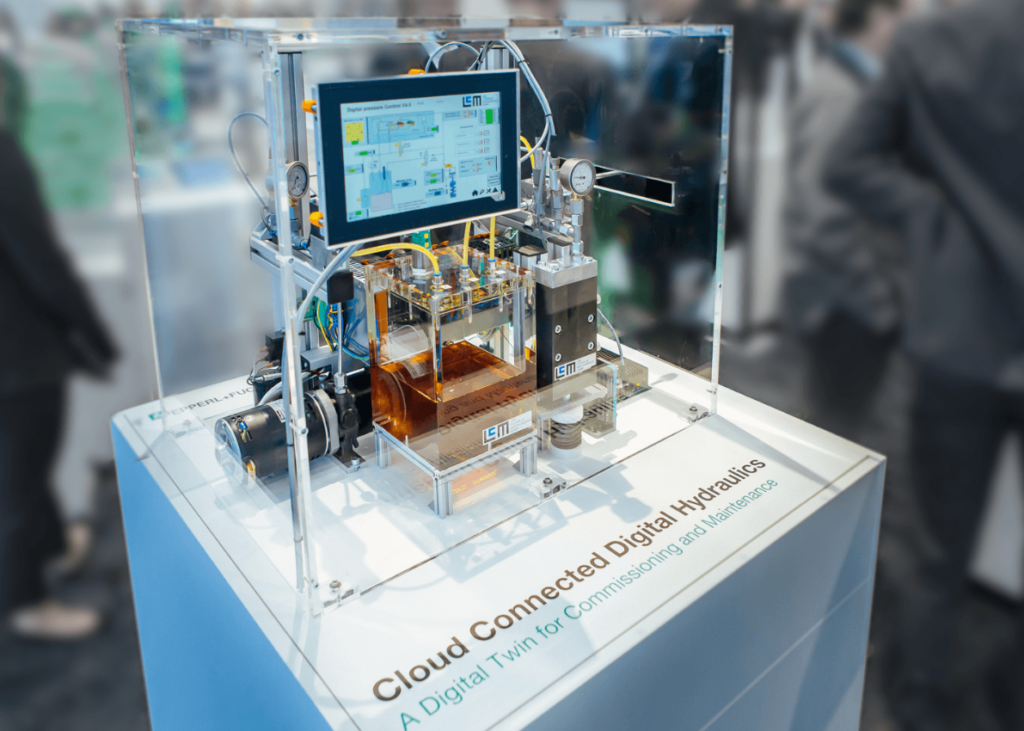
Efficient Components Create Total Transparency
What makes a 'conventional' press different from one equipped with digital hydraulics? Dr. Winkler explains: 'In comparison to conventional controllers, such as proportional and servo valves, the seat design of digital valves prevents internal leaks—this results in improved efficiency and makes them significantly more resistant to oil impurities." This type of digital valve can be used in a wide range of applications within hydraulic drive technology. 'For this reason, we at LCM have developed a digital hydraulic system with simple switch valves that, in combination with sensor technology and infrastructure from Pepperl+Fuchs, is able to regulate both position and pressure quickly and precisely—at a very reasonable cost and with low energy consumption.' This functionality is especially useful in applications where presses must maintain a specific pressure for several minutes to guarantee that the pressed parts are of consistent quality.
'To achieve this, the system switches from conventional operation to digital hydraulic operation, for which it is supplied by a gas-filled hydraulic accumulator,' explains Winkler. Ideally, the pump should not run at all during the four-minute holding phase, using almost no energy. Repeatable control of the switch valves during ballistics operation is vital for ensuring control accuracy within a tenth of a bar.
By precisely controlling the switch valves so the valve piston only performs a partial stroke, only the smallest quantities of oil are fed into the hydraulic cylinder. 'The oil tank itself is equipped with an intelligent ultrasonic sensor from Pepperl+Fuchs that continuously monitors the fill level of the tank and transfers the data to the higher-level control system via IO-Link,' adds Thomas Brezina, General Manager at Pepperl+Fuchs in Austria. 'At the same time, the PMI F90 distance measurement system from Pepperl+Fuchs reliably determines the position of the working cylinder, enabling continuous dosing of the oil,' he adds.
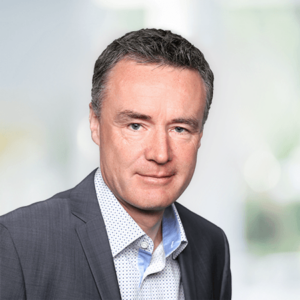
"Based on this position feedback, the valves are able to maintain the pressure to within a tenth of a bar and the position with µm accuracy. This is a significant milestone for us and our customers, who can use this technology to achieve more precise sintering results and cut costs," Winkler is proud to report.
'Data Highway' to the Cloud
However, meaningful condition monitoring is only possible if the infrastructure enables quick data exchange. 'A key part of this 'highway' that takes data straight to the cloud is the ICE3 series (PROFINET) IO-Link master from Pepperl+Fuchs,' explains Brezina. In addition to offering real-time communication via PROFINET, it is also the world's first IO-Link master equipped with an OPC UA interface—the most popular open standard for data exchange in Industry 4.0 applications. The BTC edge gateway uses this method to communicate with the IO-Link master and transfer the data to a cloud platform. There, the sensor information can be visualized on dashboards, which can be accessed from anywhere in the world, even on mobile devices. This data can also be used for applications such as asset management, condition monitoring, and predictive maintenance.
Parallel, fault-free communication via OPC UA and Ethernet-based fieldbus protocols opens up the possibility of implementing hybrid systems, Brezina confirms: "A control system coordinates all of the time-sensitive applications and processes, while less-time-sensitive aggregated status data is transferred to the cloud." MultiLink™ technology enables users to access the device simultaneously from the control system and the cloud.
"Thanks to this intelligent interaction, we have been able to close existing data gaps and transfer sensor data directly to the cloud," adds Winkler. The two companies have established a successful partnership, as can be seen from their fruitful collaboration with the panel-bending machine manufacturer Salvagnini.
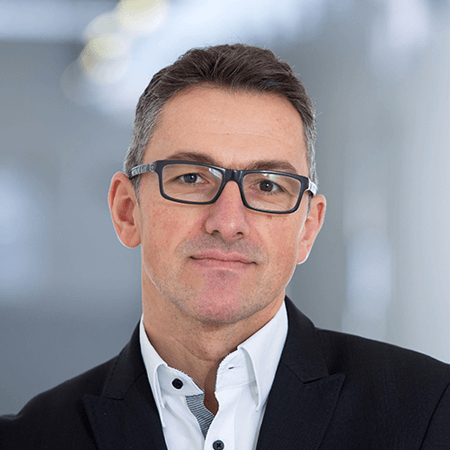
The master simultaneously transfers the data obtained by the ultrasonic sensor and the positioning system straight to the programmable logic controller and the cloud. "If a previously defined position or limit value is exceeded, oil is discharged, and vice versa," says Brezina, describing the process that takes place inside the machine. This adjustment, also known as an incremental increase, is carried out until the pressure is stable again. During this time, the positioning system transmits the current position of the working cylinder to the IO-Link master. MultiLink™ technology enables the system to transfer the sensor data at the same time via two different methods. In line with the seamless connectivity concept, data can be simultaneously transferred to the control system via PROFINET and to the cloud via OPC UA. "For example, this could be a custom cloud solution from Neoception, the Pepperl+Fuchs start-up for industrial IoT services," adds Brezina. An additional intermediate edge gateway—like the BTC from Pepperl+Fuchs—adapts the data for the cloud interface and ensures that the data transfer is secure. The result is an interconnected concept for data generation and processing. "Employees can use their smartphones or tablets to obtain an overview of the fill level in the oil tank and the position of the press at any time, thus visualizing the plant status," adds Brezina.
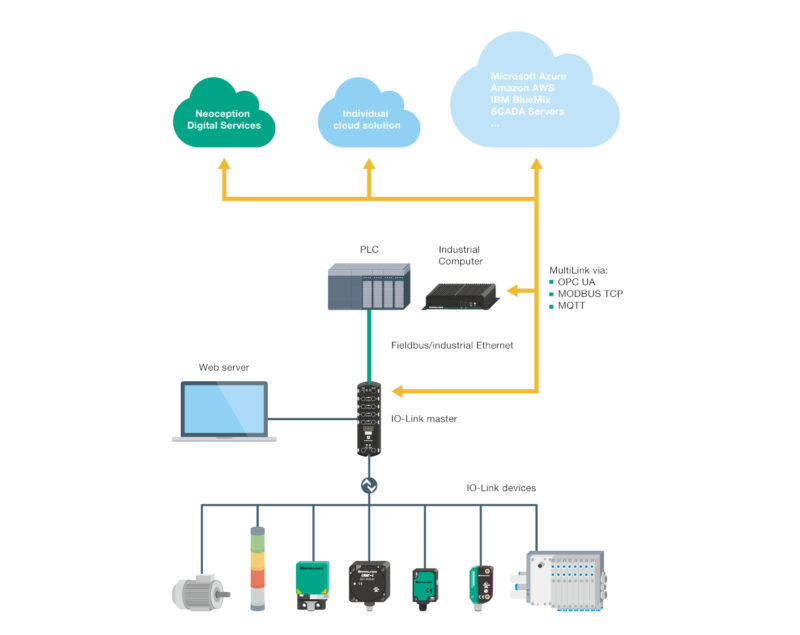
Cloud connectivity solutions from Pepperl+Fuchs
"Using the data generated and the connection to the higher-level system, we were able to close an important gap and combine our skills in a targeted manner," emphasizes Winkler. "Whether Pepperl+Fuchs sensor technology is already integrated into the plant or needs to be added as a retrofit solution, the advantages for users are clear: Digital valves can considerably increase reliability and reduce energy consumption, and have therefore raised the bar for the hydraulic plant field."
Seamless Communication at Every Level
The new ICE2 (EtherNet/IP) and ICE3 (PROFINET) IO-Link master series offer more than just a fieldbus protocol with real-time communication. They also have an OPC UA interface, which makes them ideal for cloud-based connections. The web-based configuration concept can be implemented without additional software, streamlining commissioning and making the IO-Link masters an optimal solution for stand-alone applications without a higher-level control system.