Nov 7, 2021
Retrofit for the Textile Industry
As a provider of automation solutions for the textile industry, SETEX Schermuly textile computer GmbH sets quality standards in textile production using operator panels and camera systems from Pepperl+Fuchs. A retrofit project in Honduras shows how state-of-the-art automation technology enables efficient and reliable processes.
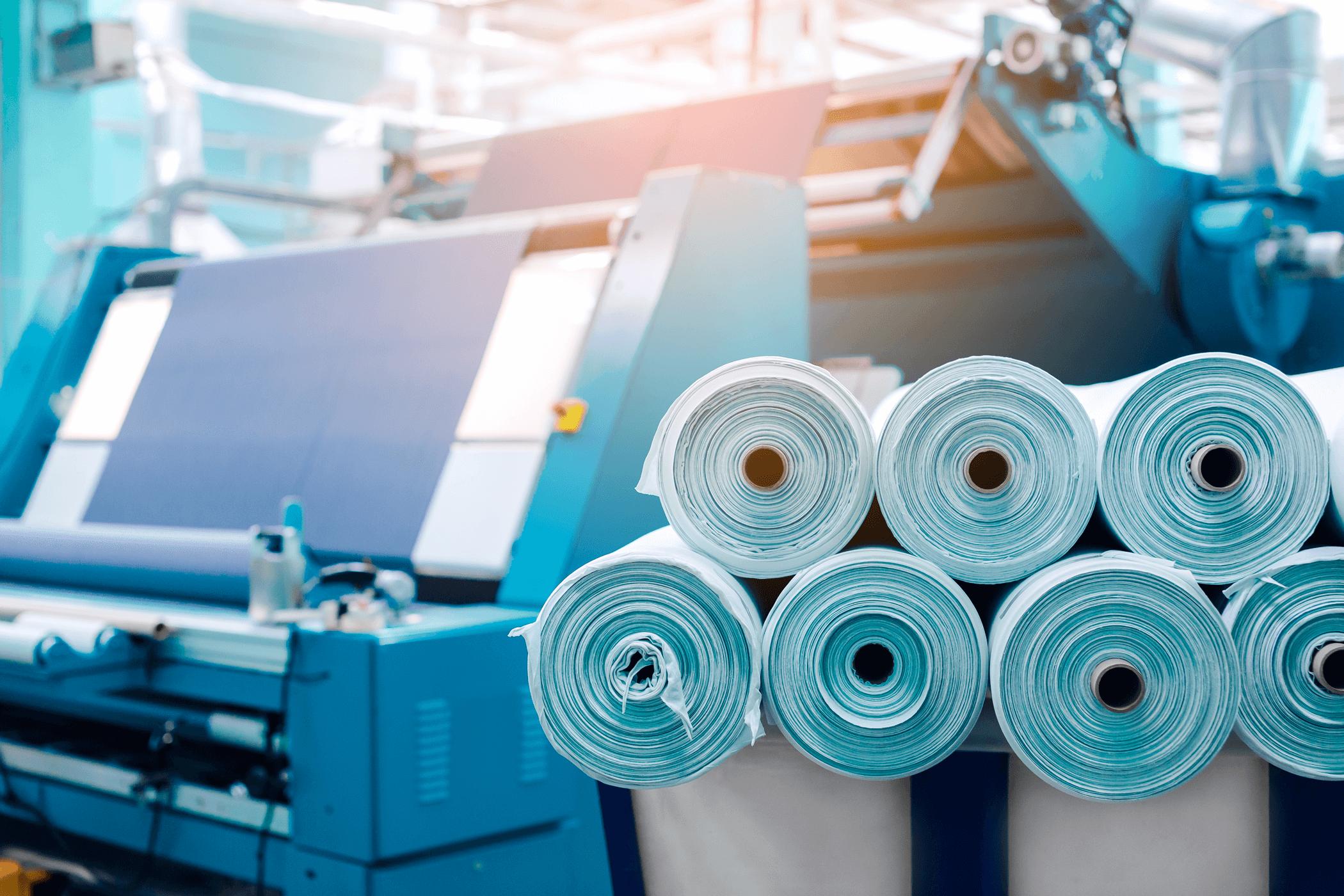
Honduras—alongside a wealth of flora and fauna and numerous national parks, this Central American country has a lot to offer as an industrial location. In addition to being one of the world's largest coffee producers, it is also home to a constantly growing textile industry. As a provider of automation solutions for the textile industry, SETEX Schermuly textile computer GmbH, based in the tranquil German town of Mengerskirchen in the district of Limburg-Weilburg, has secured its position as a technical partner to market-leading garment manufacturers. These include a well-known Honduran textile producer, which SETEX provides with operator panels and camera systems to meet its specific quality standards.
In our interview, Stefan Saam, Area Sales Manager at SETEX, Guenter Schaefer, Manager Process Control Engineering at SETEX, and Johannes Danek, Sales Engineer at Pepperl+Fuchs Vertrieb Deutschland GmbH, explain what textile production involves and how the interplay of state-of-the-art automation technologies has enabled a retrofit solution for efficient and reliable processes for the project in Honduras.
What factors need to be taken into account in textile processing and what problems was your customer experiencing?
Stefan Saam:
When processing lengths of tubular fabrics, in addition to the quality of the fabric itself, it is very important to measure its width and density with precision. This is both essential for further processing, and a key quality characteristic. Our customer in Honduras had previously tried to measure the width of the material using different technologies without success. On some machines, the width measurement was even still being carried out manually by the operating personnel.
Guenter Schaefer:
This manual work step is problematic in many respects. Checking the meter-long fabric panels and making the necessary adjustments often involves the personnel having to climb into the machinery itself, which is taller than a person. The confined spaces and rising steam make work very difficult in some cases. Unlike with measuring processes controlled using entirely digital methods, the material width is only checked at selected points. There is also a lack of consistent logging across the entire process that would allow conclusions to be drawn about the quality of the material afterward.
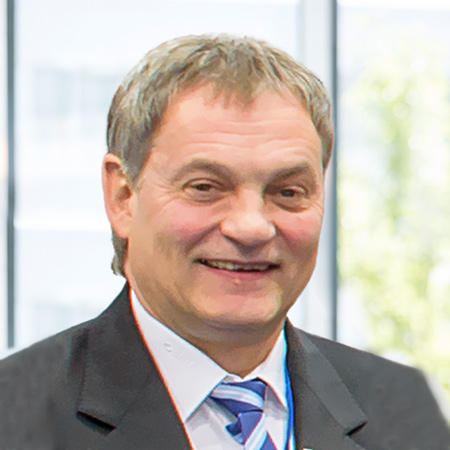
The greatest challenge was to find a suitable retrofit solution that could be used to transfer process data to the PLCs via a serial interface.
Guenter Schaefer, Manager Process Control Engineering at SETEX Schermuly textile computer GmbH
What was the requirement for this particular project?
Guenter Schaefer:
A number of older serial programmable logic controllers (PLCs) are in use at the Honduras plant. The greatest challenge was to find a suitable retrofit solution that could be used to transfer process data to the PLCs via a serial interface. In addition, the different material colors and widths of up to 1200 mm at the plant had to be measured to an accuracy of +/- 4 mm.
Stefan Saam:
When we were looking for a suitable partner company to realize this project, Pepperl+Fuchs quickly came out on top. The automation specialist from Mannheim was the only supplier to present us with a unique solution that allows modern sensor technology to be integrated into older control panels. We were also impressed by the worldwide support provided by industrial communication specialists in America, and the agile international sales network, which is available to us and the customer in Honduras around the clock.
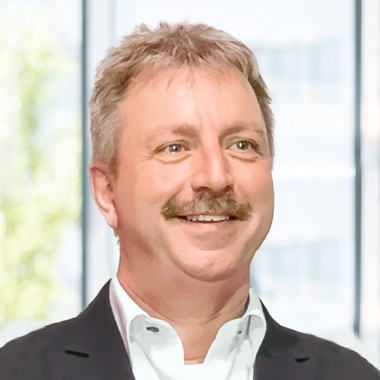
The automation specialist from Mannheim was the only supplier to present us with a unique solution that allows modern sensor technology to be integrated into older control panels.
Stefan Saam, Area Sales Manager at SETEX Schermuly textile computer GmbH
What exactly does this solution look like?
Johannes Danek:
The presence of steam and the different fabric colors that needed to be detected in the plant meant that we were unable to use components based on reflections or cameras. Instead, we decided to use the LGM8 measuring light grid with IO-Link interface, which is based on a reliable transmitter-receiver concept. This can measure material widths of up to 2100 mm with an accuracy of 4 mm using an internal beam crossover.
We therefore had to find a way to transfer the IO-Link data into the existing SETEX serial control panel, and vice versa. By using industrial communication components, SETEX now has the option of equipping existing machines with up to eight different IO-Link nodes simultaneously.
When processing lengths of tubular fabrics, in addition to the quality of the fabric itself, it is very important to measure its width and density with precision.
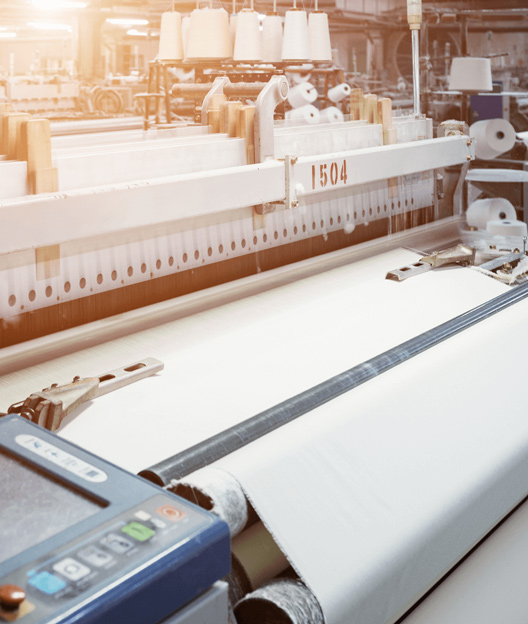
When it came to measuring the fabric width, the LGM 8 measuring light grid with IO-Link interface convinced SETEX. It can measure material widths of up to 2100 mm with an accuracy of 4 mm using an internal beam crossover.
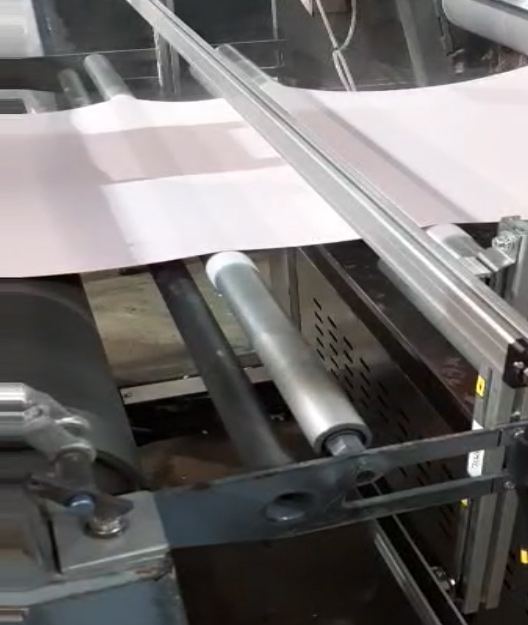
The measuring LGM8 light grids with IO-Link impress with their super-fast object detection even with 3-way beam crossings. Thanks to the IO-Link interface, all process and parameter data can be transferred to the controller. New batches and fabric widths can be easily parameterized and the extensive diagnostic data make ease machine maintenance.
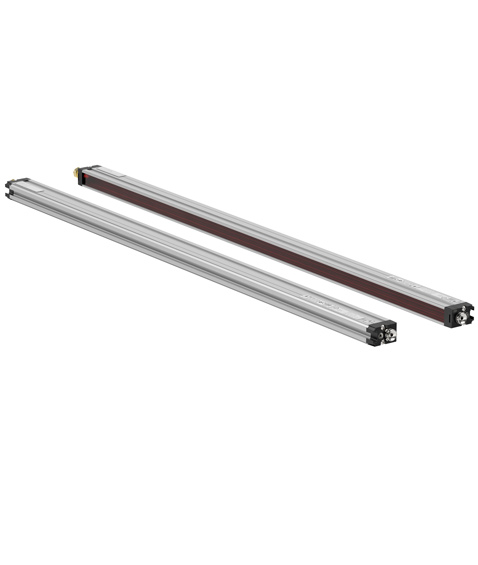
The LGM light grid and up to seven other IO-Link devices or conventional modules with binary inputs/outputs can be easily connected to the controller via an IO-Link master from the ICE2 series.
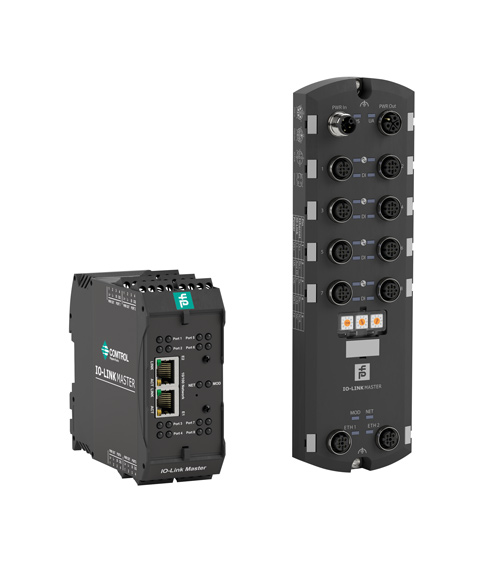
How was it possible to connect serial communication with the contemporary IO-Link standard?
Johannes Danek:
This is where our serial gateways from the DeviceMaster™ series come into play. They can be used to transfer serial device data to higher-level Ethernet or industrial Ethernet networks such as EtherNet/IP™, MODBUS TCP, and PROFINET. For the solution from SETEX, this means that the collected IO-Link process data is transmitted directly to the customer's control panel in the form of a serial Modbus RTU protocol. The ICE2 series IO-Link master allows up to eight IO-Link devices or conventional modules with discrete inputs/outputs to be connected to the control panel simultaneously. This has the added benefit that several devices can be configured and monitored in parallel via a central interface.
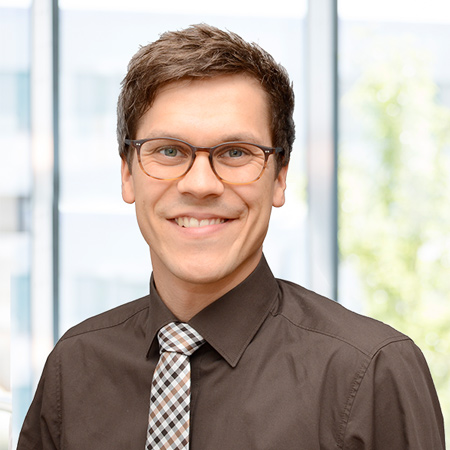
By using industrial communication components, SETEX now has the option of equipping existing machines with up to eight different IO-Link devices or conventional modules with discrete inputs/outputs to be connected to the control panel simultaneously.
Johannes Danek, Sales Engineer at Pepperl+Fuchs
What are the positive effects of using the solution?
Stefan Saam:
The textile processing sector is not comparable with other industries, such as the automotive industry, and the relevant key figures depend on a range of factors. The weave construction of a fabric and yarn alone results in high tolerances, which continue to change during the course of the process due to chemical and thermal reactions. Currently, the light grids are used to measure widths during thermal shrinking processes, where the material density and weight are of particular importance. During this process, the fabric is shrunk professionally, which prevents further shrinkage during washing and ensures that the material retains its shape over the long term. The width of the textile must be monitored at all times so that it matches the template subsequently used for punching out. This therefore requires automatic regulation of both the shrinkage and width in the machinery. Depending on the specific item, the quality and, above all, the reproducibility can be optimized by 10 %.
Do you see any further potential for optimization?
Guenter Schaefer:
We are currently testing using 2-D vision sensors from the VOS series to detect holes in the goods automatically. This important step in quality control is also carried out manually at present, which makes it suitably time-consuming, especially because the error log must also be entered manually into a database.
To date, Johannes Danek has been able to provide suitable proposals and sensor solutions for every problem in the test setups, and the latest test results are very promising. We therefore see great potential for the future—and that goes for the collaboration with Pepperl+Fuchs too!
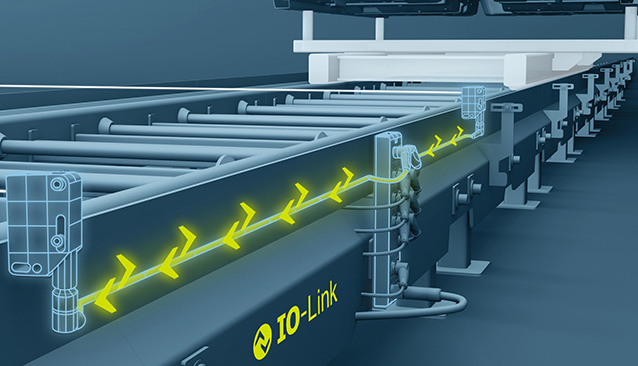
As an internationally standardized, manufacturer-independent technology, IO-Link is an essential component of the Sensorik4.0® solutions from Pepperl+Fuchs. This future-proof interface provides continuous, bidirectional communication between the control level and the lowest sensor/actuator level. For example, it enables users to perform extensive diagnostics or parameterize IO-Link devices during operation via the control panel.