February 15, 2024
When Performance Exceeds All Expectations: Ethernet-APL Proves to Be a Market-Ready Technology
2018 saw the official launch of a project that is still unique in the process industry today: Renowned manufacturers joined forces to develop a technology that closes a crucial gap—an Ethernet that is suitable for the specific requirements of the process industry. This finally paves the way for Industry 4.0 applications and IIoT in this market.
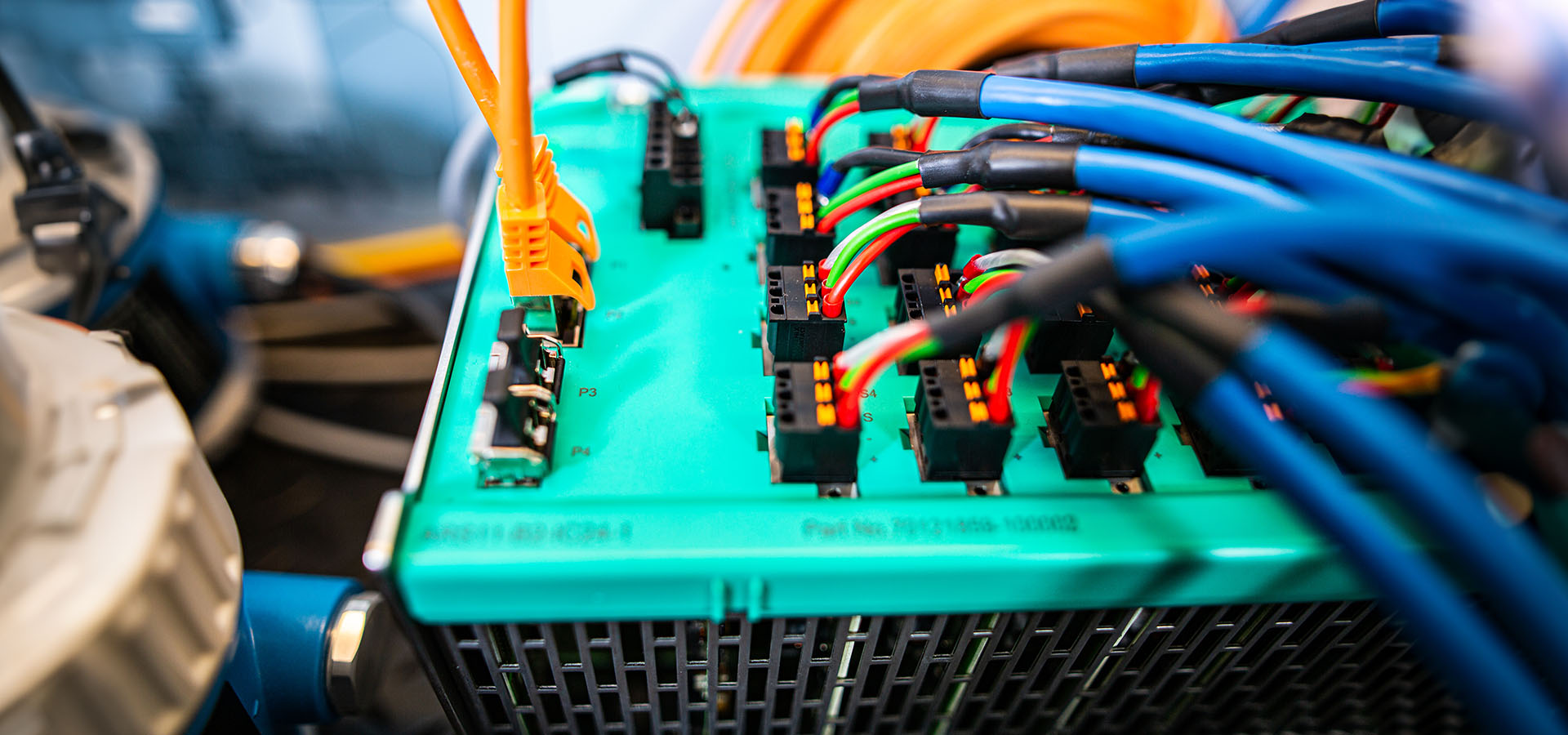
Together with the companies ABB, Endress+Hauser, Krohne, Phoenix Contact, Rockwell Automation, SAMSON, Siemens, Stahl, Vega, Emerson, and Yokogawa, Pepperl+Fuchs worked on standardizing the physical layer of a communication system for process industries. The Ethernet-APL project was organized and supported by the leading associations for industry standards FieldComm Group, ODVA, OPC Foundation, as well as PROFIBUS and PROFINET International. In this context, Pepperl+Fuchs developed the Ethernet-APL rail field switch, which is the first product to enable direct, fast, and barrier-free access to the field devices of a process plant via Ethernet-APL.
Another milestone in the development of this future technology was reached in spring 2023: Ethernet-APL has proven its market readiness in three large-scale scalability tests—the technology is ready for use! Let´s take a brief look back at the beginnings of Ethernet-APL and ask six experts from the companies involved about the structure and significance of the latest scalability tests.
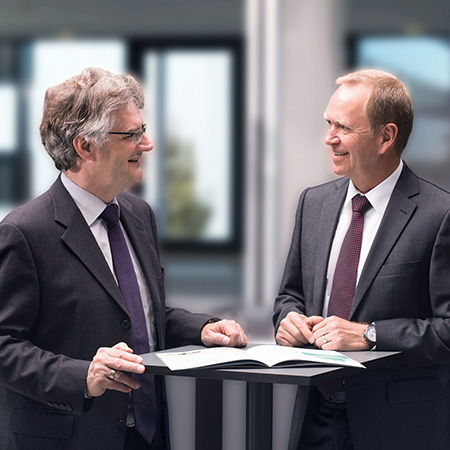
Michael Kessler, Executive Vice President Components & Technology, and Lutz Liebers, Chief Operating Officer Process Automation in the interview
Michael Kessler, Executive Vice President Components & TechnologyEthernet-APL is an Ethernet physical layer that makes it possible to communicate with devices in a process plant. The key aspect is to ensure intrinsic safety for potentially explosive areas. A very important advantage is that Ethernet-APL is significantly faster than anything hat has existed before. In my opinion, the most important feature is the end-to-end communication, which goes from the control system to the field device. This eliminates the need for gateways that require complex configuration.
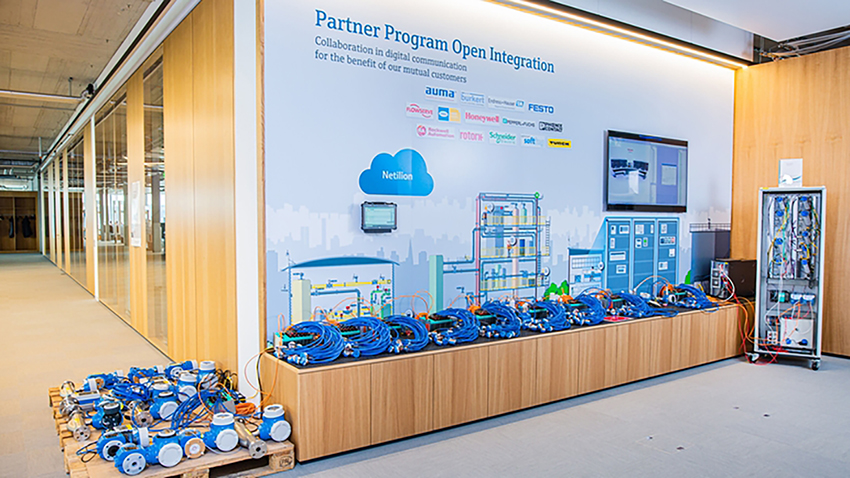
The set-up: 238 Endress+Hauser field devices were integrated into an Ethernet-APL network with Pepperl+Fuchs field switches and controllers from Honeywell, ABB and Siemens.
KesslerThat's right! Back in 2015, we presented an initial demonstrator as the result of a study that showed that the physical hurdles in the process industry—such as the required cable lengths in extensive process plants or the robustness requirements—could be overcome. The demonstrator showed the typical communication architecture of a plant with signal transmission via Ethernet on a small scale.
KesslerYou could say that. We have used the experience gained from this study and from numerous discussions to drive forward the establishment of Ethernet in process automation. The next step was to develop concepts for application-ready APL infrastructure components. Our product study on a so-called media converter that uses APL to transmit Ethernet over up to 1 000 m via two-wire cable provided an initial outlook. The product study ultimately became our Ethernet-APL field switch from FieldConnex®, which we launched on the market in 2022.
Andreas Hennecke, Head of Product Marketing Management at Pepperl+FuchsYes, that´s correct. As early as 2011, several solution providers began joint technical investigations into APL. After five years, the research had progressed so far that the IEEE Standards Association approved a development project in 2016 to expand the Ethernet standard to include a powered two-wire Ethernet, called 10BASE-T1L. The aim was to standardize Ethernet in process automation as IEEE 802.3cg by 2019. And in 2018, the APL project was officially launched with the signing of the agreement by all participating companies. Incidentally, this is the largest collaboration in the history of process automation to date and a great success for that reason alone!

Lutz Liebers, President Division Process AutomationA fundamental one—it is simply the prerequisite for this. Industry 4.0 applications in process automation only work if it is possible to transfer large volumes of data from the field level of the process plants to the information level of the Industry 4.0 architecture. With Ethernet-APL, we create an end-to-end communication path that makes valuable additional data from field devices centrally available.
LiebersI would say everything! Users will finally be able to take full advantage of the wealth of information that modern field devices and sensors record and make available. For example, they can use condition monitoring to centrally monitor the status of their field devices and therefore identify maintenance requirements at an early stage. The concept of predictive maintenance has great advantages, especially in the process industry, as it avoids short-term shutdowns and unwanted system downtimes. However, the greatest benefit is achieved when the data is used to monitor and optimize the condition of the entire system.
Frank Birgel, Product Owner at Endress+Hauser Digital SolutionsAt Endress+Hauser, quality plays a major role not only in sensor technology, but also in digital integration. The decision to set up a system-related scenario under full network load was therefore relatively easy.
Dr.-Ing. Emanuel Trunzer, Automation Engineer at BASFThe aim of the mass tests was to simulate and verify the correct functioning and robustness of a PROFINET network via an Ethernet-APL network in a realistic plant size—in other words, to leave the familiar laboratory scale. This is an essential prerequisite for the acceptance of this technology by users.
TrunzerWe at BASF were invited to contribute the requirements from the user´s perspective to this test. And then together we set up a network with almost 240 APL devices, 10 field switches, and various control systems, on which the tests were then carried out in a practical manner.
HenneckeWe also carried out not just one, but three load tests with three different control systems and components from a wide range of manufacturers.
BirgelAs part of the Open Integration Partner Program, we were able to demonstrate the advantages of Ethernet-APL technology such as redundancy, device replacement, and system expansion, but above all we were also able to guarantee them.
Gerd Niedermayer, Senior Electrical+Instrumentation Engineering Manager at BASFWe have been working with industrial partners for 3 to 5 years to jointly advance this technology. That was Pepperl+Fuchs, Endress+Hauser, and our leading system suppliers such as Honeywell, ABB, and Siemens. And the work has been very successful.
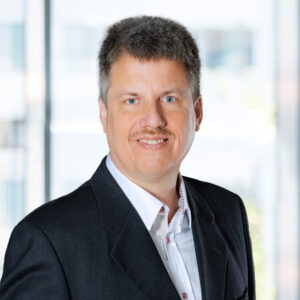
TrunzerThe test setup was very impressive—we had previously worked on a laboratory scale. To see that a network with 240 devices works really robustly and reliably was remarkable!
NiedermayerAfter five years of close cooperation with our PROFINET partners at APL, these successful tests are an important step towards using the technology in our new chemical plants in the future: We will equip two new BASF plants in Ludwigshafen with this technology and get them up and running in 2025 and reap the rewards of this collaboration together.
HenneckeThe development teams have been carrying out long-term tests with our FieldConnex field switches for years. So, we were confident that the setup would stand up to the challenges. Seeing that everything works so well in a realistic setup has the potential to convince everyone to now go down the path of digitalizing process plants.