September 2, 2019
Two-in-One—Increased Production and DCS Modernization Combined
As part of a large-scale turnaround project, Kuraray succeeded in comprehensively modernizing the control technology at its Antwerp production site with the help of its partners Yokogawa and Pepperl+Fuchs.
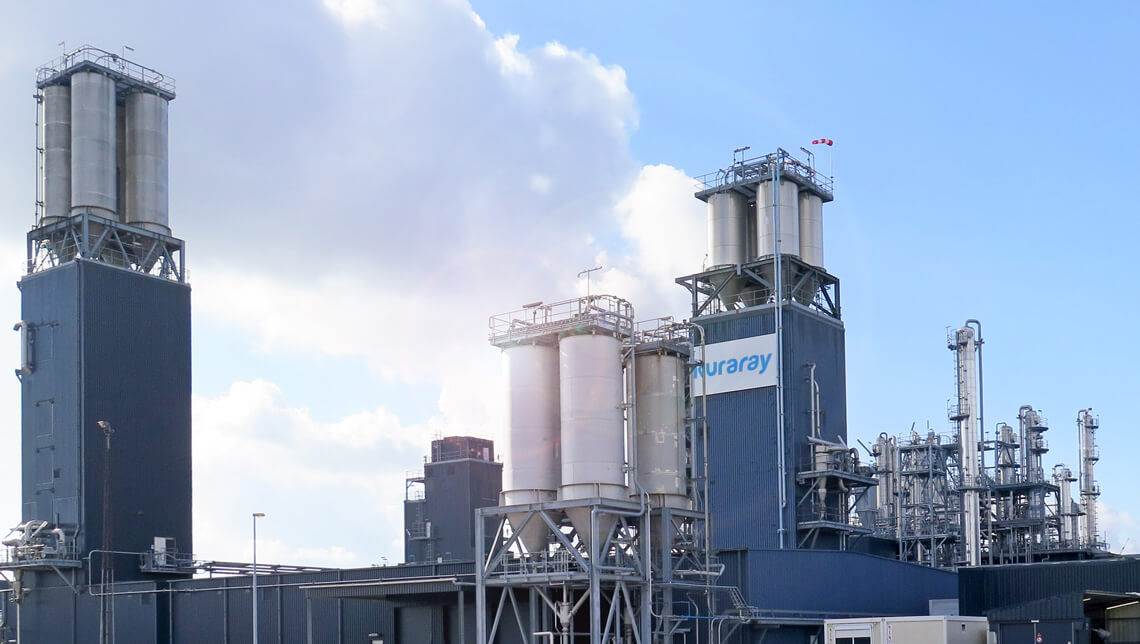
A Shared Vision
When profound changes to control technology are necessary in the process industry, all decisions must be carefully considered. What opportunities and risks does the turnaround project entail? What costs will arise and how much work will be involved? How much time will the conversion take? Kuraray, the world's largest producer of polyvinyl alcohol (PVOH) and ethyl vinyl alcohol (EVOH) resins and films, faced precisely these challenges. The solution involved active support from Yokogawa and Pepperl+Fuchs.
The initial motive for the change was a positive one, as Lars de Ryck, Senior Process and Control Engineer at Kuraray, reports. 'We started planning how to increase our production capacity to meet the steadily increasing demand for EVOH. We were also looking at the control technology throughout the plant.' These ideas led to an ambitious project: increasing production and modernizing the DCS at the same time.
The project managers at the Kuraray plant in Antwerp, Belgium—a hotspot for the European process industry—already had great confidence in Yokogawa, their long-standing control technology partner, so moving forward with the project was a no-brainer. 'We've relied on a Yokogawa control system here since 1999 and we haven´t had a single problem with any of the DCS controllers at our plant,' recalls Peter Brughmans, Senior Maintenance Engineer at Kuraray. A solid partnership was therefore already in place when the specification was drawn up for the most recent project. And once again, Yokogawa impressed the customer with its extraordinary dedication. 'After just a short time, the Yokogawa engineers had internalized and understood our production process in such detail that they were able to work more efficiently and independently every day. This saved us a lot of time at Kuraray,' Brughmans acknowledges.
Time was a key factor for the success of the project since the tight schedule encompassed several tasks, including changing the I/O platform from remote I/O to field network I/O, upgrading the network from Vnet to Vnet/IP, and upgrading to the latest CENTUM VPS Field Control Stations (FCS) and R6, the latest release of the CENTUM VP control system. The plans also covered reconfiguring the instrument room, field wiring, and signal routing. Ergonomically redesigning the control room and implementing the Plant Resource Manager (PRM) to improve asset management were the final requirements for the project.
Reasoning behind the Device List
To process this enormous list of tasks efficiently and methodically, the project team developed and maintained an extensive instrument index. 'This centralized list contained detailed information about all devices within the plant that needed to be added or adjusted,' explains Dirk Boon, Sales Manager at Yokogawa. More than 100 columns of data were available for each identification number. The columns included information such as address, cable number, marshalling cabinet ID, cross wiring ID, system cable ID, terminal ID, cabinet ID, rack ID, card ID, and channel number. This list documented all the routing—both the original configurations and the new ones. 'It took two man-years to finish the 100-column and 6000-row worksheet,' states Kurt Hellemans, Maintenance Engineer at Kuraray. The worksheet was used for creating inventory drawings for better visual transparency, and served as a central reference document for various activities, including cabinet construction and cross wiring.
Sophisticated Wiring with Pepperl+Fuchs
The reconfiguration of the instrument room was another key factor in the success of the project. After all, a well-organized wiring concept is essential for such a huge quantity of field wiring: 'We decided on an approach that gave us a clear distinction between the signal types via the cabinets,' reports Boon. System cabinets now contain only FCS and I/O modules, and additional cabinets are used for allocating and isolating the individual signal types (Ex i, Ex d, Ex d RTDs, binary I/Os).

Field control stations from Yokogawa save precious cabinet space while offering high-level performance at the same time (Image source: Yokogawa)
To efficiently connect the Ex d I/Os, Yokogawa sought support from its network and consulted its tried-and-tested partner, Pepperl+Fuchs. "We consistently use the H-System from Pepperl+Fuchs when integrating our control system solutions," Boon comments. The H-System is a flexible, scalable interface solution for electrical explosion protection developed by the Mannheim-based experts. It consists of multiple isolated barriers that are attached to a termination board via a quick-lock mechanism—no tools are necessary. This board is mounted on the standard DIN rail and the control system is connected using a specialized connector. "This control-system-specific connection and high packing density are what make the H-System so appealing to control system manufacturers like Yokogawa. Users can choose between modules with a width of 12.5 mm for the greatest single loop integrity and multichannel modules with a width of 18 mm and the highest packing density on the market. Several H‑System modules are also HART-compatible," reports Yon Barbin, the Key Account Manager at Pepperl+Fuchs who works directly with the Japanese control technology manufacturer. This close relationship allows Barbin to immediately record Yokogawa's unique project requirements and bring them to his colleagues in research and development at Pepperl+Fuchs.
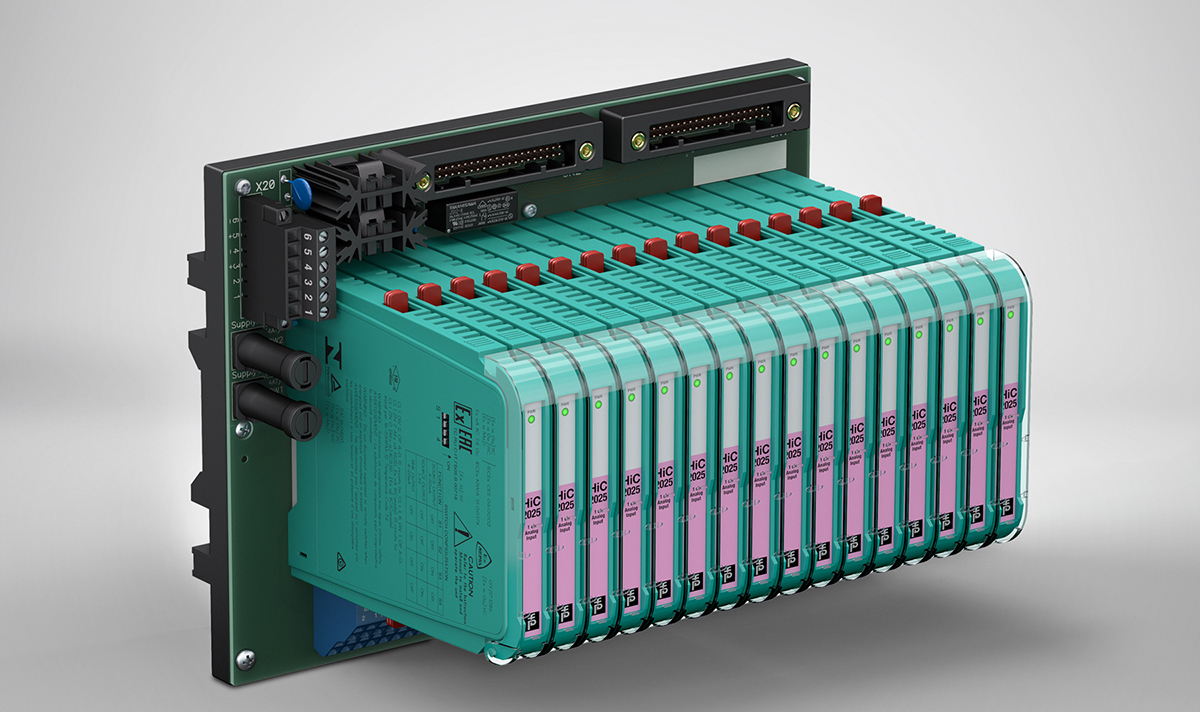
With its control-system specific connectors, the Pepperl+Fuchs H-System significantly reduces wiring efforts
Pepperl+Fuchs also collaborated closely with Yokogawa on this project to ensure that the H-System was tailored to the specific conditions at the Kuraray plant in Antwerp. "Pepperl+Fuchs ultimately presented us with a customized termination board, so we benefit from a higher packing density of channels per I/O module and rack and save valuable space in the switch cabinet," comments Brughmans. Support for Ex-d signals was also a special development since the standard H-System is designed for intrinsically safe circuits.
Six Weeks at Full Throttle
Following all this hard work by its partners, Kuraray eagerly awaited the final turnaround. After a detailed planning phase, completing the conversions and test procedures within just six weeks was all that remained. The installation teams worked in 14-hour shifts, six days a week to disconnect and successfully reconnect almost 10,000 individual cables in three and a half weeks. Next, around 50 multicore cables were extended and rerouted to the instrument room. 'This was obviously an intense part of the project, but everyone involved continued to work together effectively. The fact that the power supply to the control system only had to be interrupted for one week and the necessary software customizations were finished very quickly are proof of this,' says Brughmans, looking back on the final phase.
All Requirements Fulfilled
Now that the project has been completed successfully within the specified time frame and budget, Kuraray is delighted with its completely enhanced control technology. The expanded production plant in Antwerp is now future-proof. In addition, the successful integration of Yokogawa´s PRM creates potential for Industry 4.0 concepts. 'Smart instrument diagnostics now make it much easier to identify the maintenance status of field devices. We can also follow a predictive maintenance approach and make many checks in the field obsolete,' Hellemans comments. His colleague Brughmans also concludes on a positive note: 'The Yokogawa employees really went the extra mile and were extremely committed to making this project a success. They once again confirmed why we have never looked for a different control technology partner over the years.'
Dirk Boon from Yokogawa sees this shared understanding of collaboration as fundamental to the success of comprehensive projects like this: "For large projects such as this, it's really helpful to have already tackled some challenges together. This project was another opportunity to involve our long-standing partner Pepperl+Fuchs, which in turn made an important contribution to this sophisticated process control solution. That’s how were able to successfully combine two projects into one."