14. Mai 2024
Aufgeladen mit Expertise
Für die Transformation hin zur E-Mobilität braucht es leistungsstarke Automatisierungstechnik in der Batteriefertigung. Dafür bieten die Unternehmen der Pepperl+Fuchs Gruppe die passenden Lösungen – basierend auf ständiger technologischer Innovation und jahrzehntelanger Erfahrung in der Automobilindustrie.
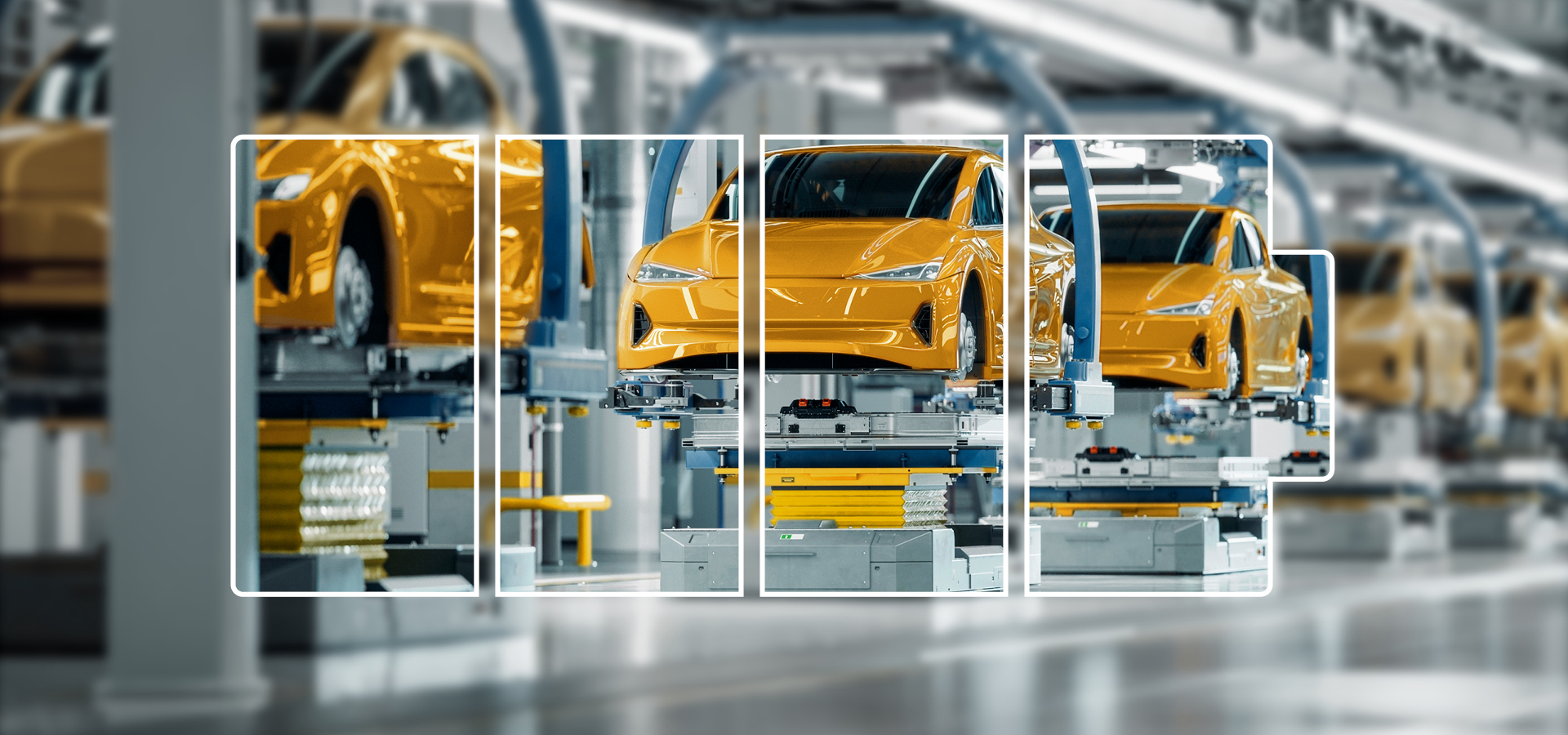
Auch wenn es so scheinen mag, ist das E-Auto nicht bloß ein Trend der Gegenwart. Lange bevor Diesel und Benziner den Markt eroberten, stellte der Franzose Gustave Trouvé im Jahr 1881 das erste Elektroauto der Öffentlichkeit vor. Es hatte 6 PS und erreichte eine Geschwindigkeit von 12 km/h sowie eine Reichweite von 14 bis 16 km. Von diesen Werten sind die heutigen Elektroautos weit entfernt: Die sportlichsten Modelle rasen mit über 1000 PS und 300 km/h die Straßen entlang. Besonders leistungsstarke Fahrzeuge schaffen es sogar auf Reichweiten von über 700 km. Ein wesentlicher Teil dieser Erfolgsgeschichte sind die technischen Fortschritte in Bezug auf das Herzstück des E-Autos — die Batterie.
Um bei der Batterieherstellung sowohl Effizienz als auch Qualität zu maximieren, braucht es die passende Automatisierungstechnik. Die Pepperl+Fuchs Gruppe bietet maßgeschneiderte Lösungen für jeden Schritt — von den Elektroden und Batteriezellen über die Module bis hin zum fertigen Batteriepack und dem Einbau in die Karosse. Dafür sorgen hochspezialisierte Tochterunternehmen innerhalb der Unternehmensgruppe, die eng und vertrauensvoll mit Automobilherstellern aus aller Welt zusammenarbeiten. Wie Anlagenbetreiber ihre Batteriefertigung erfolgreich automatisieren können, lässt sich anhand ausgewählter Lösungen von Pepperl+Fuchs, VMT Vision Machine Technik Bildverarbeitungssysteme GmbH und Polyplan GmbH nachverfolgen.
Doppelte Folien zuverlässig erkannt
Die kleinste Einheit einer Batteriezelle besteht aus zwei Elektroden und einem Elektrodenseparator. Je nach Herstellungsverfahren werden die Folien entweder wechselnd aufeinandergestapelt oder um einen Center-Pin oder Wickeldorn gewickelt. Bei all diesen Schritten sorgen die industriellen Sensoren von Pepperl+Fuchs für reibungslose Prozesse — etwa, wenn es um die besonders herausfordernde Doppellagenkontrolle beim Stapeln der Folien geht.
Da die Elektrodenfolien extrem dünn sind, kann es vorkommen, dass zwei oder mehr Folien aneinanderhaften. Für die Qualität der Batteriezellen darf der Vakuumgreifer jedoch immer nur ein Folienblatt aufnehmen, damit Anode und Kathode stets abwechselnd gestapelt werden. Auch wenn der Greifer kein Blatt abgelegt hat, muss das Stapeln unterbrochen und korrigiert werden.
Hierfür kommen IO-Link-Doppelbogensensoren zum Einsatz. Mithilfe von Ultraschallimpulsen überwachen sie den Materialfluss und erkennen, ob eine doppelte Lage zugeführt wurde. „Aufgrund der berührungslosen Detektion können die empfindlichen Folien nicht beschädigt werden“, erläutert Michael Förste, Key Account Manager Automotive bei Pepperl+Fuchs. „Das robuste Ultraschall-Messprinzip sorgt außerdem dafür, dass weder die Farbe noch die Reflexionseigenschaften der Folien das Detektionsvermögen beeinflussen.“ Zusätzlich ermöglicht die integrierte IO-Link-Schnittstelle eine vereinfachte Konfiguration, auch im laufenden Betrieb. Die Echtzeitüberwachung von Prozessdaten eröffnet darüber hinaus neue Potenziale für die Maschinenanalyse und -wartung. Dadurch lassen sich die Doppelbogensensoren optimal einstellen, was Fehldetektionen reduziert und die Anlagenverfügbarkeit erhöht.
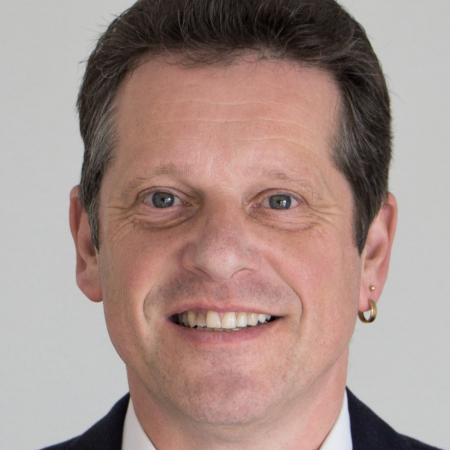
In drei Dimensionen die Qualität im Blick
Sobald die Folien ordnungsgemäß gestapelt oder gewickelt sind, wird der ionenleitfähige Elektrolyt eingefüllt und die Zelle verschlossen. Für die klassische Batteriearchitektur werden daraufhin mehrere Zellen zu einem Batteriemodul zusammengefügt, bis aus mehreren Modulen schließlich das fertige Batteriepack entsteht. Auch hierbei unterstützt Pepperl+Fuchs mit optimal abgestimmter Sensorik — etwa um die Qualität des bestückten Batteriemoduls zu kontrollieren.
„Vor der Weiterverarbeitung des Moduls muss überprüft werden, ob alle benötigten Zellen vorhanden, gerade ausgerichtet und ohne Überstand angeordnet sind“, erklärt Michael Förste. „Um Verzögerungen in der Produktion zu vermeiden, ist es außerdem wichtig, dass diese Qualitätskontrolle ohne Zeitverzug stattfindet, während das Modul auf einem Förderband oder einer Rollenbahn transportiert wird.“
Für diese Aufgabe bietet der SmartRunner Explorer 3-D eine ideale Lösung: Mit Stereo-Vision-Technologie sorgt der Vision-Sensor für eine vollautomatische Qualitätsprüfung im laufenden Prozess. Dafür erzeugt er ein hochaufgelöstes 3-D-Punktwolkenbild des gesamten Messbereichs. Das Batteriemodul und die einzelnen Zellen werden dabei in allen benötigten Details präzise abgebildet. Mit der Software ViSolution lässt sich der SmartRunner Explorer 3-D anhand von Livedaten auf intuitive Weise in Betrieb nehmen und parametrieren. Die Vorverarbeitung der Messdaten übernimmt der Sensor selbst in seinem integrierten Field Programmable Gate Array (FPGA). „So erhalten unsere Kunden schnell und unkompliziert alle Daten, die sie für die Qualitätsprüfung der Batteriemodule brauchen“, fasst Michael Förste zusammen.
Wärme sicher ableiten
Nachdem die Module korrekt bestückt und verschlossen sind, werden sie in Packs eingesetzt. Eine zentrale Rolle spielt dabei das Auftragen von Wärmeleitpaste. Denn bei jedem Lade- und Entladevorgang entsteht Wärme, die abgeleitet werden muss, um die Batterie vor Überhitzung zu schützen. Deshalb werden vor dem Einbau der Module häufig Bahnen von Wärmeleitpaste — sogenannte Gap Filler — in der Batteriewanne aufgebracht.
Bei diesem Prozess kommt eine Vision-Lösung der VMT Bildverarbeitungssysteme GmbH zum Einsatz, die sich als wegweisendes Inspektionssystem zur Kleberaupenkontrolle etabliert hat. „Mit dem VMT SpinTop G2 lässt sich die Durchgängigkeit und Korrektheit der Gap-Filler-Bahnen kontrollieren — und das parallel zum Auftrag, sodass keine zusätzliche Auswertezeit nötig ist“, erläutert Joachim Kutschka, Senior Manager Sales & Product Management. Das Inspektionssystem wird direkt am Roboterarm angebracht. Zwei Messeinheiten drehen sich mit und sorgen für eine dreidimensionale Erfassung des raupenförmig aufgebrachten Materials. Ein zusätzlich mitgeliefertes Technologiepaket ermöglicht eine einfache Kommunikation mit der Robotersteuerung, sodass das Inspektionssystem entsprechend ausgerichtet wird.
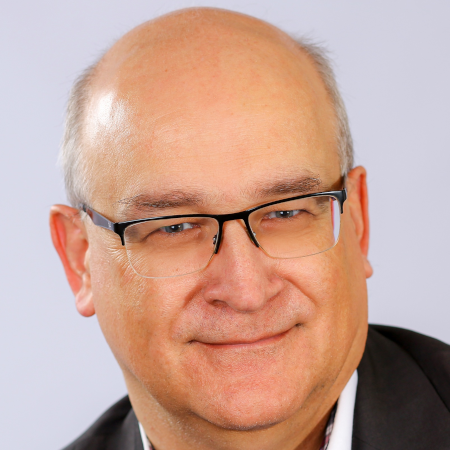
Im März 2024 hat VMT die neue Generation des SpinTop auf den Markt gebracht: Anstelle der zuvor verwendeten Infrarot-Laser werden nun hochwertige Laser mit blauem und rotem Licht im sichtbaren Spektrum eingesetzt. „Dies verbessert die Aufnahmequalität bei größeren Entfernungen und auf dunklen Oberflächen signifikant“, erklärt Kutschka. Darüber hinaus erreicht der SpinTop G2 eine Rate von bis zu 900 Scans pro Sekunde sowie eine doppelt so hohe Auflösung, was die Qualität der Überwachung deutlich erhöht. Dadurch eignet sich die Lösung nicht nur für die Prüfung des Gap-Filler-Auftrags, sondern auch für weitere Anwendungen in der Batteriefertigung — so etwa für die Kontrolle der Dichtraupen, die auf dem Wannenrand aufgebracht werden, bevor das Batteriepack mit einem Deckel verschlossen wird. „Diese Dichtungen sind oft nur wenige Millimeter dick und erfordern daher eine hochauflösende Sensorik“, so Kutschka. „Besonders dank der verdoppelten Auflösung des SpinTop G2 können wir nun herausfordernde Aufgaben wie diese noch besser lösen.“
Die VMT Bildverarbeitungssysteme GmbH bietet ihren Kunden seit über 25 Jahren schlüsselfertige Lösungen für verschiedene Anwendungen vom Presswerk über den Rohbau bis hin zur Endmontage. So wurde der SpinTop ursprünglich entwickelt, um Kleberaupen bei der Montage von Scheiben zu kontrollieren. Doch auch für die Batteriefertigung kommt das Inspektionssystem bereits in mehreren Anlagen internationaler Automobilhersteller und Dosiertechnikanbieter erfolgreich zum Einsatz. „Da sich die Prozessabläufe bei der Batterieproduktion rasant verändern, sehen wir viel Potenzial für weitere Einsatzmöglichkeiten“, blickt Joachim Kutschka optimistisch in die Zukunft.
Nachhaltig vor Korrosion geschützt
Beim Verschließen und Abdichten des Batteriepacks spielt auch die Korrosionsprävention eine wichtige Rolle. Beispielsweise an Kühlanschlüssen oder Verschraubungen muss sichergestellt sein, dass das Pack gut abgedichtet und vor Korrosion geschützt ist. Für diese Herausforderung bietet Polyplan GmbH eine besonders effiziente und ressourcenschonende Lösung. Das Unternehmen mit Sitz im bayerischen Strasslach liefert seit Jahrzehnten vollständige Fertigungszellen für Prozesse wie das Akustikschäumen oder das Türwachsen — und nun auch für die Korrosionsprävention bei der Batterieherstellung.
„Die Stellen der Batterie, die vor Korrosion geschützt werden müssen, sind häufig sehr schwer zugänglich“, erklärt Jan Jacobi, Leiter Vertrieb und Aftersales. Bei gängigen Automatisierungslösungen werde für die Versiegelung häufig zu viel Wachs gespritzt, sodass nicht nur Material verschwendet, sondern auch die Umgebung kontaminiert werde. In der Folge müsse das überschüssige Material abgereinigt und entstehende Aerosole abgesaugt werden. Demgegenüber biete die Lösung von Polyplan zahlreiche Vorteile: „Wir nutzen ein patentiertes Airless-/Airmix-Verfahren, bei dem keine Aerosole entstehen. Das Wachs wird mit einer Präzision von +/- 1 mm auf 500 mm Distanz aufgetragen. Dadurch benötigen wir nur eine minimale Menge von ca. 1 g/m, sodass wir eine langfristige Korrosionsprävention bei geringstem Medienverbrauch gewährleisten. Da der Aufwand für die zeit- und kostenintensive Reinigung und Absaugung entfällt, profitieren unsere Kunden außerdem von kürzeren Taktzeiten.“
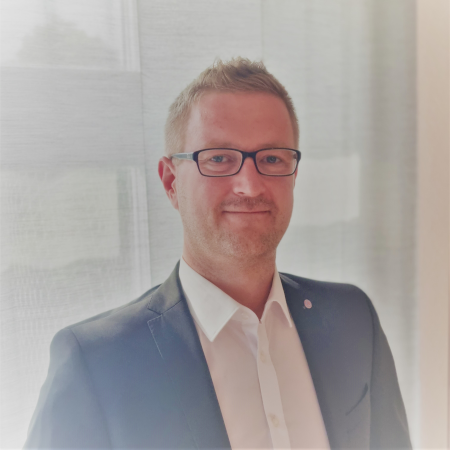
Die Technologie, die dieser Lösung zugrunde liegt, wird bereits in über 20 Produktionslinien großer Automobilhersteller für das Türwachsen genutzt. Mittlerweile hat sie sich auch bei den ersten Kunden in der Packproduktion bewährt. Vom Industrieroboter über das Wachsdosiersystem bis zur Sicherheitstechnik liefert Polyplan alles, was zu der schlüsselfertigen Roboterzelle dazugehört — jeweils abgestimmt auf die individuelle Anlage des Kunden. „Dabei nutzen wir auch Synergien innerhalb der Pepperl+Fuchs Gruppe“, fügt Jacobi hinzu. So kommt für die Objektlagekorrektur beispielsweise der VMT LineRunner zum Einsatz, ein leistungsstarker Laser-Triangulationssensor, der selbst bei schwierigen Lichtverhältnissen und wechselnden Oberflächenerscheinungen robuste Messergebnisse liefert.
Gemeinsam auf dem Weg zur nachhaltigen Mobilität
Nachdem das Batteriepack fertig verschlossen und sorgfältig überprüft ist, kann es in die Karosse eingebaut werden und von nun an viele Kilometer lang für emissionsfreie Fahrt sorgen. Neben der Doppelbogenkontrolle der Elektrodenfolien, der Qualitätsprüfung der Module, der Gap-Filler-Überwachung und der Korrosionsprävention kommen die Lösungen der Pepperl+Fuchs Gruppe in vielen weiteren Anwendungen rund um die Batterie zum Einsatz — damit Automobilhersteller auch in Zukunft die Elektromobilität immer weiter vorantreiben können.