Jun 29, 2020
Data-Driven Partnership
In October 2019, Pepperl+Fuchs opened its state-of-the-art US Distribution Center (UDC) in Katy, Texas. The 110,000-square-foot facility is the smallest of Pepperl+Fuchs’ three global distribution centers, but it provides an unparalleled showcase of the capabilities of Pepperl+Fuchs sensors.
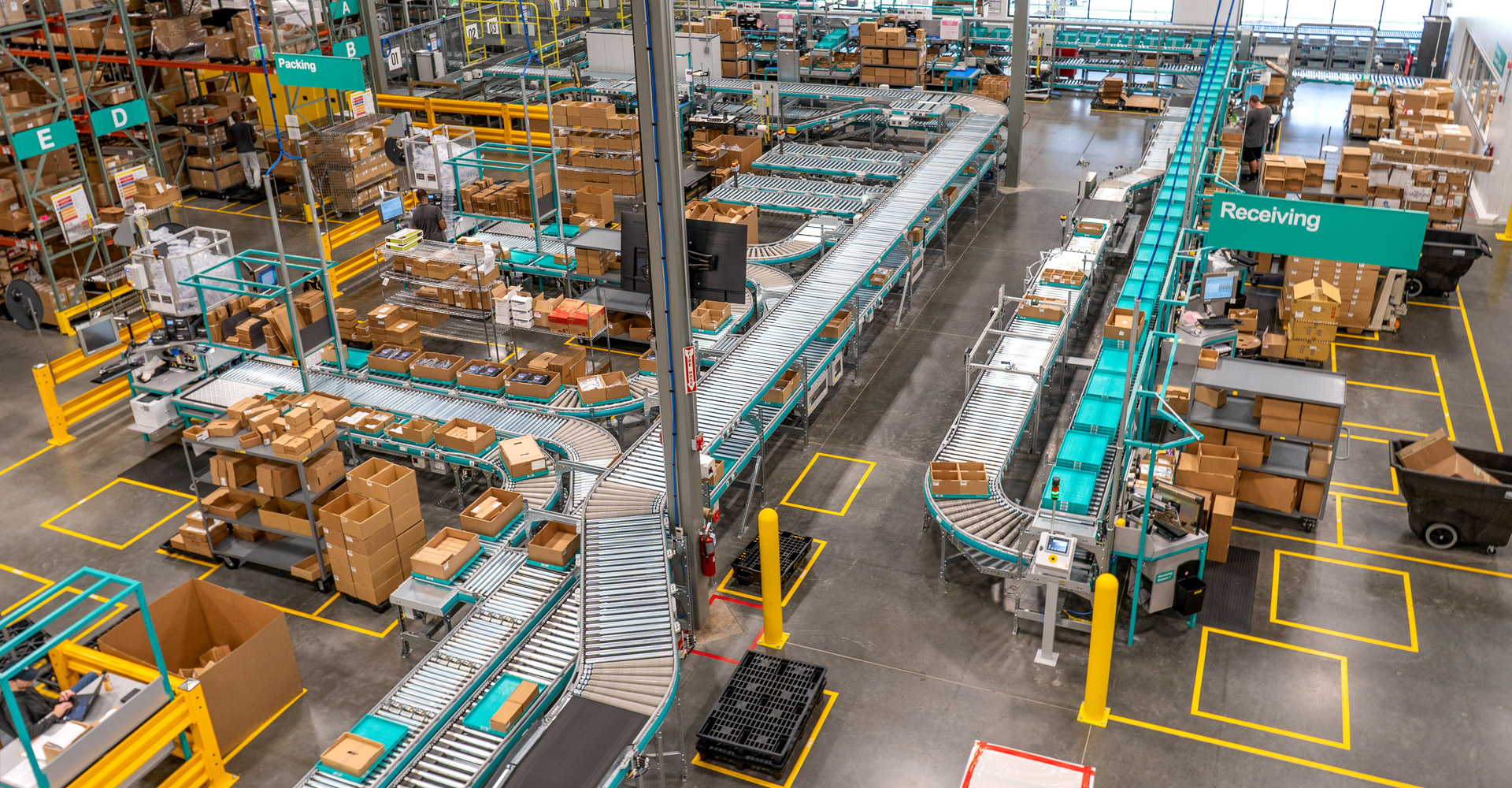
In many ways, the UDC resembles Pepperl+Fuchs’ European Distribution Center in Mannheim, Germany, and Global Distribution Center in Singapore. All three have a similar structure, technology, and operating system, with conveyors as far as the eye can see, a towering automated storage and retrieval system (AS/RS), bright green trays shuttling goods to and from, a shared ERP, and rack after rack of storage space. But the UDC is the only distribution center to rely entirely on data from Pepperl+Fuchs sensors to power its warehouse management software.
Showcasing Technology
In addition to being Pepperl+Fuchs’ North American distribution hub, the UDC also serves as a massive showroom for the company’s sensor technologies. For help creating an advanced material handling system that incorporated its own products and data, Pepperl+Fuchs partnered with SSI SCHAEFER, a leading provider of products and systems for material handling. “SSI SCHAEFER agreed to design an automated storage and retrieval system (AS/RS) that helped us showcase our sensors, and our automation technology fits well with their warehouse management technologies,” says Jim Bolin, Executive Vice President for the Americas, Process Automation. The AS/RS incorporates around 1,000 Pepperl+Fuchs sensors and software from SSI SCHAEFER.
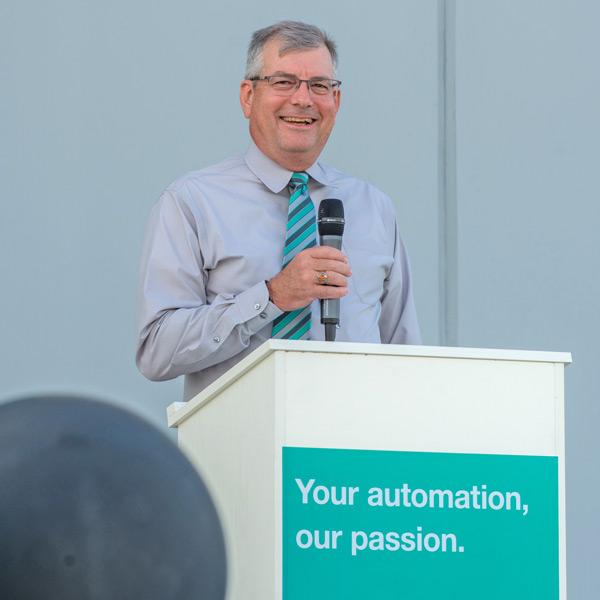
SSI SCHAEFER agreed to design an automated storage and retrieval system (AS/RS) that helped us showcase our sensors, and our automation technology fits well with their warehouse management technologies.
Jim Bolin, Executive Vice President for Process Automation, Pepperl+Fuchs AmericasPowered by Innovation
Pepperl+Fuchs sensors in use throughout the UDC send data to SSI SCHAEFER’s software, WAMAS® and WAMAS® Lighthouse. Together, sensors and software operate the entire system and provide real-time updates on key performance indicators. “The WAMAS Lighthouse software allows the company to monitor, control, and optimize productivity,” explains Jan Jagersky, SSI SCHAEFER’s director of IT solutions. The real-time data that flows from the system creates a new level of supply chain visibility for Pepperl+Fuchs’ North American operations.
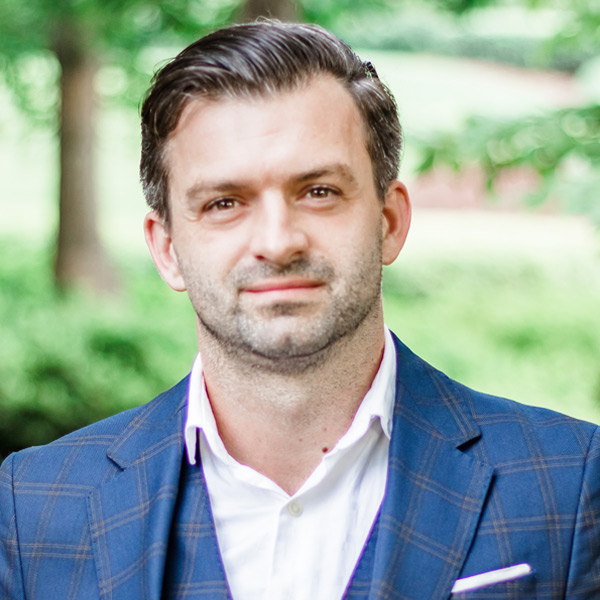
The WAMAS Lighthouse software allows the company to monitor, control, and optimize productivity.
Jan Jagersky, Director of IT Solutions at SSI SCHAEFEREvery day, Pepperl+Fuchs sensors in the UDC’s AS/RS system are busy ensuring the efficiency of the UDC’s picking and receiving processes and feeding data to WAMAS. The AS/RS has three aisles with two pick-up / drop-off locations at each end. A crane in the center of each aisle serves racks to the right and left, retrieving and delivering products to and from the end locations. IO-Link-enabled R100 series triangulation sensors align the crane to the rack vertically and horizontally. A PCV read head uses Data Matrix code tape to position the crane vertically with millimeter accuracy. A VDM100 distance sensor positions the crane horizontally within the racks. Finally, an optical data coupler transfers all Ethernet data at 100 mbps full duplex directly to and from the crane as it is moving.
The AS/RS has 18,000 storage locations and currently stores about 6,000 finished goods and 5,000 different raw materials. A VB24 barcode scanner mounted on the scan bridge ensures that all of these goods and materials are in the correct trays when they travel to and from the AS/RS.
The AS/RS has 18,000 storage locations and currently stores about 6,000 finished goods and 5,000 different raw materials. Pepperl+Fuchs sensors provide data to WAMAS software.
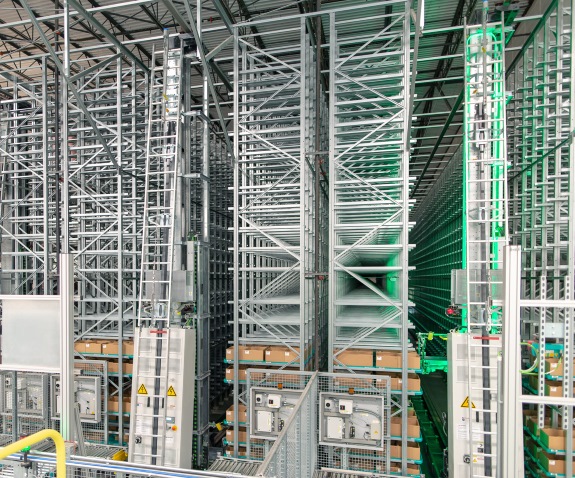
IO-Link-enabled R100 series triangulation sensors align the crane to the rack vertically and horizontally. A PCV read head uses Data Matrix code tape to position the crane vertically with millimeter accuracy.

A VDM100 distance sensor positions the crane horizontally within the racks.
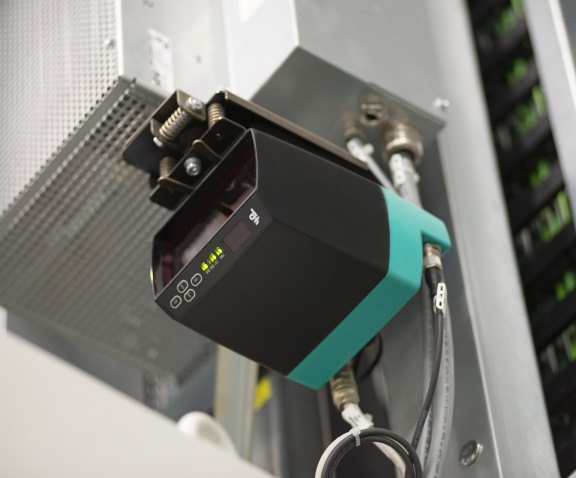
The optical data coupler LS682 transfers all Ethernet data at 100 mbps full duplex directly to and from the crane as it is moving.
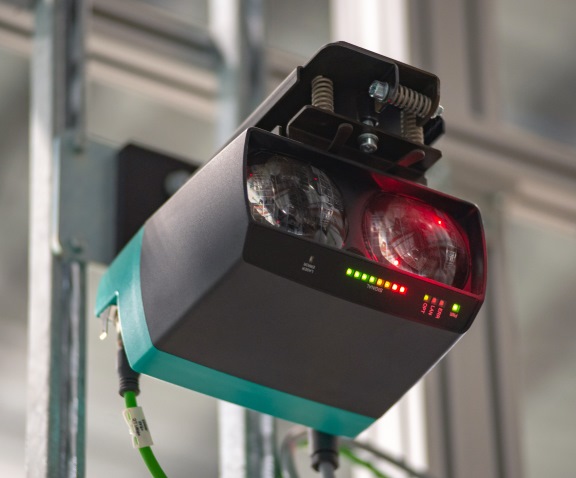
A VB24 barcode scanner mounted on the scan bridge ensures that all of these goods and materials are in the correct trays when they travel to and from the AS/RS.
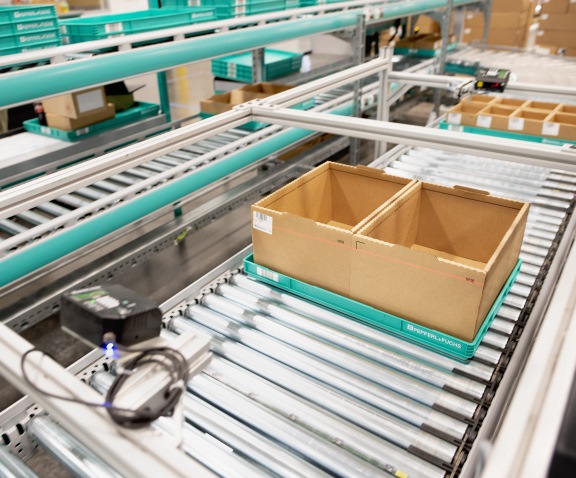
Lighting the Way to More Efficient Picking
When items must be shipped out, they are automatically retrieved from the AS/RS and delivered to picking stations on bright green trays. Pickers fill orders using a pick-to-light system that consists of four SSI SCHAEFER pick-to-light workstations and an R2000 2-D LiDAR sensor. The system uses signal lamps to indicate which products within a tray need to be picked for an order. When a specific part or product is needed, the lamps shine on the box containing the ordered item. A picker removes the ordered items and transfers them to a tray that holds up to four shipping boxes.
The R2000 2-D sensor monitors the shipping boxes to ensure the right product is added to the right box. Each tray of boxes is divided into four predefined zones. When a picker places an item in a box, the R2000 detects the presence of the worker’s arm in that zone. If the worker places an item in the incorrect box, the sensor will trigger an alert. Once all orders in a tray have been boxed, pickers press a button to confirm that the orders have been filled. This prompts the system to transport the tray of orders to shipping.
Combining the R2000 and pick-to-light system creates a precise, paperless, and optimized picking process. An additional pick station for internal work orders enables Pepperl+Fuchs employees to pick the materials needed for custom applications and deliver them to on-site production.
Built for Continued Growth
By harnessing the power of its own sensors and partnering with SSI SCHAEFER, Pepperl+Fuchs has been able to automate processes that had been largely manual before the UDC was built. “Receiving has been cut from an hour down to 15 minutes and parts picking has been cut from four minutes to one minute,” says Colin Akers, Pepperl+Fuchs’ director of operations for North America. The additional data will also help management optimize staff levels based on order volume and plan preventive maintenance to minimize downtime.
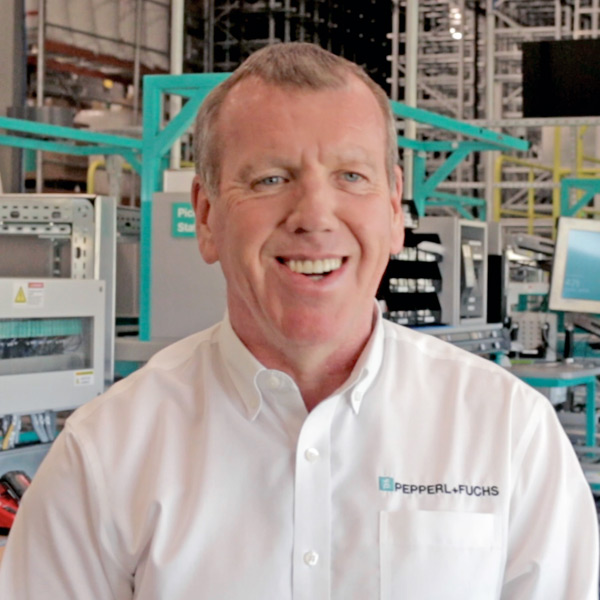
Receiving has been cut from an hour down to 15 minutes and parts picking has been cut from four minutes to one minute.
Colin Akers, Pepperl+Fuchs’ Director of Operations for North America“Traditional systems aren’t this transparent. As [Pepperl+Fuchs’] business evolves, we can help them take advantage of new opportunities,” says Jagersky. To ensure continuous process improvement, Pepperl+Fuchs and SSI SCHAEFER continue to meet monthly to discuss the system, the progress that has been made, and plans for the future.