29. Mai 2022
Am Puls der Zeit – Zwischen Wissenschaft, Forschung und Industrie
Im Technologiezentrum TZ PULS Produktions- und Logistiksysteme der Hochschule Landshut kann sich jeder ein Bild davon machen, wie auch kleine und mittlere Unternehmen eine auf ihre Bedürfnisse abgestimmte, smarte industrielle Produktion und Intralogistik aufbauen können. Mit dabei: modernste Sensoren und Automatisierungskomponenten von Pepperl+Fuchs.
Die moderne Fabrik mit intelligenten Produktions- und Logistiksystemen muss nicht mehr gebaut werden — sie existiert. Und zwar in Deutschland, genauer im niederbayerischen Dingolfing. Anders als vielleicht vermutet, handelt es sich aber nicht um das Werk eines namhaften großen Automobilherstellers. Wer sehen möchte, wie sich modernste Intralogistik gestaltetet, muss ins Technologiezentrum Produktions- und Logistiksysteme der Hochschule Landshut, kurz TZ PULS, und sich dort mit dem wissenschaftlichen Leiter Prof. Dr. Markus Schneider unterhalten. Der Wirtschaftswissenschaftler hat eine exakte Vorstellung, wie die moderne industrielle Fertigung gelingen kann.
In enger Zusammenarbeit mit Automatisierungsspezialisten wie Pepperl+Fuchs sucht Schneider nach organisatorischen und technischen Lösungen für die perfekten Produktions- und Logistikabläufe. Gefragt nach seiner Intention: „Wir denken für den Mittelstand und unterstützen die Unternehmen, weiterhin in einem Hochlohnland wie Deutschland wettbewerbsfähig produzieren zu können.“ Das ist jedoch nicht immer leicht, wie er und sein Team im Rahmen einer Führung im TZ PULS berichten.
Entscheidend für eine gelungene Automatisierung ist der Prozess
Vom Besuchersteg aus überblickt man die komplette, vollfunktionale Lern- und Musterfabrik. Mit oben auf der Galerie sind Prof. Schneider und zwei seiner wissenschaftlichen Mitarbeiter, Lisa Schuler (M. Sc.) und Tobias Ettengruber (M. Eng.), sowie Rudolf Buchner, Vertriebsingenieur Fabrikautomation bei Pepperl+Fuchs. „Mehr als das, was hier an Maschinen und Komponenten zu sehen ist, braucht es erst einmal nicht, um eine komplette interne Wertschöpfungskette vom Wareneingang bis zum Versand abzubilden“, erklärt Schneider. Von hier oben präsentiert sich Fachbesuchern aus aller Welt die perfekte Nachbildung eines Wertstroms aus Wareneingang, Lager- und Kommissionierzone, drei Fertigungsbereichen und Warenausgang.
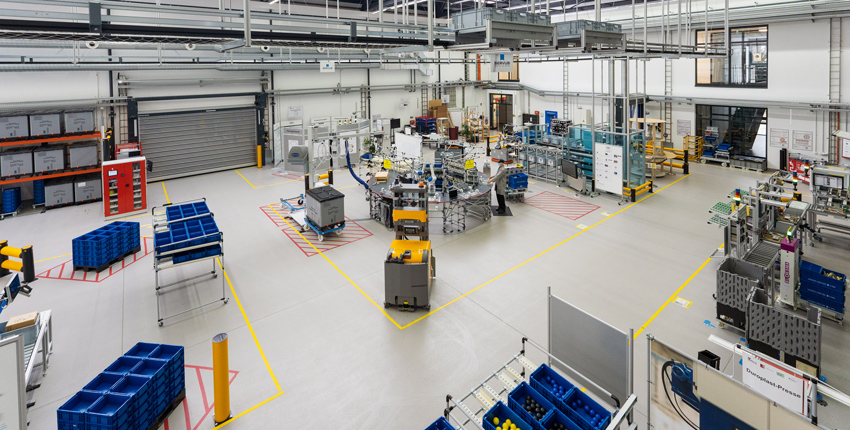
Schneider, selbst Fabrik- und Logistikplaner mit jahrelanger Praxiserfahrung in der Automobilindustrie, erläutert, warum er die Musterfabrik gemeinsam mit seinem Team so ausgelegt hat. Seine Erfahrung aus hunderten Beratungsgesprächen und Unternehmensbesuchen zeige ihm, dass es primär darauf ankomme, dass Fertigungsunternehmen als erstes einen genauen Blick auf die Qualität ihrer Prozesse werfen. Aus seiner Sicht seien hier am Technologiestandort Deutschland die größten Probleme vorhanden. Schneider erklärt: „Viele Unternehmen gehen ihre Probleme ausschließlich von der technischen Seite an und lassen den Prozess als solchen unbeachtet. Wenn Sie einen schlechten Prozess digitalisieren, haben sie einen schlechten digitalisierten Prozess und wenn sie einen schlechten Prozess automatisieren, haben sie am Ende einen schlechten automatisierten Prozess.“
Prozesse vertikal betrachten
Dort setzt Schneider mit seiner Forschung im ersten Schritt an. Und zahlt dabei sogar auf Themen wie Nachhaltigkeit und Umweltschutz ein, da er die Prozesse durchaus auch vertikal „denkt“. Das könne Unternehmen auf lange Sicht dabei unterstützen, ihre Fertigungen nicht in die Fläche zu erweitern, sondern in die Höhe. Für den Wirtschaftswissenschaftler und sein Team ist eines zentral: „Mit dem TZ PULS haben wir eine gesicherte Basis in Deutschland geschaffen, an dem sich jedes fertigende Unternehmen prozessual orientieren kann. Mit unserer Lean Factory holen wir Unternehmen dort ab, wo sie heute stehen und zeigen, wie man mit einfachen strukturellen und organisatorischen Maßnahmen stabile Prozesse schafft.“ Denn, so Schneider: „Wir denken für den Mittelstand. Und der zeigt sich sehr vielfältig.“
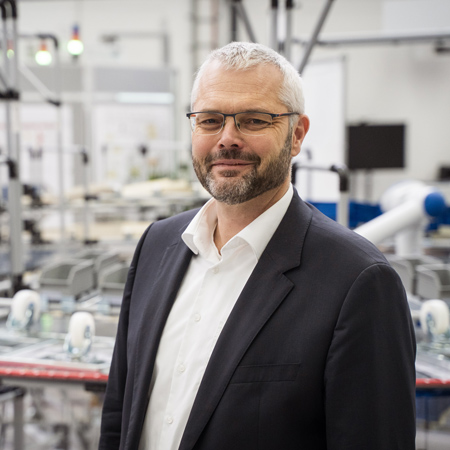
Produktionskonzepte und Sensorik flexibel gedacht
Schneider wird nicht müde zu betonen, wie wichtig es ist, Fortschritt nicht ausschließlich technisch zu betrachten, sondern stets und zuerst immer den Prozess. Die Ingenieure im TZ PULS versuchen deshalb, ihre Forschung so nah an der Arbeitsrealität anzulehnen, wie irgend möglich. „An dieser Fertigungsanlage in der Musterfabrik können wir z. B. 185.000 Bodenroller effizient herstellen. Wir können diese Anlage aber auch zu einer klassischen Werkstattfertigung umbauen und gemeinsam mit einem Kunden dann zu einer Fließfertigung umgestalten.“ So ließen sich Konzepte für Lean-Produktion am besten veranschaulichen. „Was hingegen unsinnig sei: Einfach mal RFID-Komponenten in einem alten Prozess verbauen“, darin sind sich Schneider, Schuler und Ettengruber einig. Vielmehr sei es für Unternehmen wichtig, sich beim Prozess an grundlegenden Prinzipien zu orientieren. „Und die“, so Ettengruber, „lassen sich auch auf die Technik anwenden.“
Für die Realisierung der intelligenten Lager- und Logistikprozesse in der Musterfabrik des TZ PULS kommen verschiedenste Technologien von Pepperl+Fuchs zum Einsatz. „Die Zusammenarbeit mit dem TZ PULS ist eine für beide Seiten befruchtende Kooperation. Bestes Beispiel ist das Lager in der Musterfabrik. Dort werden klassischerweise Distanzsensoren verwendet. Dennoch haben wir gemeinsam an dieser Stelle auch mit kapazitiven Sensoren und Ultraschallsensorik experimentiert“, erklärt Buchner und fügt hinzu: „Tests wie diese bringen beide Seiten voran, denn der hier abgebildete Intralogistikbereich erlaubt eine Live-Demo, die sich nahezu auf alle Bereiche und Branchen anwenden lässt.“
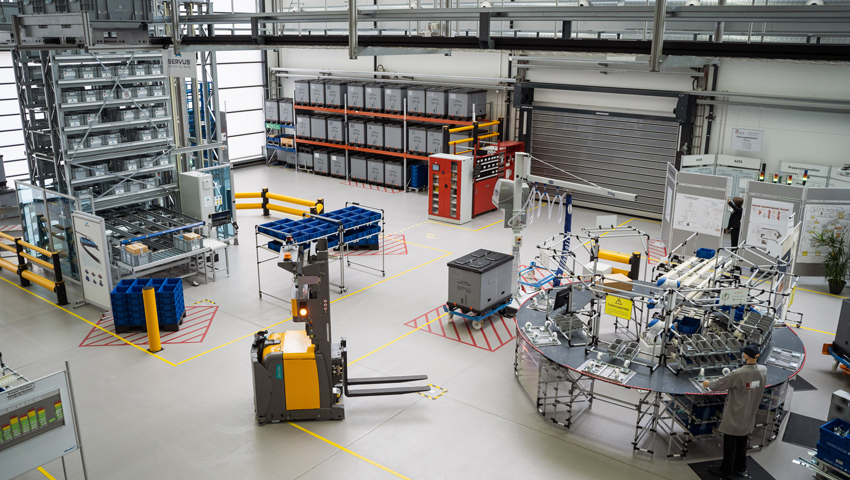
Warum fachlicher Austausch so wichtig ist
So konnte Buchner beispielsweise einen seiner Kunden, ein namhaftes deutsches Messtechnik-Unternehmen, mit den Experten vom TZ PULS verknüpfen. Das Ergebnis: Die ursprünglich vom Unternehmen für ihre Intralogistik favorisierte RFID-Lösung wurde in Betrachtung aller Prozesse hinterfragt. Zusammen mit dem Kunden und dem TZ PULS erarbeiteten Buchner und alle Beteiligten eine genau auf die Prozesse des Unternehmens abgestimmte Intralogistiklösung. Buchner ist ein Aspekt dabei besonders wichtig: „Die Kooperation mit dem TZ PULS eröffnet echte Chancen, den Erkenntnisgewinn aus Forschung und Sensorentwicklung in die breite Masse der Industrie zu transportieren. Unsere Kunden sind enorm vielfältig; nicht alle können sich diese neuen Prozesse immer vorstellen. Hier in der Musterfabrik des TZ PULS haben sie die Möglichkeit, sich moderne intralogistische Prozesse anzuschauen — von simpel bis sehr komplex.“
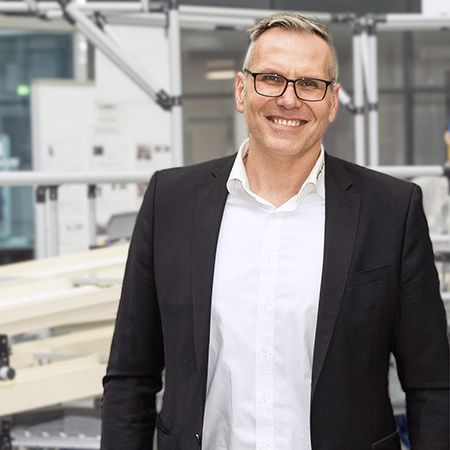
Von der U-Zelle zur O-Zelle: so kann das Morgen aussehen
Professor Schneider deutet auf zwei weitere wichtige „Mitarbeiter“ seines Teams: lebensgroße Puppen in Arbeitskleidung, die dem Besucher täuschend echt die Arbeit an Werkbank und Planungstafel suggerieren. „Wir stellen immer den Menschen in den Mittelpunkt — ob Werker oder Führungskraft.“ Auch deshalb haben er und sein Team die starre U-Zelle in der Fertigung aufgebrochen und daraus eine O-Zelle gemacht. Das Ziel: Der Werker soll automatisiert mit Material, aber auch Informationen versorgt werden. Aufwendiges Holen und Bringen soll künftig entfallen. Schneider betont: „Wir nutzen die einzigartigen Fähigkeiten des Menschen und automatisieren stattdessen die Logistik.“ Kein leichtes Unterfangen, aber möglich. Auch dank der hochwertigen Automatisierungstechnik von Pepperl+Fuchs. Ein RFID-System, optoelektronische Sensoren, der 2-D-LiDAR-Sensor R2000, Ultraschallsensoren, induktive und kapazitive Sensoren sowie die IO-Link-Master der Serien ICE2 und ICE3 — all diese Komponenten machen das virtuose Jonglieren von Daten auf der Meta-Ebene möglich und den Prozess in der Musterfabrik damit beherrschbar.
Digitalisierte Fertigungsprozesse
Der Arbeitsalltag von Lisa Schuler gestaltet sich nach dem Prinzip „Trial and Error“, sprich Probieren und Optimieren. Die wissenschaftliche Mitarbeiterin hat, u. a. durch Programmierung einer Schnittstelle, das softwareseitige Konzept mitentwickelt, um den Werker kontinuierlich automatisiert mit Material für die Fertigung versorgen zu können. „Der Clou: Ein manuelles Eingreifen im Sinne von ,Teile-Nachschub holen‘ entfällt. Möglich machen es RFID-Komponenten von Pepperl+Fuchs, die über moderne Schnittstellen und Protokolle verfügen“, erklärt Schuler.
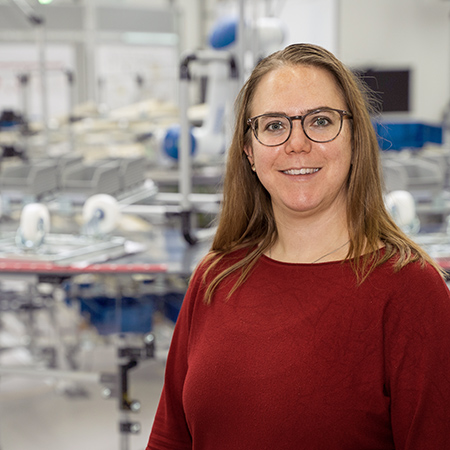
Um die Komplexität von Schulers Aufgabe zu verstehen, lohnt es, sich den Aufbau der O-Zelle vor Augen zu führen: Der Werker an seinem Platz (außen) montiert beispielsweise Rollwägen. Mittig, im inneren der O-Zelle, ist ein Roboter positioniert. Gehen dem Werker jetzt z. B. die Schrauben aus, platziert er die leere Schraubenbox unterhalb seiner Werkbank in einem Kanban-Regal. Mit Hilfe von RFID wird jetzt die leere Box detektiert: Die Daten hinter der produkt- bzw. objektbezogenen Information sind auf einem eingelassenen RFID-Tag gespeichert. Ein RFID-Schreib-/Lesekopf identifiziert die auf der Schraubenbox angebrachte Identifikationsnummer und kann die benötigten Informationen an die Steuerung weiterleiten, die nun die Transportkoordinaten zur Verfügung stellt. Alles was der mittig in der O-Zelle platzierte Sechs-Achs-Roboter jetzt tun muss, ist mit Hilfe der entsprechenden Koordinaten eine neue Box mit Schrauben in das Kanban-Regal zu liefern und die leere Box am definierten Ort abzustellen. Der Werker kann sich also voll und ganz auf seine Montage konzentrieren.
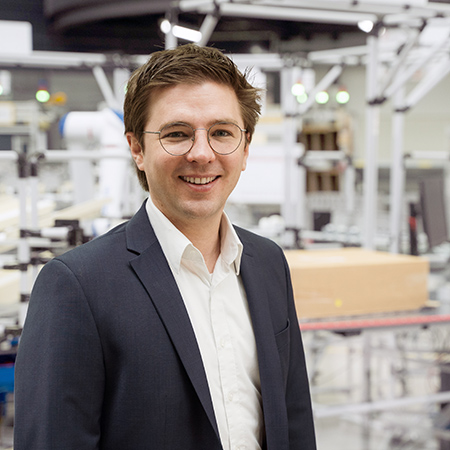
IO-Link-Master: der Weg in die digitale Vernetzung
Ettengruber betont: „Wenn wir neue Prozesse etablieren, denken wir auch in die Zukunft. Die IO-Link-Systemlösungen von Pepperl+Fuchs ebnen uns den Weg in die digitale Vernetzung.“ Der Mannheimer Sensorikhersteller bietet ein durchgängiges Portfolio vom Sensor bis in die Cloud. Insbesondere hervorzuheben ist der IO-Link-Master mit MultiLinkâ¢-Technologie. Basierend auf dem Mehrfachzugriffskonzept können Sensordaten parallel zur gleichen Zeit klassisch an eine SPS übermittelt werden sowie z. B. über MQTT an Cloud-basierte Systeme, übergeordnete Steuerungen oder auch an Warehouse-Management-Systeme. Bestehende Anlagen können so erweitert werden, ohne in die eigentliche Automatisierungssteuerung einzugreifen. Die im IO-Link-Master integrierten Standards wie OPC UA oder MQTT vereinfachen das Aufsetzen von Prozessen und halten den Programmieraufwand gering. Lisa Schuler, zuständig für die Integration und Vernetzung der Systeme am TZ PULS, zeigt was Ettengruber meint: Mit zwei Klicks navigiert sie sich in ihr Programm und kann die Daten aller in der Fabrik verbauten Sensoren abgreifen und weiterverarbeiten.
Intelligente Intralogistik nicht ohne fahrerlose Transportfahrzeuge
So ist etwa das fahrerlose Transportfahrzeug (FTF) von Jungheinrich mit einem 2-D-LiDAR-Sensor R2000 von Pepperl+Fuchs bestückt, um sich gefahrenfrei bewegen zu können und z. B. die Übergabe der Großladungsträger (GLT) zuverlässig zu realisieren. Der R2000 basiert auf dem Messverfahren PRT (Pulse Ranging Technology) und ist ideal geeignet für exakte und hochdynamische Positionsbestimmungen. „Mit Hilfe des R2000 kann sich der Stapler 360° frei in der Halle bewegen. Darüber hinaus garantieren die sehr hohe Winkelauflösung und der besonders kleine Lichtfleck des 2-D-LiDAR-Sensors höchste Präzision und somit einen sehr genauen Positionswert — perfekt für moderne und dynamische Produktions- und Logistikabläufe wie hier im TZ PULS“, fügt Buchner hinzu.
Spielwiese Hochregal
Das mehrere Meter hohe Regal mit den GLT, welches das FTF anfährt, ist für den Ingenieur Ettengruber besonders wichtig, zeigt es doch die Vielfalt an Automatisierungsoptionen: „Hier am Regal haben wir jetzt testweise viele Pepperl+Fuchs Sensoren unterschiedlichster Funktionsprinzipien an verschiedenen Positionen verbaut. Zum einen sind klassische induktive Näherungsschalter, zum anderen optoelektronische Sensoren im Einsatz; auch Ultraschallsensoren befinden sich an den Verstrebungen. Dabei ist es aber nicht so, dass diese, einmal montiert, dauerhaft an einer Position verbleiben.“ Vielmehr testet Ettengruber Platzierungen, demontiert, setzt diese anderenorts neu und eröffnet sich und seinem Team so immer wieder neue Denkansätze für eine zukunftsweisende Intralogistik und deren Prozesse.
Die Kooperation zwischen Wissenschaft, Forschung und einem Automatisierungsspezialisten wie Pepperl+Fuchs steht damit beispielhaft für den so wichtigen Wissensaustausch, um die Industrie und den Mittelstand wettbewerbs- und damit zukunftsfähig zu machen.