23. August 2021
Immer in Bewegung
Fahrerlose Transportsysteme (FTS) ermöglichen schnellere und effizientere Prozesse in Produktion und Intralogistik. Das Produktionswerk von Pepperl+Fuchs in Trutnov (Tschechische Republik) setzt seit Anfang des Jahres FTS-Systeme ein. Erfahren Sie, mit welchen Herausforderungen das Team bei der Einführung konfrontiert war und welche Vorteile FTS mit sich bringen.
Lautlos bewegen sie sich durch die Produktionshallen und transportieren Waren und Materialien genau dorthin, wo sie gerade gebraucht werden. In Zeiten zunehmender Automatisierung kommen fahrerlose Transportsysteme (FTS) immer häufiger in der Produktion, der Lagerlogistik oder etwa in Fertigungsstraßen der Automobilindustrie zum Einsatz. Dort tragen sie maßgeblich zur Erleichterung des Arbeitsalltags bei, indem sie Ressourcen schonen und einen schnelleren Materialtransport ermöglichen.
Auch im Pepperl+Fuchs Werk im tschechischen Trutnov setzt man seit Anfang des Jahres auf fahrerlose Transportsysteme. Vor welchen Herausforderungen das Team bei der Implementierung stand und welche Vorteile die automatisierten Produktionshelfer mit sich bringen, weiß Stepan Potocek. Am Standort Trutnov setzt er sich als Lean Consultant gemeinsam mit seinem Team für schlankere, agilere Produktionsprozesse ein.
Lange Laufwege und Wartezeiten standen für die Mitarbeiter des tschechischen Pepperl+Fuchs Werks bislang an der Tagesordnung. Im alten Produktionsgebäude waren Produktion und Warenlager auf zwei Ebenen verteilt, sodass sämtlicher Warentransport über einen Aufzug abgewickelt werden musste: „Es gab im gesamten Gebäude nur einen Aufzug, um den gesamten Materialfluss abzuwickeln und das Rohmaterial auf einem Rollwagen vom Erd- ins Obergeschoss zu transportieren,“ erinnert sich Potocek: „So war es nicht immer ganz einfach, einen reibungslosen Betrieb aufrechtzuerhalten.“ Als schließlich feststand, dass in Trutnov ein neues Gebäude errichtet wird, hatte das Team um den Lean Consultant alle Hände voll zu tun, um die zukünftigen Abläufe in Produktion und Logistik von Grund auf zu optimieren, vermeidbare Laufwege und damit ein Vielfaches an Zeit einzusparen — ganz im Sinne des Lean-Management-Konzepts.
Weg frei für ein neues Produktionskonzept
Nach einer einjährigen Bauphase war es Mitte 2020 dann soweit und das Werk, in dem vor allem induktive Näherungsschalter und Spezialsensoren hergestellt werden, zog in eine komplett ebenerdige Halle mit einer 3.000-m²-Produktionsfläche, einem 1.500 m² großen Lager und 1.500 m² technischen Anlagen.
„Bereits fünf Monate zuvor haben wir ein Team aus sechs Personen gebildet, das sich schwerpunktmäßig mit der Bedarfsanalyse und der Erstellung eines neuen Anlagendesigns befasst hat“, erinnert sich Potocek an die Anfangsphase ihrer Planung. Daraus entstanden ist ein völlig neues Produktionskonzept, in dem nahezu alle Fertigungszellen in einer U-Form angeordnet sind und jeweils über eigene Übergabestellen für Rohmaterial, Kanban-Material sowie fertige Produkte verfügen. Da sich diese speziellen Stationen direkt am Haupttransportweg befinden, war auch die Basis zur Nutzung fahrerloser Transportfahrzeuge (FTF) geschaffen.
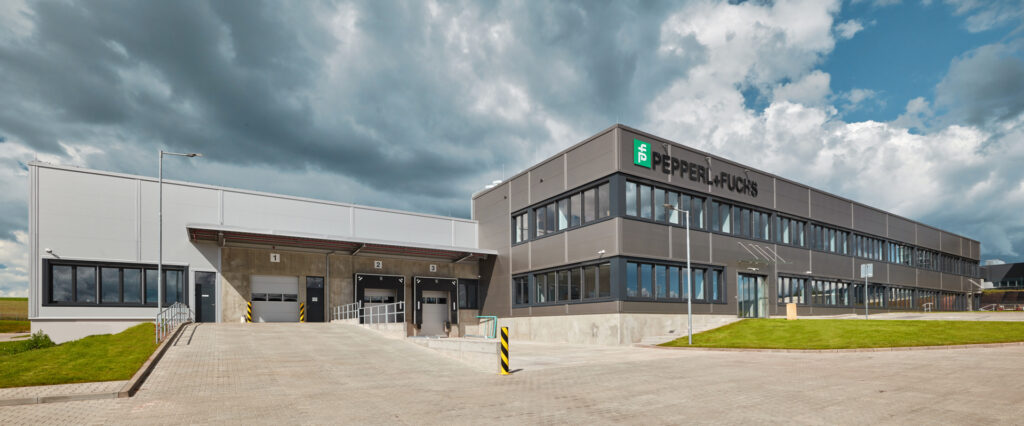
Zusätzlich ist das neue Gebäude mit zwei Rolltoren ausgestattet, welche die Fertigung mit dem Warenlager verbinden. „So können fertig produzierte Waren sowie leere Kanban-Boxen einfach auf fahrerlosen Transportsystemen durch das eine Tor und noch zu verarbeitendes Material durch das andere Tor transportiert werden, welches sich in der Mitte der Produktionshalle befindet“, ergänzt er. Dadurch entsteht ein durchdachter Warenkreislauf, der eine automatisierte Erfassung der Kanban-Materialeingänge und -Ausgänge via RFID erlaubt.
Die Grundlage für das neue Konzept und damit auch die Suche nach einer geeigneten FTS-Lösung bildete eine sogenannte Value Stream Map, die das Team bereits in der ersten Planungsphase erstellt hatte, erklärt Potocek: „Diese bildet die zukünftigen Warenströme ab und zeigt auf, welche Anforderungen und Bedürfnisse sich für die Ausgestaltung der Produktionsprozesse ergeben. Auf Basis dieser Analyse lässt sich ableiten, wie viele Transportboxen für die gesamte Produktion benötigt werden und welche Strecke unsere autonom fahrenden Fahrzeuge voraussichtlich pro Schicht zurücklegen.“ So entstand schließlich ein umfangreicher Evaluationsbogen, der die Anforderung an die Lösung den verfügbaren FTS-Technologien gegenüberstellt.
Die Qual der Wahl
Ob die Entscheidung auf ein netz- oder batteriebetriebenes System fällt, hängt ganz von der individuellen Anwendung und den Bedingungen ab. „Für uns stand schnell fest“, so Potocek, „dass wir eine Out-of-the-Box-Lösung suchen, die keine besonderen Programmierkenntnisse erfordert und sich einfach in unser neues Anlagenkonzept integrieren lässt.“
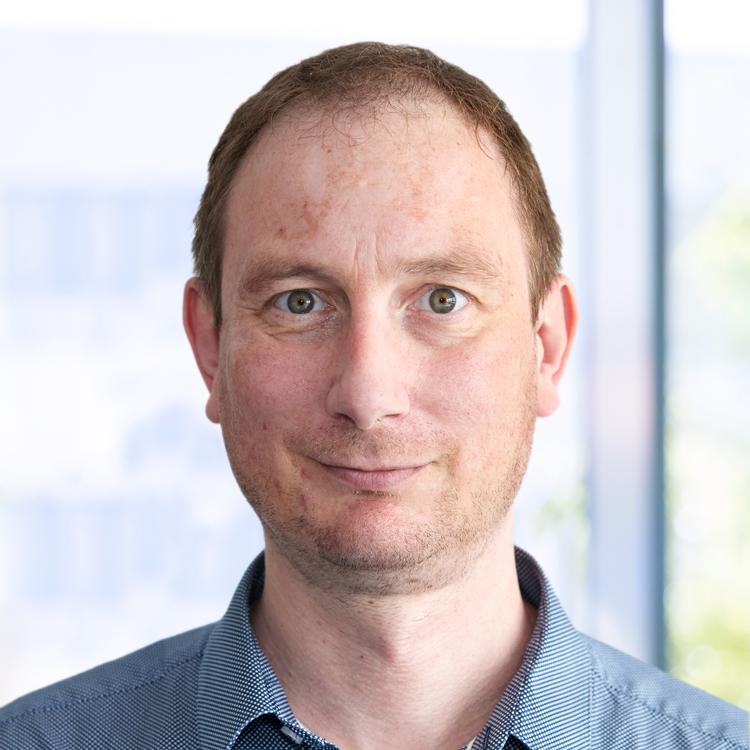
Mit dem fahrerlosen Transportsystem LEO-Locative wurde schnell die passende Lösung gefunden. Die BITO-Lagertechnik Bittmann GmbH, das deutsche Unternehmen hinter LEO-Locative, bietet kompakte, flexibel skalierbare FTS-Lösungen für Behälter und Kartonagen, die sich dezentral steuern lassen — und nebenbei ganz ohne WLAN oder Leitrechner auskommen. Dank der optischen Spurführung können Fahrbefehle einfach mithilfe optischer Marker auf dem Boden an das fahrerlose Transportfahrzeug übergeben werden.
„In Kooperation mit dem tschechischen Tochterunternehmen BITO skladovacà technika CZ s.r.o. haben wir schließlich ein völlig einzigartiges System entwickelt, in dem alle aktiven Komponenten Teil des FTF sind, die Übergabestationen hingegen als passive Komponenten fungieren“, berichtet Pavel Grund, der den Rollout in seiner Funktion als Test Support EMS von Anfang an begleitete. „Mit diesem System können wir uns ein flexibles Produktionsumfeld bewahren, in dem kurzfristige Anpassungen der Produktionsabläufe problemlos möglich sind, ohne dass dabei Rücksicht auf die Anbindung an die elektronische Infrastruktur genommen werden muss“, ergänzt Potocek.
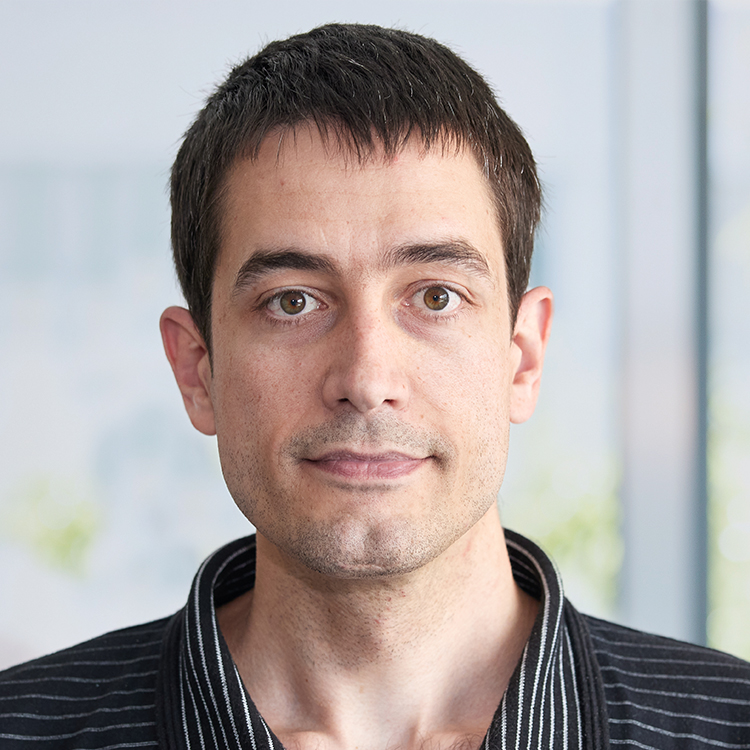
Design und Funktion kombiniert
Noch bevor die fahrerlosen Transportsysteme in den Produktionsprozess implementiert werden konnten, galt es, eine Reihe unterschiedlicher Anforderungen an Design und Funktionalität zu beachten. So wurden die fahrerlosen Transportfahrzeuge beispielsweise mit dem 2-D-LiDAR-Sensor R2100 von Pepperl+Fuchs ausgestattet, um eine zuverlässige Erfassung des Umfelds zu gewährleisten und Zusammenstöße zu vermeiden. „Zur optischen Spurführung der fahrerlosen Transportfahrzeuge kommt unser DataMatrix-Positioniersystem PGV (Position Guided Vision) zum Einsatz“, schildert Grund. Dieses besteht aus einem Kamerasystem mit integrierter Beleuchtungseinheit, welches die am Boden angebrachten Farbbänder und DataMatrix-Codebänder selbst in engen Kurvenfahrten zuverlässig erkennt. Der Reflexionslichttaster der Serie GLV18 wiederum überwacht den Verladevorgang und sendet zur Weiterfahrt ein Startsignal an das FTF, um zum nächsten Stopp weiterzufahren.
Doch damit nicht genug: Um auch dem Kanban-Gedanken Rechnung zu tragen, wurde das System um zusätzliche Komponenten sowie um ein RFID-System erweitert: Darunter der induktive Sensor der Baureihe VariKont L, der zuverlässig detektiert, ob sich das Fahrzeug außerhalb oder innerhalb der Übergabestation befindet. Dort angekommen, überwacht die Lichtschranke ML100 mit integrierter Hintergrundausblendung den Beladevorgang und erkennt, ob die Boxen richtig positioniert wurden, sodass sie beim Weitertransport nicht herunterfallen.
An den beiden Rolltoren sind seitlich jeweils ein RFID-Schreib-/Lesekopf der Serie F190 sowie eine IdentControl-Auswerteeinheit angebracht. Das Transportfahrzeug verfügt über einen RFID-Tag, der das Öffnen des Rolltors auslöst, sobald sich das FTF annähert. Auch die Kanban-Boxen selbst sind mit eigenen RFID-Tags ausgestattet, um den Materialfluss jederzeit überwachen zu können.
So konnte das Team aus Tschechien ein intelligentes, aufeinander abgestimmtes Intralogistik-Konzept entwickeln, in dem nun lange Wege oder die Suche nach Materialien der Vergangenheit angehören, resümiert Potocek: „Dank des LEO-Locative-Transportsystems und der perfekt darauf abgestimmten Sensorik sparen wir nicht nur Zeit, sondern reduzieren auch das Unfallrisiko um ein Vielfaches, sodass weder Mensch noch Material zu Schaden kommen.“