Hydrogen March! Get There with the Right Infrastructure
March 27, 2024
Green hydrogen is set to close the gap in emission-free mobility. In addition to the charging infrastructure, a large-scale network of hydrogen filling stations is needed to ensure that the transformation of transportation also succeeds in heavy goods transport. In collaboration with Maximator Hydrogen, Pepperl+Fuchs has developed explosionproof solutions for the safe operation of such systems.
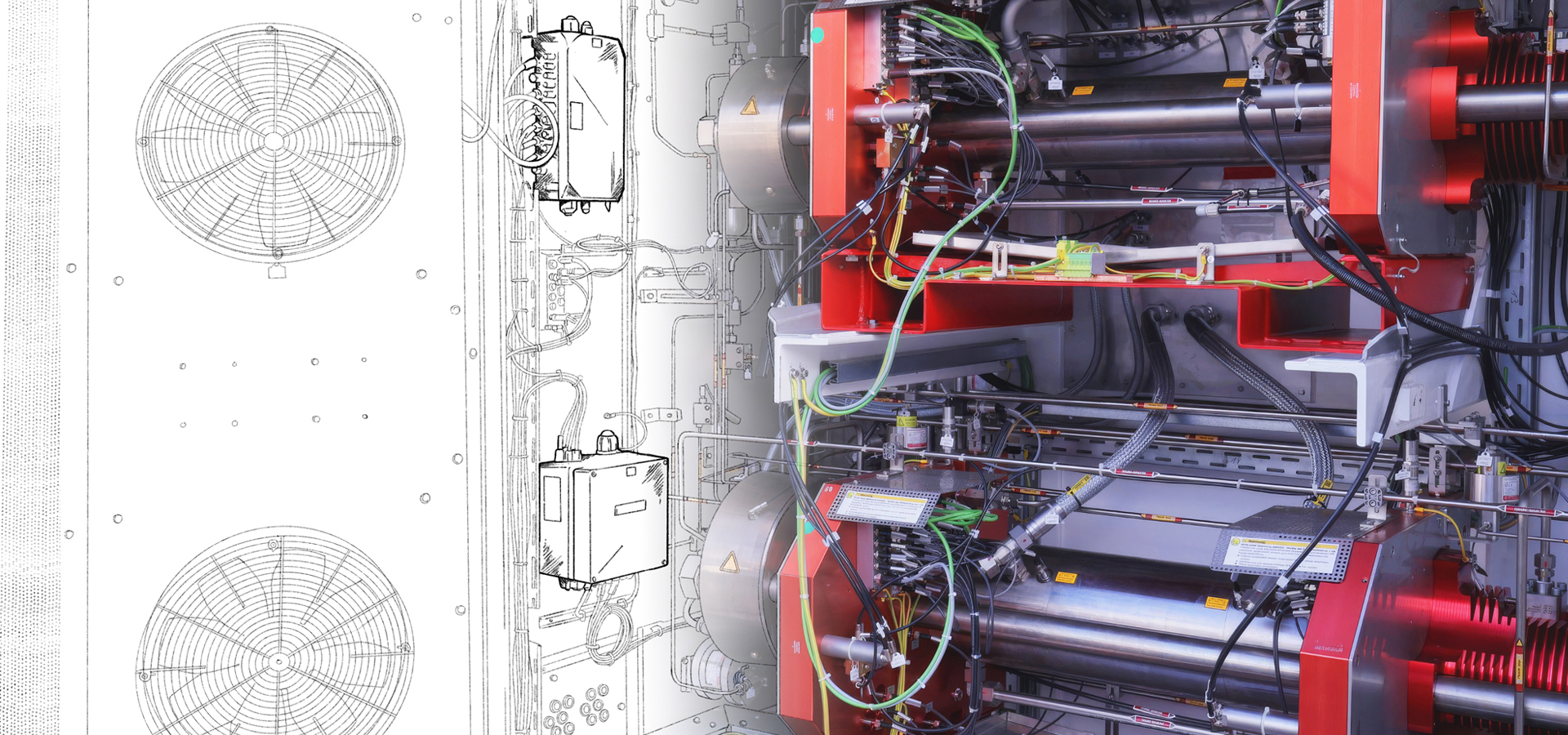
Electromobility alone will not bring about the transformation of transportation. Alternatives to battery-powered electric vehicles are needed, especially for commercial vehicles and heavy goods vehicles, due to their operating range, payload, and long charging times. One possible solution is hydrogen: a very manageable amount of the gas is sufficient to supply even large engines or fuel cells with fuel over long distances or with a demanding height profile. If the hydrogen is obtained from renewable energies or natural resources, driving is completely emission-free. For the gas to be used on a wide scale in road transport, however, the necessary infrastructure and a well-developed network of hydrogen filling stations are needed to enable continuous long-distance transportation. Maximator Hydrogen GmbH, based in Nordhausen, Germany, specializes in the manufacture of such systems. The company relies on customized solutions from Pepperl+Fuchs for mechanical and electrical explosion protection in signal processing.
Short Refueling Times, Long Operating Ranges
Hydrogen has a very high energy density: One kilogram of compressed hydrogen has an energy content of 33 kilowatt hours and therefore contains around three times as much energy as one kilogram of crude oil. Depending on the size of the vehicle tank, ranges of up to 600 kilometers are already possible today. In heavy-duty transport, developments in fuel cell technology and storage tanks are progressing, with ranges of up to 1,200 kilometers being targeted. Refueling hydrogen takes just a few minutes, similar to petrol and diesel. Short refueling times, ranges of over 500 to 1,000 kilometers at comparatively low costs and an unrestricted payload are of decisive economic importance, especially for logistics companies.
Most major commercial vehicle manufacturers have now added hydrogen-powered trucks and buses to their portfolio and are constantly developing them further. However, if you opt for a vehicle with a fuel cell drive, route planning requires good preparation. Depending on the region, the current network of hydrogen filling stations is not very well developed. According to h2stations.org, there were only around 920 stations around the world in 2023. The densest concentration of existing and planned hydrogen filling stations is in Europe, Japan, and South Korea, with slightly larger gaps in China. Along the coasts of North America and in eastern Australia, as well as in New Zealand, there are only a few hydrogen filling stations so far. It is therefore obvious that there is a need for action here. The potential is huge.
Rising Demand for Hydrogen Filling Stations
'We are still in the early stages of expanding the hydrogen filling station network, but the curve is clearly going upwards. We estimate the foreseeable demand for new facilities at around 20,000 filling stations per year worldwide,' explains Erik Albrecht-Laatsch, Head of Engineering at Maximator Hydrogen, adding confidently: 'We want to supply at least 20 % of these.'
The company has exceeded this target in Switzerland's already well-developed infrastructure network: as of today, 16 of a total of 17 facilities are operated by Maximator Hydrogen. In this comparatively small country, it was primarily logistics companies and large food retailers that pioneered the construction of hydrogen filling stations for their vehicle fleets along the supply chains and built up a nationwide network. The advantage of this is that the H2 filling stations are just as freely accessible and usable for all other road users.
From Scandinavia to Western and Southern Europe, the plant manufacturer is involved in several hydrogen infrastructure projects. The company is part of the Schmidt Kranz Group, which has its roots in mining technology. The expertise in high-pressure technology is held by the subsidiary Maximator GmbH, which has been active in this section since the 1970s. In 2019, the decision was made to create Maximator Hydrogen, a specialist supplier that focuses entirely on the production of hydrogen filling stations. In terms of technology, this was an obvious step, as hydrogen is also at the center of compression, i.e. the compression of a gas. The aggregate state of the alternative fuel makes the decisive difference to the classic filling station for conventional fuels. There, a liquid simply has to be pumped from a large tank into a smaller one. The refueling process with hydrogen, on the other hand, is much more complex, as a highly compressed gas has to be pumped from one pressure tank into another.
Transfer Processes under High Pressure
'High-pressure technology plays an important role in the entire system chain for hydrogen filling stations,' explains Albrecht-Laatsch. The gas flows out of the electrolyzer at a relatively low overpressure of 30 to 60 bar. The pressure level of the storage tank of a hydrogen filling station is much higher—around 1,000 bar for a high-pressure storage tank.
The transportation of hydrogen via pipeline, where significantly lower pressure levels are sufficient, plays more of a role in industrial applications. For use in road transport, the gas is primarily delivered by truck trailer, just like conventional fuel, with on-site electrolysis becoming increasingly important. On its way from production in the electrolyzer to the actual vehicle tank, the hydrogen is subject to several decanting processes and pressure changes. A full passenger car tank reaches around 700 bar; for commercial vehicles, so-called heavy-duty vehicles such as trucks, tractors, trains, or ships, the pressure is around half that. 'As a rule, the pressure difference of the hydrogen between the dispensing storage tank and the vehicle tank is not sufficient. The hydrogen must therefore be compressed so that the desired quantity arrives where it is needed quickly enough,' explains Marcel Urban, Team Lead Electrical Engineering at Maximator Hydrogen.
Hydrogen Compressor with a Unique Selling Point
Maximator Hydrogen has developed the MAX Compression System, the heart of its systems, to compress the hydrogen. The actual work is performed by a hydraulically driven, two-stage piston compressor, which compresses the hydrogen to up to 1,000 bar. Its pistons are fitted with seals, which are subject to unavoidable, heavy wear due to the prevailing high pressure level. Their service life is around 600 operating hours, after which they have to be replaced. Maximator Hydrogen's compressor system has a unique selling point here: Where changing a piston seal with other manufacturers entails several days of downtime—because the compressor unit has to be dismantled or completely replaced to change the seal, for example—Maximator Hydrogen's system carries out this maintenance fully automatically within a few minutes. Depending on the version, three to thirteen seals are kept in a magazine as a spare stock. The 'Automatic Seal Exchange' technology, triggered by sensors, detects when a seal is worn and replaces it automatically.
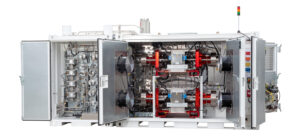
The MAX Compression System, the compressor for the hydrogen, is one of the central elements of the entire system. Several explosionproof solutions and sensors from Pepperl+Fuchs are used here.
Modular Systems, Explosionproof Signal Processing
Another of the manufacturer's strengths is the modular flexibility of its hydrogen filling stations. All elements, from delivery, compression, and storage to refueling, can be individually configured according to the requirements of the filling station operator. This is where the explosionproof components and solutions from Pepperl+Fuchs play a decisive role. This is because, regardless of the respective design, the systems are complex with sophisticated control and signal processing. As hydrogen has a very high ignitability, the entire signaling and processing must be explosion-proof. The extensively equipped control boxes contain, among other things, isolated barriers and decentralized control components, some of which are fail-safe, as well as connections for sensors such as temperature sensors and pressure transmitters. Before they can be mounted in the systems, they must be certified in accordance with the explosion protection guidelines. However, standard explosion protection components are not always suitable for all requirements. The modular flexibility of Maximator Hydrogen's systems also requires flexible solutions in terms of explosion protection.
Flexibility in Explosion Protection—Is That Possible?
'Two requirements come together here that don't actually get along very well,' says Matthias Ernst, Regional Sales Manager for Process Automation at Pepperl+Fuchs. 'On the one hand, there are the rigid requirements for explosion protection certification and, on the other, the concept of modular flexibility for filling station systems. If subsequent changes are made to a system once it has been certified, the point is quickly reached where a complete recertification is required. All it takes is the addition of extra circuits or a change to the temperature range,' explains Ernst.
With this point, he is referring to a modification that became necessary when Maximator Hydrogen received orders from Scandinavia last year. The systems there have to function perfectly even at significantly lower outside temperatures. The housings are therefore sometimes heated when necessary. 'A heater requires a relatively large amount of electrical energy, and that is anything but a trivial matter when it comes to explosion protection,' says Urban. 'In addition to the heating module, other components such as isolated barriers for additional temperature sensors and control components for reading the signals may be required, depending on the configuration according to our customers' requirements. This often results in a very complex and, above all, individually adapted assembly in the terminal boxes,' Urban continues.
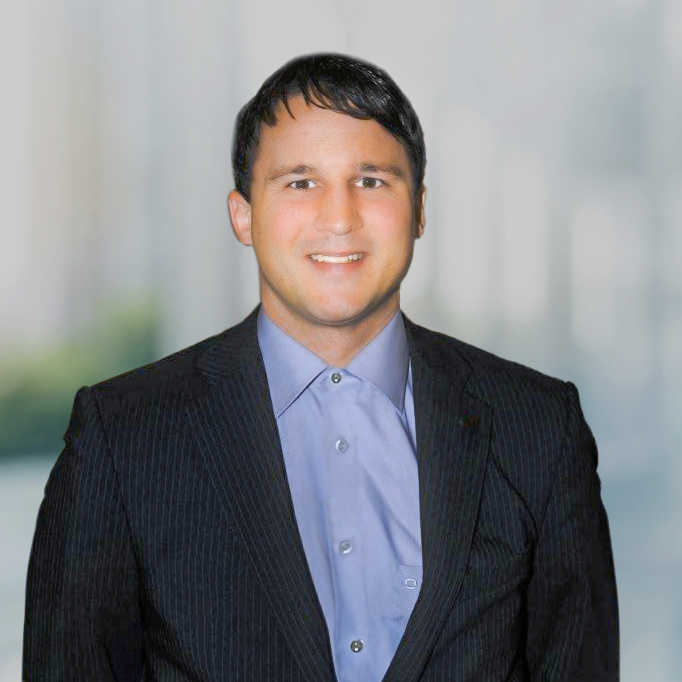
There are also differences in certifications worldwide. "If the hydrogen filling stations are built in the USA, the requirements for explosion protection are also different. While in Europe, potentially explosive atmospheres are divided into Zones for which ATEX certifications are required, in North America corresponding certifications by Class/Division are necessary," explains Ernst.
A single certification process can take months or even more than a year. If it were required for every product adaptation, this would lead to enormous delays. Pepperl+Fuchs therefore worked closely with Maximator Hydrogen to develop a flexible solution concept for explosion-protected signal processing in its systems.
Certified Flexible Enclosure Solutions Provide the Decisive Advantage
The central elements developed by Pepperl+Fuchs for explosion-protected signal processing in the various modules of the hydrogen filling station are Ex e enclosures. Ex e stands for the 'increased safety' type of protection. The key advantage here is the modular flexibility: the explosion-proof enclosures are supplied ex works with a minimum configuration of approx. 70—80% enclosure utilization, but are already certified for maximum utilization. 'Maximator Hydrogen can carry out the final assembly of the enclosures itself, depending on the individual configuration of the system,' explains Ernst. In addition to intrinsic safety barriers such as the K-System from Pepperl+Fuchs, control components from other manufacturers are also integrated into the certified enclosure solution. Renewed certification is not necessary for this, as this is already covered in the declaration of conformity and certification of the solution.
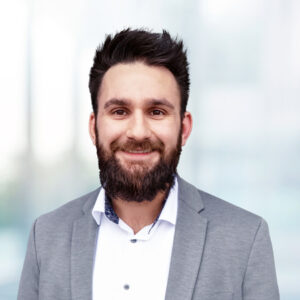
"Other suppliers were unable to deliver this modularity. The fact that we can equip the Ex e enclosures with final control components ourselves, depending on customer requirements, also gives us decisive advantages over our competitors," confirms Urban. "The Ex e solutions from Pepperl+Fuchs are now used in almost all the modules we use to assemble our systems. The only exception is the storage module, which does not require a complex control system," reports Albrecht-Laatsch. Several solutions for signal distribution and intrinsically safe circuits are used in the MAX Compression System for compressing the hydrogen, the heart of the systems. "On our modules for receiving and delivering the hydrogen to the trailers, we use another Ex e housing in a stainless steel design, which is also equipped with a touch control panel. Here, the truck driver is shown specific operating instructions when delivering or receiving hydrogen and can start the individual steps in the correct sequence," explains Albrecht-Laatsch.
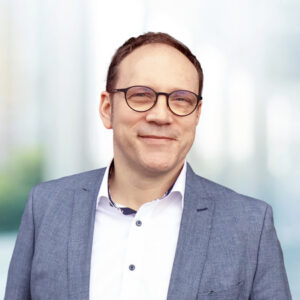
Development, Production, and Certification from a Single Source
'We initially tried another provider, but the collaboration was pretty rocky,' recalls Urban. 'Then we turned to Pepperl+Fuchs—we were of course familiar with the company as a specialist in explosion protection. From that time forward, everything went very smoothly and in a solution-oriented manner.' The expertise of the company's own Solution Engineering Center (SEC) in Bühl, Germany, which the Pepperl+Fuchs sales department can call on if standard components are not sufficient for certain applications, also contributed to this. Pepperl+Fuchs has six SECs worldwide that specialize in developing tailor-made solutions for hazardous areas. In addition to planning the perfect solution and engineering, it oversees the entire manufacturing and certification process.
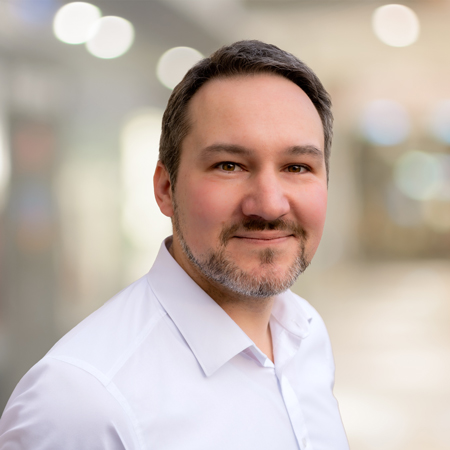
"Maximator Hydrogen needed not only technical flexibility, but also flexibility in terms of certifications and standards. We offer our customers tailor-made modular and standardized engineering solutions that fit their applications exactly and can be used in their plants worldwide, with all specifications," explains Mike Karcher, Head of the Order Management Unit at the SEC in Bühl. "The standardization of the solution is the crucial point here, as this also means considerable cost savings for the customer," continues Karcher.
Standards experts from Pepperl+Fuchs are involved from start to finish. They check the production drawing, the offer engineering, and then the finished solutions so that they can be delivered with the corresponding declaration of conformity and the required certification. In the end, the customer receives a 100 % certified product.
Cooperative Development
Receiving contributions from all sides is important for smooth cooperation, emphasizes Ernst: 'The earlier we are involved in the development of the system, the easier and faster we can find the optimal solution. Our contacts at Maximator Hydrogen involved us in the planning right from the start. Our first joint project involved several such solutions and was completed after just under a year—including the orientation phase and pandemic-related delays. For the next generation of systems, it only took a good three months for the customized housing solutions to be developed, produced, and certified.' A total of five to ten solutions from Pepperl+Fuchs are in use in one hydrogen filling station generation. Once developed, Maximator Hydrogen can order them again and again as required, just like a standard product. 'The collaboration with Maximator Hydrogen is absolutely on an equal footing and it's fun to develop the right solutions for their systems together,' reports Ernst.
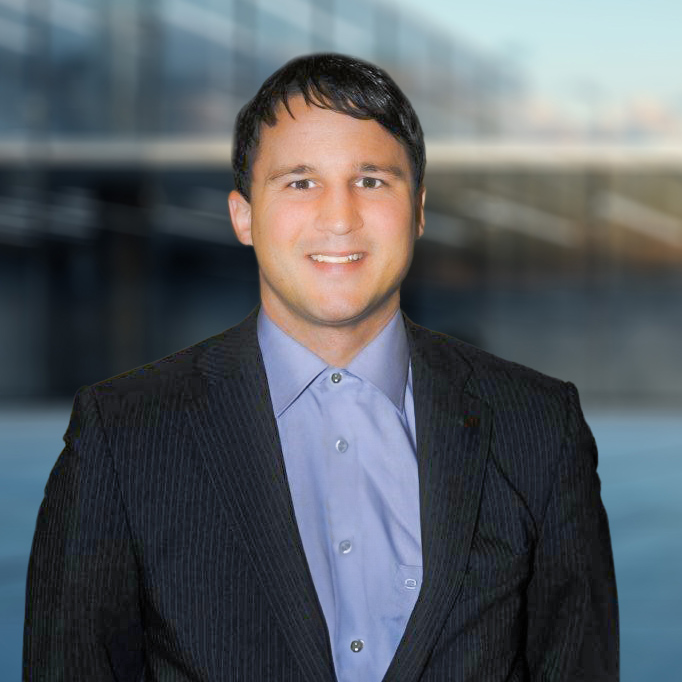
Convincing Quality and Documentation
In addition to the good cooperation, the engineers at Maximator Hydrogen praise the high quality of Pepperl+Fuchs products and the competent handling of all explosion protection issues. 'This also applies to the documentation, which is particularly important in explosion-hazardous areas,' emphasizes Urban. 'We have unrestricted access to all details, which is by no means a matter of course with other providers. Overall, we have a very productive and successful partnership, a real win-win situation. We are currently working together on further solutions for the new generation of filling stations in order to serve the dynamically growing hydrogen market.'
Learn more
Our Solutions,
as Individual as You
Subscribe now
Would you like to find out more about customized solutions from Pepperl+Fuchs? Register via the form below to receive regular updates.

Receive regular updates on customized solutions from Pepperl+Fuchs!
Subscribe now