April 4, 2023
To the Laboratory: State-of-the-Art Industrial Pneumatic Tube Systems
In applications such as the chemicals industry, steel works, and cement works, every production lot has to be analyzed. State-of-the-art industrial pneumatic tube systems from QCS Rohrpost GmbH in Remscheid, Germany ensure that sampling in the laboratory takes place as quickly as possible. To ensure that the samples can be clearly assigned and tracked, QCS Rohrpost uses RFID sensors from Pepperl+Fuchs.
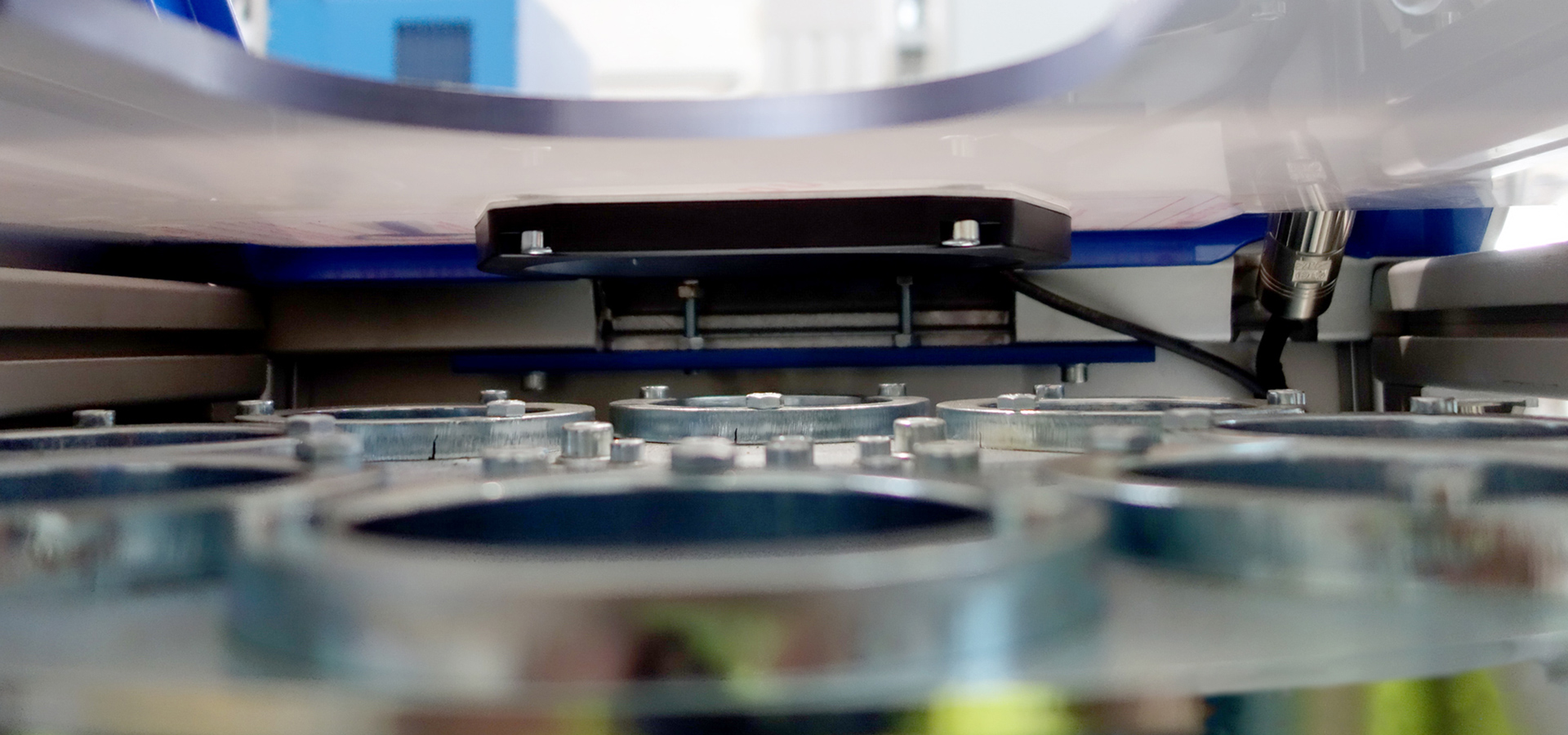
When you hear the word 'pneumatic tube' you think of times gone by, when information was mainly passed from the sender to the addressee in paper form. In fact, the first functioning pneumatic tube system was put into operation at the London Telegraph Office in 1853. Until late into the 20th century, the pneumatic tube was a widely used means of sending letters, files, or proofs back and forth within large post offices, printing houses, and corporate headquarters. This era came to an end with the advent of digitalization. But there are also areas of application for which the pneumatic tube is still the quickest and safest means of transport, for example: sample analysis in industrial production processes, time-critical laboratory analyzes in hospitals, or safe money removal at toll stations.
Industrial Pneumatic Tube Systems: A Modern Solution Instead of Old Technology
Unlike information, material samples cannot be sent electronically. Samples from production processes—whether in the production of special steels or chemical products—continue to require physical transport. 'In central processes in the chemical, steel, and cement industries, samples must be taken several times a day so that their composition can be analyzed. Production cannot continue until the laboratory reports the results. A modern pneumatic tube system can significantly contribute to reducing costs, increasing efficiency, and reducing CO2 emissions,' says Heinz Sepke, Founder and Managing Director of QCS Rohrpost GmbH.
As different as the materials and processes are, each of these industries has the same starting point: A mixture of different components should be fed to the next processing step. Before this transfer, it is necessary to know the exact composition of the material, and to be able to correct it if necessary. For this purpose, a sample is sent from the furnace or converter to the in-house laboratory, which can be several kilometers away on a large plant site. In terms of speed and reliability, no other means of transport can keep up with the pneumatic tube.
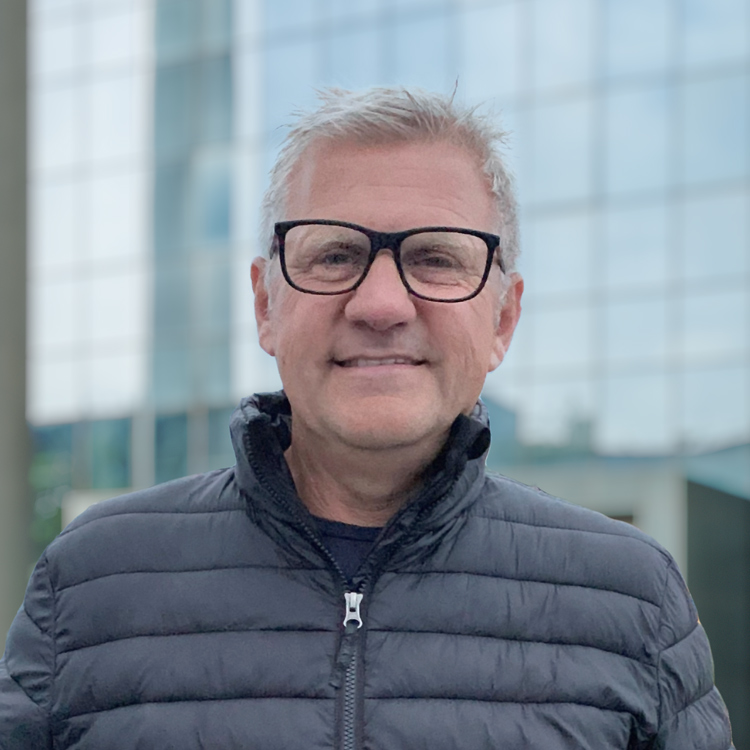
Speed Is Essential
In a steelworks, for example, liquid metal is bubbling at about 1500 °C in a melting pot that holds several tons. It will later conform to a precisely defined standard for a specific steel grade, such as stainless steel or aluminum. These standards define exactly what carbon content is permissible and the composition of the iron alloy. When the steel is in a liquid state, any deviations from the desired result can still be corrected. Before they drain the crucible contents and transfer them to the rolling line, the steel boilers therefore use a lance to draw a sample from the melt and send it to the in-house laboratory.
There, a layer is milled from the cooled metal piece and the composition of the material is precisely determined using spectroscopy. 'During sample analysis, the furnace needs to be heated further to keep the metal in a liquid state, which requires considerable energy input. Especially with rising energy costs, speed is essential. And of course, the crucible cannot be refilled while the analysis is ongoing. The time and cost factor plays a significant role here,' explains Heinz Sepke.
Save Time, Energy, and Costs
'Literally every minute counts,' says Sepke. 'The sooner the results from the sample analysis are available, the quicker production can continue, and the lower the energy consumption and CO2 emissions.' Collecting the sample by courier, driving across a vast site, and personally delivering it to the laboratory can sometimes take quite a long time. By contrast, a pneumatic tube carrier can reach speeds of 20 to 40 meters per second, and the sample lands directly in the laboratory's sampling station. 'For our customers in the steel industry, for example, up to 2000 samples a day are examined in one plant alone. It is therefore easy to imagine the savings in time, energy consumption, CO2 emissions, and the associated costs that are achieved by using a pneumatic tube system. The system also increases efficiency throughout the entire process. The installation of such a modern industrial pneumatic tube system quickly pays for itself,' explains Heinz Sepke.
The function principle of the pneumatic tube has not changed since its inception in the 19th century: A cylindrical container is sent from a transmitting station to a receiving station using pressure and suction. In QCS Rohrpost systems, the carriers are usually transported to the sample station in the laboratory at a pressure of 0.1 millibar, and back to the sampling station via vacuum suction. However, modern industrial pneumatic tube carriers are in no way comparable to those previously used in offices. 'These are high-tech carriers made of special aluminum. They are extremely light and can therefore travel even more quickly through the pneumatic tube system,' emphasizes Heinz Sepke.
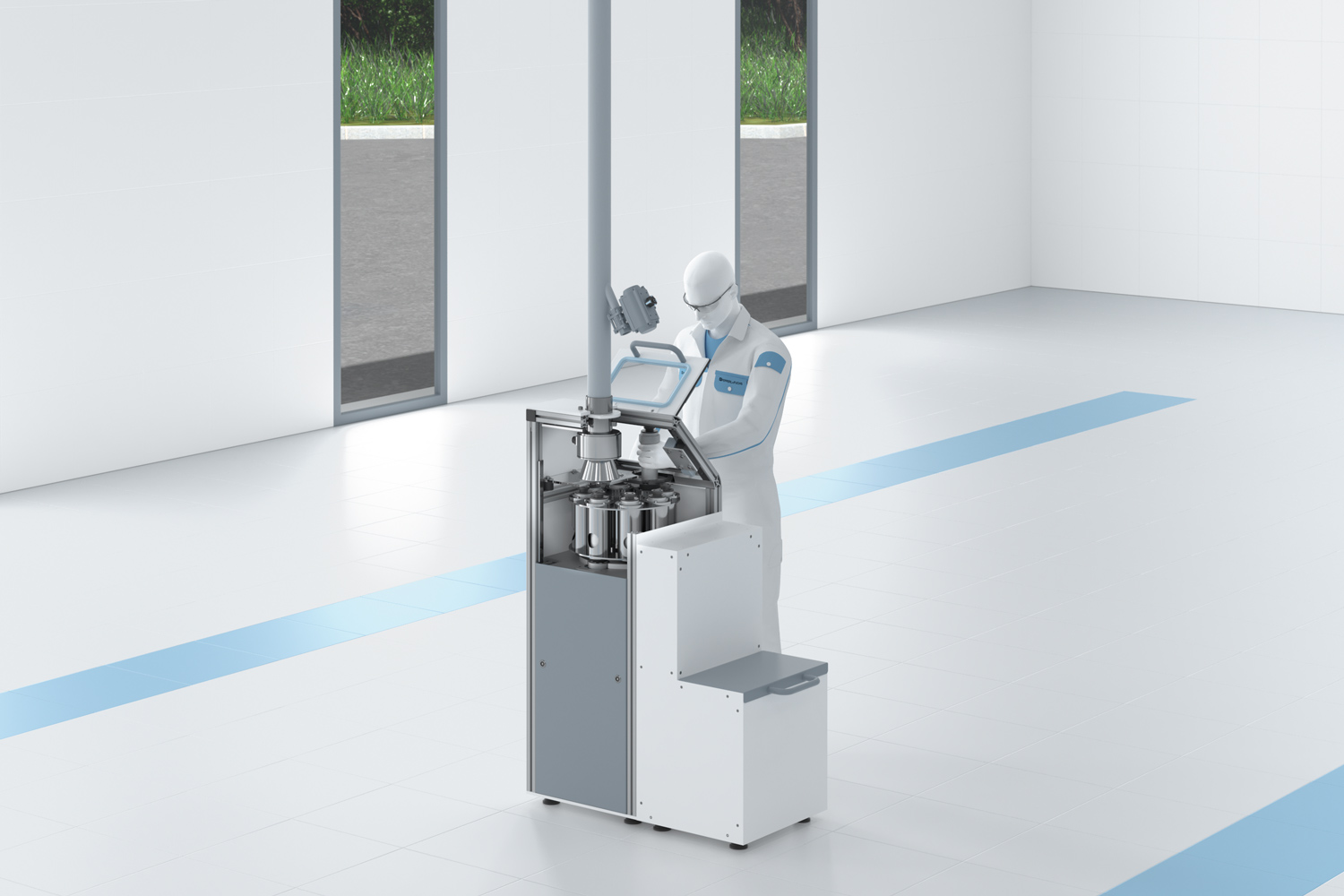
In the steel or chemical industry, several thousand samples are examined every day in one plant alone. With a pneumatic tube system, the samples are sent directly to the in-house laboratory at a speed of up to 40 m/s and their composition can be analyzed.
Reliable Identification Using RFID
To automate sample handling and ensure quick and reliable processes, QCS Rohrpost uses RFID sensors from Pepperl+Fuchs. 'Up to eight samples can arrive at a multiple receiving station at the same time. In some laboratories, there are up to 12 such receiving stations and several dozen operating stations within the plant,' says Sepke, describing common practices. Therefore, clear allocation and prioritization of the samples is essential. RFID is the optimal solution for this purpose. 'Unambiguous and reliable identification forms the basis for automating and ensuring traceability in the processes involved in sample analysis,' says Heinz Sepke.
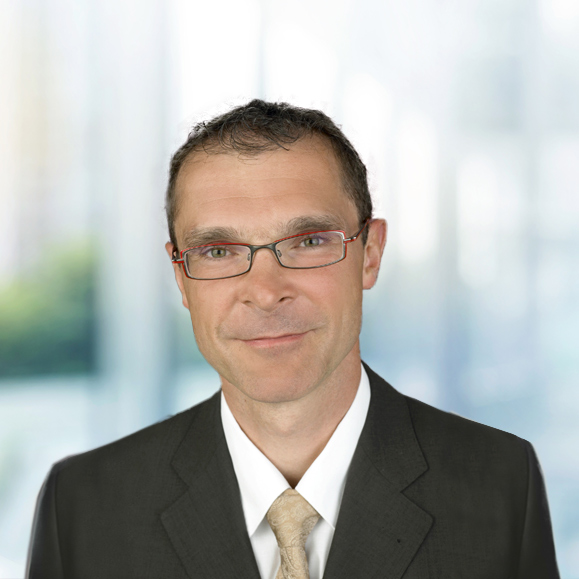
"The sample is sent to a receiving station in the laboratory. A round IQC21-16 RFID tag is embedded in the head of each carrier. This contains all the required data for the sample. When the tag arrives at a multiple receiving station in the laboratory, it is read out by an IQH1-F198-M-V1 ring-shaped RF read/write device, which is integrated into a turntable ("revolver".) The controller records the lot from which the sample originates and assigns a sample ID to the consignment. The laboratory therefore also knows with which priority it should be analyzed," explains Stefan Hillenhinrichs, Sales Engineer at Pepperl+Fuchs, explaining the process. The ring-shaped and especially flat design of the IQH1-F198 RFID read/write device enables optimal and space-saving integration into the receiving station.
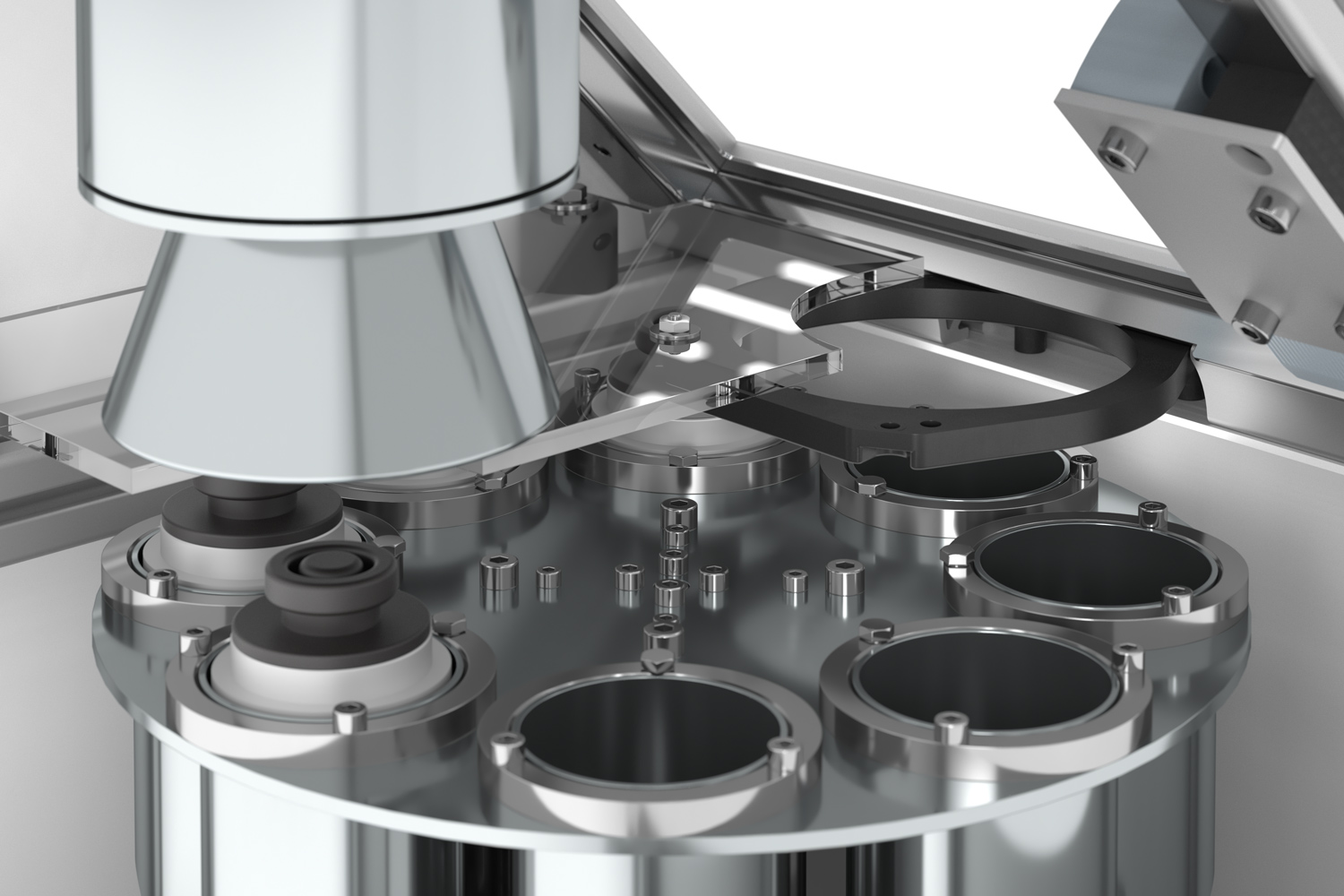
Insight into the interior of the pneumatic tube station: The ring-shaped F198 HF RFID read/write device, which is ideally integrated into the station, reads the data stored on the transponder of the pneumatic tube carrier and reliably identifies each individual sample.
To the Lab: At 150 km/h and Using Smart Sensor Technology
For multiple transmitting and receiving stations and various transport lines, a sophisticated system of turnouts and transfer stations ensures that each carrier finds the right path. 'Steelworks or large chemical plants can have 20 km of pipelines,' reports Heinz Sepke.
Before the carrier lands in the receiving station, however, it must be braked by reducing the compressor power for the respective pipe. QCS therefore mounts an NRB15 series inductive sensor with IO-Link interface from Pepperl+Fuchs at a certain distance in front of the receiving station. This detects the approaching carrier and sends the brake signal to the controller. 'A carrier with sample contents can weigh up to 2 kg. On its way to the sample station, it reaches a speed of about 150 km/h—without braking, it would be a dangerous bullet,' explains Heinz Sepke. In systems that cover long distances, OBT300-R103 diffuse mode sensors with an IO-Link interface are also installed. They detect that a carrier has passed a certain waypoint. The smart IO-Link sensors therefore provide important data on the functionality and status of the system. If a carrier gets stuck, it is easy to determine the area of the system in which the carrier is located. This saves time and effort during servicing—especially with a current lack of service personnel—and any delays in the production process are avoided.
Pneumatic Tube 4.0: Digital Data Acquisition
Managing Director Heinz Sepke and his son Mario Sepke, Business Development Manager, are working on setting up the pneumatic tube system with digital data acquisition in accordance with Industry 4.0 so that it is future-proof. Together with the Pepperl+Fuchs subsidiary Neoception, they are currently developing an app that combines all sensor data from the various plant areas of their systems and provides a comprehensive overview of each carrier, including the sample content and processing status. 'In the future, the app should digitally record every movement in our stations and systems and give plant operators a comprehensive overview of the processes,' explains Mario Sepke. 'To do this, we need smart sensors and the expertise to integrate the data. With Pepperl+Fuchs and Neoception, we have two very strong partners in this regard. We are working very closely together to further develop and digitalize our pneumatic tube systems, which creates great synergy effects for both sides,' says Mario Sepke.
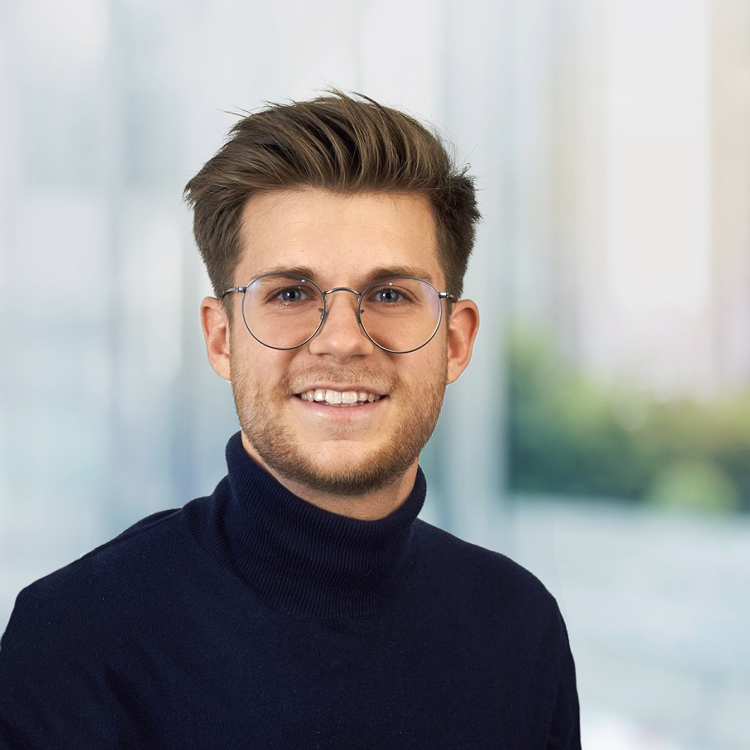
The Sepkes are taking further steps in terms of sustainability and recycling: They are working on how to recover and process the raw materials from the samples to avoid production waste. "With thousands of samples a day, this is also a significant cost factor and offers great savings potential for our customers," adds Mario Sepke